Making secure and reliable connections for pipes and hoses is crucial in various applications, from plumbing systems to industrial machinery. Two popular methods for achieving this are swaging and crimping. While both involve compressing a fitting onto a pipe or hose, they have distinct characteristics and applications.
Let’s delve into the world of swaging vs. crimping to help you choose the right method for your next project.
What I Swaging
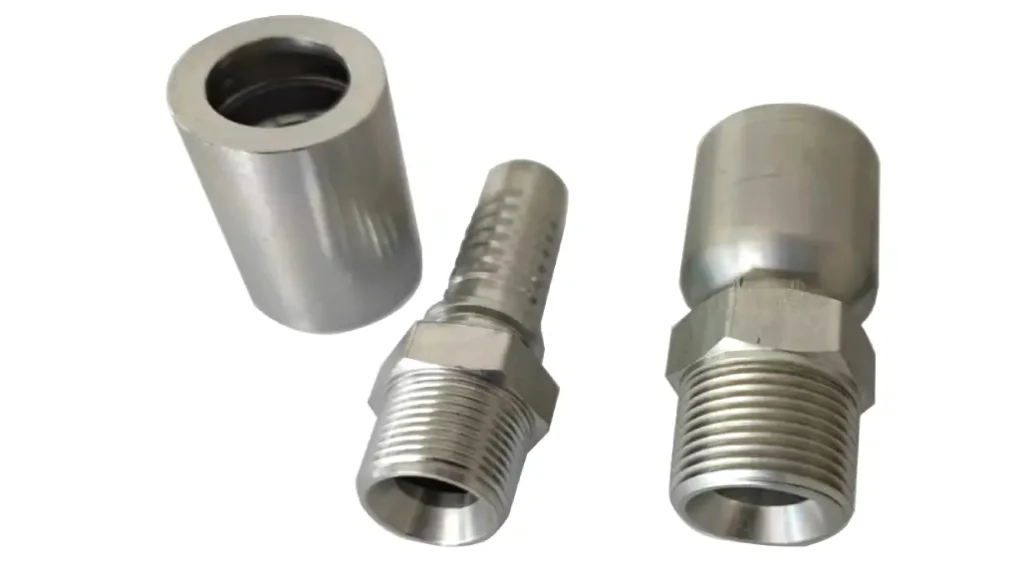
Swaging utilizes a mechanical crimping process to create a permanent connection. Here’s a breakdown of its key features:
Connection Method: A dedicated swaging tool applies pressure, typically using a die and punch mechanism, to compress a sleeve or collar on the fitting around the inserted pipe or hose. This tightens the grip, forming a secure connection.
Installation: The process involves inserting the pipe or hose into the fitting and then using the swaging tool to compress the sleeve or collar. Swaging tools come in various forms, ranging from handheld options for smaller projects to hydraulic presses for large-scale applications.
Benefits:
- Fast Installation: Once you’ve mastered the technique, swaging can be a relatively quick way to create connections.
- Secure Connections: When installed correctly, swaged fittings form strong and leak-proof connections, ideal for high-pressure applications.
- Cost-Effective: Swage fittings and the corresponding crimping tools are generally less expensive compared to some alternatives.
Applications of Swage Fittings:
Swage fittings are commonly used in various applications where secure connections are crucial:
- Plumbing Systems: For connecting pipes in residential or commercial plumbing systems, especially for copper or PEX tubing.
- Hydraulic Lines: In machinery and equipment that relies on hydraulic systems for power transmission.
- Gas Lines: For certain low-pressure gas applications where local building codes permit their use.
What Is Crimping
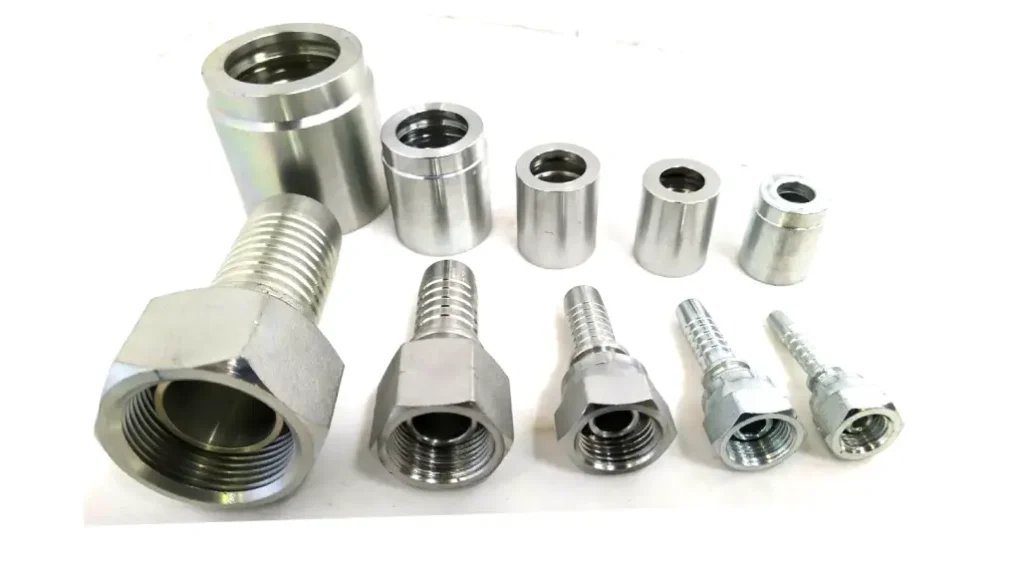
Crimping, similar to swaging, also involves compressing a fitting onto a pipe or hose. However, the mechanism and tools differ slightly.
Connection Method: Crimping utilizes a specialized crimping tool with pre-shaped jaws or dies designed to compress a ferrule (a ring or sleeve) around the inserted pipe or hose and the fitting. This creates a tight seal and secure connection.
Installation: The process involves inserting the pipe or hose into the fitting, then placing the ferrule over the connection point. Finally, the crimping tool is used to compress the ferrule, creating the desired grip.
Benefits:
- Fast Installation: Crimping, like swaging, can be a relatively quick process, especially with the right tools.
- Secure Connections: When done correctly with compatible components, crimped connections can be strong and leak-proof.
- Versatility: Crimping tools and ferrules are available in various sizes and styles to accommodate different pipe or hose diameters and materials.
Applications of Crimp Fittings:
Crimp fittings are widely used in various applications:
- Plumbing Systems: For connecting pipes in water supply lines, drainage systems, and PEX tubing connections.
- Fuel Lines: In low-pressure fuel lines for applications like automobiles or small engines (always follow manufacturer recommendations and local regulations).
- Air Conditioning and Refrigeration Systems: Crimp fittings can be used for refrigerant lines or compressed air lines, depending on the specific system and compatibility with the refrigerant or air pressure.
Swaging vs. Crimping: A Side-by-Side Comparison
Choosing the right connection method for your project depends on various factors like application requirements, ease of use, and cost.
Here’s a side-by-side comparison of swaging and crimping to help you make an informed decision:
Feature | Swaging | Crimping |
---|---|---|
Connection Method | Mechanical crimping using a die and punch to compress a sleeve on the fitting. | Crimping tool with pre-shaped jaws compresses a ferrule around the fitting and pipe/hose. |
Installation Tools | Dedicated swaging tool (handheld or hydraulic press) matching the fitting size and type. | Crimping tool with compatible jaws and ferrules for the specific fitting and pipe/hose combination. |
Installation Complexity | Requires a specific tool and proper technique to ensure even crimping. | Requires a specific tool and selecting the right ferrule size. Improper crimping technique can lead to issues. |
Speed | Relatively fast installation once the technique is mastered. | Can be fast with the right tools and practice. |
Security of Connection | Strong and leak-proof when installed correctly. | Secure and leak-proof when done correctly with compatible components. |
Cost | Generally less expensive for fittings and tools compared to crimping. | Fitting costs can be comparable, but crimping tools might be more expensive. |
Reusability | Fittings are typically not reusable due to deformation during crimping. | Ferrule reusability depends on the type, but crimped connections are generally considered permanent. |
Applications | Common in plumbing (copper, PEX), hydraulic lines, and low-pressure gas lines (where permitted). | Common in plumbing (water supply, drainage, PEX), fuel lines (low-pressure, following regulations), air conditioning and refrigeration (depending on system). |
Swaging vs. Crimping: Choosing the Right Connection Method
Selecting the right connection method between swaging and crimping hinges on several key factors. Here’s a deeper dive to help you make the most informed decision for your project:
Application Requirements:
- Pressure Rating: Consider the maximum pressure your system will experience. Both swaging and crimping can create secure connections, but if you’re dealing with high-pressure applications like hydraulic lines, swaging might be a preferred choice due to its potential for a slightly stronger grip.
- Material Compatibility: Ensure the chosen method (swaging or crimping) is compatible with the materials of your pipe or hose and the fitting itself. This is crucial to avoid issues like corrosion or weakened connections. For example, swaging is commonly used with copper and PEX tubing, while crimping offers more versatility for various materials.
- Environmental Conditions: If your connection will be exposed to harsh environments like extreme temperatures, vibrations, or corrosive elements, prioritize methods offering superior durability. Swaging might be a good option for such scenarios due to the tight, often permanent, nature of the connection.
Ease of Use:
- Skill Level: If you’re a DIY enthusiast and are comfortable mastering a new technique, swaging can be a viable option. However, crimping might be simpler for beginners as it often involves selecting the right ferrule size and using a dedicated crimping tool.
- Project Complexity: For projects with numerous connections, the speed advantage of either method might be a factor. Both swaging and crimping can be relatively fast once you’re familiar with the process.
- Availability of Tools: If you already have a crimping tool and compatible ferrules readily available, crimping might be the more convenient choice. However, if you need to purchase new tools altogether, swaging tools tend to be generally less expensive.
Additional Considerations:
- Reusability: If your project requires frequent disassembly and reassembly, crimping might be a better option, especially if the specific ferrule type allows for reusability. Swaged connections are typically considered permanent due to the deformation of the fitting during the crimping process.
- Visual Appeal: While functionality is paramount, consider the aesthetics of your project if exposed plumbing is a factor. Some swage fittings offer a more polished look with chrome or nickel finishes, while crimped connections might have a bulkier appearance due to the ferrule.
Always Remember:
- Manufacturer‘s Instructions: Regardless of the chosen method, always follow the manufacturer‘s instructions for proper installation. This ensures you use the correct tools, fittings, and techniques for a secure and leak-proof connection.
- Local Building Codes: In some cases, local building codes might have restrictions on the use of swaging or crimping for specific applications. Always consult your local regulations or a qualified professional if unsure.
By carefully considering these factors, you can confidently choose between swaging and crimping for a robust and reliable connection in your next project.