Bulkhead fittings are essential components in countless industries, providing a secure and reliable way to connect systems to external environments. Whether you’re working on a marine vessel, a chemical processing plant, or an aerospace application, understanding bulkhead fittings is crucial.
This comprehensive guide will delve into the world of bulkhead fittings, exploring their functions, types, materials, and installation processes. Whether you’re a seasoned engineer or a DIY enthusiast, this information will equip you with the knowledge to select and utilize bulkhead fittings effectively.
Let’s dive in!
What Are Bulkhead Fittings
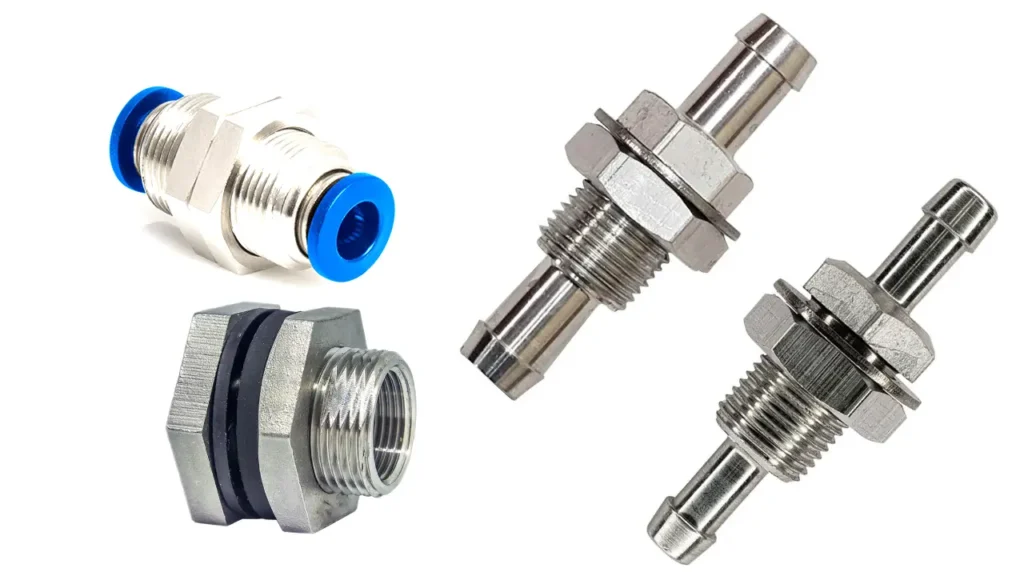
A bulkhead fitting is a specialized connector that allows for a fluid or gas to pass through a barrier, typically a wall or panel.
It’s commonly used in industries where sealing against external elements is crucial, such as marine, aerospace, and industrial applications. Bulkhead fittings are designed to provide a secure and leak-proof connection, ensuring the integrity of the system.
How Does a Bulkhead Fitting Work?
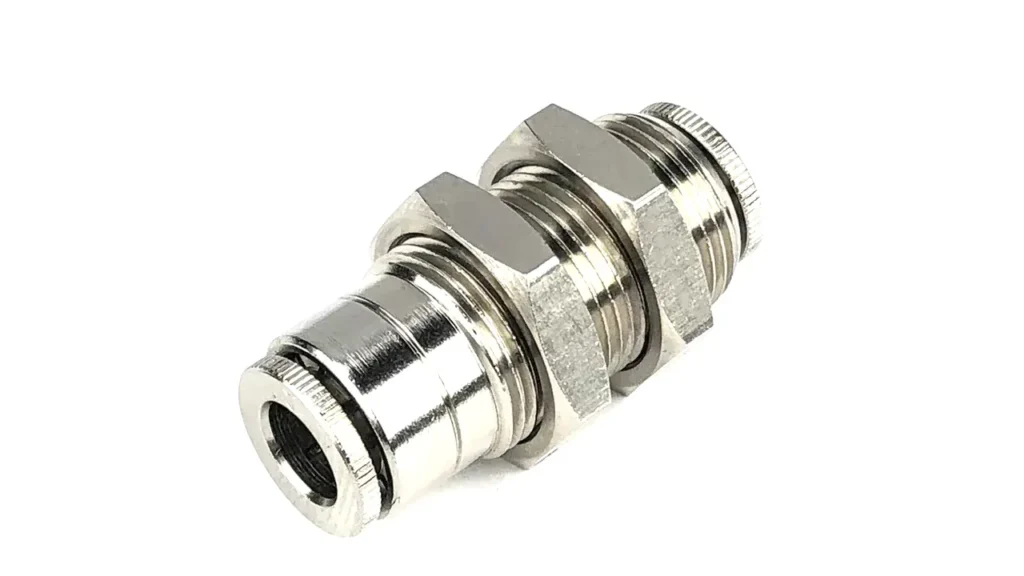
A bulkhead fitting essentially creates a controlled passage through a barrier. This barrier could be a tank wall, a ship’s hull, or any other solid surface. Its primary function is to allow fluids or gases to pass through this barrier safely and securely.
Components of a Bulkhead Fitting
A typical bulkhead fitting consists of two main parts:
- The Bulkhead Connector: This part is installed into the barrier. It has threads or a clamping mechanism to secure it in place.
- The Bulkhead Nut: This part is tightened onto the connector to create a seal and secure the hose or pipe.
How Do Bulkhead Fittings Work:
- Installation: The bulkhead connector is inserted into a pre-drilled hole in the barrier. It’s then secured using appropriate methods (bolts, clamps, etc.) to prevent leakage.
- Connection: A hose or pipe is attached to the connector, and a gasket or seal is often used between the connector and the hose to ensure a tight fit.
- Securing: The bulkhead nut is tightened onto the connector, compressing the gasket and creating a watertight or airtight seal.
The key to a bulkhead fitting’s effectiveness lies in the creation of a strong, leak-proof seal. This is achieved through a combination of proper installation, the use of appropriate gaskets, and the correct tightening of the bulkhead nut.
Types of Bulkhead Fittings
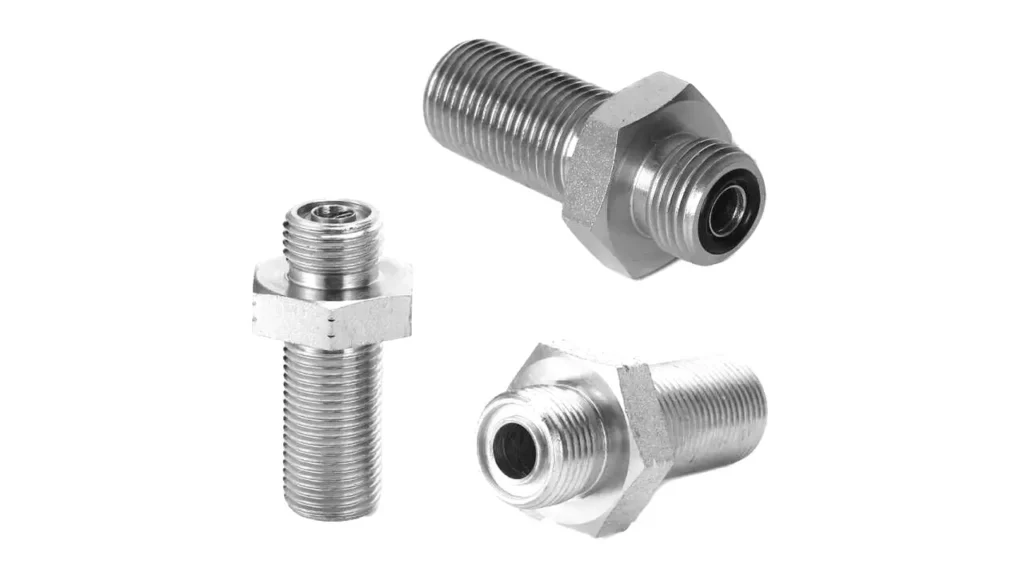
Bulkhead fittings come in various configurations to suit different applications and installation requirements.
Here are some common types:
Based on Connection Type:
Threaded Bulkhead Fittings: These are the most common type, featuring threaded connections on both ends. They offer a secure and reliable seal.
- Standard Threaded: Threaded on the outer side of both ends and the inner side of one end.
- Double Threaded: Threaded on both the front and back ends.
Clamp-Type Bulkhead Fittings: These use clamps to secure the fitting to the bulkhead and the hose or pipe. They are often used in applications where frequent connections and disconnections are required.
Quick Disconnect Bulkhead Fittings: Designed for rapid coupling and uncoupling, these fittings are ideal for applications where time is critical.
Based on Orientation:
Straight Bulkhead Fittings: These have a straight orientation, with the hose or pipe connecting directly to the bulkhead.
Angled Bulkhead Fittings: These have a bent or angled design, allowing for connections in confined spaces or at different angles.
Based on Material:
- Stainless Steel: Offers excellent corrosion resistance and durability.
- Brass: Provides good conductivity and machinability.
- Plastic: Lightweight and often used in less demanding applications.
- Other Alloys: Specific alloys may be used for specialized applications.
Other Types:
- Banjo Bulkhead Fittings: These feature a banjo bolt and two washers for a secure connection.
- Flanged Bulkhead Fittings: These have flanges for bolting to the bulkhead.
The choice of bulkhead fitting depends on factors such as the thickness of the bulkhead, the type of fluid or gas being handled, the pressure and temperature conditions, and the frequency of connections and disconnections.
Materials Used in Bulkhead Fittings
The choice of material for a bulkhead fitting depends on the specific application and environmental conditions. Common materials include:
- Stainless steel: Offers excellent corrosion resistance and durability.
- Brass: Provides good conductivity and machinability.
- Plastic: Lightweight and often used in less demanding applications.
- Other alloys: Specific alloys may be used for specialized applications, such as those involving high temperatures or pressures.
Applications of Bulkhead Fittings
Bulkhead fittings are widely used in a variety of industries:
- Marine industry: For connecting hoses to boat hulls for water intake, fuel supply, or bilge pumps.
- Aerospace industry: For transferring fluids or gases within aircraft or spacecraft.
- Chemical industry: For handling hazardous or corrosive substances.
- Food and beverage industry: For cleaning and sanitizing equipment.
- Industrial applications: For various fluid transfer and containment systems.
How to Install a Bulkhead Fitting
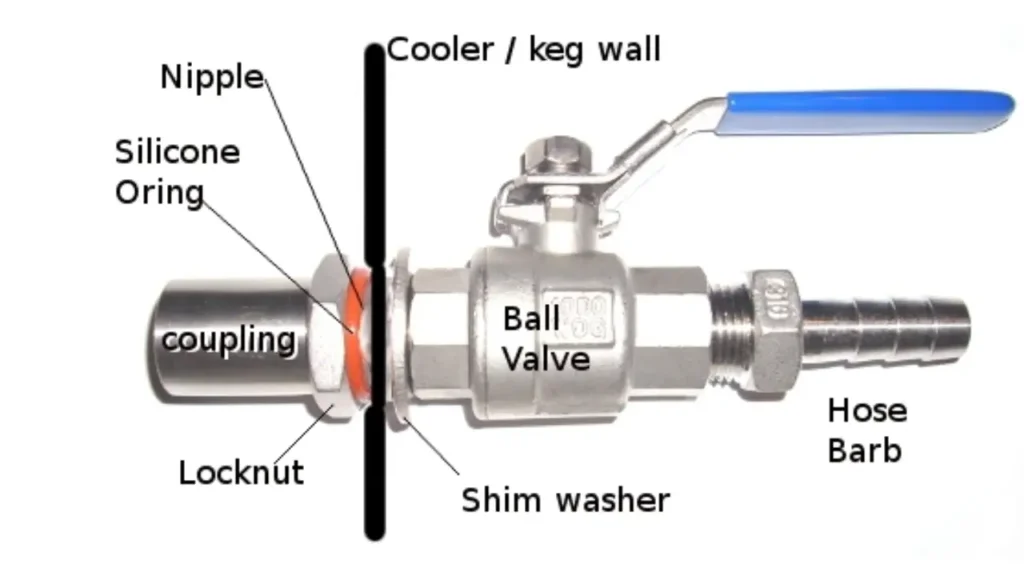
Installing a bulkhead fitting requires careful attention to detail to ensure a secure and leak-proof connection.
Here’s a general guide:
- Choose the right fitting: Select a bulkhead fitting that is compatible with the hose or pipe size, material, and the thickness of the bulkhead.
- Prepare the bulkhead: Drill a hole in the bulkhead with the correct diameter for the bulkhead fitting. Ensure that the hole is clean and free of burrs.
- Insert the bulkhead connector: Insert the bulkhead connector into the hole and secure it with the appropriate method, such as a nut and bolt or a clamping ring.
- Connect the hose or pipe: Attach the hose or pipe to the bulkhead connector using the appropriate fittings and clamps.
- Tighten the bulkhead nut: Tighten the bulkhead nut securely to create a watertight seal.
Note: Specific installation procedures may vary depending on the type of bulkhead fitting and the application. Always refer to the manufacturer‘s instructions for detailed guidance.
Tips for Maintaining Bulkhead Fittings
To ensure the longevity and performance of your bulkhead fittings, follow these tips:
- Regular inspection: Check for signs of wear, damage, or leaks.
- Proper tightening: Ensure the bulkhead nut is tightened securely but avoid overtightening.
- Lubrication: Apply a suitable lubricant to the threads of the bulkhead fitting to prevent seizing.
- Avoid excessive force: Do not apply excessive force when connecting or disconnecting hoses.
By following these guidelines, you can maintain the integrity of your bulkhead fittings and prevent potential problems.
Conclusion
Bulkhead fittings are essential components in countless industries, providing reliable and secure connections between systems and their environments. Understanding the different types, materials, and installation methods is crucial for selecting the right fitting for your specific needs.
By carefully considering factors such as the application, fluid or gas type, pressure, and temperature, you can ensure optimal performance and longevity of your system.
Are you ready to upgrade your system with the perfect bulkhead fitting? Contact [Your Company Name] today to discuss your requirements and explore our wide range of high-quality bulkhead fittings. Our experts are here to assist you in finding the ideal solution for your project.