The hydraulic hose crimping machine is an indispensable tool in various industries, ensuring secure and reliable connections for hydraulic systems. As technology advances, understanding the latest developments in these machines becomes crucial for optimizing operations and maintaining safety. This guide aims to provide a comprehensive overview of hydraulic hose crimping machines in 2025.
We’ll explore the latest advancements, best practices, and essential considerations for selecting and operating these machines. Whether you’re a seasoned professional or new to the field, this guide will equip you with the knowledge to make informed decisions1 and enhance your hydraulic system’s performance.
What Is a Hydraulic Hose Crimping Machine
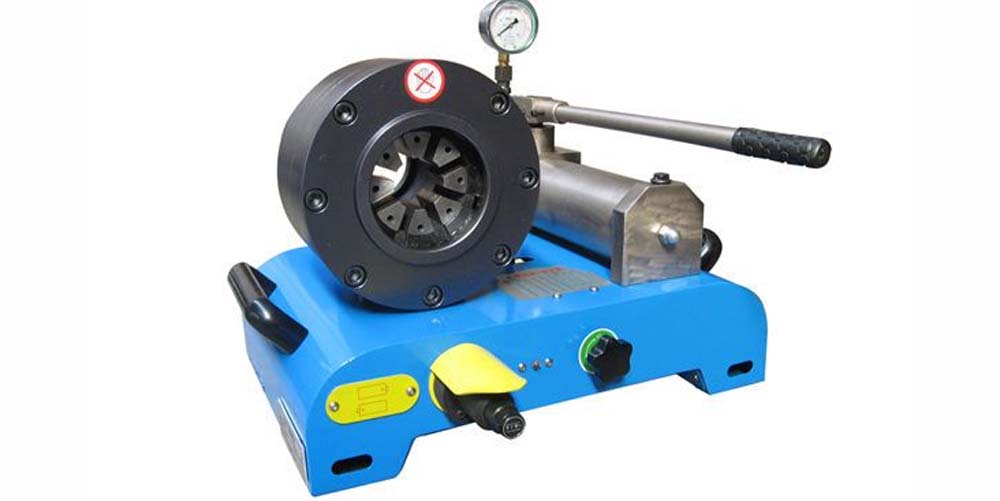
The hydraulic hose crimping machine, also named hydraulic hose crimper, is the hydraulic hose crimping tool used to connect the two ends of two hydraulic hoses together.
Of course, the hydraulic hose crimping machine can also be used for you to connect two wires, cables, tubes, and also other flexible materials, so the hydraulic hose crimping machine is an important tool for you to handle hydraulic hose connection for the hydraulic line.
The hydraulic hose crimping machine can help you assemble the hydraulic hoses to the hydraulic-powered machinery to transfer the water-based liquid or petroleum-based liquid for the construction machinery that includes the hydraulic system.
How Does A Hydraulic Hose Crimping Machine Work
A hydraulic hose crimping machine works by the pressurized liquid to drive a piston into a cylinder where it compresses a hydraulic hose die against the hydraulic hose.
The hydraulic hose crimping machine can connect the hydraulic hose and hydraulic hose fittings, making them connected firmly without leaving any space for leaking hydraulic fluids.
The hydraulic hose crimper dies can form a permanent bend in the location of the contact area; the die spring will be backed up, leaving a permanently bent section of the hydraulic hose end to make it a conjoined well.
Types of Hydraulic Hose Crimping Machine
Hydraulic hose crimping machines are essential tools for securely attaching fittings to hydraulic hoses. Choosing the right machine ensures efficient and reliable connections. These machines vary in design and functionality to cater to different industrial needs. We will explore the main types of hydraulic hose crimping machines, highlighting their features and benefits.
Manual Hydraulic Hose Crimping Machines
Manual hydraulic hose crimping machines are operated by hand, making them portable and suitable for on-site repairs and low-volume production. They typically feature a hand-operated pump that generates the necessary hydraulic pressure to crimp fittings onto hoses. These machines are compact and require no electrical power, making them ideal for field applications where portability is crucial.
Features include a simple, robust design, ease of use, and low maintenance requirements. Benefits include portability, cost-effectiveness for small operations, and the ability to perform quick repairs in remote locations. Manual crimpers are often preferred for their simplicity and reliability in situations where electrical power is unavailable or impractical.
Electric Hydraulic Hose Crimping Machines
Electric hydraulic hose crimping machines use an electric motor to generate hydraulic pressure, offering increased speed and efficiency compared to manual machines. They are suitable for medium to high-volume production and applications requiring consistent crimping force. These machines are typically bench-mounted and offer greater precision and control over the crimping process.
Features include automated crimping, adjustable crimping force, and digital control panels for precise settings. Benefits include increased productivity, consistent crimping quality, and reduced operator fatigue. Electric crimpers are ideal for workshops and production facilities where efficiency and precision are paramount.
Pneumatic Hydraulic Hose Crimping Machines
Pneumatic hydraulic hose crimping machines use compressed air to generate hydraulic pressure, providing a balance of speed and power. They are suitable for applications requiring high-volume production and consistent crimping force. These machines are often used in industrial settings where compressed air is readily available.
Features include fast crimping cycles, adjustable crimping force, and compatibility with automated production lines. Benefits include high productivity, consistent crimping quality, and reduced operator fatigue. Pneumatic crimpers are ideal for manufacturing environments where speed and reliability are crucial.
Automated Hydraulic Hose Crimping Machines
Automated hydraulic hose crimping machines are designed for high-volume production and integration into automated manufacturing lines. They feature advanced control systems and robotic arms to automate the crimping process, minimizing manual intervention. These machines offer the highest level of precision and efficiency, ensuring consistent and reliable crimping results.
Features include robotic automation, programmable crimping sequences, and integrated quality control systems. Benefits include maximum productivity, consistent crimping quality, and reduced labor costs. Automated crimpers are ideal for large-scale manufacturing operations where efficiency and precision are critical for maintaining production output and quality standards.
How to Crimp Hydraulic Hose Fittings?
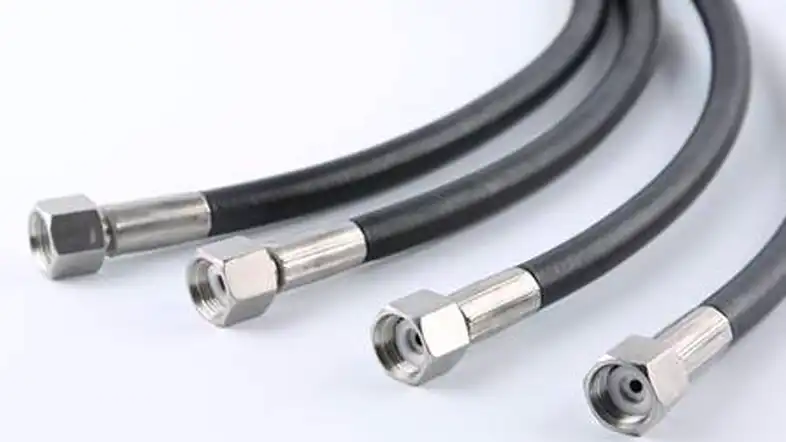
Crimping hydraulic hose fittings correctly is crucial for ensuring leak-free and reliable hydraulic connections. Proper crimping prevents hose failures and maintains system integrity. We’ll guide you through the essential steps to crimp hydraulic hose fittings accurately.
Step 1: Prepare the Hydraulic Hose and Fittings
Begin by selecting the correct hydraulic hose and fittings for your application. Ensure they are compatible in terms of size, pressure rating, and material. Inspect the hose and fittings for any damage or defects. Cut the hydraulic hose to the required length using a specialized hose cutter, ensuring a clean, square cut to prevent leaks and ensure proper fitting insertion.
Step 2: Mark the Crimping Length
Measure and mark the crimping length on the hydraulic hose. This mark indicates the area where the fitting will be crimped onto the hose. Consult the fitting manufacturer’s specifications for the correct crimping length. Accurate marking ensures the fitting is properly seated and crimped, preventing leaks and ensuring a secure connection.
Step 3: Insert the Hose into the Fitting
Carefully insert the hydraulic hose into the fitting until it reaches the marked crimping length. Ensure the hose is fully inserted and properly aligned with the fitting. This step is crucial for achieving a secure and leak-free connection. Proper insertion ensures the fitting grips the hose correctly during the crimping process.
Step 4: Set Up the Crimping Machine
Select the correct die set for the hydraulic hose and fitting size. Install the dies into the crimping machine according to the manufacturer’s instructions. Adjust the crimping machine’s settings to the required crimping diameter, based on the fitting manufacturer’s specifications. Proper setup of the crimping machine ensures accurate and consistent crimping results.
Step 5: Crimp the Fitting
Position the hydraulic hose and fitting assembly into the crimping machine. Activate the crimping machine to compress the dies and crimp the fitting onto the hose. Apply consistent pressure and ensure the fitting is crimped evenly around the hose. After crimping, inspect the connection to ensure it is secure and meets the manufacturer’s specifications.
Step 6: Verify the Crimped Connection
After crimping, verify the connection’s integrity by measuring the crimped diameter and comparing it to the manufacturer’s specifications. Inspect the crimped area for any signs of damage, such as cracks or deformations. Perform a pull test, if required, to ensure the fitting is securely attached to the hose. Accurate verification ensures a reliable and leak-free hydraulic connection.
Here is a short video showing the hydraulic fitting crimping process below:
How to Crimp a Hydraulic Hose
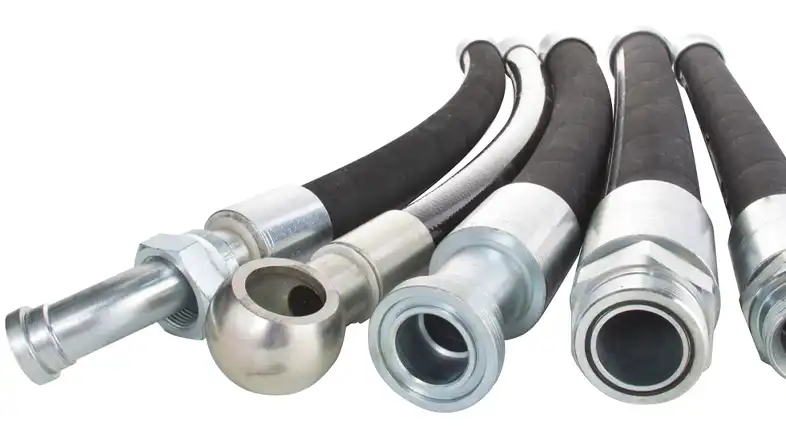
Crimping a hydraulic hose correctly is crucial for ensuring leak-free and reliable hydraulic connections. Proper crimping prevents hose failures and maintains system integrity. We’ll guide you through the essential steps to crimp a hydraulic hose accurately.
Step 1: Prepare the Hydraulic Hose and Fittings
You should begin by selecting the correct hydraulic hose and fittings for your application. Ensure they are compatible in terms of size, pressure rating, and material. Inspect the hose and fittings for any damage or defects. Cut the hydraulic hose to the required length using a specialized hose cutter, ensuring a clean, square cut to prevent leaks and ensure proper fitting insertion.
Step 2: Mark the Crimping Length
Next, you need to measure and mark the crimping length on the hydraulic hose. This mark indicates the area where the fitting will be crimped onto the hose. Consult the fitting manufacturer’s specifications for the correct crimping length. Accurate marking ensures the fitting is properly seated and crimped, preventing leaks and ensuring a secure connection.
Step 3: Insert the Hose into the Fitting
Carefully insert the hydraulic hose into the fitting until it reaches the marked crimping length. Ensure the hose is fully inserted and properly aligned with the fitting. This step is crucial for achieving a secure and leak-free connection. Proper insertion ensures the fitting grips the hose correctly during the crimping process.
Step 4: Set Up the Crimping Machine
Then, you must select the correct die set for the hydraulic hose and fitting size. Install the dies into the crimping machine according to the manufacturer’s instructions. Adjust the crimping machine’s settings to the required crimping diameter, based on the fitting manufacturer’s specifications. Proper setup of the crimping machine ensures accurate and consistent crimping results.
Step 5: Crimp the Fitting
Position the hydraulic hose and fitting assembly into the crimping machine. Activate the crimping machine to compress the dies and crimp the fitting onto the hose. Apply consistent pressure and ensure the fitting is crimped evenly around the hose. After crimping, inspect the connection to ensure it is secure and meets the manufacturer’s specifications.
Step 6: Verify the Crimped Connection
After crimping, you need to verify the connection’s integrity by measuring the crimped diameter and comparing it to the manufacturer’s specifications. Inspect the crimped area for any signs of damage, such as cracks or deformations. Perform a pull test, if required, to ensure the fitting is securely attached to the hose. Accurate verification ensures a reliable and leak-free hydraulic connection.
Hydraulic Hose Crimping Dies
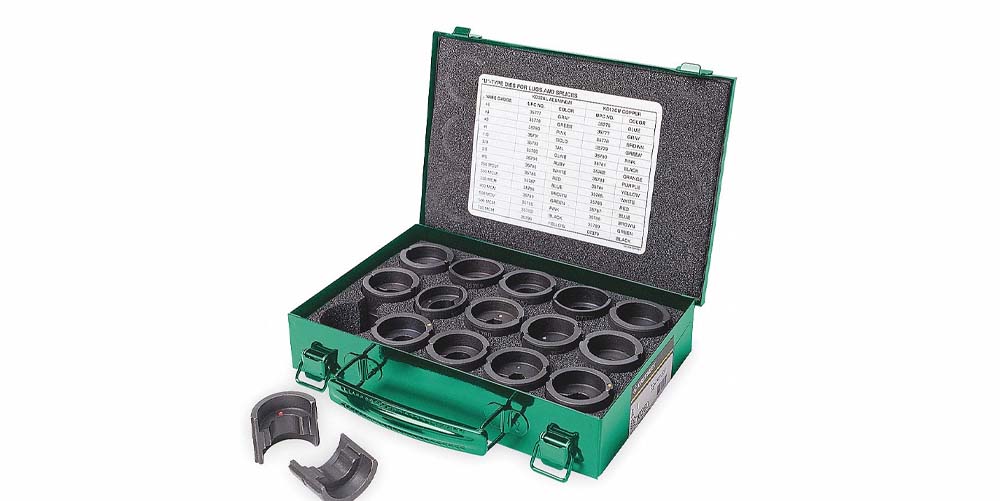
Hydraulic hose crimping dies are specialized tools designed to create a secure and leak-proof connection between a hydraulic hose and a fitting. These dies are precision-engineered to ensure optimal crimping performance and the longevity of the hose assembly.
Key Factors to Consider When Choosing Crimping Dies:
- Hose Size: The die set must be compatible with the specific size and type of hose being used.
- Fitting Type: Different fitting types require specific die sets to ensure proper crimping.
- Crimping Machine Compatibility: The die set must be compatible with the hydraulic hose crimping machine.
- Material Quality: High-quality die sets are essential for producing consistent and reliable crimps.
Common Types of Crimping Dies:
- Compression Dies: These dies compress the fitting onto the hose, creating a mechanical bond.
- Swaging Dies: These dies shape the fitting and hose material to create a tight, leak-proof connection.
Importance of Proper Die Selection and Use:
- Safety: A properly crimped hose connection is essential for safe operation of hydraulic systems.
- Performance: A secure connection ensures optimal hydraulic fluid flow and system performance.
- Longevity: A well-crimped hose can withstand high pressures and harsh operating conditions.
Hydraulic Hose Crimping Machine Advantages
Here are some advantages of hydraulic hose crimping machines.
Hydraulic hose press machines offer numerous advantages for businesses and individuals involved in hydraulic systems:
1. Enhanced Safety:
- Leak-Proof Connections: Proper crimping ensures a secure and leak-proof connection, reducing the risk of fluid leaks and potential accidents.
- Reduced Risk of Failure: Well-crimped hoses are less likely to fail under pressure, minimizing downtime and costly repairs.
2. Increased Efficiency:
- Faster Assembly: Hydraulic hose crimping machines significantly speed up the assembly process compared to manual methods.
- Consistent Quality: Automated crimping ensures consistent and reliable connections, reducing the risk of human error.
- Reduced Labor Costs: A single operator can efficiently crimp multiple hoses, saving labor costs.
3. Cost-Effective:
- Long-Term Savings: By preventing leaks and failures, hydraulic hose crimping machines can save money on maintenance and replacement costs.
- Increased Equipment Lifespan: Proper crimping extends the life of hydraulic hoses and components.
4. Versatility:
- Multiple Hose Sizes and Fittings: Hydraulic hose crimping machines can handle a wide range of hose sizes and fitting types.
- Customizable Settings: Many machines offer adjustable pressure and cycle time settings to accommodate various applications.
5. Improved Productivity:
- Reduced Downtime: Quick and efficient crimping minimizes downtime and maximizes productivity.
- Increased Output: A hydraulic hose crimping machine can significantly increase the number of hoses crimped per day.
By investing in a quality hydraulic hose crimping machine, businesses can improve safety, efficiency, and overall productivity.
Conclusion
Hydraulic hose crimping machine are essential tools for ensuring the safety and reliability of hydraulic systems. By understanding the different types of machines, their key features, and proper operation, you can make informed decisions to select the right equipment for your specific needs.
Ready to upgrade your hydraulic systems with high-quality hoses?
Contact Kingdaflex today to explore our wide range of hydraulic hoses and fittings. Our expert team can help you select the right products for your specific application and provide expert advice on installation and maintenance.