When selecting fittings for piping systems, the choice between cast iron and malleable iron can significantly impact performance and longevity. Both materials have unique properties that cater to different applications. This blog post aims to clarify the distinctions, helping you make informed decisions.
Understanding the differences between these iron fittings is crucial for ensuring your piping system’s reliability. We’ll delve into their manufacturing processes, material characteristics, and ideal use cases, providing a comprehensive comparison to guide your selection.
What Are Cast Iron Fittings
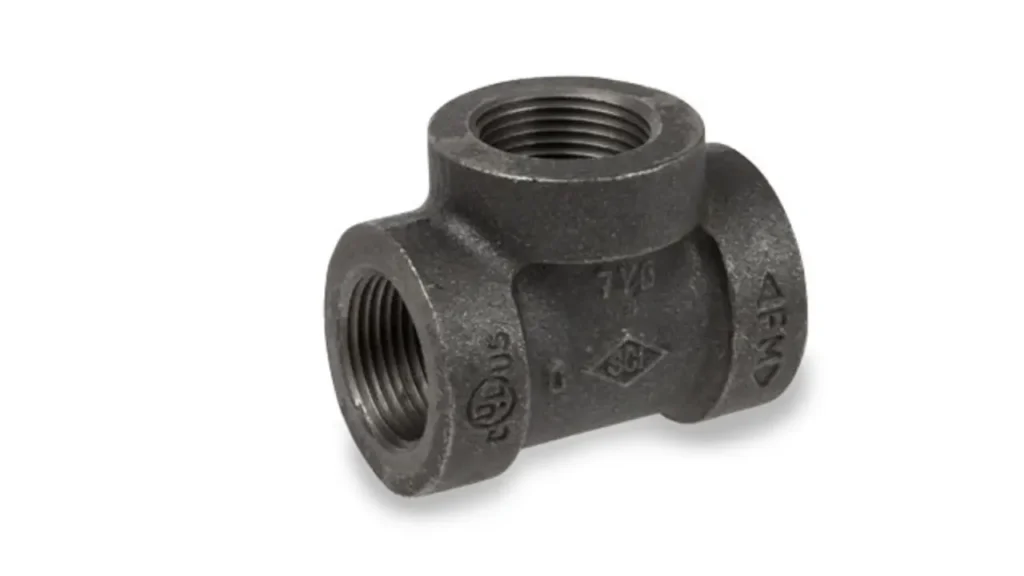
Cast iron fittings are pipe components made from cast iron, a ferrous alloy known for its strength and hardness. These fittings are created by pouring molten cast iron into molds, which then solidify into the desired shapes. Cast iron’s high carbon content contributes to its rigidity and resistance to deformation under pressure, making it suitable for applications where durability is crucial.
However, cast iron is also inherently brittle, meaning it can fracture under impact or tensile stress. Therefore, cast iron fittings are typically used in systems where these stresses are minimal, such as drain-waste-vent (DWV) systems, underground water pipes, and low-pressure applications. While strong in compression, its lack of ductility limits its use in applications with high vibration or shock.
What Are Malleable Iron Fittings
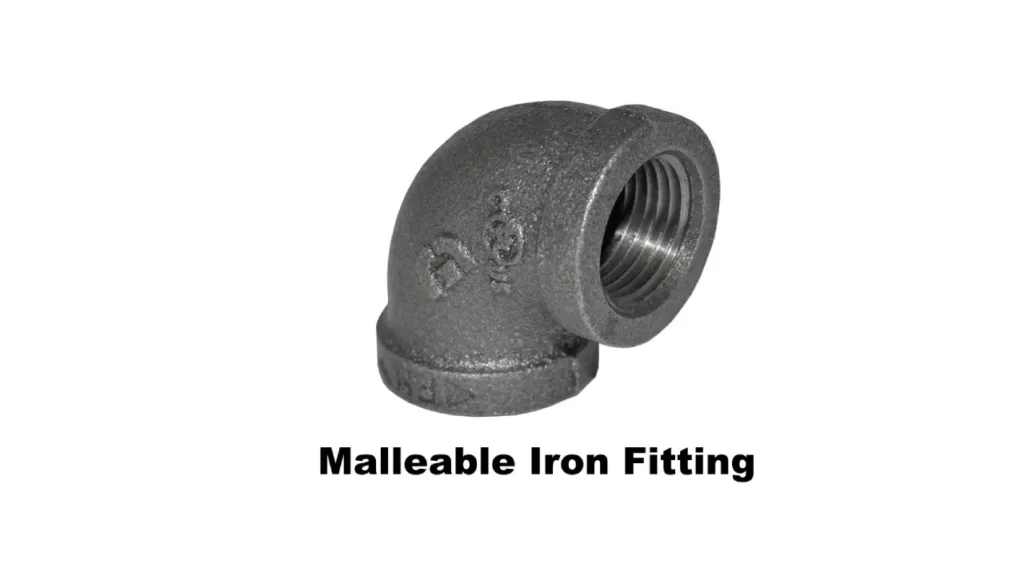
Malleable iron fittings are pipe fittings crafted from a specific type of cast iron that undergoes a unique heat treatment process known as “malleabilization.” This process transforms the initially brittle white cast iron into a more ductile and robust material. By heating the cast iron to high temperatures and holding it there for an extended period, the iron carbide within the material breaks down, forming temper carbon nodules. This structural change significantly enhances the fitting’s ability to withstand impact and tensile forces.
These fittings are widely favored in various piping systems due to their increased strength and flexibility compared to standard cast iron. They are particularly valuable in applications requiring resistance to mechanical stress and vibration, such as gas lines, plumbing, and industrial piping. The malleabilization process imparts a level of toughness that makes them reliable in demanding environments where durability and long-term performance are essential.
Cast Iron vs Malleable Iron Fittings
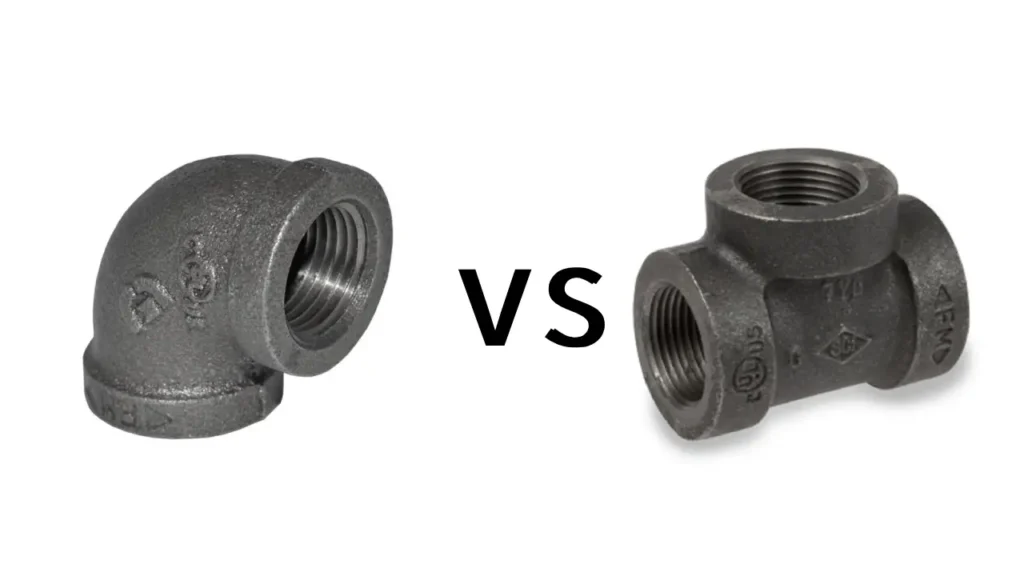
Cast Iron Fittings: In-Depth Analysis
Cast Iron Fitting Features:
High Compressive Strength: Cast iron’s inherent hardness makes it exceptionally resistant to compression forces. This is why it’s historically been used in applications where the primary stress is crushing or bearing a load.
Rigid and Hard Material: The high carbon content in cast iron creates a rigid, unyielding structure. While advantageous in some scenarios, this rigidity also contributes to its brittleness.
Relatively Inexpensive: Due to the simpler manufacturing process and readily available materials, cast iron fittings are generally more cost-effective than their malleable iron counterparts.
Good Corrosion Resistance in Specific Environments: Cast iron forms a protective oxide layer that can resist corrosion in certain environments, particularly in soil and wastewater. However, this resistance is limited and can break down in acidic or highly corrosive conditions.
Brittle, Prone to Fracture Under Tensile Stress or Impact: This is the most significant drawback. Tensile stress (pulling force) or sudden impacts can cause cast iron to fracture without significant deformation. This limits its use in applications where these forces are present.
Cast Iron Fitting Benefits:
- Cost-Effective for Low-Pressure Applications: For systems where pressure demands are low and impact is minimal, cast iron provides a budget-friendly solution.
- Excellent for Drain, Waste, and Vent (DWV) Systems: The rigid nature and corrosion resistance to wastewater make cast iron ideal for DWV systems, where structural integrity and longevity are crucial.
- Suitable for Underground Applications Due to Compressive Strength: Its ability to withstand soil pressure makes cast iron suitable for underground pipes, where it can bear significant loads.
Cast Iron Fitting Applications:
Drain, Waste, and Vent (DWV) Systems: This remains the primary application, leveraging its resistance to wastewater and structural stability.
Sewer and Water Mains: Historically, cast iron was widely used for water and sewer mains due to its compressive strength and availability.
Low-Pressure Piping Systems: Any system where pressure is low and impact is minimal can benefit from the cost-effectiveness of cast iron.
Fire Sprinkler Systems (in Some Cases): Depending on local codes and pressure requirements, cast iron may be used in certain fire sprinkler systems.
Cast Iron Fitting Installation Methods:
Typically Uses Hub-and-Spigot Connections with Lead and Oakum or Compression Gaskets: This traditional method involves packing oakum (hemp fiber) and pouring molten lead into the joint to create a seal. Modern installations often use compression gaskets.
Some Threaded Cast Iron Fittings Exist: While less common, threaded cast iron fittings are available for specific applications.
Requires Careful Handling to Avoid Impact Damage: Due to its brittleness, cast iron must be handled with care during transportation and installation to prevent fractures.
Corrosion Resistance:
Good resistance to soil and wastewater, but limited in acidic environments.
Temperature Resistance:
Suitable for moderate temperatures, but not for extreme heat.
Pressure Rating:
Lower pressure rating compared to malleable iron, limiting its use in high-pressure systems.
Manufacturing Process:
Molten iron is poured into molds, allowed to cool, and then removed. This simple process contributes to its lower cost.
Malleable Iron Fittings: In-Depth Analysis
Features:
- High Tensile Strength and Ductility: The malleabilization process transforms the brittle white cast iron into a material with significantly improved tensile strength and ductility.
- Resistant to Impact and Vibration: The increased ductility allows malleable iron to absorb impact and vibration, making it more resilient in demanding applications.
- Enhanced Corrosion Resistance, Especially When Galvanized: Galvanization provides a robust protective layer, significantly enhancing corrosion resistance, especially in outdoor and corrosive environments.
- Suitable for High-Pressure and High-Temperature Applications: The increased strength and thermal stability make malleable iron suitable for high-pressure and high-temperature systems.
- Stronger Than Standard Cast Iron: The heat treatment process results in a material that is significantly stronger and more durable than standard cast iron.
Malleable Iron Fitting Benefits:
Reliable in Demanding Applications: The enhanced strength and ductility make malleable iron fittings reliable in applications where stress, impact, and vibration are present.
Long Service Life: The combination of strength, corrosion resistance, and thermal stability contributes to a long service life, reducing maintenance and replacement costs.
Versatile for Various Piping Systems: The wide range of sizes, shapes, and thread configurations makes malleable iron fittings suitable for diverse piping systems.
More Forgiving During Installation Than Cast Iron: The ductility of malleable iron makes it more forgiving during installation, reducing the risk of fractures.
Malleable Iron Fitting Applications:
Gas Lines: The high strength and leak-proof connections make malleable iron ideal for gas lines, where safety is paramount.
Plumbing Systems: Malleable iron is used in various plumbing applications, including water and steam lines.
Hydraulic Systems: The high-pressure rating makes malleable iron suitable for hydraulic systems.
Industrial Piping: Malleable iron is widely used in industrial piping systems, where durability and reliability are essential.
High-Pressure Steam and Air Lines: The high temperature and pressure capabilities make malleable iron suitable for steam and air lines.
Malleable Iron Fitting Installation Methods:
Primarily Threaded Connections (NPT): Threaded connections are the standard for malleable iron fittings, allowing for easy assembly and disassembly.
Easier to Install and Disassemble: Threaded connections simplify installation and maintenance.
Requires Pipe Thread Sealant for Leak-Proof Connections: Pipe thread sealant (Teflon tape or pipe dope) is essential for creating leak-proof connections.
Corrosion Resistance:
Excellent, especially when galvanized, making it suitable for outdoor and corrosive environments.
Temperature Resistance:
High temperature capabilities, making it suitable for steam and other high-temperature applications.
Pressure Rating:
Higher pressure rating than cast iron, allowing for use in high-pressure systems.
Manufacturing Process:
White cast iron is heat-treated (malleabilized) in a controlled environment. This process transforms the microstructure of the material, resulting in improved properties.
Microstructure and Material Transformation:
Cast Iron: Its microstructure is characterized by graphite flakes, which contribute to its brittleness. These flakes act as stress concentrators, making the material prone to cracking. The carbon is primarily in the form of graphite flakes.
Malleable Iron: The heat treatment process (malleabilization) transforms the graphite flakes into temper carbon nodules. These nodules are more rounded and dispersed, reducing stress concentration and significantly improving ductility and impact resistance. The carbon is in the form of nodules.
Joint Integrity and Sealing:
Cast Iron: Hub-and-spigot joints, while robust, can be more challenging to seal effectively, especially over time. Lead and oakum joints require skilled labor and can be susceptible to leaks due to ground movement or thermal cycling.
Malleable Iron: Threaded connections, when properly sealed with Teflon tape or pipe dope, provide reliable and leak-proof joints. The tapered threads create a mechanical seal, and the sealant fills any remaining gaps. This makes them far more reliable in situations with vibrations.
Weight and Handling:
Cast Iron: Generally heavier than malleable iron fittings of the same size, making them more cumbersome to handle and install. This can increase labor costs and the risk of injury.
Malleable Iron: Lighter and easier to handle, contributing to faster and more efficient installation. This is a significant advantage in applications where space is limited or where frequent assembly and disassembly are required.
Environmental Considerations:
Cast Iron: While durable, the traditional lead and oakum jointing method poses environmental concerns due to lead leaching. Modern gaskets have helped mitigate this.
Malleable Iron: Galvanized malleable iron fittings offer enhanced corrosion resistance, reducing the need for frequent replacements and minimizing waste.
Standards and Codes:
Both types of fittings are subject to industry standards and codes, which vary depending on the application and region. These standards specify material properties, dimensions, and testing requirements. It’s crucial to select fittings that comply with the relevant standards to ensure safety and performance.
Cost vs. Long-Term Value:
While cast iron may have a lower initial cost, malleable iron’s longer service life and reduced maintenance requirements can provide better long-term value, especially in demanding applications. You must consider total cost of ownership.
Applications in specific industries:
Oil and Gas: Malleable iron is heavily used due to its ability to handle high pressures and corrosive environments.
Construction: Cast iron is still used in DWV systems, while malleable iron is used for gas lines and other critical applications.
Manufacturing: Malleable iron is used in hydraulic and pneumatic systems.
Agriculture: Both are used depending on the needed application. Cast iron for drainage, and malleable iron for higher pressure water lines.
Here is a chart showing the differences between cast iron fittings and malleable iron fittings in the following:
Feature | Cast Iron Fittings | Malleable Iron Fittings |
Material | Cast Iron | Malleable Iron (Heat-treated cast iron) |
Strength | High compressive strength, brittle | High tensile strength, ductile |
Impact Resistance | Low | High |
Corrosion Resistance | Moderate | High (especially galvanized) |
Temperature Resistance | Moderate | High |
Pressure Rating | Lower | Higher |
Applications | DWV, sewer, water mains | Gas lines, plumbing, hydraulic, industrial |
Installation | Hub-and-spigot, threaded (less common) | Threaded (NPT) |
Cost | Lower | Higher |
Manufacturing | Casting | Casting + heat treatment |
Ductility | Brittle | Ductile |
Weight | Heavier | Lighter |
Joint Integrity | More challenging to seal | Easier to seal with threaded connections |
Environmental Impact | Potential lead concerns with traditional joints | More environmentally friendly with galvanization |
Long-Term Value | Lower initial cost | Higher long-term value due to durability |
This chart provides a quick reference for comparing the two types of fittings, making it easier to choose the right one for your specific needs. Remember to consider factors like pressure, temperature, corrosion resistance, and installation requirements when making your selection.
Conclusion
The distinction between cast iron and malleable iron fittings lies primarily in their material properties. Cast iron, while strong, is brittle, whereas malleable iron gains ductility through heat treatment, making it more resilient. Choosing the right fitting depends on the specific demands of your application.
For those requiring durable and reliable malleable iron fittings, Kingdaflex offers a wide selection of wholesale hydraulic fittings. We provide products that meet stringent industry standards, ensuring longevity and performance in your piping systems.
Elevate your projects with high-quality malleable iron fittings. Contact Kingdaflex today to explore our wholesale options and find the perfect fittings for your hydraulic needs.