Abrasive sandblasting hoses are the unsung heroes of surface preparation, playing a vital role in industries ranging from construction to automotive. Choosing the right hose is crucial for efficiency, safety, and cost-effectiveness.
This ultimate guide dives deep into the world of abrasive sandblasting hoses. We’ll explore their construction, the various types available, key factors to consider when selecting a hose, and best practices for maintenance and safety, empowering you to make informed decisions.
What Is An Abrasive Sandblasting Hose?
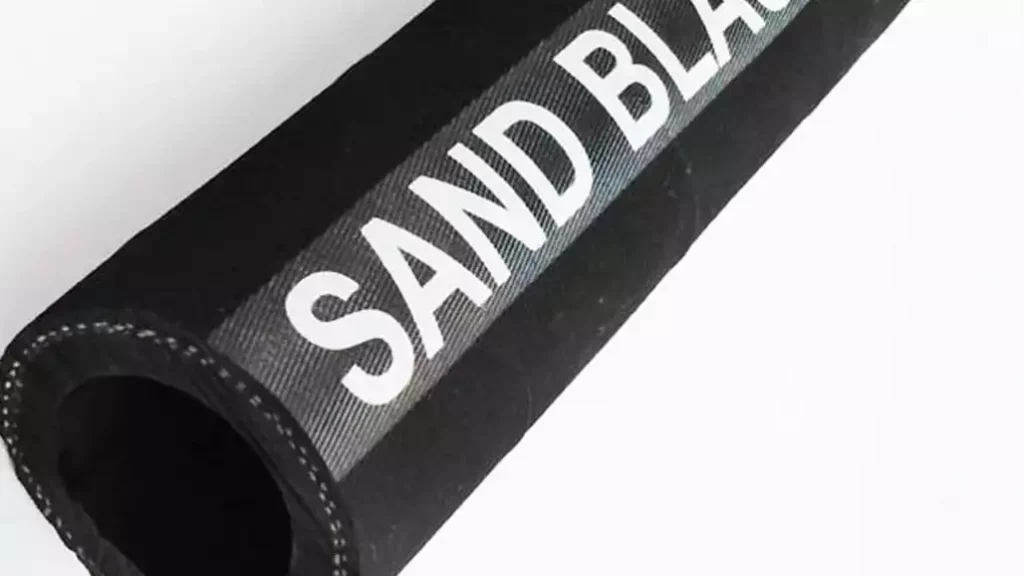
An abrasive sandblasting hose is a specialized type of hose that is used to convey abrasive materials, such as sand, steel shot, and aluminum oxide, from a sandblasting machine to the target surface.
These sandblast hoses are designed to withstand the high pressure and abrasion that is involved in sandblasting operations.
How Does An Abrasive Sandblasting Hose Work?
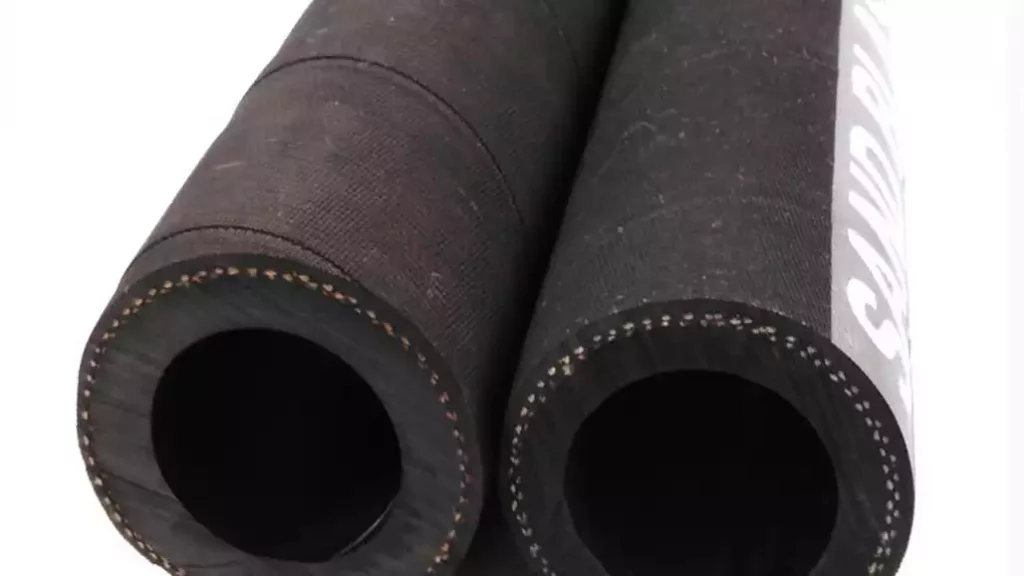
A sandblasting hose works by connecting the sandblasting machine to the target surface. The sandblast hose is filled with abrasive material, which is then propelled at high speeds through the hose and out of the nozzle. The force of the abrasive material hitting the surface is what causes the cleaning or preparation process.
An abrasive sandblasting hose functions as a conduit, expertly channeling a high-velocity stream of abrasive material from the sandblasting machine to the targeted surface.
Compressed air, generated by an air compressor, acts as the propellant, creating the necessary pressure to drive the abrasive media through the hose. This powerful mixture exits the hose through a specialized nozzle, which focuses the stream and directs the abrasive particles with force against the workpiece.
The impact of the abrasive material against the surface is what achieves the desired outcome, whether it’s cleaning away old coatings, removing rust and contaminants, smoothing rough areas, or preparing a surface for further treatment.
The sandblast hose itself is engineered to withstand this demanding process. It features a robust inner lining, typically made of abrasion-resistant rubber, to prevent wear from the fast-moving media. Reinforcement layers within the hose structure provide the strength to handle the high pressure, while the outer cover offers protection against external abrasion and environmental factors.
Different Types of Abrasive Sandblasting Hoses
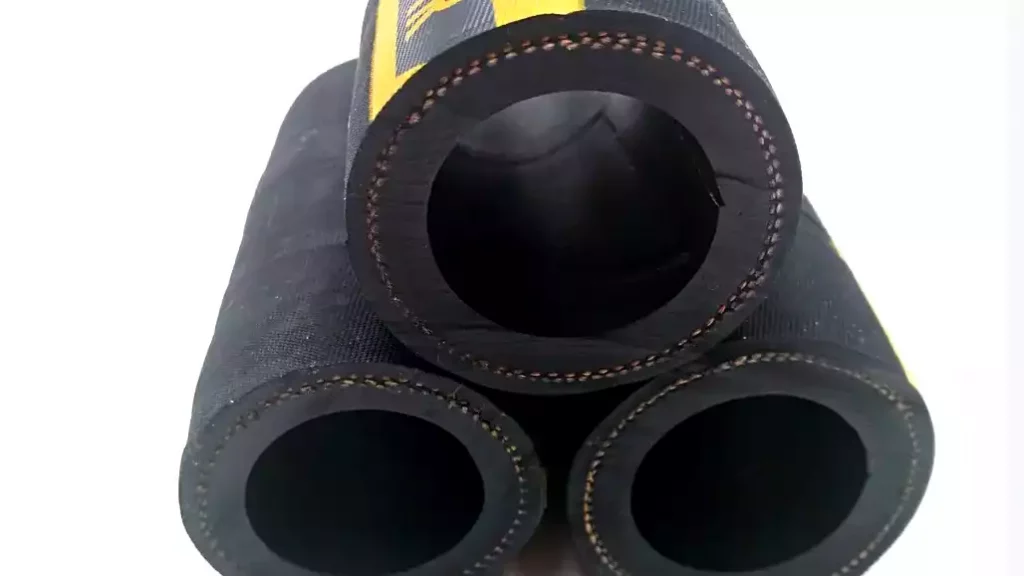
Selecting the right abrasive sandblasting hose is critical for optimal performance and safety. Various types cater to specific applications and abrasive media. Understanding these differences will help you choose the most suitable hose for your needs, ensuring efficiency and longevity of both the hose and your sandblasting equipment.
Let’s explore the common types of abrasive sandblasting hoses available.
Rubber Abrasive Hoses
Rubber abrasive hoses are a common choice due to their flexibility and good abrasion resistance. They are typically constructed with multiple layers, including a wear-resistant inner tube, reinforcement plies for pressure handling, and an outer cover for protection against environmental factors and external abrasion. These hoses offer a balance of durability and flexibility for general sandblasting tasks.
Polyurethane Abrasive Hoses
Polyurethane hoses stand out for their exceptional abrasion resistance, often outperforming rubber in demanding applications with aggressive media. While generally less flexible than rubber hoses, their extended lifespan in harsh conditions can lead to long-term cost savings. They are a preferred option when dealing with sharp or highly abrasive materials.
PVC Abrasive Hoses
PVC abrasive hoses are a more economical option suitable for lighter-duty sandblasting tasks and less abrasive media. They are typically lightweight and flexible but may not offer the same level of abrasion or pressure resistance as rubber or polyurethane hoses. These are often used in applications where cost is a primary concern and the demands are not extreme.
Anti-Static Abrasive Hoses
Anti-static abrasive hoses are crucial in environments where static electricity buildup poses a risk, such as when working with flammable materials. These hoses incorporate conductive materials that dissipate static charges, preventing sparks and ensuring a safer working environment. They are a mandatory safety feature in specific industrial settings.
How to Choose the Best Abrasive Sandblasting Hose
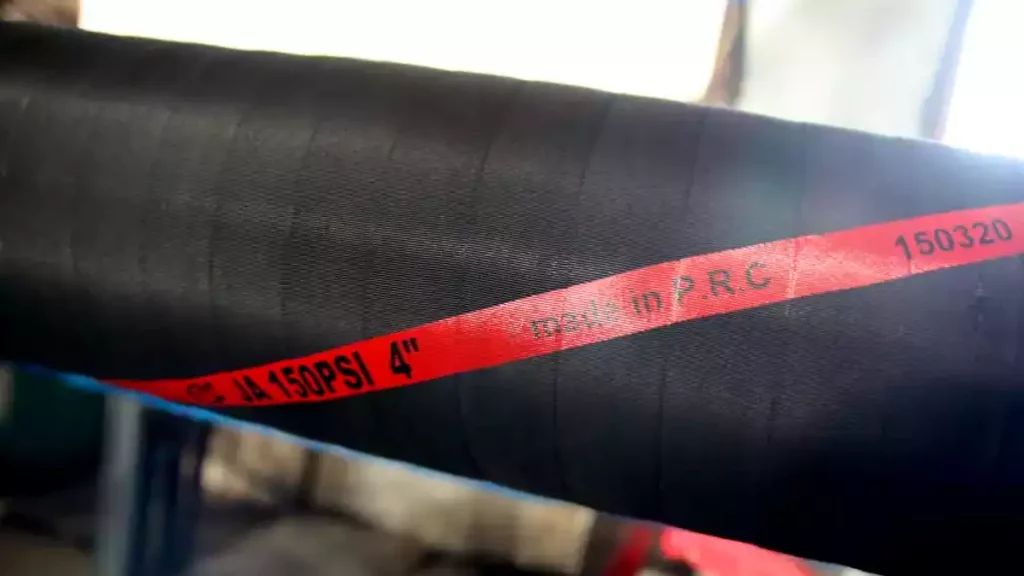
When choosing an abrasive sandblasting hose, there are several factors to consider, including the type of abrasive material being used, the size and length of the hose, and the level of pressure required for the job. Here are some tips to help you choose the best abrasive sandblasting hose for your needs:
- Consider the Type of Abrasive Material – Different abrasive materials require different types of hoses. For example, aluminum oxide is highly abrasive and requires a durable, high-pressure hose, while glass beads are less abrasive and can be used with a lighter, more flexible hose.
- Determine the Length and Size of the Hose – The length and size of the hose you choose will depend on the size of the job and the distance between the sandblasting machine and the target surface. Longer hoses may be required for larger jobs, while shorter hoses are ideal for smaller, more confined areas.
- Determine the Required Pressure – The level of pressure required for the job will depend on the type of abrasive material being used and the target surface. Higher pressure hoses are required for more abrasive materials and harder surfaces, while lower pressure hoses are suitable for softer materials and less demanding applications.
Sandblasting Hose Applications
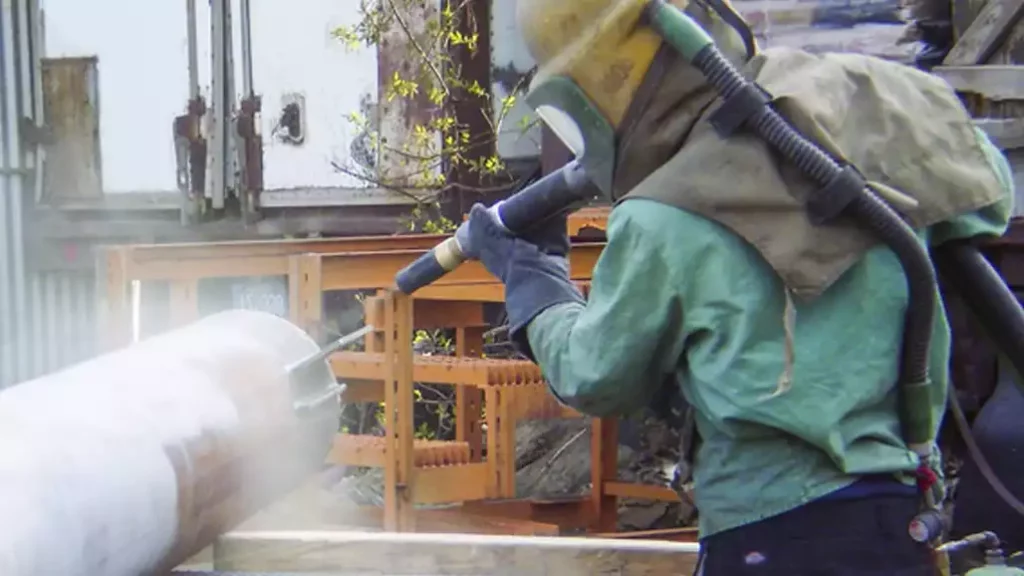
Sandblasting hoses are used in a variety of applications that require the delivery of abrasive materials under high pressure.
The following table provides some examples of common sandblasting hose applications:
Application | Description | Hose Material | Inner Diameter | Length | Pressure Rating |
---|---|---|---|---|---|
Surface preparation | Removing rust, paint, and other coatings from surfaces prior to painting or coating | Synthetic rubber | 1/2″ to 1-1/4″ | Up to 100 feet | 150 psi to 200 psi |
Shipbuilding and repair | Cleaning and removing coatings from ship hulls, decks, and tanks | Synthetic rubber or polyurethane | 3/4″ to 2″ | Up to 200 feet | 150 psi to 250 psi |
Construction | Cleaning and preparing concrete surfaces for repair or coating | Synthetic rubber | 1-1/4″ to 2″ | Up to 100 feet | 150 psi to 200 psi |
Industrial cleaning | Removing buildup and residue from equipment and machinery | Synthetic rubber or polyurethane | 1/2″ to 2″ | Up to 200 feet | 150 psi to 250 psi |
Oil and gas | Cleaning and preparing metal surfaces for welding or painting in oil rigs and refineries | Synthetic rubber or polyurethane | 1/2″ to 2″ | Up to 200 feet | 150 psi to 250 psi |
Sandblast Hose 2-Ply
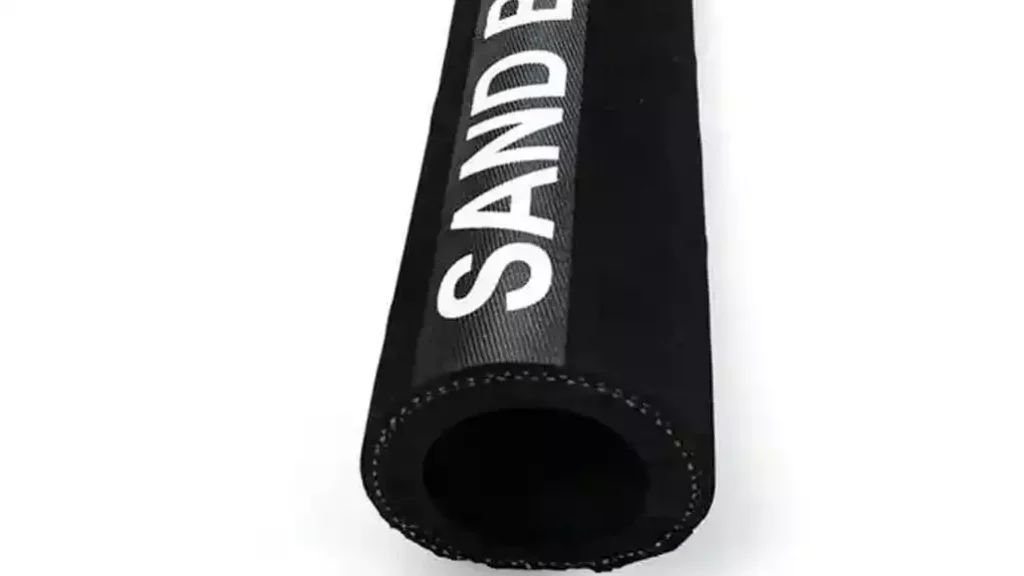
Kingdaflex Blasting, your one-stop shop for serious sandblasting equipment, provides a hardy line of 2-ply blast hoses. The Kingdaflex 2-ply hose accepts properly-sized couplings and nozzles and is compatible with all forms of blast media.
In terms of hose size offerings, the 2-ply lies between the supa hose and the 4-ply line. Whereas the supa is a skinnier and more flexible hose, the 2-ply hose offers a stiffer alternative for serious abrasive blasting jobs. But in comparison to 4-ply hoses, the 2-ply offers increased flexibility without sacrificing durability.
Each 2-ply hose comes with reinforced features, just like our 4-ply series, and is often used for similar industrial jobs.
A 2 ply sandblasting hose is made with two liners:
- An abrasive resistant natural rubber liner consisting of two layers
- A high tensile, textile cord reinforced liner.
As mentioned above, the cover of the hose is weather, ozone, and abrasion resistant. The small inner diameter sandblasting hose can be used for shorter runs and as a sandblasting cabinet hose. It can also be used as your “whip hose,” or the final 10 to 15 ft at your blast nozzle for better control.
Our 2 ply sandblasting hose is sold in 10″, 25″, 50″, 100″ and bulk 200″ +/- 6 inches.
Working Pressure: 217 psi.
In any pressure blast system, your blast hose should be three or four times the ID of your nozzle orifice. Choosing the right size for your blast hose has 2 major benefits – it prolongs the life of your hose and helps maintains adequate pressure at the blast nozzle.
Sandblast Hose 4-Ply
If you’re in the market for a serious piece of abrasive blasting equipment with more support and higher pressure than a 2 braid or Supa hose, then the 4 ply abrasive blasting hose is the natural next step.
Our 4-ply blast hose is made with two liners:
- An abrasive resistant natural rubber liner consisting of four layers with a high tensile
- A textile cord-reinforced liner
The casing is weather, ozone, and abrasion resistant, making it the ideal piece of blasting equipment for industrial settings. Crewmen typically move up to the 4-ply hose when working near railroads or shipyards knowing they can rely on the reinforced exterior. This blast hose is tough enough to withstand the typical weathering caused by dragging and won’t collapse under the weight of light traffic.
The 4-ply sandblasting hose is sold in 10″, 25″, 50″, 100″ and bulk 200″ lengths +/- 6 inches.
Work pressure: 290 psi.
How to Install Sandblasting Hose?
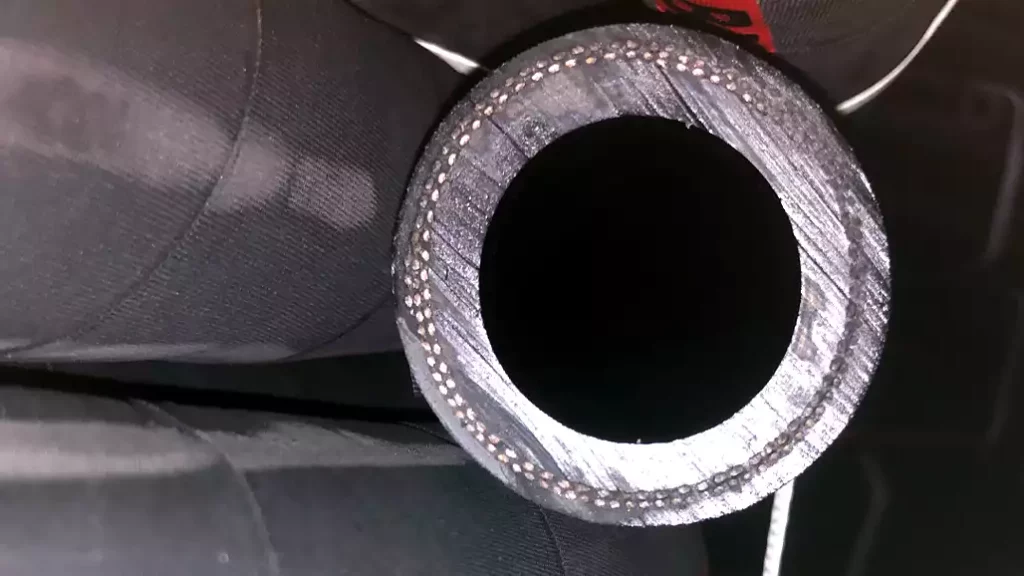
Proper installation of your sandblasting hose is essential for safe and efficient operation. A correctly installed sandblast hose minimizes the risk of leaks, bursts, and other hazards, while also ensuring optimal material flow and blasting performance. Taking the time to follow these steps carefully will contribute to a safer and more productive sandblasting process.
Let’s walk through the necessary steps to install your abrasive sandblasting hose correctly.
Step 1: Inspect the Sandblasting Hose and Fittings
Before you begin, thoroughly inspect the new sandblast hose for any signs of damage that may have occurred during shipping or handling. Check for cuts, abrasions, or deformities along the length of the hose. Also, examine the hose fittings to ensure they are the correct type and size for your equipment and are free from any damage or debris that could impede a secure connection.
Step 2: Prepare the Sandblasting Hose Ends
Ensure the ends of the sandblast hose are clean and free from any dust, dirt, or debris. If necessary, use a clean cloth to wipe the interior and exterior of the hose ends. For optimal sealing, it’s often recommended to cut the sandblasting hose ends squarely. Specialized hose cutters are available for this purpose, ensuring a clean and even surface for the fittings to mate with.
Step 3: Attach the Sandblasting Hose Fittings
Carefully slide the appropriate fittings onto the prepared ends of the sandblast hose. Depending on the type of fittings you are using (e.g., threaded, quick-connect), follow the manufacturer’s instructions for proper attachment. Ensure the fittings are fully seated and tightened according to the recommended torque specifications to create a secure and leak-proof connection. Avoid over-tightening, which could damage the hose or fittings.
Step 4: Connect to Equipment
Once the fittings are securely attached to the sandblasting hose, connect one end of the hose to the outlet of your sandblasting pot or machine and the other end to the nozzle holder. Ensure these connections are also tight and secure, following the equipment manufacturer’s guidelines. Double-check that all connections are properly aligned and there are no signs of cross-threading or misalignment that could lead to leaks or failures under pressure.
Step 5: Perform a Pressure Test
Before commencing any sandblasting operations, it is crucial to perform a pressure test to check for any leaks or weaknesses in the sandblast hose and connections.
Gradually pressurize the system to its maximum operating pressure (or slightly below, as recommended by the hose manufacturer) and carefully inspect all connections and the entire length of the sandblasting hose for any signs of leaks, bulging, or other issues. If any problems are detected, immediately depressurize the system and address the issue before proceeding with sandblasting.
How to Measure Sandblasting Hose?
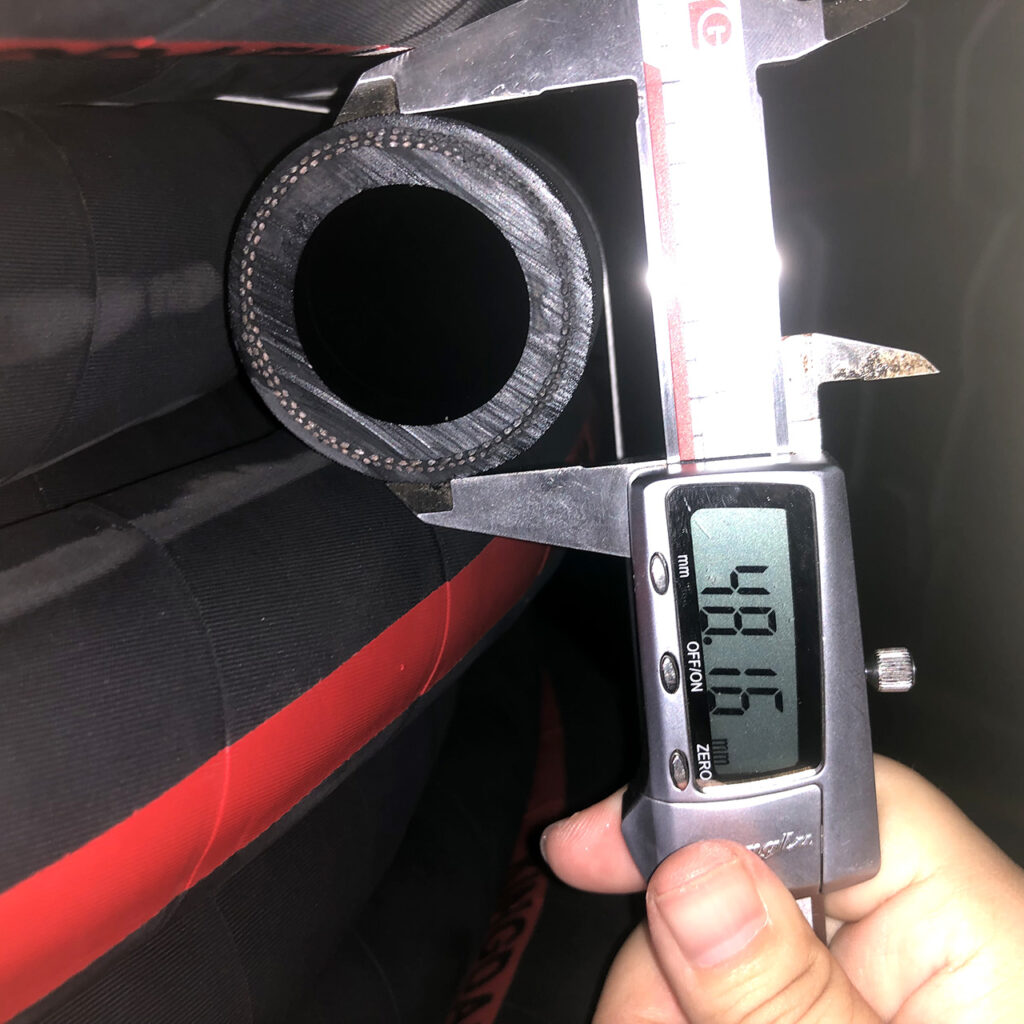
Measuring a sandblast hose accurately is crucial for ensuring compatibility with your sandblasting equipment and maintaining optimal performance. Just like measuring a hydraulic hose, precision is key. Following these steps will guide you through the process of obtaining the correct dimensions for your sandblasting hose.
Step 1: Determine the Hose Inner Diameter (ID)
The inner diameter (ID) is the measurement across the inside opening of the sandblasting hose. Using calipers or a ruler, carefully measure the distance between the inner walls at the hose end. Ensure you measure the widest part of the opening for an accurate reading. The ID is typically expressed in inches or millimeters and is a critical factor for proper material flow and fitting compatibility.
Step 2: Measure the Hose Length
To determine the correct hose length, use a measuring tape to measure from the very end of one fitting to the very end of the other fitting. If you are replacing an existing sandblast hose, lay it straight and measure its entire length, including the fittings. For new installations, consider the distance between your sandblasting pot and the work area, allowing for some slack to prevent kinking or strain during operation.
Step 3: Identify the Hose Pressure Rating
Locate the pressure rating marked on your existing sandblasting hose. This is usually printed along the side of the hose. It’s crucial to select a replacement hose with an equal or higher pressure rating to ensure it can safely handle the operating pressure of your sandblasting equipment. Using a hose with an insufficient pressure rating can lead to dangerous failures.
Step 4: Determine the SandblastHose Material
Examine your current sandblasting hose to identify the material it’s made from. Common materials include rubber, polyurethane, or a combination of both. The material type is important for compatibility with the abrasive media you’ll be using and the overall durability of the hose. Ensure the new hose material is suitable for your specific application.
Step 5: Identify the Fitting Types and Sizes
Carefully inspect the fittings on your current sandblasting hose. Note the type of connection (e.g., threaded, quick-connect) and the size of the threads or couplings. You will need to match these fittings with your new sandblast hose to ensure a secure and leak-proof connection to your sandblasting equipment and nozzle holder. Mismatched fittings can lead to leaks and safety hazards.
Conclusion
In conclusion, selecting the right abrasive sandblasting hose is paramount for achieving efficient, safe, and cost-effective surface preparation. Understanding the different hose types, installation procedures, and measurement techniques empowers you to make informed decisions tailored to your specific needs and applications. By considering factors like abrasion resistance, pressure rating, and material compatibility, you can optimize your sandblasting operations.
This ultimate guide has provided a comprehensive overview of abrasive sandblasting hoses, equipping you with the knowledge to navigate the selection process. Remember that proper installation and regular inspection are crucial for maximizing the lifespan and safety of your hose. Investing in a quality hose that meets your requirements will ultimately lead to improved productivity and reduced downtime.
For those seeking reliable and high-quality abrasive sandblasting hoses, consider exploring the offerings from Kingdaflex. They provide a wide range of hoses suitable for various industrial applications. Contact Kingdaflex today to get wholesale sandblasting hose solutions that meet your specific demands and ensure optimal performance in your abrasive blasting projects.