As an essential component of offshore oil and gas operations, floating hoses are subject to harsh environmental conditions and constant wear and tear. The floating hose can lead to dangerous accidents and expensive downtime without proper maintenance.
This article provides essential guidelines on floating hose maintenance to ensure safety, longevity, and efficient operation.
Introduction
Offshore oil and gas operations rely heavily on floating hoses to transport oil and gas between production platforms and processing facilities. These hoses are designed to withstand extreme weather conditions, waves, currents, and other environmental factors. However, regular maintenance is essential to keep them in good condition and prevent accidents.
Understanding Floating Hoses
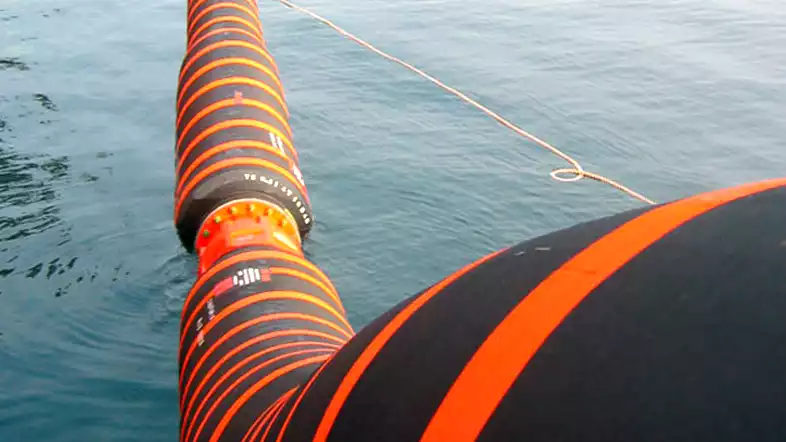
Floating hoses are typically made of a flexible rubber or plastic material that is reinforced with multiple layers of steel cables or synthetic fibers. These hoses are designed to withstand high pressures and bending moments while remaining buoyant in water.
Common Causes of Floating Hose Failures
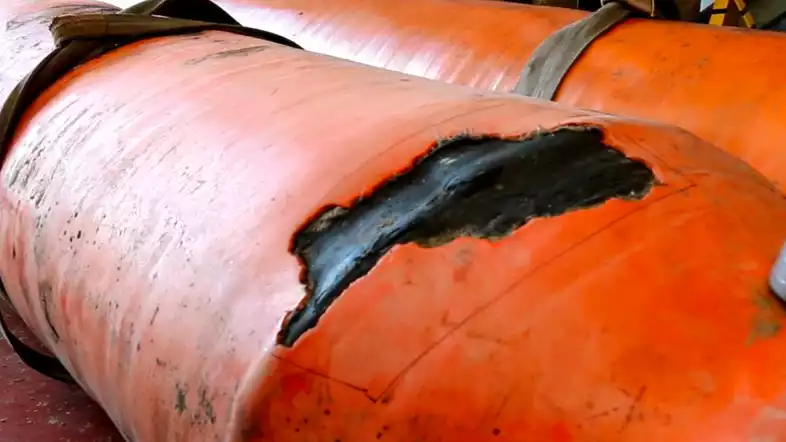
Floating hoses can fail for various reasons, including wear and tear, exposure to sunlight, corrosion, and rough handling. Some of the most common causes of floating hose failures are:
Abrasion
Floating hoses are subject to constant rubbing against other equipment or the seabed, causing wear and tear on the surface. This can lead to leaks or ruptures.
Sunlight Exposure
UV radiation from sunlight can cause the rubber material of the floating hose to degrade over time, making it more susceptible to cracking and ruptures.
Corrosion
Saltwater and other chemicals can cause corrosion on the steel cables or synthetic fibers of the floating hose, weakening its structural integrity.
Bending Fatigue
Floating hoses are designed to bend and flex with the movement of the sea. However, repeated bending can cause the reinforcing cables to break, leading to catastrophic failure.
Floating Hose Maintenance Guidelines
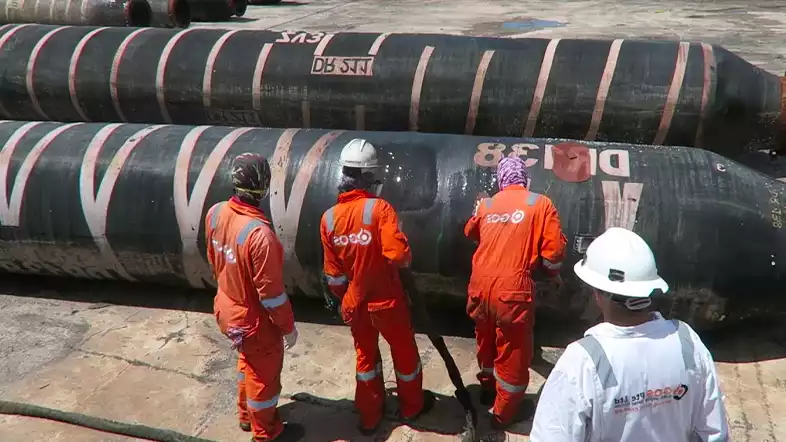
Regular maintenance and inspection of floating hoses are essential to ensure their safe and efficient operation. Here are some guidelines to follow:
Inspection
Inspect the floating hoses regularly for signs of wear and tear, abrasion, cracking, or any other visible damage. Check the end fittings, seals, and clamps for corrosion or signs of looseness.
Floating hoses are a crucial component in offshore oil and gas operations as they transport fluids from one location to another. However, like any equipment, they are subject to wear and tear over time, which can result in leaks, ruptures, and other issues. That is why it is crucial to perform regular inspections to identify any potential problems and ensure that the hoses are in good condition.
During inspections, it is essential to look for signs of wear and tear, such as cracks, abrasions, and deformations in the hose. Additionally, the connections between the hoses and the equipment must be thoroughly checked to ensure they are secure and free of damage. Other components, such as the buoyancy modules and the anchoring systems, should also be inspected for any signs of damage or wear.
One of the critical factors in performing successful inspections is to follow a well-defined inspection plan. The plan should include specific details of what components to inspect, how to inspect them, and how often the inspection should take place. It should also specify the equipment required, such as cameras, gauges, and other tools.
It is also important to note that inspections should not only be performed when issues are identified. Regular inspections can help identify potential problems before they occur, preventing costly downtime and repairs. It is recommended that floating hoses be inspected at least twice a year, depending on usage and environmental conditions.
Floating Hose Cleaning
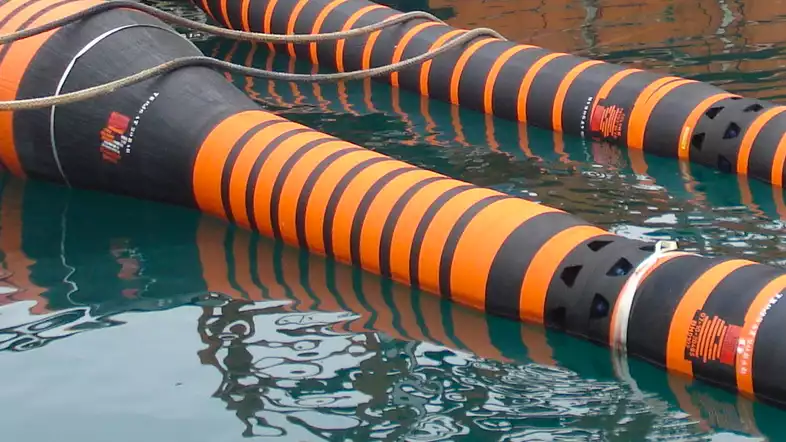
Cleaning floating hoses is another critical aspect of their maintenance. These hoses are exposed to various environmental factors such as saltwater, sand, and debris, which can lead to the build-up of dirt and other particles inside the hoses. Over time, this build-up can lead to clogs and reduce the flow of fluids through the hose.
Cleaning floating hoses involves removing any dirt or debris that has accumulated inside the hose. The cleaning process may involve the use of specialized cleaning agents or solvents that are specifically designed to dissolve and remove dirt and other particles. These agents are usually environmentally friendly and biodegradable, ensuring that they do not cause any harm to the marine environment.
It is essential to use the appropriate cleaning agent for the type of floating hose you have. For example, if the hose is made of rubber, it is recommended to use a cleaning agent that is specifically designed for rubber hoses. The cleaning agent should also be compatible with the type of fluid that the hose transports to avoid any chemical reactions that may cause damage to the hose.
Cleaning should be performed regularly, depending on the frequency of use and environmental conditions. If the hose is used in a particularly harsh environment, it may need to be cleaned more frequently to prevent the build-up of dirt and debris. It is also important to clean the hose after every use, especially if it has been exposed to harsh environmental conditions.
Floating Hose Storage
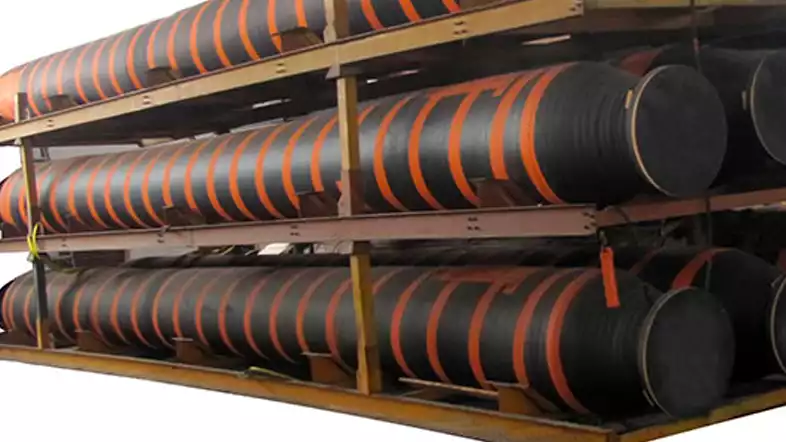
Proper storage of floating hoses is crucial to their maintenance and longevity. Hoses that are not stored correctly may be subject to damage, which can lead to leaks, ruptures, and other issues.
The first step in proper storage is to ensure that the hoses are clean and dry before storing them. Any dirt, sand, or debris left on the hose can cause damage over time, so it is important to remove these particles before storing the hose.
The hoses should be stored in a dry, cool, and well-ventilated area away from direct sunlight and sources of heat. Exposure to heat and direct sunlight can cause the hoses to degrade and become brittle over time. It is also important to avoid storing the hoses in areas where they may be subject to excessive moisture or humidity, as this can cause the hoses to deteriorate and mold to grow.
Hoses should be stored in a manner that does not cause any sharp bends or kinks, which can cause damage to the hose. It is recommended to store hoses in a straight, flat position or wound onto a reel or drum to prevent any damage during storage. Storing the hoses on a reel or drum also makes it easier to transport them to their next location.
It is important to inspect hoses before and after storage to ensure that they are in good condition. Any signs of damage, such as cracks, abrasions, or deformations, should be addressed immediately to prevent any further damage or safety concerns.
Replacement
Replace the floating hoses if there are signs of significant wear and tear, cracks, or ruptures. It is better to replace them before a failure occurs.
Conclusion
Floating hose maintenance is crucial to ensure safe and efficient offshore oil and gas operations. Regular inspection, cleaning, lubrication, proper storage, and timely replacement can extend the life of the hoses and prevent accidents.