In the industrial world, hydraulic systems play a pivotal role in powering heavy machinery and equipment. These systems rely on hydraulic hoses to transmit fluids under high pressure, enabling the smooth functioning of various applications.
However, one common and potentially dangerous issue that can occur is a “hydraulic hose blowout.” In this article, we will explore the causes, prevention measures, and solutions to tackle hydraulic hose blowouts.
Hydraulic systems are the backbone of many industries, powering everything from construction equipment to manufacturing machinery. However, these systems are not without their vulnerabilities, and one of the most critical issues that can arise is a hydraulic hose blowout.
In this article, we will delve into the causes, prevention, and solutions for this potentially dangerous problem.
What Are Hydraulic Hoses?
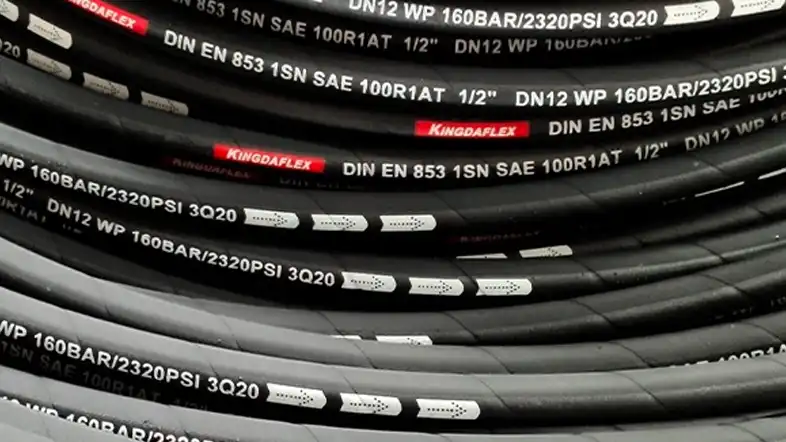
Hydraulic hoses are flexible tubes designed to transport hydraulic fluid between various components within a hydraulic system. These hoses are specifically engineered to withstand high-pressure conditions, making them crucial components in a wide range of industrial and machinery applications.
The primary function of hydraulic hoses is to transmit hydraulic power from one part of a hydraulic system to another. This power transmission enables the operation of machinery, equipment, and tools used in various industries such as construction, manufacturing, agriculture, and aviation.
Hydraulic hoses are typically constructed using several layers of materials, including an inner tube, reinforcement layers (usually made of high-strength materials like steel or synthetic fibers), and an outer cover. The inner tube is in direct contact with the hydraulic fluid and needs to be compatible with the type of fluid used in the system.
Due to their flexibility, hydraulic hoses can be routed through complex machinery and equipment, allowing for the efficient transmission of hydraulic energy to perform tasks such as lifting heavy loads, bending metal, operating construction equipment, and even controlling the landing gear of aircraft.
In summary, hydraulic hoses are essential components in hydraulic systems, serving as the conduits for the transmission of hydraulic fluid and power, enabling the operation of a wide range of industrial applications.
Importance in Industrial Applications
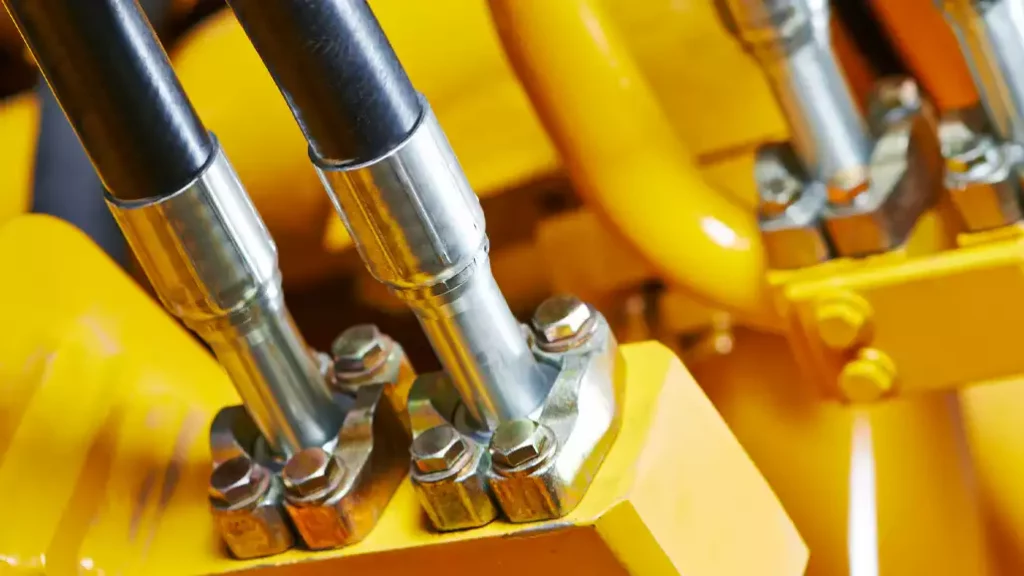
These hydraulic hoses are vital in industrial applications, where they transmit hydraulic power to perform tasks such as lifting heavy loads, bending metal, and even powering aircraft landing gear. Without reliable hydraulic hoses, many industrial processes would come to a standstill.
Here is a list of hydraulic hose applications.
Hydraulic hoses find diverse applications across various industries due to their ability to transmit hydraulic power efficiently and reliably. Some of the key hydraulic hose applications include:
Construction Equipment: Hydraulic hoses are extensively used in construction machinery such as excavators, bulldozers, cranes, and loaders. They enable precise control of equipment functions like lifting, digging, and moving heavy materials.
Agriculture: Hydraulic hoses play a vital role in agricultural machinery like tractors and combines. They power implements such as plows, seeders, and harvesters, making farming more efficient.
Manufacturing: Hydraulic systems are integral in manufacturing processes. Hydraulic hoses help control machinery like hydraulic presses, metal-forming machines, and injection molding equipment, ensuring precise and consistent results.
Aviation: Aircraft rely on hydraulic systems to operate landing gear, flaps, and brakes. Hydraulic hoses are critical components in these systems, providing the necessary power for safe takeoffs and landings.
Automotive Industry: Hydraulic hoses are used in vehicles for power steering and transmission systems. They enable smooth and responsive steering control and gear shifting.
Marine Applications: Hydraulic hoses are employed in marine equipment such as cranes, winches, and steering systems on boats and ships. They help with heavy lifting and navigation.
Mining: In mining operations, hydraulic hoses power drilling rigs, conveyors, and crushers. They facilitate the extraction and transport of minerals and ores.
Oil and Gas: Hydraulic hoses are used in drilling rigs, offshore platforms, and pipeline maintenance. They handle the high pressures and demanding conditions in the oil and gas industry.
Material Handling: Hydraulic hoses are utilized in material handling equipment like forklifts and conveyor systems. They enable the efficient movement and positioning of goods in warehouses and distribution centers.
Forestry: Logging machinery relies on hydraulic hoses for functions like tree cutting, log loading, and processing. These hoses ensure the safety and productivity of forestry operations.
Waste Management: Hydraulic hoses are employed in garbage trucks and compactors to handle waste collection and disposal efficiently.
Emergency Services: Hydraulic rescue tools, commonly known as “jaws of life,” used by firefighters and emergency responders, depend on hydraulic hoses to extricate people from vehicles after accidents.
Industrial Machinery: Hydraulic hoses are found in various industrial machines, including presses, metal shears, and hydraulic elevators, enhancing productivity and precision.
In each of these applications, hydraulic hoses are crucial components that enable the precise control of hydraulic power, contributing to the efficiency, safety, and reliability of diverse industrial processes and equipment.
Causes of Hydraulic Hose Blowouts
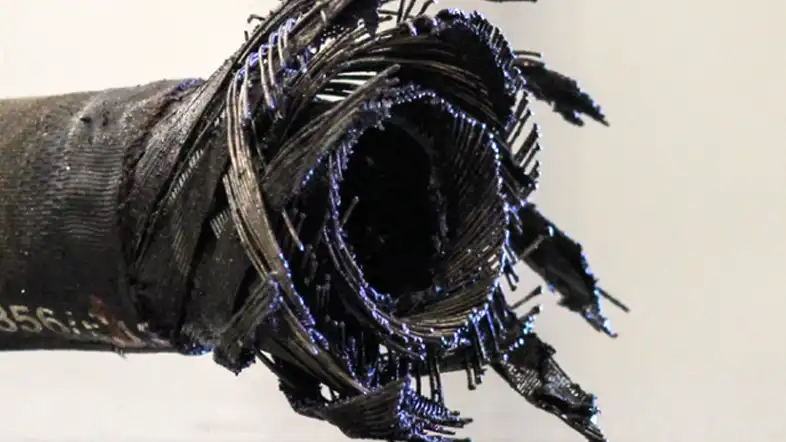
Age and Wear
One common cause of hydraulic hose blowouts is the natural aging and wear of the hose material. Over time, exposure to the elements, heat, and pressure can degrade the hose’s structural integrity.
Excessive Pressure
Running a hydraulic system at pressures beyond the hose’s rated capacity is a recipe for disaster. Excessive pressure can cause the hose to burst, leading to a blowout.
Abrasion and Friction
Hydraulic hoses can become damaged when exposed to abrasive materials or friction against nearby surfaces. This wear and tear can weaken the hose and eventually lead to a blowout.
High Temperatures
Extreme temperatures, whether too hot or too cold, can affect the hose’s material properties, making it more susceptible to failure.
Improper Installation
Incorrect hydraulic hose installation, including sharp bends, twists, or using the wrong fittings, can strain the hose and result in premature failure.
Here is the video showing the case of hydraulic hose blow out.
Preventing Hydraulic Hose Blowouts
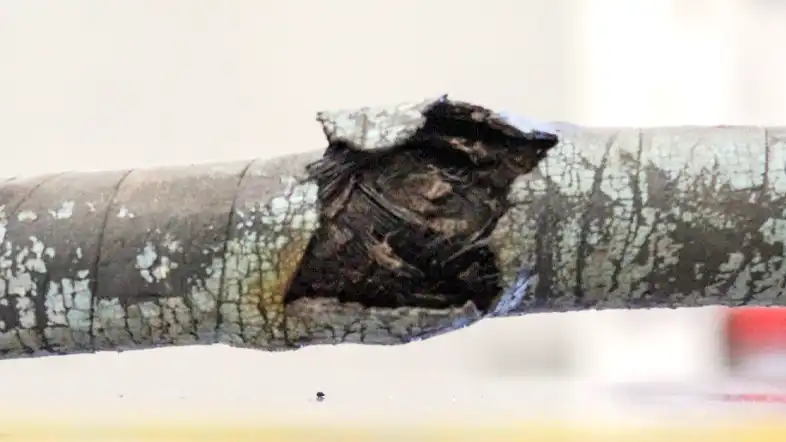
Regular Inspection and Maintenance
Frequent inspections and maintenance checks are essential to identify and replace worn-out hoses before they lead to blowouts.
Proper Pressure Control
Operating the hydraulic system within the recommended pressure limits is crucial to prevent hose blowouts.
Hose Protection Measures
Protective measures such as guards, sleeves, and routing to prevent abrasion can extend the lifespan of hydraulic hoses.
Correct Fluid Selection
Choosing the right hydraulic fluid and ensuring it’s compatible with the hose material is imperative in preventing chemical degradation.
Adequate Training
Training operators and maintenance personnel in the proper handling and care of hydraulic hoses is essential for overall safety.
Dealing with Hydraulic Hose Blowouts
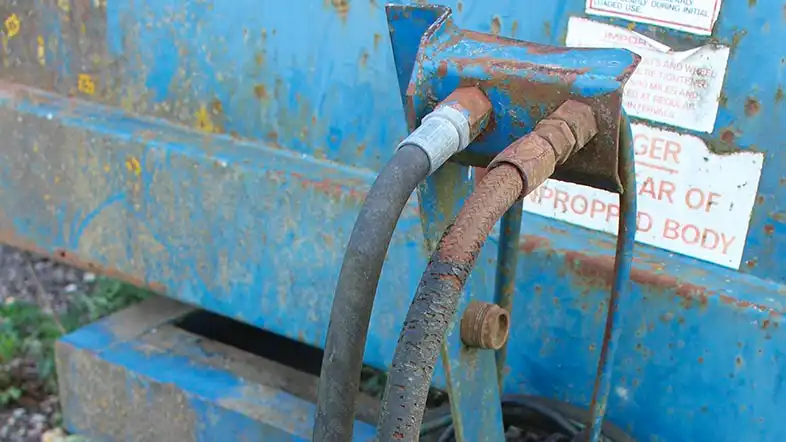
Safety First
In the event of a hose blowout, safety should be the top priority. Shut down the system immediately and ensure that everyone is a safe distance away from the affected area.
Isolating the System
Isolate the damaged hose by closing off valves and relieving pressure from the system to prevent further damage. You can get to know more about hydraulic hose isolation.
Replacing the Damaged Hose
Replace the blown-out hydraulic hose with a new one, ensuring it meets the system’s specifications and requirements. How to Replace A Hydraulic Hose? [Hydraulic Hose Replacement Guide Step by Step]
Post-Breakdown Evaluation
After resolving the issue, it’s essential to conduct a thorough evaluation to identify the root cause and implement preventive measures.
Conclusion
Hydraulic hose blowouts can pose significant risks to both personnel and equipment in various industries. By understanding the causes, taking preventive measures, and knowing how to respond in case of a blowout, you can ensure the safety and efficiency of hydraulic systems in your workplace.
FAQs
Can hydraulic hoses be repaired once they blow out?
It’s generally safer and more effective to replace a blown-out hydraulic hose rather than attempting repairs, as the integrity of the hose may be compromised.
How often should hydraulic hoses be inspected?
Regular inspections should be conducted according to the manufacturer’s recommendations, but a general rule of thumb is to inspect hoses every 500 hours of operation.
Can using a higher-rated hydraulic hose prevent blowouts
While using a higher-rated hose may provide additional safety margin, it’s crucial to ensure that all components in the hydraulic system are compatible and rated accordingly.
Are hydraulic hose blowouts preventable through maintenance alone?
While maintenance plays a vital role in prevention, other factors like proper installation, pressure control, and hose protection measures are equally important.
What should I do if a hydraulic hose blowout causes fluid leakage?
In case of fluid leakage, contain the spill using appropriate materials and follow environmental safety procedures to minimize damage.