A trip to any welding workshop or a glance at the equipment of a professional welder will reveal an assortment of tools. One key component that plays a crucial role in the welding process is the welding argon hose. This may appear as a simple piece of equipment but its role is vital.
The welding argon hose is pivotal to ensuring safe and efficient welding practices. Our comprehensive guide will delve deep into this indispensable tool, its uses, maintenance, safety precautions, and purchasing considerations.
What is a Welding Argon Hose?
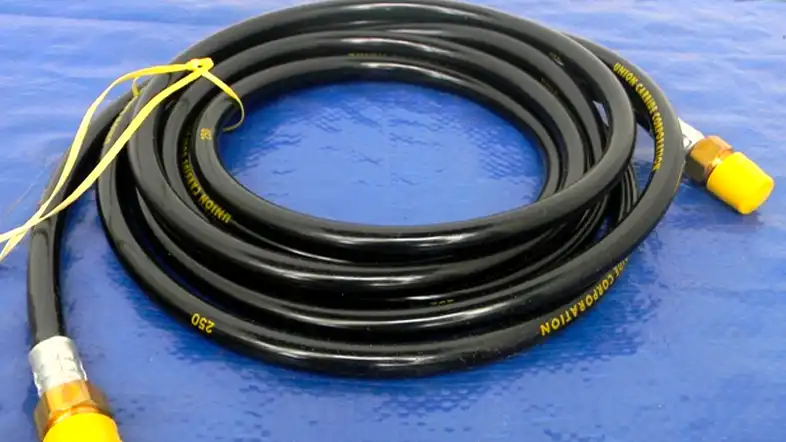
The argon welding hose is a specially designed conduit that transports argon gas from the gas cylinder to the welding torch during the welding process. Its role is to ensure a steady, controlled, and safe flow of the inert argon gas. To grasp the importance of the argon welding hose, we first need to understand the role of argon gas in welding.
Argon Gas: The Silent Worker in Welding
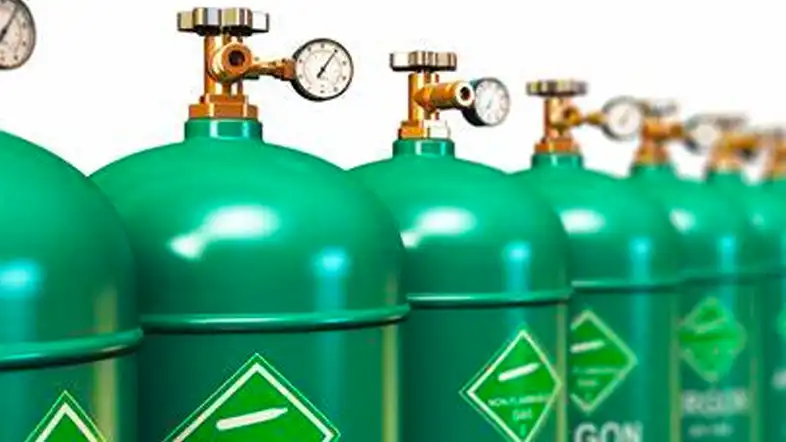
Argon gas plays an integral role in various welding processes, especially in Gas Tungsten Arc Welding (GTAW) and Gas Metal Arc Welding (GMAW). Its role, while often overshadowed by the more visible components of welding, is vital in ensuring the high quality and integrity of the finished weld.
Argon is an inert or noble gas. This simply means that it has a very low tendency to react with other elements. Due to this characteristic, argon doesn’t undergo chemical reactions during the welding process, even when exposed to the high heat levels typically generated. The non-reactivity of argon makes it the perfect shield gas in welding applications.
When a welder initiates the electric arc during the welding process, the heat generated is intense and can easily reach thousands of degrees Celsius. At these high temperatures, the surrounding air—composed mostly of oxygen and nitrogen—can react with the molten metal and cause various defects in the weld.
This is where argon gas steps in. When argon gas is released from the welding argon hose, it displaces the surrounding air and forms a protective shield around the welding zone. This shield of argon gas prevents the reactive gases in the air from reaching the molten metal. As a result, the risk of oxidation, nitrogen absorption, and other harmful reactions is significantly reduced, leading to a cleaner and stronger weld.
Additionally, argon has a low thermal conductivity, which helps to concentrate the heat of the arc in the welding area. This can result in more efficient welding, particularly for materials that require high heat levels.
Despite its silent work, the role of argon in welding is highly significant. From improving weld quality to increasing efficiency, argon gas truly is the unsung hero of the welding world. The proper use and management of this resource, including the correct operation of the argon welding hose, are therefore crucial aspects of successful and efficient welding.
Types of Welding Argon Hoses
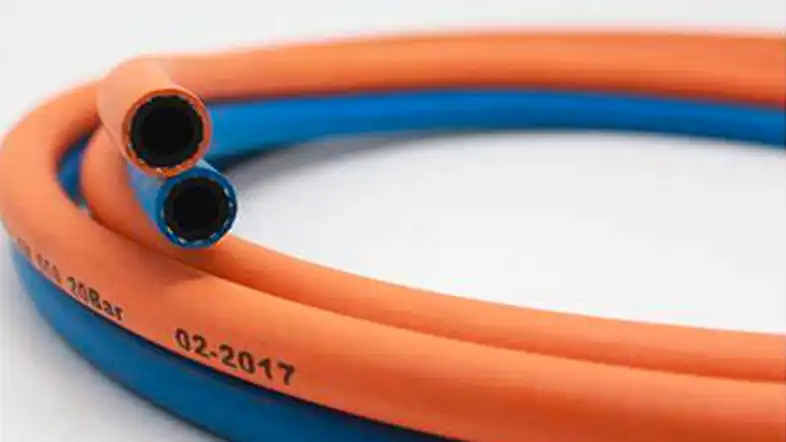
In the world of welding, the argon hose plays an indispensable role. As we have established, this humble component ensures a steady, controlled, and safe flow of argon gas from the cylinder to the welding torch. However, not all argon hoses are created equal. Depending on the specific requirements of the welding operation, different types of argon hoses may be employed. Let’s delve into a few common types you’re likely to encounter.
Rubber Argon Hoses
Rubber is one of the most common materials used in the production of argon hoses. Known for its excellent flexibility, resistance to abrasion, and relatively low cost, rubber hoses are widely used in various welding operations.
Despite their many advantages, rubber hoses are not immune to shortcomings. The material can degrade over time, especially under extreme temperatures and prolonged exposure to sunlight. Regular inspection and timely replacement of rubber argon hoses are thus crucial to maintaining safety and efficiency in welding operations.
PVC Argon Hoses
PVC (Polyvinyl Chloride) is another popular material choice for argon hoses. PVC hoses are typically lighter and more flexible than their rubber counterparts. They also demonstrate superior resistance to weather conditions, UV light, and chemicals, contributing to a longer lifespan.
However, PVC hoses might not be suitable for all welding operations. They tend to have a lower heat resistance than rubber hoses, which could potentially be a concern in high-temperature welding environments.
Hybrid Argon Hoses
Hybrid hoses represent the best of both worlds, combining the strength and heat resistance of rubber with the lightweight flexibility of PVC. These hoses are designed to withstand demanding welding conditions while offering a comfortable and manageable experience for the welder.
Choosing a hybrid hose can be a sound investment, especially for professional welders dealing with a wide range of welding operations. But bear in mind that the superior qualities of hybrid hoses often come with a higher price tag.
Stainless Steel Braided Argon Hoses
For welding operations that demand the highest degree of durability and safety, stainless steel braided argon hoses are often the go-to choice. Encased in a protective layer of stainless steel braiding, these hoses offer unmatched resistance to heat, abrasion, and physical damage.
They are especially favored in industrial settings where the hose may be exposed to rough handling or hazardous conditions. But, they may not be necessary for less demanding environments, such as home workshops or hobbyist applications.
In conclusion, there isn’t a “one-size-fits-all” type of welding argon hose. Each type has its unique strengths and weaknesses, and the best choice depends largely on your specific needs, operating conditions, and budget. It’s crucial to evaluate these factors thoroughly before making a purchase. Remember, a well-chosen hose will not only improve your welding efficiency but also contribute significantly to your safety.
Materials Used in Welding Argon Hoses
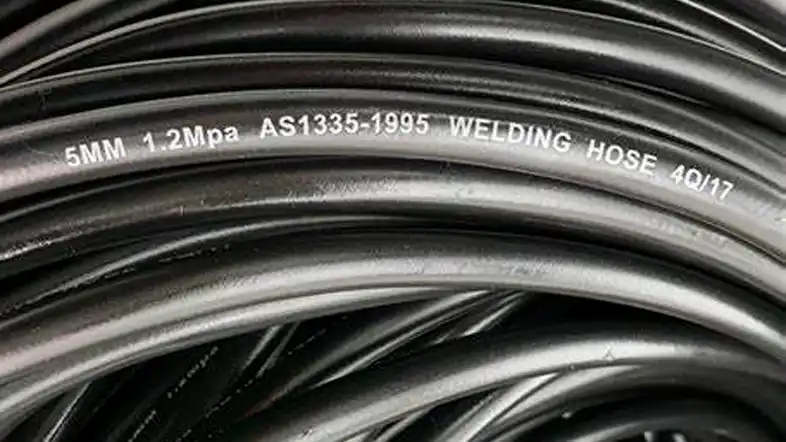
The welding argon hose is a vital component in the overall welding setup, responsible for transporting the protective argon gas from the cylinder to the welding torch. Argon, an inert gas, acts as a shield during the welding process to prevent oxidation and ensure a clean, strong weld. This critical task is dependent on the material composition of the hose, which can greatly impact the hose’s durability, flexibility, and performance.
Rubber Hoses
Rubber is one of the most commonly used materials in welding argon hoses due to its excellent durability and flexibility. Rubber hoses can withstand a wide range of temperatures and conditions, making them suitable for various welding environments. Furthermore, rubber has excellent resistance against abrasion and wear, which ensures that the hose remains functional and reliable over time.
One potential downside to rubber hoses is their weight. They are typically heavier than hoses made from other materials. This could be a consideration for welders who need to move their setup frequently or perform overhead welding tasks.
PVC Hoses
Polyvinyl Chloride, or PVC, is another material often used in the manufacturing of welding argon hoses. PVC hoses are light and flexible, which makes them an ideal choice for welders who require mobility. They also offer good resistance to chemicals and oils, contributing to their durability.
However, PVC hoses may not perform as well under extreme temperatures. Cold environments can cause the hose to become rigid, affecting its flexibility, while very high temperatures could potentially damage the hose material.
Hybrid Hoses
Hybrid hoses are a relatively new addition to the world of welding argon hoses, designed to combine the best qualities of rubber and PVC. These hoses offer the durability and temperature resistance of rubber with the lightweight and flexibility benefits of PVC.
Hybrid hoses are an excellent choice for welders who require a high degree of mobility and durability from their equipment. However, they are generally more expensive compared to rubber and PVC hoses, and their newness to the market means long-term performance data may not be readily available.
In conclusion, the material of the welding argon gas hose is a vital consideration when setting up a welding rig. Each material—whether it’s rubber, PVC, or a hybrid—has its strengths and weaknesses, and the best choice depends on the specific requirements of the welding task at hand. A thorough understanding of these materials can help you make an informed decision and ensure a safe, efficient, and high-quality welding process.
Argon Hose for TIG Welding: Ensuring Precision and Quality
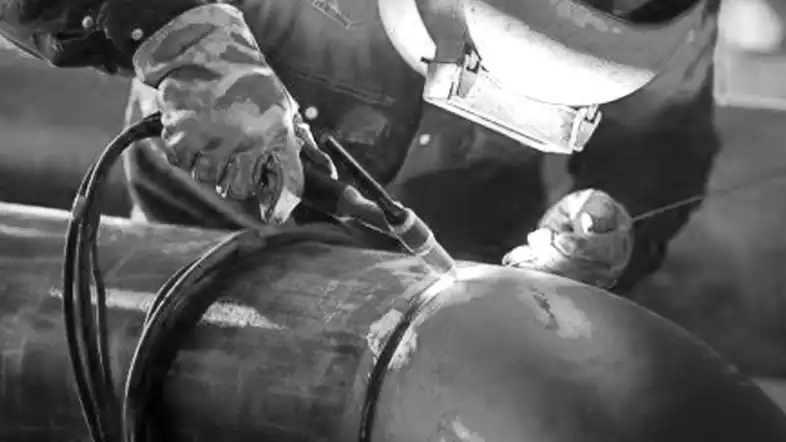
Tungsten Inert Gas (TIG) welding, also known as Gas Tungsten Arc Welding (GTAW), is a type of welding process where a non-consumable tungsten electrode delivers the current to the welding arc. One of the most critical components in this process is the argon gas, which is delivered through the argon hose. The argon gas plays a pivotal role in creating a clean and precise weld in TIG welding.
Argon in TIG Welding
In TIG welding, argon gas is utilized due to its inert characteristics. When heated, the argon gas forms a protective envelope around the weld area, shielding it from atmospheric contamination, such as oxygen and nitrogen. This protection is vital as the introduction of these gases into the weld area could cause poor weld quality, leading to defects like porosity or a weakened weld seam.
Argon’s inert properties also mean that it doesn’t interfere with the heat created by the welding arc. This ensures a stable and concentrated heat source, allowing for greater precision and control during the welding process. This is particularly important in TIG welding, as it is often used for detailed, precise work and high-quality welds.
The Argon Hose in TIG Welding
The argon hose in TIG welding serves as the conduit that delivers the argon gas from the gas cylinder to the welding torch. The hose must be designed to withstand the pressure of the gas and be resistant to any physical damage or deterioration over time.
When choosing an argon hose for TIG welding, it’s essential to consider the hose’s length and diameter. The length should be sufficient to allow for free movement around the work area, but not excessively long as it could lead to gas wastage or a drop in pressure. Similarly, the diameter of the hose affects the flow rate of the argon gas. A hose with a larger diameter will allow for a higher flow rate, which may be necessary for larger, more intensive TIG welding tasks.
Safety Considerations for Argon Hose in TIG Welding
As with all components in the welding process, safety is paramount when using an argon hose for TIG welding. Before each use, it’s important to inspect the hose for any signs of damage, such as cracks, cuts, or abrasions. Any damaged hoses should be replaced immediately to prevent gas leaks.
Moreover, always ensure that the hose fittings are securely attached to the gas cylinder and the welding torch. Loose fittings could result in gas leaks, which pose a safety risk. It’s also advisable to check for any signs of corrosion on the fittings, as this could weaken their structural integrity over time.
In conclusion, the argon hose plays a vital role in the TIG welding process. It’s a crucial link in the chain that leads to precise, high-quality welds. Therefore, understanding its function, ensuring its quality, and adhering to safety precautions are fundamental for any successful TIG welding operation.
Diameter and Length: How to Choose the Right One?
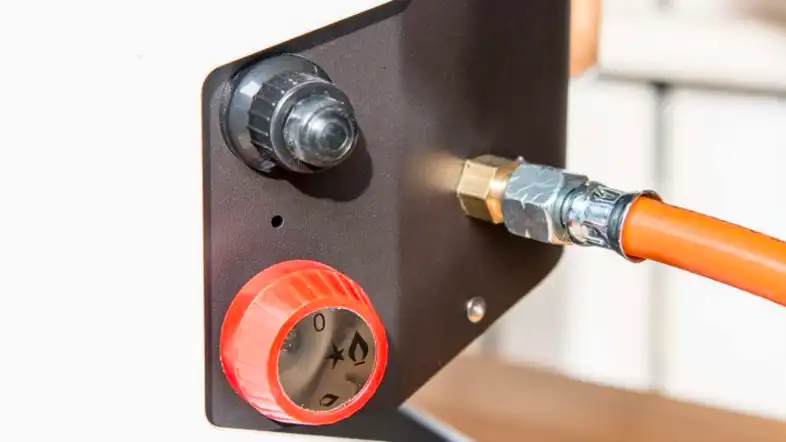
When it comes to choosing a argon gas hose welding, two critical factors to consider are the diameter and length of the hose. These elements greatly influence the efficiency and safety of your welding process.
Choosing the right size may seem like a trivial matter, but in the world of welding, it’s the small details that often have the most significant impact.
Understanding the Role of Diameter
The inner diameter of a welding argon hose refers to the width of the internal passageway that the argon gas flows through. This diameter is usually specified in inches or millimeters. The main rule of thumb is: the larger the diameter, the higher the volume of gas that can pass through the hose per unit of time.
However, the diameter is not just about the amount of gas. It also plays a significant role in maintaining the appropriate pressure of the gas as it reaches the welding torch.
If the diameter is too small, it might restrict the flow and create undue pressure, which can not only hamper the efficiency of the welding process but also pose safety risks. On the other hand, if the diameter is too large, it might lead to unnecessary gas wastage.
The Importance of Hose Length
The length of the welding argon hose is another crucial factor to consider. Generally, hoses come in a variety of lengths, and the we can customize the right welding argon hose to meet your specific needs.
If your welding operations involve a significant amount of movement or if your gas cylinder is positioned at a considerable distance from the welding area, you might require a longer hose. However, remember that the longer the hose, the greater the potential for pressure drop and gas loss, especially if the hose diameter is not appropriately matched.
Shorter hoses, in contrast, might be more suitable for compact welding stations where the gas cylinder and the welding torch are in close proximity. They are also preferable when high precision welding is needed, as they can provide a more stable and consistent gas flow.
Balancing Diameter and Length
Selecting the right diameter and length for your welding argon hose is all about balance. You must find a size that provides an optimal flow rate and pressure for your specific welding requirements while minimizing gas wastage. This balance often comes from understanding your welding needs, the type of welding you are performing, and the nature of the argon gas.
In conclusion, when choosing a welding argon hose, don’t overlook the importance of its diameter and length. It’s not a one-size-fits-all situation, so take the time to understand your needs and make an informed decision. After all, the right hose can contribute significantly to the efficiency, quality, and safety of your welding operations.
Fittings in Welding Argon Hoses
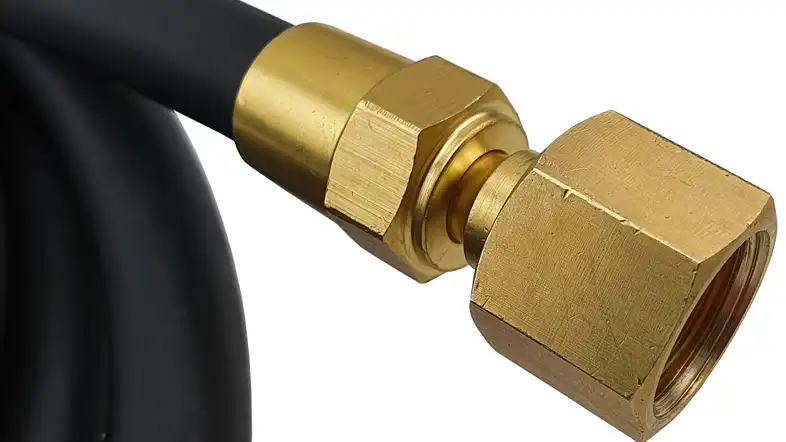
When discussing the welding argon hose, it is impossible not to mention one of its most important components – the fittings. These seemingly small components have a monumental task. They create a secure connection between the welding argon hose and the welding equipment, namely the argon gas cylinder and the welding torch. This unassuming part of the welding argon hose is responsible for ensuring a smooth, uninterrupted, and safe passage of the argon gas during the welding process.
Anatomy of Fittings
Fittings typically consist of two main components: the body and the nut. The body, which can be the male or female part, is the section that fits into or wraps around the hose. The nut is the part that secures the connection by tightening over the body. The design and specifications of the fittings should match those of the welding torch and the gas cylinder to ensure a seamless and safe connection.
Materials Used in Fittings
Fittings can be made from a variety of materials. Brass is a popular choice because of its durability, resistance to corrosion, and affordability. Stainless steel is another excellent option, providing added strength and corrosion resistance, although at a higher price point. The choice of fitting material can be influenced by factors such as the type of gas being used, the working pressure, and the welding environment.
Types of Fittings for Welding Argon Hoses
There are several types of fittings used in welding argon hoses. Some of the common ones include:
- Barbed Fittings: These have a ridged or barbed end that inserts into the hose, creating a tight grip. A clamp or ferrule is often used to secure the connection.
- Compression Fittings: These use a compression nut that tightens around the hose and fitting to create a leak-proof seal.
- Crimp Fittings: These require a crimping tool to deform the fitting, securing it to the hose.
- Quick-Disconnect Fittings: These allow for quick and easy connection and disconnection without the need for tools. They are particularly useful in situations where the hose needs to be frequently attached and detached.
Each type of fitting has its own advantages and disadvantages, and the choice depends on the specific requirements of the welding operation.
Importance of Correctly Fitted Fittings
Ensuring that your fittings are correctly attached is critical for a safe and efficient welding operation. Improperly fitted fittings can lead to gas leaks, reduced welding performance, and potential safety hazards. It is always recommended to check the fittings for any signs of wear or damage before use. Additionally, it’s essential to replace the fittings immediately if any issues are detected.
In conclusion, fittings in welding argon hoses may be small, but they are incredibly vital. Understanding their types, functions, and maintenance requirements can significantly enhance your welding operations’ safety and efficiency. Remember, in the world of welding, every component, no matter how small, plays a crucial part.
The Importance of Hose Inspection and Maintenance
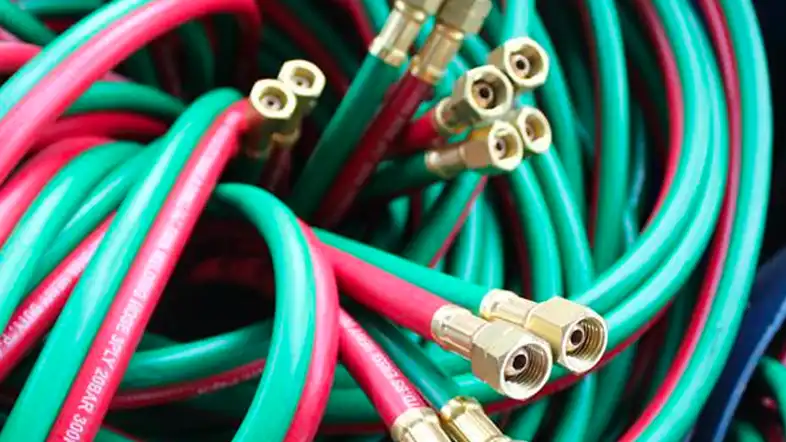
The welding argon hose serves as a vital lifeline in the welding process. It’s the conduit through which argon gas travels from the cylinder to the welding torch. The consistent and safe delivery of this gas is pivotal for successful and safe welding operations. Therefore, regular inspection and maintenance of the welding argon hose become of paramount importance.
Maintaining Optimal Performance
A well-maintained welding argon hose is critical for maintaining the optimal performance of your welding equipment. Over time, hoses can degrade due to wear and tear, exposure to harsh environmental conditions, or simply aging. These factors can cause issues like leaks or blockages, which can impact the flow rate of the argon gas. When the gas flow is compromised, the quality of the welds can suffer. Regular inspection and maintenance help identify and address these issues early, ensuring the hose continues to perform at its best.
Ensuring Safety
Beyond performance, safety is a major reason for regular hose inspection and maintenance. Argon is an asphyxiant. In high concentrations, it can displace oxygen in a room, creating a serious health hazard. A damaged or degraded hose can leak, leading to an increased concentration of argon gas in the air. Therefore, routine checks and timely repairs or replacements can significantly reduce the risk of accidents and maintain a safe working environment.
Extending the Lifespan of the Hose
Proper care and maintenance can extend the lifespan of your welding argon hose. By identifying minor issues early, you can prevent them from developing into major problems that can necessitate a complete hose replacement. Regular cleaning, proper storage, and appropriate handling can help preserve the condition of the hose, offering you better value for your investment.
Compliance with Regulations
In many jurisdictions, regular inspection and maintenance of welding equipment, including the argon hose, are not just good practice—they’re legal requirements. Routine checks can ensure compliance with these regulations and help avoid potential penalties or liabilities.
In conclusion, the importance of welding argon hose inspection and maintenance cannot be overstated. It’s not just about maintaining the quality of your welds—it’s about ensuring safety, extending the lifespan of your equipment, and keeping within the legal guidelines. Remember, a small investment in routine checks can save a lot of trouble down the line.
How to Purchase the Right Welding Argon Hose
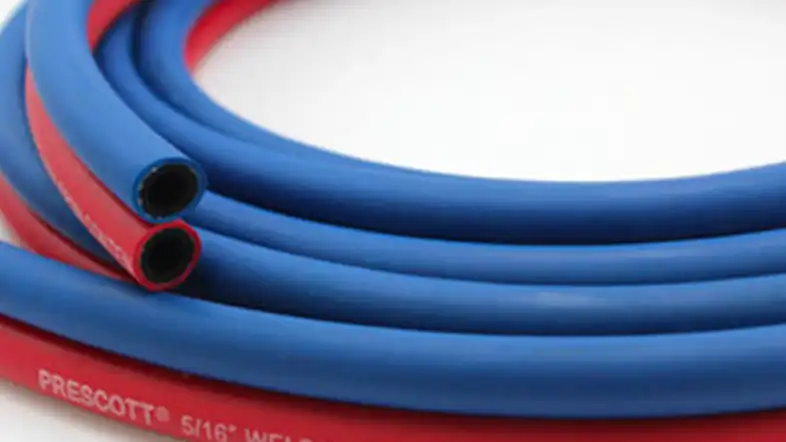
The welding argon hose is a vital part of any welding setup, enabling the smooth, controlled, and safe flow of argon gas from the cylinder to the welding torch. However, with numerous types, materials, and sizes available in the market, purchasing the right welding argon hose might appear overwhelming. This section aims to demystify the process and provide a clear roadmap for your buying decision.
Understand Your Requirements
Before venturing into the marketplace, the first step is to thoroughly understand your welding requirements. Consider the scale of your operations, the type of welding you’re involved in, the frequency of use, and the working conditions.
For instance, if you’re involved in heavy-duty welding or use your equipment frequently, you’ll require a hose made of robust material that can withstand the rigors of intense use. Alternatively, for occasional use or smaller-scale operations, a standard hose might suffice.
Consider the Material
Welding argon hoses are typically made from rubber, PVC, or a combination of materials (hybrids).
Rubber hoses, while slightly more expensive, offer excellent flexibility, durability, and resistance to heat and wear. They are ideal for heavy-duty or high-temperature welding applications.
PVC hoses are lighter and more affordable but may not offer the same level of durability or heat resistance as their rubber counterparts. They are suitable for light-duty or occasional use.
Hybrid hoses combine the best properties of both materials, offering good flexibility, durability, and heat resistance at a reasonable price.
Choose the Right Diameter and Length
The diameter and length of the hose significantly impact the flow rate of argon gas during the welding process. A hose with a larger diameter or longer length can deliver more gas but may also be heavier and more cumbersome to handle.
Ensure that the hose length is sufficient to comfortably reach your workspace from the gas cylinder without putting strain on the connections. However, avoid excessively long hoses as they can lead to reduced gas flow and potential tripping hazards.
Quality of Fittings
The fittings connect the hose to the gas cylinder and the welding torch. They should provide a tight, leak-free seal to ensure safe and efficient gas flow. Look for high-quality brass fittings as they offer excellent durability and resistance to corrosion.
Price and Warranty
Finally, consider your budget. While it might be tempting to opt for the cheapest option, remember that a welding argon hose is a long-term investment. A slightly more expensive, high-quality hose can save you money in the long run by offering better performance and a longer lifespan.
Also, look for hoses that come with a manufacturer’s warranty. This can provide peace of mind and protection against manufacturing defects.
In conclusion, purchasing the right welding argon hose involves careful consideration of your welding needs, the hose material, diameter, length, the quality of fittings, and your budget. With these factors in mind, you can confidently make an informed buying decision that enhances your welding efficiency and safety.
FAQs
What role does argon gas play in welding?
Argon gas creates a protective shield around the welding zone, preventing oxidation and enhancing the weld’s quality.
What factors should I consider when purchasing a welding argon hose?
Consider factors like the material of the hose, its diameter and length, the quality of fittings, and the price range.
How often should a welding argon hose be inspected?
A regular inspection is recommended, though the frequency might depend on the intensity of use and working conditions.
Why is safety important when using a welding argon hose?
Safety is paramount as any negligence could lead to leaks, causing accidents and posing health risks.
What are the common materials used in welding argon hoses?
Common materials include rubber, PVC, and hybrid materials.
Can I use any hose for argon gas in welding?
No, it’s crucial to use a hose specifically designed for argon gas to ensure safety and effectiveness.
Conclusion
The welding argon hose may seem like a minor component in the grand scheme of welding operations, but its role is indispensable. Whether you’re a professional welder or a hobbyist, understanding this tool can enhance your welding efficiency, safety, and overall work quality.
So, the next time you look at that hose connecting your welding torch and gas cylinder, remember, it’s more than just a conduit—it’s a lifeline for your welding operations.