In the world of fluid handling and transportation, there exists a remarkable invention known as the peristaltic pump. This ingenious device has found its application in various industries, from pharmaceuticals to food production, offering a unique way of moving fluids.
In this article, we will delve into the intricacies of peristaltic pumps, understanding their working principles, applications, and advantages.
What Is A Peristaltic Pump?
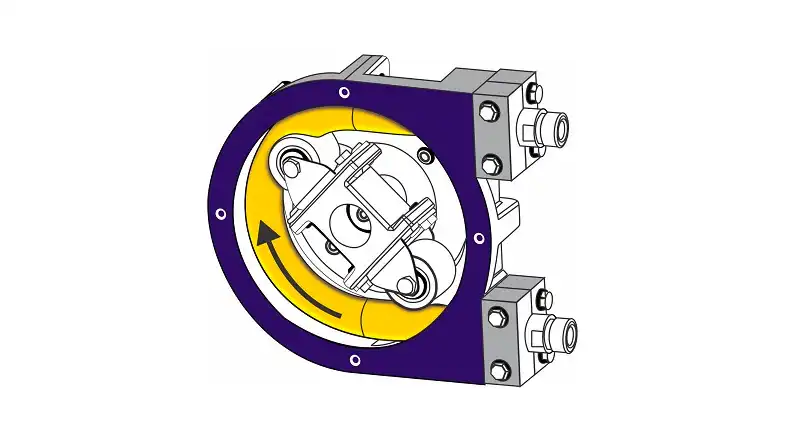
A peristaltic pump, also known as a hose pump or tube pump, is a positive displacement pump that operates by compressing and relaxing a flexible tube or hose.
Unlike traditional pumps that use impellers, pistons, or diaphragms to move fluids, peristaltic pumps utilize a “rolling” motion to gently transport liquids without contaminating or damaging them.
What Is A Peristaltic Pump Used For?
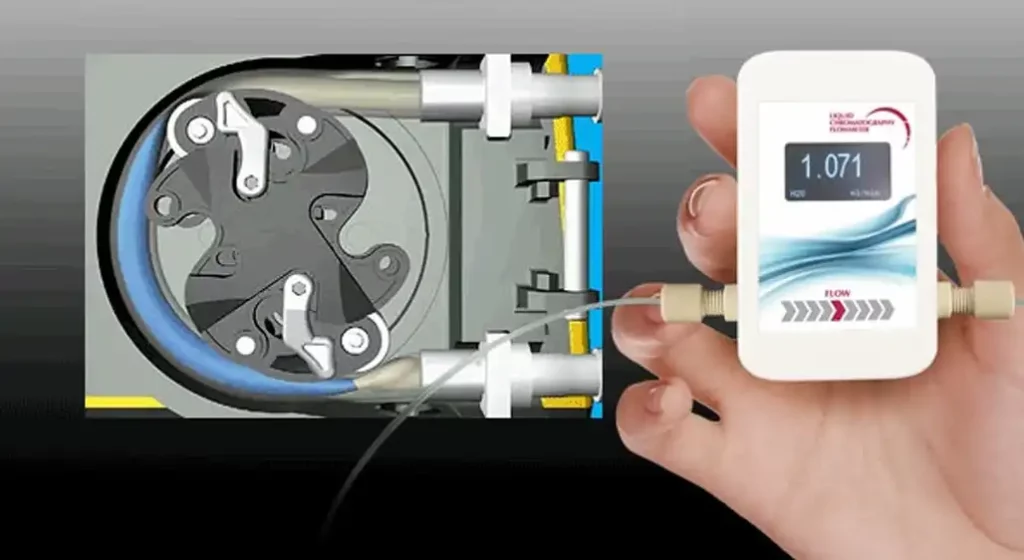
A peristaltic pump is used for various fluid-handling applications across different industries. It operates based on a principle called peristalsis, which mimics the natural process of muscle contractions in the human digestive system.
In a peristaltic pump, a flexible tube or hose is squeezed by rollers or shoes in a rotating mechanism. This squeezing action creates a series of vacuum pockets that draw fluid through the tube, and it then pushes the fluid out in a controlled and pulsatile manner.
Here are some common uses of peristaltic pumps:
- Medical and Pharmaceutical: Peristaltic pumps are frequently employed in medical and pharmaceutical applications. They are used for precise and sterile fluid transfer in processes such as drug manufacturing, IV medication delivery, and laboratory research.
- Food and Beverage: Peristaltic pumps are utilized in the food and beverage industry for tasks like transferring ingredients, handling sensitive or viscous fluids, and metering additives or flavorings.
- Water Treatment: They are used in water treatment systems to dose chemicals like chlorine or pH adjusters, as well as for transferring and sampling water and wastewater.
- Chemical and Petrochemical: Peristaltic pumps are ideal for handling corrosive and abrasive chemicals because the fluid only comes into contact with the inside of the tubing. They are used in chemical processing, laboratory settings, and the transfer of hazardous materials.
- Environmental Monitoring: Peristaltic pumps are employed in environmental monitoring instruments for tasks such as groundwater sampling and collecting water samples from various depths in wells.
- Biotechnology: In biotech laboratories, peristaltic pumps are used for precise fluid handling in applications like cell culture, chromatography, and DNA sequencing.
- Analytical Instruments: They are utilized in analytical instruments like liquid chromatography, where accurate and consistent flow rates are essential for separating and analyzing compounds.
- Mining: Peristaltic pumps are used in mining operations for tasks such as transferring slurry, dosing reagents, and pumping abrasive slurries without damage to the equipment.
- Printing: In large-format printing and industrial inkjet applications, peristaltic pumps are used to deliver ink accurately and maintain consistent print quality.
- Research and Development: Peristaltic pumps are valuable tools in various research and development processes that require precise fluid handling, including material testing and prototype development.
The key advantages of peristaltic pumps include their ability to provide accurate and repeatable flow rates, handle a wide range of fluids, prevent cross-contamination, and require minimal maintenance. These features make them suitable for applications where precision, hygiene, and versatility are crucial.
How Does a Peristaltic Pump Work?

A peristaltic pump operates using a simple yet ingenious mechanism. It relies on the concept of peristalsis, which is the rhythmic, wave-like motion that occurs in various biological processes, such as the contraction of muscles in your digestive system to move food along.
Here’s a step-by-step explanation of how a peristaltic pump works:
- Components: A typical peristaltic pump consists of three main components: rollers or shoes, flexible tubing, and a housing.
- Rollers or Shoes: These components are mounted on a rotor within the pump. They are usually made of materials like rubber or silicone and are designed to press against the flexible tubing.
- Flexible Tubing: The fluid that needs to be transported flows through a flexible tube or hose. This tubing is positioned in the pump in such a way that it passes through the rollers or shoes.
- Housing: The housing holds the rollers or shoes in place and guides the movement of the flexible tubing.
- Compression: When the peristaltic pump is in operation, the rollers or shoes rotate. As they rotate, they come into contact with the flexible tubing. When they press against the tubing, they create a series of occlusions or “pockets” in the tubing.
- Peristaltic Action: This is where the magic happens. As the rollers or shoes press against the tubing, they effectively “pinch” it shut at certain points along its length. These pinched points create a series of isolated chambers within the tubing.
- Fluid Movement: The key to peristaltic pumps is that they move fluids by squeezing and releasing the tubing in a pulsatile, peristaltic fashion. When a section of the tubing is pinched shut by the roller, it traps a specific volume of fluid within that chamber. As the roller moves away and releases the tubing, it creates a vacuum effect behind it, causing the trapped fluid to be drawn into the chamber. This action effectively propels the fluid forward through the tubing.
- Continuous Process: As the rollers or shoes continue to rotate, this peristaltic action is repeated along the entire length of the tubing. This process is continuous, creating a smooth and consistent flow of fluid from the inlet to the outlet of the pump.
One of the key advantages of peristaltic pumps is that the fluid being pumped only comes into contact with the tubing, and there is no contact with the pump’s internal components. This makes peristaltic pumps ideal for applications where the purity and integrity of the fluid must be maintained, such as in the pharmaceutical and food industries.
Additionally, because the tubing is the only part of the pump in contact with the fluid, it is easy to replace and maintain, contributing to the pump’s reliability and longevity.
How to Control a Peristaltic Pump
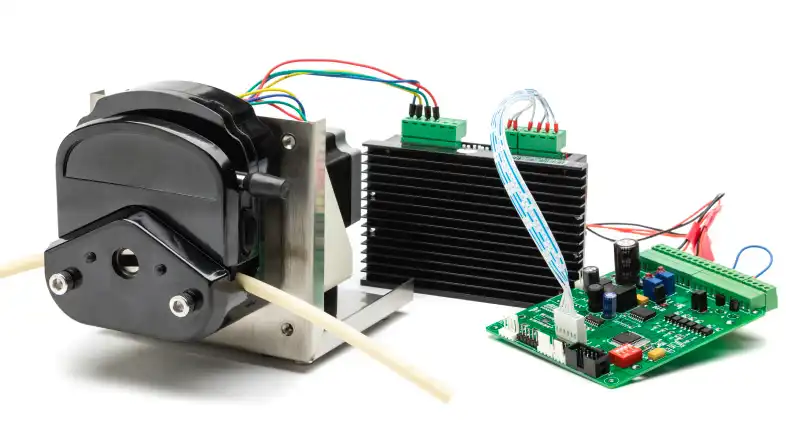
Controlling a peristaltic pump involves several steps to manage its flow rate and operation effectively. Here’s how to control a peristaltic pump:
- Power On: Ensure the pump is properly connected to a power source and turned on.
- Set Speed: Most peristaltic pumps come with variable speed settings. Adjust the speed control to the desired rate for your application. Slower speeds reduce flow rates, while faster speeds increase them.
- Prime the Pump: Before starting the pump, make sure the tubing is correctly installed and primed. Priming ensures that the fluid flows smoothly through the tubing without air bubbles.
- Start the Pump: Activate the pump using the provided controls, which can include buttons, switches, or digital interfaces.
- Monitor Flow: Keep an eye on the flow rate to ensure it meets your requirements. Adjust the speed if necessary to achieve the desired flow.
- Stop the Pump: When your operation is complete, stop the pump using the controls.
- Maintenance: Regularly inspect the tubing for wear and tear. If the tubing needs replacement, follow the manufacturer’s guidelines for tube replacement.
- Safety Precautions: Adhere to safety protocols, such as wearing appropriate protective gear and following any specific guidelines for the substances you’re handling.
- Programmable Control (Optional): Some advanced peristaltic pumps offer programmable features. If available, use these features to automate the pump’s operation, set precise dosing schedules, or integrate it into a larger system.
- Shut Down: When you have completed your work, turn off the pump, and disconnect it from the power source.
Remember that the specific control methods and features may vary depending on the brand and model of the peristaltic pump you are using. Always refer to the manufacturer’s instructions and guidelines for precise control and maintenance procedures.
Applications of Peristaltic Pumps
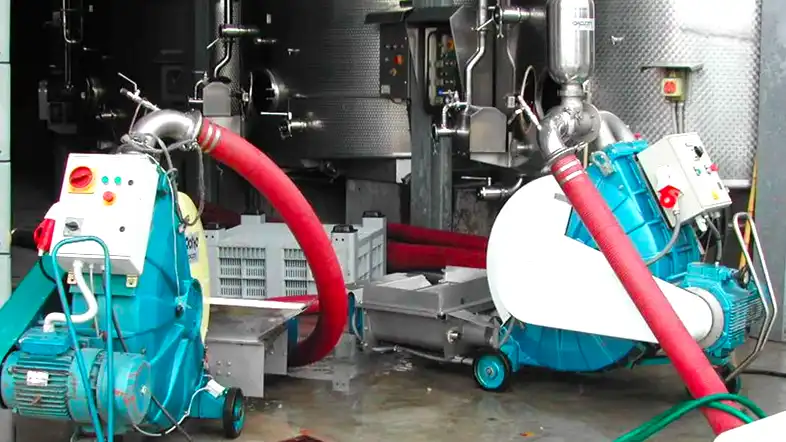
Medical and Pharmaceutical Industries
In the medical field, peristaltic pumps are used for drug delivery, dialysis, and in laboratories for accurate liquid handling. Their ability to maintain sterility and avoid contamination is crucial in these applications.
Food and Beverage Industry
Peristaltic pumps are employed in food processing to transfer sensitive ingredients like dairy, sauces, and chocolate. Their hygienic design ensures product integrity and minimizes waste.
Water Treatment and Environmental Applications
These pumps play a vital role in wastewater treatment and chemical dosing, thanks to their ability to handle corrosive and abrasive fluids with ease.
Advantages of Peristaltic Pumps
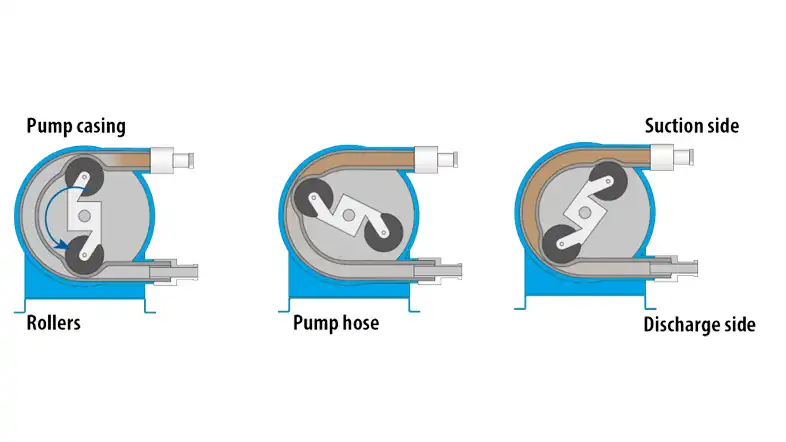
Peristaltic pumps offer a range of distinct advantages that make them a preferred choice in various industries. Here are some of the key advantages of peristaltic pumps:
No Contamination: Peristaltic pumps are designed in a way that ensures the fluid being pumped only comes into contact with the inside surface of the flexible tubing. There are no valves, seals, or other pump components that contact the fluid. This design eliminates the risk of contamination from the pump itself, making peristaltic pumps ideal for applications where maintaining the purity and integrity of the fluid is critical, such as in pharmaceutical manufacturing or food processing.
Precise Flow Control: Peristaltic pumps excel at providing precise control over flow rates. The pulsatile nature of their operation allows for accurate dosing and metering of fluids. This level of control is invaluable in industries where precise fluid handling is required, such as in laboratories or chemical processing.
Low Maintenance: Peristaltic pumps have minimal moving parts that come into contact with the fluid. Since there are no valves, seals, or diaphragms to wear out, the maintenance requirements are significantly reduced. This leads to lower maintenance costs and less downtime for equipment servicing.
Gentle on Fluids: The peristaltic action of these pumps is inherently gentle. The fluid is moved in a pulsatile manner without being subjected to shear forces or abrupt changes in pressure. This is crucial when handling shear-sensitive or fragile fluids, ensuring that they remain unaltered during transport.
Self-Priming: Peristaltic pumps are typically self-priming, meaning they have the ability to create a vacuum in the tubing to draw in the fluid from the source. This self-priming capability simplifies the setup and operation of the pump.
Versatility: Peristaltic pumps can handle a wide range of fluids, including corrosive, abrasive, viscous, and high-purity liquids. Their versatility makes them suitable for diverse applications, from chemical dosing to transferring sensitive ingredients in the food industry.
Low Risk of Leaks: Since there are no dynamic seals in contact with the fluid, peristaltic pumps have a low risk of leakage. This is especially important when dealing with hazardous or expensive chemicals, as it reduces the risk of spills and product loss.
Easy Tubing Replacement: If the tubing becomes worn or needs replacement, it can be easily and quickly swapped out without the need for specialized tools or extensive downtime. This ease of tubing replacement contributes to the pump’s overall reliability.
Energy Efficiency: Peristaltic pumps are known for their energy efficiency. They consume less power compared to some other pump types, which can result in cost savings over time.
Minimal Maintenance Costs: Due to their low maintenance requirements and durable design, peristaltic pumps often have lower overall operating costs compared to other pump types. This cost-effectiveness is attractive to many industries.
Peristaltic pumps offer a unique combination of precision, purity, and reliability in fluid handling. Their advantages make them a preferred choice for applications where the quality and integrity of the transported fluid are paramount, and where precise flow control is essential. Whether in pharmaceuticals, food production, or environmental applications, peristaltic pumps continue to play a vital role in various industries.
Choosing the Right Peristaltic Pump
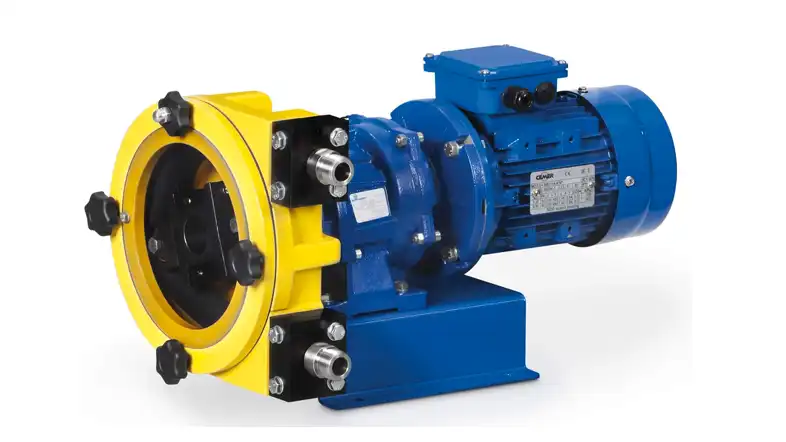
Selecting the right peristaltic pump is crucial to ensure optimal performance and efficiency for your specific application. Several factors should be taken into consideration when making your choice. Here’s a guide on how to choose the right peristaltic pump:
Flow Rate Requirements: Determine the required flow rate for your application. Peristaltic pumps are available in a range of flow rates, from microliters per minute to liters per minute. Select a pump that can handle the volume of fluid you need to move.
Fluid Compatibility: Consider the nature of the fluid you will be pumping. Peristaltic pumps are versatile and can handle various fluids, including corrosive, abrasive, viscous, and high-purity liquids. Ensure that the materials used in the pump’s construction, including the tubing, are compatible with your specific fluid.
Pressure Requirements: Different applications may require different levels of pressure. Peristaltic pumps come in various models with varying pressure capabilities. Be sure to choose a pump that can provide the necessary pressure for your application.
Tubing Size: The size of the tubing used in the peristaltic pump affects the flow rate and pressure capabilities. Larger tubing generally allows for higher flow rates, while smaller tubing can handle lower flow rates but may provide higher pressure. Select the appropriate tubing size based on your needs.
Temperature Range: Consider the temperature of the fluid you’ll be pumping. Some peristaltic pumps are designed to handle a wide temperature range, while others have limitations. Ensure that the pump can safely operate within the temperature range of your application.
Chemical Compatibility: If you are dealing with chemicals, verify that the pump materials are resistant to chemical corrosion. Some peristaltic pumps offer tubing options that are specifically designed to resist chemical attack.
Ease of Tubing Replacement: Check how easy it is to replace the tubing in the pump. Some pumps have user-friendly tubing replacement systems that allow for quick and hassle-free changes. This can reduce downtime and maintenance efforts.
Automation and Control: Determine whether you require automation and precise control over the pump operation. Some peristaltic pumps come with advanced control options, such as variable speed settings and programmable features, which can be advantageous for applications that demand precise fluid handling.
Budget Considerations: Like any equipment purchase, budget constraints may play a role in your decision. While peristaltic pumps are known for their reliability and low maintenance costs, consider both the initial purchase price and long-term operating costs.
Consult with Experts: If you’re unsure about which peristaltic pump is best for your application, consult with experts or manufacturers in the field. They can provide guidance and recommendations based on their expertise.
Warranty and Support: Check the manufacturer’s warranty and the availability of customer support. A reliable warranty and accessible support can provide peace of mind in case of any issues or questions.
Choosing the right peristaltic pump is essential to ensure efficient fluid handling while meeting the specific requirements of your application. Taking the time to carefully assess your needs and considering the factors mentioned above will help you make an informed decision and select a pump that delivers optimal performance and reliability.
Maintenance and Care
Regular maintenance is essential to keep peristaltic pumps in optimal condition. This includes inspecting tubing for wear, checking rollers for proper alignment, and cleaning components as needed.
Peristaltic Pump vs. Other Pump Types
When it comes to selecting a pump for fluid handling applications, you’ll encounter various types, each with its own set of advantages and disadvantages. Here, we’ll compare peristaltic pumps to other common pump types to help you understand their unique qualities and when to choose one over the other:
Peristaltic Pump
Advantages:
- No Contamination: Peristaltic pumps are known for their excellent fluid containment. The fluid only contacts the tubing, eliminating the risk of contamination from pump components.
- Precise Flow Control: Peristaltic pumps offer precise control over flow rates, making them ideal for applications requiring accurate dosing.
- Low Maintenance: Minimal contact between moving parts and fluid reduces wear and tear, leading to lower maintenance costs.
- Gentle on Fluids: Their gentle peristaltic action is ideal for shear-sensitive or fragile fluids.
- Self-Priming: Peristaltic pumps are typically self-priming, simplifying setup.
Disadvantages:
- Limited Flow Rates: They may not be suitable for high-flow applications compared to some other pump types.
- Tubing Wear: The tubing can wear out over time and may need replacement.
Centrifugal Pump
Advantages:
- High Flow Rates: Centrifugal pumps are known for their ability to move large volumes of fluid quickly.
- Wide Range of Sizes: They come in various sizes and can handle a wide range of flow rates and pressures.
- Cost-Effective: They are often cost-effective for high-flow applications.
Disadvantages:
- Risk of Contamination: Centrifugal pumps have multiple internal components that can contact the fluid, which may pose contamination risks.
- Less Precise Flow Control: They are not as precise in controlling flow rates as peristaltic pumps.
- Maintenance: They require more maintenance due to wear and tear on impellers and seals.
Diaphragm Pump
Advantages:
- No Cross-Contamination: Diaphragm pumps have a diaphragm that separates the fluid from the pumping mechanism, reducing the risk of cross-contamination.
- Accurate Flow Control: They provide precise flow control and can handle a wide range of pressures.
- Suitable for Abrasives: Diaphragm pumps can handle abrasive fluids.
Disadvantages:
- Complex Design: They have a more complex design than peristaltic pumps, making maintenance and repair potentially more challenging.
- Maintenance Costs: Diaphragms may require frequent replacement, increasing maintenance costs.
- Not Ideal for Shear-Sensitive Fluids: They may not be suitable for shear-sensitive fluids due to their diaphragm action.
Piston Pump
Advantages:
- High Pressure: Piston pumps excel at generating high pressures, making them suitable for applications requiring high force.
- Precise Metering: They offer precise fluid metering and are used in applications like injection and dispensing.
Disadvantages:
- Risk of Contamination: Like centrifugal pumps, piston pumps have multiple internal components that contact the fluid, which may pose contamination risks.
- Maintenance: Maintenance can be complex, and seals and pistons may need replacement.
Gear Pump
Advantages:
- Smooth Flow: Gear pumps provide a smooth and continuous flow of fluid.
- Versatile: They can handle a wide range of viscosities and are often used in hydraulic systems.
Disadvantages:
- Risk of Contamination: Gear pumps have close internal clearances where fluids can leak, potentially leading to contamination.
- Limited for High-Viscosity Liquids: In some cases, high-viscosity fluids can cause challenges.
In summary, the choice between peristaltic pumps and other pump types depends on the specific requirements of your application. Peristaltic pumps excel in situations where contamination, precise flow control, and low maintenance are paramount. However, for high-flow or high-pressure applications, other pump types like centrifugal, diaphragm, piston, or gear pumps may be more suitable, despite potential drawbacks related to contamination risks and maintenance needs.
Environmental Considerations
Peristaltic pumps are known for their energy efficiency and minimal environmental impact. Their gentle operation and low energy consumption make them a sustainable choice.
Conclusion
Peristaltic pumps have revolutionized the way we handle fluids in various industries. Their gentle, precise, and contamination-free operation makes them indispensable for applications ranging from medicine to food production. As technology continues to advance, we can only imagine the new frontiers that peristaltic pumps will conquer.
FAQs
Are peristaltic pumps suitable for high-pressure applications?
Yes, there are specialized peristaltic pumps designed to handle high-pressure fluids.
Can peristaltic pumps handle viscous liquids?
Absolutely, peristaltic pumps excel at moving viscous fluids like syrups and pastes.
Are peristaltic pumps environmentally friendly?
Yes, they are energy-efficient and have a minimal environmental footprint.
Where can I find high-quality peristaltic pumps?
You can explore reputable manufacturers and suppliers online or consult with industry experts.
Do peristaltic pumps require a lot of maintenance?
No, they have minimal moving parts in contact with the fluid, reducing maintenance needs.
Peristaltic pumps represent a remarkable marriage of simplicity and efficiency in fluid handling. Their widespread adoption across industries attests to their reliability and effectiveness, making them a cornerstone in modern fluid transportation solutions.