Hydraulic hoses are critical components in numerous industrial and mobile applications, transmitting high-pressure fluids for power and control.
Their integrity is paramount to ensure safe and reliable operation. Hydrostatic testing is a crucial procedure that assesses the strength and integrity of hydraulic hoses before they are put into service.
This blog post will delve into the intricacies of hydraulic hose hydrostatic testing, covering its significance, the testing process, and the benefits it offers in enhancing safety, extending service life, and preventing costly failures. We will also discuss the industry standards and regulations that govern hydrostatic testing procedures to ensure consistent and reliable results.
What Is Hydraulic Hose Hydrostatic Testing
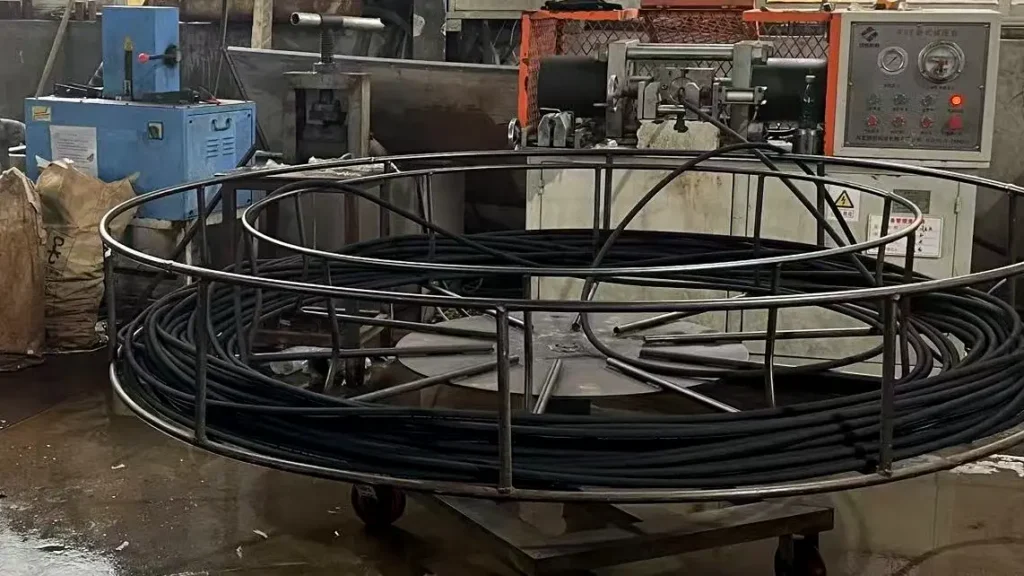
Hydraulic hose hydrostatic testing is a critical quality control process that involves pressurizing a hydraulic hose with a fluid (typically water) to a specific level. This pressure is significantly higher than the hose’s normal operating pressure.
Hydrostatic testing is a crucial safety procedure for hydraulic hoses. True
Hydrostatic testing involves pressurizing the hose with fluid to identify weaknesses. This ensures the hose can withstand operating pressures and prevents potential failures, which can lead to accidents and injuries.
Hydrostatic testing is not necessary for hydraulic hoses. False
Hydrostatic testing is a crucial safety procedure for hydraulic hoses. It involves pressurizing the hose with a liquid, typically water, to a level exceeding its normal operating pressure. This process helps to identify weaknesses or defects in the hose that could lead to failure under pressure. Regularly scheduled hydrostatic testing ensures the integrity of hydraulic systems and helps to prevent accidents and injuries.
Why Need Hydraulic Hose Hydrostatic Testing
Hydraulic hose hydrostatic testing is crucial for several key reasons:
Safety:
- Preventing catastrophic failures: High-pressure hydraulic systems can be extremely dangerous. Hose failures can result in:
- High-pressure fluid jets: These can cause serious injuries to personnel.
- Equipment damage: Sudden fluid release can damage machinery and surrounding equipment.
- Fire hazards: In some cases, leaking hydraulic fluid can ignite.
- Minimizing accidents: Hydrostatic testing helps identify and address potential issues before they lead to accidents, ensuring a safer working environment.
Reliability:
- Preventing unexpected downtime: Hose failures can cause sudden and unexpected equipment shutdowns, leading to:
- Production delays and losses
- Increased maintenance costs
- Disruptions to operations
- Maintaining productivity: By ensuring hose integrity, hydrostatic testing helps maintain consistent and reliable system operation.
Quality Control:
- Ensuring product quality: Hydrostatic testing is an essential part of the quality control process for hydraulic hose manufacturers.
- Meeting industry standards: Many industries have specific regulations and standards regarding the safety and performance of hydraulic hoses. Hydrostatic testing helps ensure compliance with these standards.
Cost-Effectiveness:
- Reducing repair and replacement costs: Identifying and addressing potential issues during testing is significantly more cost-effective than dealing with the consequences of a catastrophic failure.
- Extending hose lifespan: By identifying and addressing potential problems early on, hydrostatic testing can help extend the service life of hydraulic hoses.
How to Do Hydraulic Hose Hydrostatic Testing
Hydraulic hose hydrostatic testing is a critical quality control procedure employed to ensure the safety and reliability of hydraulic hoses.
This process involves subjecting the hose to a controlled, elevated pressure to identify potential weaknesses or defects that could lead to catastrophic failures in real-world operation.
1. Preparation
- Visual Inspection: Carefully examine the hose for any visible defects such as cuts, abrasions, kinks, or signs of previous damage.
- Cleanliness: Ensure the hose and surrounding area are clean and free of debris.
- Safety Precautions:
- Wear appropriate safety gear, including safety glasses, gloves, and protective clothing.
- Ensure the testing area is well-ventilated and away from ignition sources.
- Have a fire extinguisher readily available.
2. Test Setup
- Secure Mounting: Mount the hose securely in a test rig or fixture.
- Connect to Pressure Source: Connect one end of the hose to a reliable pressure source, such as a hydraulic pump or compressed air system.
- Install Pressure Gauge: Connect a calibrated pressure gauge to the hose to monitor pressure during the test.
3. Pressurization
- Gradual Increase: Gradually increase the pressure within the hose.
- Target Pressure: Increase the pressure to the specified test pressure, which is typically 1.5 to 2 times the hose’s working pressure.
- Maintain Pressure: Hold the pressure at the test level for the specified duration, usually 30-60 seconds.
4. Inspection
- Visual Check: Continuously monitor the hose for any signs of leakage, bulging, or deformation during pressurization and holding.
- Sound Check: Listen for any unusual sounds, such as hissing or cracking, which may indicate leaks.
5. Pressure Release
- Gradual Release: Slowly and gradually release the pressure from the hose.
6. Post-Test Inspection
- Final Check: Conduct a final visual inspection of the hose for any signs of damage or distress.
7. Documentation
- Record Test Results: Record all test data, including the test pressure, holding time, and any observed anomalies.
- Maintain Records: Keep accurate records of all hydrostatic tests for future reference and maintenance purposes.
Important Notes:
- Refer to Manufacturer‘s Specifications: Always consult the manufacturer‘s specifications for the specific hose type regarding recommended test pressures and procedures.
- Industry Standards: Adhere to relevant industry standards and regulations for hydraulic hose testing.
- Qualified Personnel: Hydrostatic testing should only be performed by qualified and trained personnel.
Conclusion
Hydrostatic testing is a crucial step in ensuring the safety and reliability of hydraulic hose systems. By subjecting hoses to controlled pressure, potential weaknesses or defects can be identified before they lead to catastrophic failures. This proactive approach minimizes downtime, prevents costly repairs, and safeguards personnel from potential hazards.
Ready to upgrade your hydraulic systems with high-quality, reliable hoses?
Kingdaflex offers a wide range of wholesale hydraulic hoses designed to meet the most demanding applications. Our hoses undergo rigorous quality control measures, including hydrostatic testing, to ensure exceptional performance and longevity. Contact us today to learn more about our products and discuss your specific requirements.