Connecting an air hose to an air compressor is a fundamental task for anyone using pneumatic tools or equipment. A secure and leak-free connection is crucial for efficient operation and safety. Improper connections can lead to pressure loss, reduced tool performance, and potential hazards. Understanding the correct procedure ensures optimal functionality and longevity of both the compressor and the hose.
This blog post will guide you through the essential steps for connecting an air hose to an air compressor. We’ll cover the necessary tools, safety precautions, and best practices to ensure a reliable connection. Whether you’re a seasoned professional or a first-time user, this guide will provide the knowledge needed to connect your air hose safely and effectively.
What Is Air Hose
An air hose is a flexible tube designed to transport compressed air from an air compressor to various pneumatic tools and equipment. These hoses are essential for powering tools like air wrenches, nail guns, spray guns, and tire inflators, enabling efficient operation in industrial, automotive, and domestic settings. They are engineered to withstand the pressures generated by air compressors and deliver a consistent airflow to the connected tools.
Air hoses are typically made from materials like rubber, PVC, polyurethane, or hybrid blends, each offering distinct advantages in terms of flexibility, durability, and resistance to abrasion, chemicals, and temperature variations. The selection of the appropriate hose material and size is crucial for ensuring efficient and safe operation, preventing pressure drops, and maximizing the performance of pneumatic tools.
How to Connect Air Hose to Compressor
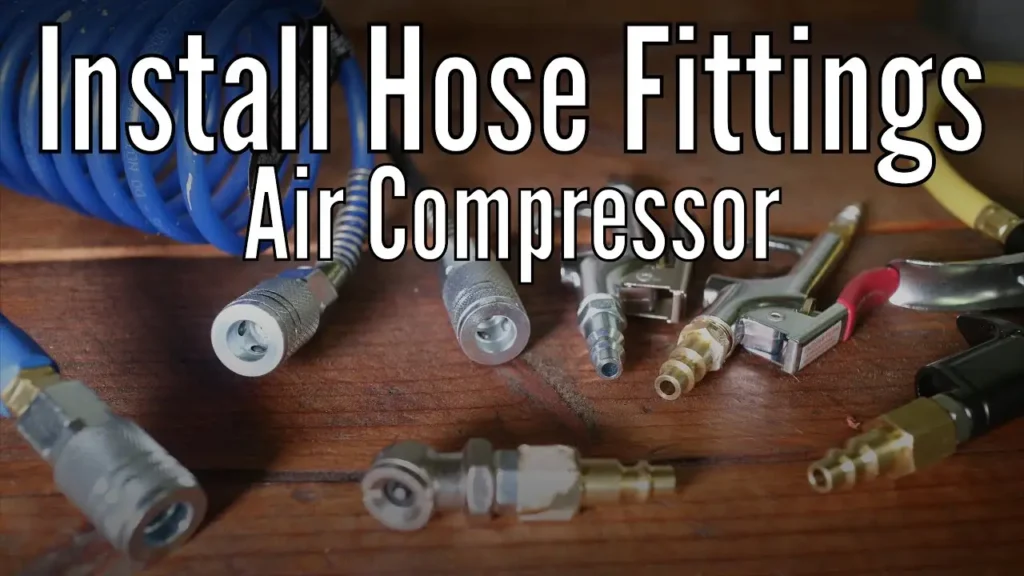
Connecting an air hose to an air compressor is a fundamental task for anyone using pneumatic tools. Proper connection ensures a secure, leak-free seal, preventing pressure loss and maintaining consistent airflow. Here’s a step-by-step guide to connecting an air hose to an air compressor.
Step 1: Preparing the Compressor and Hose
Before connecting the air hose, ensure the air compressor is turned off and unplugged to prevent accidental activation. This safety precaution is crucial to avoid injury or damage during the connection process. Inspect both the compressor’s outlet and the hose’s inlet for any signs of damage, such as cracks, rust, or debris, which could compromise the connection. Clean any dirt or debris with a clean cloth.
Proper preparation ensures a safe and effective connection. Inspect all parts, and ensure they are clean. Any damage, or debris, could cause a leak.
Check the compressor’s outlet and the hose’s inlet for compatibility. Most air compressors use quick-connect fittings, which allow for easy and secure connections. Ensure the hose has the correct type of fitting to match the compressor’s outlet. If needed, use an adapter to bridge any compatibility issues. Verify that the hose’s inner diameter (ID) and length are suitable for the intended application and tool requirements.
Selecting the correct fittings, and ensuring compatibility, is very important. Any incorrect fittings will cause leaks, and could cause damage to the compressor.
Step 2: Attaching the Quick-Connect Fitting
If both the compressor and hose have quick-connect fittings, align the hose’s male fitting with the compressor’s female fitting. Push the male fitting firmly into the female fitting until you hear a click, indicating a secure connection. Some quick-connect fittings have a locking mechanism that requires you to pull back on the collar before pushing in the male fitting. Ensure the locking mechanism engages properly to prevent accidental disconnection.
A secure quick-connect fitting is essential for preventing leaks. Ensure that the fitting is fully engaged and locked.
For threaded connections, wrap Teflon tape around the male threads to create a leak-free seal. Thread the hose fitting onto the compressor’s outlet, turning it clockwise until it’s snug. Avoid over-tightening, as this can damage the threads. Use a wrench to tighten the connection if necessary, but be careful not to overtighten.
Threaded connections require careful tightening to prevent leaks. Too tight, or too loose, can cause issues.
Step 3: Testing the Connection
After connecting the air hose, turn on the air compressor and allow it to build pressure. Listen for any hissing sounds or feel for air leaks around the connection point. If you detect any leaks, turn off the compressor, unplug it, and re-tighten the connection or inspect for damage. Apply a soapy water solution to the connection point to check for leaks; bubbles will form if there’s a leak.
Testing the connection is crucial for ensuring a leak-free seal. Any leak should be addressed before using the air compressor.
Once you’ve confirmed a leak-free connection, test the airflow by attaching a pneumatic tool to the hose and operating it. Ensure the tool receives adequate pressure and airflow for proper operation. If there are any issues with airflow or pressure, check the hose’s ID and length, as well as the compressor’s output (CFM).
Testing with a tool ensures proper airflow. Any issues with the tool, could indicate a problem with the hose, or the connection.
Air Compressor Hose Connection Types
Connecting air hoses to compressors requires understanding the various connection types to ensure a secure and leak-free seal. Different connection types offer varying levels of convenience and compatibility. Here’s a breakdown of common air compressor hose connection types.
Quick-Connect Fittings
Quick-connect fittings are the most common type of connection for air compressor hoses, prized for their ease of use and speed. These fittings consist of a male plug and a female coupler, allowing for rapid connection and disconnection without the need for tools. The male plug is inserted into the female coupler, and a locking mechanism secures the connection, preventing accidental disconnections during operation.
These fittings are widely used in both professional and DIY settings due to their convenience and efficiency. Quick-connect fittings are available in various sizes and materials, including brass, steel, and plastic, to suit different applications and pressure requirements. Their design allows for quick tool changes and hose extensions, improving productivity and ease of use.
However, it’s crucial to ensure compatibility between the male and female fittings, as different manufacturers may use slightly varying designs. Regular inspection and maintenance are essential to prevent leaks and ensure proper functioning. Quick-connect fittings can wear over time, leading to air leaks or difficulty in connecting and disconnecting.
Threaded Fittings
Threaded fittings, also known as screw-on fittings, provide a secure and reliable connection for air compressor hoses. These fittings typically feature male and female threads, which are screwed together to create a tight seal. Threaded fittings are commonly used in heavy-duty applications or when a more permanent connection is required. They offer excellent resistance to pressure and vibration, ensuring a leak-free connection.
These fittings are often made from durable materials like brass or steel, which can withstand high pressures and harsh environments. Threaded fittings require the use of Teflon tape or thread sealant to create a proper seal and prevent leaks. They offer a robust connection that is less prone to accidental disconnection compared to quick-connect fittings.
However, threaded fittings require more time and effort to connect and disconnect compared to quick-connect fittings. They also require the use of tools, such as wrenches, to tighten and loosen the connections. It’s crucial to ensure the threads are properly aligned and tightened to prevent leaks and damage to the fittings.
Barb Fittings
Barb fittings are another type of connection used for air compressor hoses, particularly in low-pressure applications or when flexibility is crucial. These fittings feature a barbed end that is inserted into the hose, and a clamp or ferrule is used to secure the connection. Barb fittings are often used with flexible hoses, such as polyurethane or rubber hoses, which can easily expand and contract around the barbs.
These fittings are relatively inexpensive and easy to install, making them a popular choice for DIY projects and light-duty applications. Barb fittings offer good flexibility and can accommodate slight variations in hose size. However, they may not be suitable for high-pressure applications or when a very secure connection is required.
It’s crucial to use appropriate clamps or ferrules to secure the hose to the barb fitting and prevent leaks. Regular inspection and maintenance are essential to ensure the connection remains tight and leak-free. Barb fittings can loosen over time due to vibration or hose movement, leading to air leaks and reduced performance.
Conclusion
In conclusion, properly connecting an air hose to an air compressor is crucial for safe and efficient operation. Ensuring a secure, leak-free connection prevents pressure loss and maintains consistent airflow to your pneumatic tools. Following the correct steps and using appropriate fittings guarantees optimal performance and minimizes potential hazards.
Regularly inspecting and maintaining your air hose connections is essential for longevity and safety. Checking for wear, damage, or leaks prevents unexpected failures and ensures consistent pressure delivery. Adhering to manufacturer guidelines and using quality components contributes to a reliable and efficient air compressor system.
For a wide range of durable and reliable air hoses designed for seamless compressor connections, choose Kingdaflex. We offer wholesale options with various sizes and materials to meet your specific needs. Contact us today to explore our product offerings and ensure your air compressor systems operate at peak performance.