Hydraulic systems are the backbone of countless industrial and mobile applications, and at their heart are hydraulic fittings. These small but mighty components are essential for connecting hoses, tubes, and pipes, ensuring the reliable and leak-free transfer of hydraulic fluid under immense pressure.
This guide will demystify hydraulic fittings, exploring their types, functions, and the critical role they play in system integrity. Understanding these components is key to maintaining efficient and safe hydraulic operations.
What Are Hydraulic Fittings?
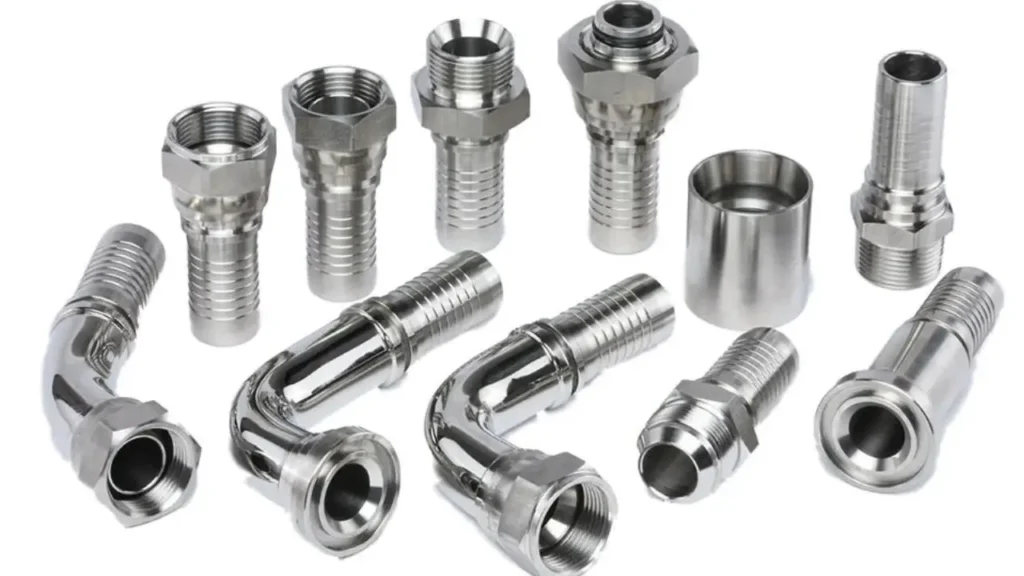
Hydraulic fittings are crucial components in hydraulic systems, serving as connectors that join hydraulic hoses, tubes, and pipes to various other parts like cylinders or valves. Their primary function is to facilitate the controlled flow of hydraulic fluid, enabling power transmission and preventing leaks to ensure the system operates efficiently and safely.
These hydraulic fittings come in a wide array of types, sizes, materials, and pressure ratings, each designed for specific applications and sealing requirements within diverse hydraulic machinery.
What Are the Different Hydraulic Fittings?
Choosing the correct hydraulic fittings is crucial for the safe and efficient operation of any hydraulic system. With a variety of designs available, each serving distinct purposes and pressure ratings, it’s important to understand their characteristics. Here are some of the most common types of hydraulic fittings:
O-Ring Face Seal (ORFS) Fittings
ORFS fittings are renowned for their superior leak prevention capabilities, particularly in high-pressure and high-vibration environments. They feature an O-ring at the flat face of the fitting, which creates a tight, metal-to-metal seal when compressed against a flat mating surface. This design makes them highly reliable and a preferred choice in industries where leak-free connections are paramount, such as construction and agriculture.
JIC (Joint Industry Council) 37° Flare Fittings
JIC fittings are widely utilized in fluid power systems due to their robust and easily maintainable design. They create a seal by mating a 37° flared male end with a 37° cone on the female port. This metal-to-metal seal provides a strong, durable connection that is suitable for medium to high-pressure applications and allows for repeated assembly and disassembly without compromising seal integrity.
NPT (National Pipe Tapered) Fittings
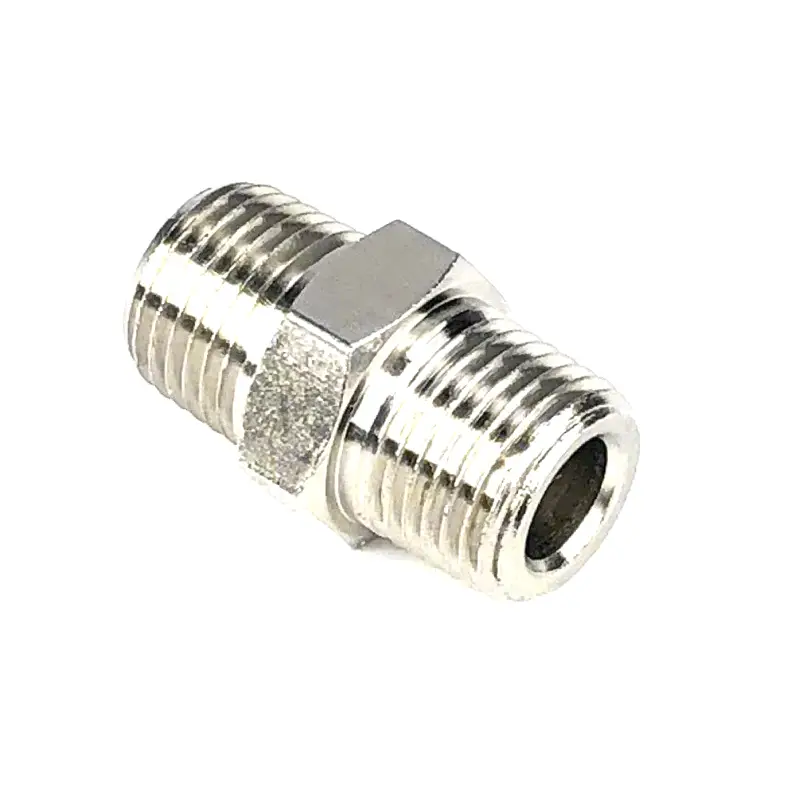
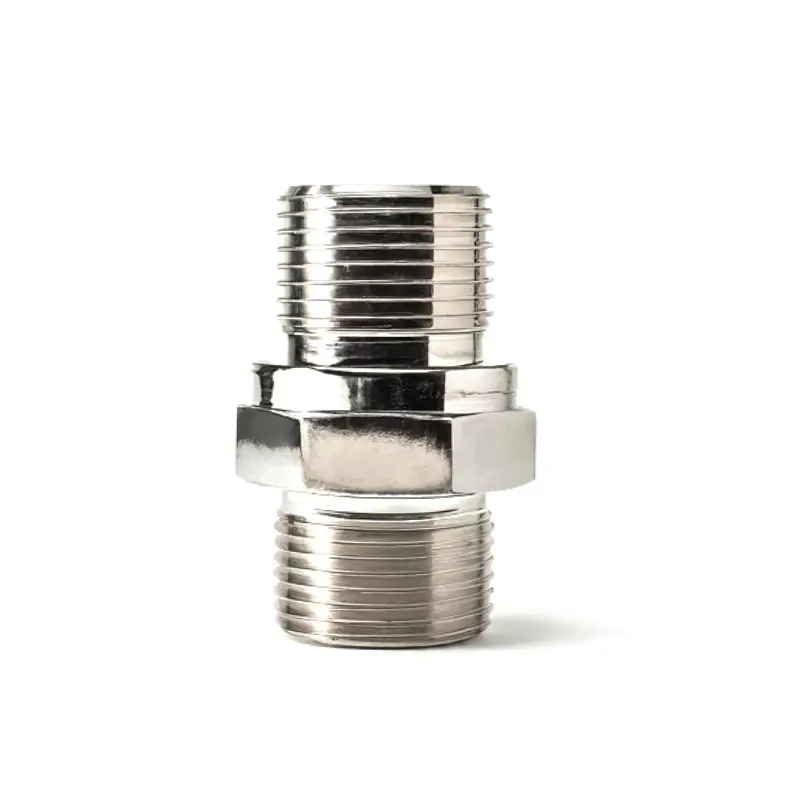
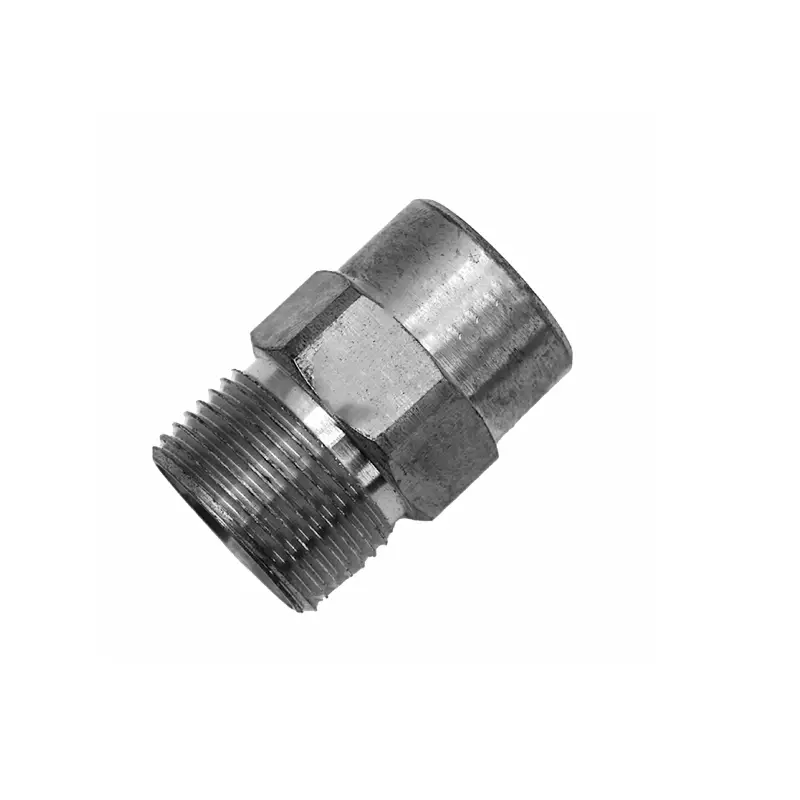
NPT fittings are a long-standing standard in North America, characterized by their tapered threads. The seal in NPT connections is achieved by the deformation of the threads as they are tightened, creating a wedge-like effect that provides a secure, albeit not always leak-proof without sealant, connection. These fittings are commonly found in a wide range of general-purpose hydraulic applications, particularly where permanent or semi-permanent connections are desired.
BSP (British Standard Pipe) Fittings
BSP fittings are prevalent in Europe, Asia, and other parts of the world, with two main variations: BSP Parallel (BSPP) and BSP Tapered (BSPT). BSPP fittings use parallel threads and typically rely on an O-ring or a bonded seal for leak-free operation, while BSPT fittings have tapered threads that create a seal through thread deformation, similar to NPT. Both types are widely used in low to medium-pressure hydraulic systems.
Compression Fittings
Compression fittings are designed for quick and straightforward installation without the need for welding or flaring. They utilize a compression nut and ferrule that, when tightened, bite into the tubing to create a mechanical seal. These fittings are generally used in lower-pressure hydraulic applications or in situations where easy assembly and disassembly are required, such as in instrumentation and light-duty fluid transfer lines.
What to Use to Seal Hydraulic Fittings
Effective sealing is paramount for the reliability and longevity of hydraulic systems, preventing fluid leaks that can lead to inefficiency, contamination, and safety hazards. The choice of sealant depends largely on the type of fitting, operating pressure, temperature, and the hydraulic fluid used. Understanding the various sealing methods is crucial for proper installation and maintenance.
Thread Sealant Tape (PTFE Tape/Teflon Tape)
Thread sealant tape, commonly known as PTFE or Teflon tape, is a thin, non-adhesive film used primarily on tapered pipe threads (like NPT and BSPT fittings). It works by deforming into the thread imperfections when tightened, creating a physical barrier that prevents fluid bypass. It’s easy to apply and provides a lubricated surface for smoother assembly. While effective for many low to medium-pressure applications, it’s generally not recommended for high-pressure systems or for fittings that create a seal through metal-to-metal contact or O-rings, as it can introduce contamination if not applied correctly.
Liquid Thread Sealants (Pipe Dope)
Liquid thread sealants, often referred to as “pipe dope,” are anaerobic compounds that cure in the absence of air and in the presence of metal ions. They are applied to the threads of fittings, filling any gaps and imperfections to create a strong, pressure-resistant seal. These sealants are particularly effective for NPT and BSPT fittings and offer excellent chemical and mechanical resistance. They provide a more robust and reliable seal than tape in many high-pressure and critical applications, reducing the risk of leaks and thread galling.
O-Rings
O-rings are elastomeric seals typically used in fittings like O-Ring Face Seal (ORFS) and O-Ring Boss (ORB) connections. They are designed to be compressed between two mating surfaces, creating a secure, leak-proof seal. The material of the O-ring (e.g., Nitrile, Viton, EPDM) is chosen based on compatibility with the hydraulic fluid, temperature, and pressure requirements. O-rings provide highly reliable seals, especially in dynamic applications, and allow for repeated assembly and disassembly without significantly degrading the seal’s integrity, provided the O-ring itself is in good condition.
Metal-to-Metal Seals
Some hydraulic fittings, such as JIC 37° flare fittings, rely on a metal-to-metal contact to create a seal. In these designs, the precision machining of the mating surfaces ensures a tight fit that prevents fluid leakage. While these connections typically do not require additional sealants like tape or liquid compounds, cleanliness and proper tightening are crucial to ensure the integrity of the metal-to-metal seal. Any damage or imperfections on the sealing surfaces can lead to leaks.
How to Identify Hydraulic Fittings?
Accurately identifying hydraulic fittings is essential for proper system assembly, maintenance, and repair. Mismatched fittings can lead to leaks, system failure, and safety hazards. Identification typically involves examining several key characteristics, often requiring measuring tools.
Step 1: Examine the Sealing Surface and Thread Type
The most crucial step is to determine how the fitting seals and the type of thread it uses. Look closely at the end of the fitting. Does it have a flared cone (like JIC), a flat face with an O-ring (ORFS), a tapered thread (NPT, BSPT), or a parallel thread with a seal groove (BSPP)? The presence or absence of an O-ring, a specific flare angle, or the thread’s taper will narrow down the possibilities significantly.
Step 2: Measure the Thread Diameter
Using a caliper, measure the outside diameter of the male threads or the inside diameter of the female threads. For tapered threads, measure at the largest point. This measurement will be approximate and will need to be cross-referenced with standard fitting charts (e.g., NPT, BSP, UNF/UNS) to determine the nominal size. Remember that actual measured diameters often don’t perfectly match nominal sizes.
Step 3: Determine the Thread Pitch (Threads Per Inch or Millimeter)
For parallel threads (like JIC, ORFS, BSPP, and SAE straight thread), use a thread pitch gauge to count the number of threads per inch (TPI) or measure the distance between threads in millimeters. This is a critical measurement for distinguishing between similar-sized fittings with different thread standards, such as UNF and Metric threads. For tapered threads, this step is less critical as the taper itself is a primary identifier.
Step 4: Observe the Fitting’s Configuration and Shape
Note the overall shape and configuration of the fitting. Is it a straight connector, an elbow, a tee, or a cross? Does it have a hex nut for tightening? Are there any distinguishing features, such as a swivel nut or a specific type of seat? This helps in identifying the fitting’s function and can further aid in narrowing down the possibilities.
Step 5: Check for Identifying Markings
Many fittings have manufacturers’ markings, part numbers, or material designations stamped on them. While not always present or legible, these markings can be invaluable for precise identification, especially for proprietary or specialized fittings. If a part number is found, a quick search of the manufacturer’s catalog can often provide all the necessary specifications.
How to Connect Hydraulic Fittings?
Properly connecting hydraulic fittings is crucial for ensuring the integrity, efficiency, and safety of any hydraulic system. Incorrect installation can lead to costly leaks, system malfunctions, and potential hazards. While specific procedures vary slightly by fitting type, the overarching goal is to create a secure, leak-free seal.
Step 1: Connecting JIC (Joint Industry Council) 37° Flare Fittings
To connect JIC fittings, first ensure both the male and female flare seats are clean and free of burrs or damage. Align the male fitting with the female port. Hand-tighten the swivel nut until it is snug. Then, using a wrench, tighten the nut a specified number of flats or to a recommended torque value. The metal-to-metal contact of the 37° flare creates the seal, so over-tightening can deform the flare and lead to leaks.
Step 2: Connecting O-Ring Face Seal (ORFS) Fittings
Connecting ORFS fittings involves aligning the male fitting, which has a flat face with an O-ring, with the female port. Ensure the O-ring is properly seated in its groove and is not twisted or damaged. Hand-tighten the nut until the O-ring makes contact with the flat face of the female port. Then, tighten the nut with a wrench to the manufacturer’s recommended torque specification. The O-ring is compressed between the two flat faces, providing a reliable, leak-proof seal.
Step 3: Connecting NPT (National Pipe Tapered) Fittings
For NPT fittings, apply a suitable thread sealant, such as PTFE tape or liquid pipe dope, to the male tapered threads. Wrap PTFE tape clockwise, starting from the second thread, ensuring it doesn’t extend beyond the first thread.
For liquid sealant, apply a thin, even coat. Hand-tighten the fitting until snug. Then, using a wrench, turn the fitting an additional 1 to 3 turns past hand-tight, or to the manufacturer’s specified torque. The tapered threads deform and compress the sealant to create the seal.
Step 4: Connecting BSPP (British Standard Pipe Parallel) Fittings
BSPP fittings with parallel threads typically require a sealing washer, such as a bonded seal or an O-ring, placed between the shoulder of the male fitting and the face of the female port. Ensure the sealing washer is correctly positioned and undamaged.
Hand-tighten the fitting until the sealing washer makes contact with the port face. Then, use a wrench to tighten the fitting to the recommended torque, compressing the washer to create the seal. Avoid over-tightening, as it can damage the washer.
Step 5: Connecting Compression Fittings
To connect compression fittings, slide the compression nut and then the ferrule(s) onto the tube in the correct orientation. Insert the tube squarely into the fitting body until it bottoms out. Tighten the compression nut with another wrench while holding the fitting body steady with one wrench.
For initial assembly, tighten until you feel a sudden increase in resistance, then turn an additional 1 to 1.5 turns for metallic ferrules, or according to manufacturer specifications. This action causes the ferrule to compress onto the tube and create a seal against the fitting body.
Hydraulic Hose Benefits
Hydraulic hoses are indispensable components in a vast array of hydraulic systems, offering numerous benefits that contribute to their widespread use across industries. Their inherent flexibility is a primary advantage, allowing fluid power to be transmitted between moving and stationary machine components, or in applications where rigid piping would be impractical. This flexibility also simplifies installation in confined spaces and absorbs vibrations, reducing stress on the overall system and extending component lifespan.
Hydraulic hoses provide exceptional versatility in terms of pressure capacity, temperature resistance, and fluid compatibility. They are engineered to withstand extreme pressures and varying temperatures, ensuring reliable performance in demanding environments.
- Flexibility: Enables connections between moving parts and simplifies routing in complex machinery.
- Vibration Absorption: Reduces noise and stress on system components, enhancing durability.
- High Pressure Capability: Designed to safely convey fluids under intense pressure, critical for heavy machinery.
- Chemical Compatibility: Available in materials resistant to a wide range of hydraulic fluids, preventing degradation.
- Temperature Resilience: Maintains integrity and performance across broad temperature fluctuations.
Hydraulic Hose Uses
Hydraulic hoses are integral to the operation of countless modern machines, acting as the arteries that transmit hydraulic fluid power. Their ability to handle high pressures, withstand diverse temperatures, and resist various fluids makes them indispensable across a wide spectrum of industries, enabling machinery to perform complex tasks with precision and force. Without these flexible conduits, many of today’s industrial and mobile applications would be impossible.
The applications of hydraulic hoses are incredibly diverse, impacting almost every sector of the global economy. From heavy-duty construction to precision manufacturing, these hoses are the backbone of hydraulic systems that power essential equipment.
- Construction: Hydraulic hoses are extensively used in excavators, bulldozers, cranes, loaders, and other heavy equipment to power their hydraulic arms, buckets, and lifting mechanisms, enabling digging, lifting, and moving heavy materials.
- Agriculture: Modern farming relies heavily on hydraulic hoses for operating tractors, combine harvesters, sprayers, and irrigation systems, facilitating tasks like plowing, planting, cultivating, and harvesting.
- Manufacturing and Industrial Automation: In factories and assembly lines, hydraulic hoses power robotic arms, presses, material handling equipment, and other machinery that requires precise and powerful movements for manufacturing processes.
- Mining: Earthmoving equipment, drilling rigs, and material conveyance systems in mining operations depend on robust hydraulic hoses to withstand harsh conditions and transmit the immense power needed for extraction.
- Automotive: Hydraulic hoses are found in vehicle braking systems, power steering, suspension, and even in manufacturing processes for stamping and assembling car parts.
- Marine and Aerospace: From steering systems and winches on ships to landing gear and flight control surfaces in aircraft, hydraulic hoses play a critical role in ensuring reliable operation in these highly demanding environments.
Conclusion
Hydraulic fittings are essential for connecting components in hydraulic systems, ensuring efficient power transmission. This guide has explored their diverse types and critical role in various applications.
Understanding these fittings is key to system integrity and performance. Proper selection and installation prevent leaks and maximize operational efficiency.
For all your wholesale hydraulic fitting needs, trust Kingdaflex to provide reliable and high-quality solutions.