In the industry of diesel engines, keeping the fuel flowing smoothly is paramount. A reliable fuel delivery system is essential for optimal performance, from the mighty workhorses of construction equipment to the dependable hearts of commercial trucks. Hydraulic hoses often play a crucial role in this system, but are they always the right choice for diesel fuel applications?
This comprehensive guide dives deep into the filed of hydraulic hoses for diesel fuel. We’ll explore the intricacies of material selection, industry standards, pressure considerations, and best practices for ensuring a safe and efficient fuel delivery system.
What Is Diesel Fuel
Diesel fuel is a liquid fuel primarily used in diesel engines, which are compression-ignition engines. It’s a complex mixture of hydrocarbons obtained from crude oil distillation. Unlike gasoline, which is more volatile and used in spark-ignition engines, diesel fuel has a higher boiling point and viscosity. This results in a slower, more controlled combustion process, making it suitable for heavy-duty applications.
The composition of diesel fuel varies, but it typically includes alkanes, cycloalkanes, and aromatic hydrocarbons. Its cetane number, which indicates its ignition quality, is a crucial characteristic. Diesel fuel’s high energy density and efficient combustion contribute to its widespread use in transportation, construction, and power generation. However, its combustion also produces pollutants, leading to ongoing efforts to reduce emissions through fuel modifications and engine technologies.
Understanding Hydraulic Hose Material Compatibility
The key difference between a hydraulic hose and a diesel fuel hose lies in their material composition. Standard hydraulic hoses, designed for withstanding high pressure and transferring hydraulic fluids (like mineral oil), might not be compatible with diesel fuel.
Diesel fuel, with its unique chemical properties, can degrade certain hose materials over time, leading to leaks, ruptures, and potential safety hazards.
So, what materials are suitable for diesel fuel hoses?
- Synthetic Rubber: Nitrile rubber (NBR) is a popular option, offering good resistance to diesel fuel and its additives. However, it’s crucial to choose NBR hoses specifically formulated for fuel as some general-purpose NBR blends might not be suitable. Fluorocarbon rubber (FKM), also known as Viton®, provides superior resistance to a wider range of fuels and additives, but comes at a higher cost.
- Thermoplastics: Nylon (PA) hoses are increasingly being used for diesel applications. They offer good chemical resistance, lightweight construction, and transparency for visual inspection. However, nylon hoses generally have lower pressure ratings compared to rubber options.
Is Hydraulic Hose Rated for Diesel Fuel
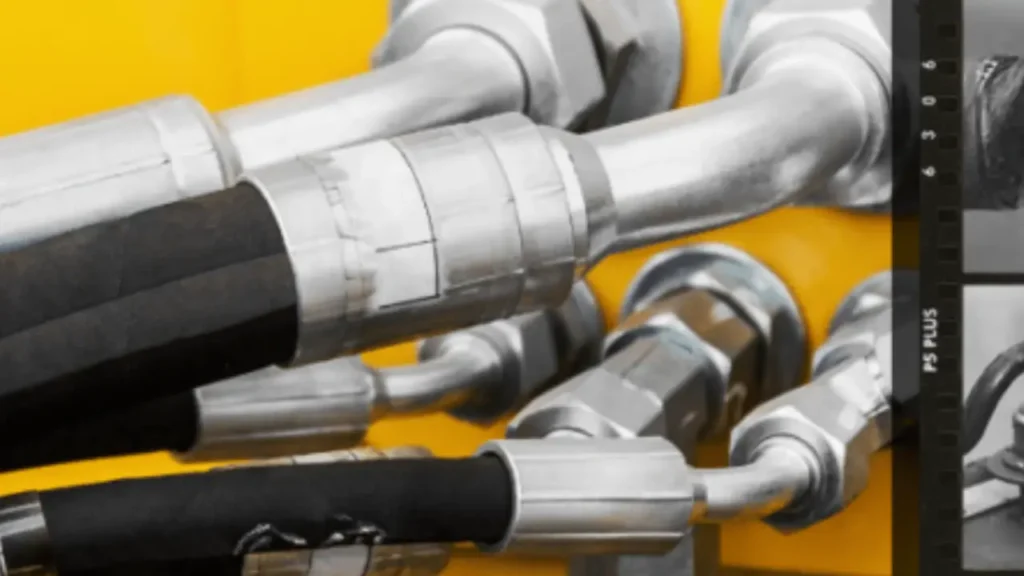
Not all hydraulic hoses are rated for diesel fuel. Here’s the breakdown:
- Standard hydraulic hoses: These are generally not suitable for diesel fuel. They might be designed for mineral oil, which has different properties than diesel fuel. Using a standard hydraulic hose with diesel fuel could lead to degradation, leaks, and potential failures.
- Specific diesel-rated hydraulic hoses: There are hydraulic hoses specifically designed and manufactured for use with diesel fuel. These hoses use materials like nitrile rubber (NBR) or fluorocarbon rubber (FKM) that are compatible with the chemical makeup of diesel fuel and its additives.
Key points to remember:
- Material matters: Choose a hose material specifically formulated for diesel fuel applications.
- Industry standards: Look for hoses that comply with standards like SAE J30R or ISO 4217 for added assurance.
- Consult a professional: If unsure about hose compatibility, consult a qualified hydraulics or fuel system specialist.
In short, while some hydraulic hoses are designed for diesel fuel, not all are. Always double-check the material compatibility and choose a hose specifically rated for diesel applications.
Can Hydraulic Hose Be Used for Diesel Fuel
You can use hydraulic hose for diesel fuel under certain conditions. Here’s the breakdown:
- Not all hydraulic hoses are created equal: Standard hydraulic hoses, designed for mineral oil, might not be compatible with diesel fuel. Diesel can degrade these hoses, leading to leaks and potential safety hazards.
- Diesel-rated hydraulic hoses exist: Look for hoses specifically designed for diesel applications. These hoses use materials like nitrile rubber (NBR) or fluorocarbon rubber (FKM) that can handle diesel fuel and its additives.
Here’s what to consider before using hydraulic hose for diesel:
- Material Compatibility: Ensure the hose material is specifically formulated for diesel fuel. Standard NBR might not be enough; consider FKM for wider compatibility.
- Industry Standards: Look for hoses that comply with SAE J30R (diesel fuel line) or ISO 4217 (fuel injection/transfer) for guaranteed compatibility.
- Pressure Requirements: The hose’s pressure rating should meet or exceed your fuel system’s pressure.
In essence, it’s best to avoid standard hydraulic hoses for diesel. Always prioritize hoses specifically designed and rated for diesel fuel applications to ensure safety and optimal performance.
If you’re unsure about hose compatibility, consult a qualified professional in hydraulics or fuel systems. They can guide you towards the right choice for your specific needs.
What Type of Hose is Best for Diesel Fuel
For diesel fuel applications, you need a hose specifically designed for fuel service. Here are some key characteristics and hose types:
Fuel-Resistant Materials: The hose must be made of materials resistant to diesel fuel and its additives. Common materials include:
- Nitrile rubber: A popular choice due to its good resistance to oils, fuels, and abrasion.
- EPDM rubber: Offers excellent resistance to ozone, heat, and weathering.
- Synthetic rubber blends: Developed for specific fuel types and operating conditions.
Pressure and Temperature Ratings: The hose must be able to withstand the pressures and temperatures encountered in the diesel fuel system.
Flexibility and Durability: The hose should be flexible enough for easy installation and routing while maintaining its structural integrity. It should also be resistant to abrasion, kinking, and other forms of wear and tear.
Industry Standards: Ensure the hose meets relevant industry standards for fuel service, such as SAE (Society of Automotive Engineers) standards.
Specific Types of Fuel Hoses:
- Fuel Injection Hoses: Designed for high-pressure fuel injection systems in modern diesel engines.
- Fuel Transfer Hoses: Used for transferring diesel fuel between tanks or vehicles.
- Return Hoses: Used to return excess fuel from the injection system to the fuel tank.
Always consult with the hose manufacturer or a qualified professional to select the most appropriate hose for your specific diesel fuel application.
Choosing the Right Material for Diesel Fuel Hydraulic Hose
Selecting the appropriate material for your diesel fuel hose depends on several factors:
- Fuel Type: Biodiesel blends or fuels with high aromatic content might require specific hose materials with enhanced compatibility.
- Temperature Range: Consider the operational temperature range of your engine. Some materials, like NBR, might show reduced performance at extreme temperatures.
- Pressure Requirements: Ensure the chosen hose meets or exceeds the pressure rating of your fuel system.
Industry Standards and Certifications:
Safety is paramount when dealing with fuel systems. Look for hoses that comply with industry standards like SAE J30R (for Diesel Fuel Line and Diesel Return Line Hose) or ISO 4217 (for Fuel Injection and Transfer Hoses). These standards ensure the hoses meet specific performance and material compatibility criteria.
Hydraulic Hose Construction
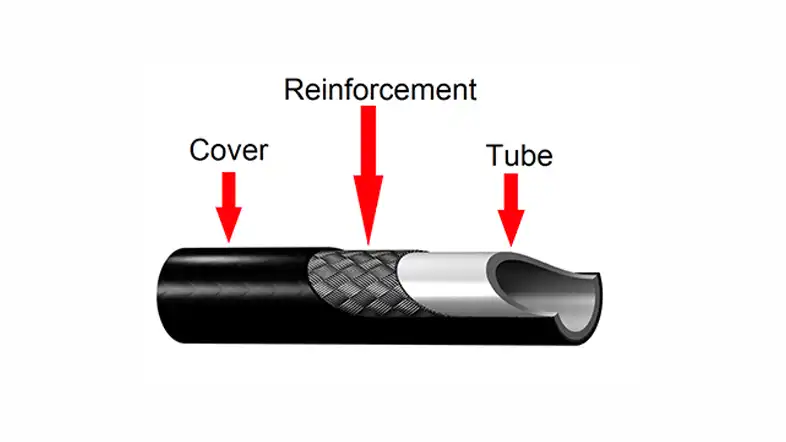
Material selection is just one piece of the puzzle. The overall construction of the hose also plays a vital role:
- Inner Tube: This is the layer that comes in direct contact with the fuel. The chosen material must be resistant to degradation and ensure minimal fuel permeation.
- Reinforcement Layer: This layer provides strength and helps the hose withstand pressure. Common options include braided steel or synthetic fibers. The type and braid pattern of the reinforcement will impact the flexibility and pressure rating of the hose.
- Outer Cover: This protects the hose from external abrasion, weather elements, and potential ozone exposure.
Choosing the Right Construction:
Consider these factors when selecting the hose construction:
- Working Pressure: The chosen hose must handle the maximum pressure encountered in your fuel system, with a safety factor built-in.
- Flexibility: If frequent bending is involved, a hose with a more flexible construction might be necessary.
- Environmental Considerations: Choose a cover material that can withstand the expected environmental conditions, including temperature extremes, sunlight exposure, and potential contact with chemicals.
Selecting the Perfect Diesel Fuel Hose
Now that you understand the importance of material compatibility and hose construction, here’s a step-by-step guide to selecting the perfect diesel fuel hose:
- Identify Your Fuel Type: Know the specific type of diesel fuel you’ll be using, including any biodiesel blends or special additives.
- Determine Pressure Requirements: Consult your engine manual or equipment specifications to find the working pressure of your fuel system.
- Consider Environmental Conditions: Factor in expected temperature range, potential exposure to sunlight, and any other relevant environmental factors.
- Choose the Right Material and Construction: Based on the above factors, select a hose material and construction that meets your specific needs. Opt for hoses that comply with relevant industry standards.
- Consult with a Professional: If you have any doubts or need assistance selecting the right hose, don’t hesitate to consult with a qualified hydraulics or fuel system specialist.
How to Install Hydraulic Hoses for Diesel Fuel Line
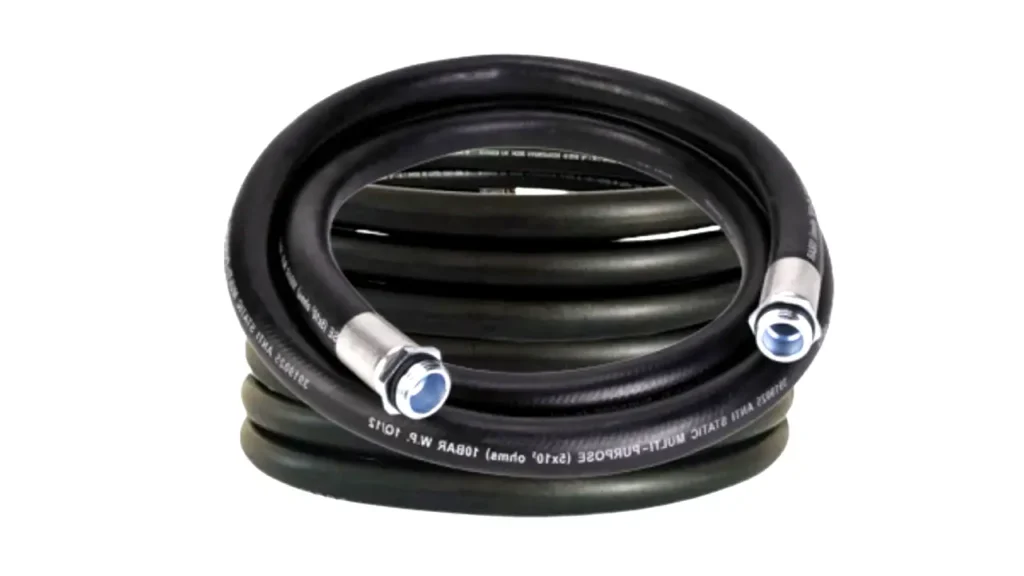
Installing hydraulic hoses for diesel fuel lines requires careful attention to detail and adherence to safety standards. Proper installation ensures leak-free connections and optimal fuel delivery, preventing potential hazards and system failures.
Here’s a step-by-step guide to installing hydraulic hoses for diesel fuel lines.
Step 1: Preparing the Hose and Fittings
The initial stage involves meticulous preparation to ensure compatibility and cleanliness. Begin by selecting hoses and fittings specifically rated for diesel fuel. Verify that the hose material is resistant to diesel’s chemical properties and that the pressure rating exceeds the system’s maximum operating pressure. Inspect all fittings for damage or defects, and ensure they are clean and free of debris.
Correct selection of the hose and fittings, and a clean workspace, is paramount. Any contamination can cause issues with the fuel system. The hose must be rated for diesel fuel, and the pressure rating must be sufficient.
Cut the hose to the required length using a specialized hose cutter to ensure a clean, square end. Avoid using saws or abrasive tools, as they can leave debris and damage the hose. Clean the hose’s interior with compressed air or a suitable solvent to remove any particles or contaminants. Lubricate the hose end and fitting with diesel fuel or a compatible lubricant to facilitate assembly.
Step 2: Assembling the Hose and Fittings
Slide the appropriate ferrule or crimp sleeve onto the hose end, ensuring it is correctly oriented. Insert the fitting into the hose end until it bottoms out, ensuring a secure connection. Align the ferrule or crimp sleeve with the crimping marks on the fitting, if applicable. Use a hydraulic crimping machine or a manual crimper to compress the ferrule onto the hose end, following the manufacturer’s specifications for crimping pressure and die selection.
Accurate crimping is crucial for a secure and leak-free connection. Over-crimping can damage the hose or fitting, while under-crimping can result in leaks. Follow the manufacturer’s crimping specifications closely, and use calibrated crimping equipment. Inspect the crimped connection for any signs of damage or deformation.
After crimping, inspect the hose assembly for any signs of damage or deformation. Verify that the ferrule is evenly compressed and that the hose is securely held in place. Perform a pull test to ensure the ferrule’s grip strength. Check that the hose is properly aligned with the fitting, without any excessive bending or twisting.
Step 3: Installing the Hose Assembly
Position the hose assembly in the desired location, ensuring it is routed correctly and avoids any sharp bends, kinks, or abrasion points. Secure the hose assembly using appropriate clamps or brackets, ensuring it is adequately supported and protected from movement or vibration. Connect the hose assembly to the fuel system components, such as fuel pumps, filters, or injectors, using the appropriate fittings and adapters.
Proper routing and secure connections are essential for preventing leaks and ensuring optimal fuel delivery. Avoid routing the hose near heat sources or sharp edges that could damage it. Ensure all connections are properly tightened and sealed to prevent leaks. Inspect the installed hose assembly for any signs of stress or strain.
After installation, perform a pressure test to ensure the connection is leak-free and can withstand the system’s operating pressures. Monitor the connection for any signs of leaks or pressure drops. Document the test results and retain them for quality control and future reference.
Step 4: Testing and Inspection
Following installation, conduct a thorough inspection of the hose assembly to verify its integrity. Check for any signs of leaks, damage, or improper connections. Start the engine and visually inspect the hose assembly for leaks or signs of stress while the fuel system is under pressure. Use a leak detection solution, such as soapy water or a specialized fluid, to identify any subtle leaks.
Testing is the only way to be sure that the hose assembly is safe for use. Any sign of a leak, or pressure drop, means that the assembly is not safe.
Document all test results, including pressure readings, observations, and any detected leaks. Retain these records for quality control and future reference. This documentation is essential for ensuring consistency and traceability in your fuel systems.
Conclusion
Selecting the right hydraulic hose for diesel fuel applications is crucial for ensuring safety, reliability, and optimal performance. By carefully considering factors such as pressure, temperature, chemical compatibility, and abrasion resistance, you can choose the ideal hose for your specific needs.
Remember, using the wrong type of hose can lead to leaks, hose failure, and potential damage to the fuel system. Always prioritize safety and consult with qualified professionals for specific applications and recommendations.
Ready to upgrade your diesel fuel systems with high-quality hydraulic hoses?
Explore our wide selection of wholesale hydraulic hoses at kingdaflex.com. We offer a variety of hoses specifically designed for diesel fuel applications, ensuring optimal performance and long-term reliability. Contact us today for a quote or to discuss your requirements with our experienced hydraulic hose team.