Have you ever wondered about the journey of a hydraulic fitting from raw material to a critical component in complex machinery? The manufacturing of these seemingly small parts is a testament to precision engineering, ensuring leak-proof connections under immense pressure.
This process involves meticulous design, advanced machining, and rigorous quality control. Understanding how hydraulic fittings are made reveals the dedication to durability and performance that underpins every reliable hydraulic system.
What Are Hydraulic Fittings?
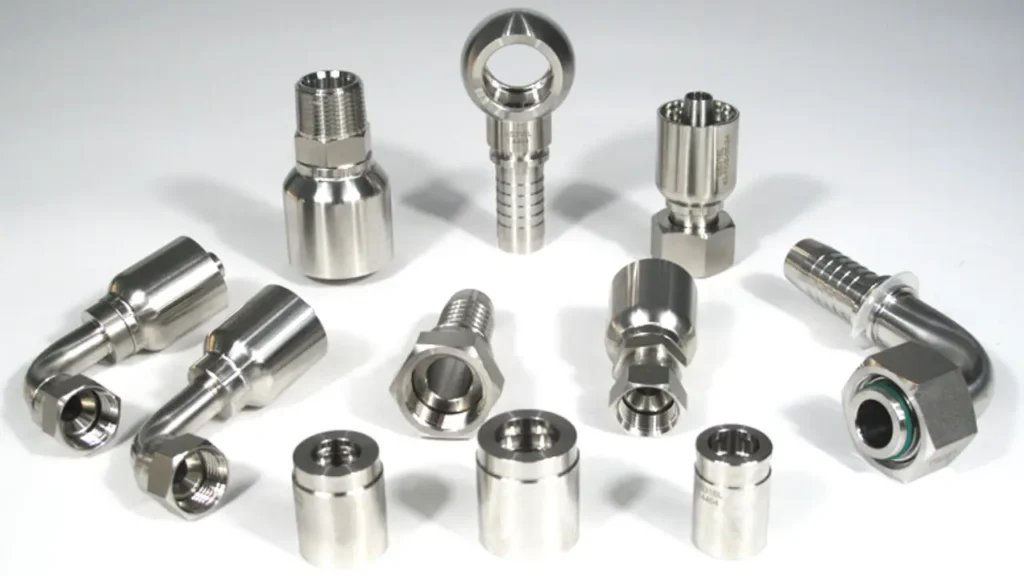
Hydraulic fittings are specialized mechanical components designed to connect various parts of a hydraulic system, such as hoses, tubes, pipes, and other hydraulic components (e.g., cylinders, pumps, valves). Their primary function is to facilitate the controlled flow of hydraulic fluid while maintaining a secure, leak-proof connection under high pressure and often demanding environmental conditions.
Without these fittings, a hydraulic system would be unable to transmit power or perform its intended tasks.
- Connection and Flow: They provide the pathways for hydraulic fluid to travel between different components, allowing it to be directed, combined, or diverted as needed within the system.
- Leak Prevention: A crucial role of hydraulic fittings is to create and maintain a tight seal, preventing the leakage of hydraulic fluid, which is essential for system efficiency, safety, and environmental protection.
- Pressure Containment: Hydraulic systems operate under significant pressure. Fittings are specifically engineered and manufactured to withstand these high pressures without rupturing or failing, ensuring the integrity and safety of the entire system.
- Variety and Versatility: Due to the wide range of applications, operating conditions, and international standards, hydraulic fittings come in numerous types, sizes, materials, and sealing methods. This versatility allows them to be tailored to specific operational needs, from heavy machinery to aerospace systems.
How Are Hydraulic Fittings Made?
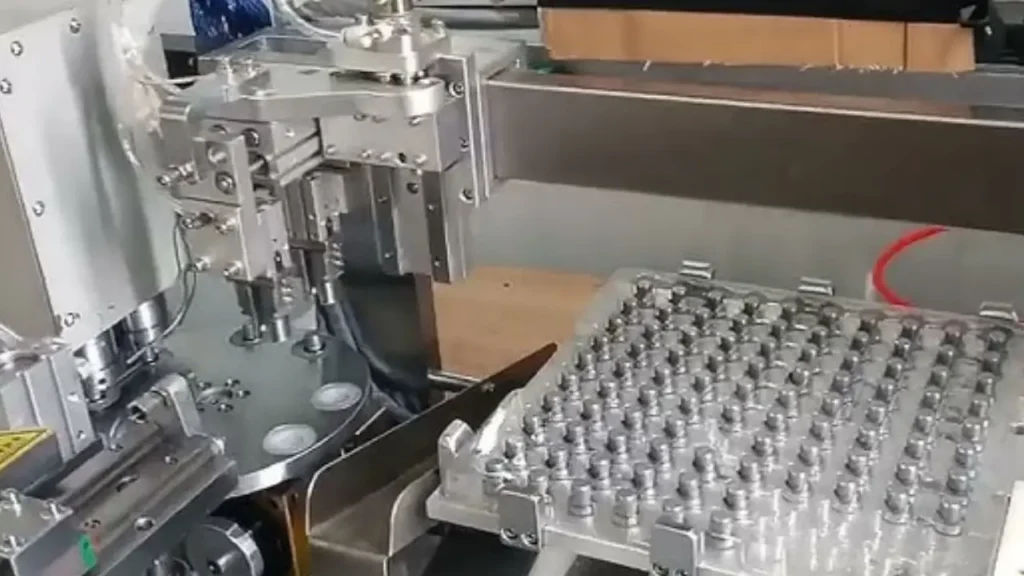
The precision and complexity involved in hydraulic fitting manufacturing are crucial for the performance and safety of hydraulic systems worldwide. Producing these vital components requires a sophisticated blend of material science, advanced machining processes, and stringent quality control, ensuring they withstand extreme pressures and environments.
Step 1: Design and Material Selection
The manufacturing process begins long before any material is cut, with meticulous design. Engineers use CAD (Computer-Aided Design) software to create detailed blueprints of each fitting, considering its specific function, pressure rating, and the type of hydraulic system it will serve. This design phase also involves determining the optimal material, which is critical for the fitting’s performance and longevity.
Common materials include carbon steel for its strength and cost-effectiveness, stainless steel for superior corrosion resistance in harsh environments, and brass for its ductility and excellent corrosion resistance in certain fluid applications. The choice of material is also influenced by the intended working pressure, temperature range, and compatibility with various hydraulic fluids, ensuring the finished fitting meets demanding operational requirements.
Step 2: Raw Material Cutting Process
Once the design and material are finalized, the manufacturing moves to the raw material cutting stage. Large bars or rods of the selected metal are precisely cut into smaller segments that will form the individual fittings. This initial cutting is crucial for efficiency and minimizing material waste in subsequent machining operations.
Advanced cutting technologies, such as high-speed saws or abrasive cutting machines, are employed to ensure clean, accurate cuts. The size of these raw slugs is carefully controlled, as they will serve as the blanks from which the intricate features of the hydraulic fittings will be machined. This step sets the stage for the precision shaping to follow.
Step 3: CNC Machining (Turning and Lathe Operations)
The heart of modern hydraulic fitting manufacturing lies in Computer Numerical Control (CNC) machining, particularly turning and lathe operations. In this phase, the raw metal blanks are mounted onto CNC lathes, which rotate the workpiece at high speeds while stationary cutting tools precisely remove material. This process is used to create the fitting’s cylindrical body, external diameters, and the initial formation of features like flanges and internal bores.
These multi-axis CNC machines are programmed to execute complex cuts with extreme precision, ensuring consistent dimensions and smooth surface finishes. The automated nature of CNC turning allows for high volume production with minimal human intervention, maintaining tight tolerances critical for the fitting’s integrity and ability to seal effectively under high pressure.
Step 4: CNC Machining (Milling, Drilling, and Boring)
Following the primary turning operations, additional CNC machining processes like milling, drilling, and boring are employed to create the more complex features of the hydraulic fitting. Milling operations use rotating multi-point cutting tools to shape flat surfaces, create hexagonal wrench flats, or add intricate grooves and contours that cannot be formed by turning alone.
Drilling and boring operations are critical for creating precise internal passages and cavities within the fitting, such as fluid pathways or spaces for O-rings. These CNC-controlled machines ensure that holes are drilled to exact depths and diameters, and that internal bores are perfectly concentric and smooth. This precision is vital for proper fluid flow, pressure containment, and effective sealing.
Step 5: Grinding and Finishing
After the primary machining operations, fittings often undergo grinding and finishing processes to achieve the required surface smoothness and dimensional accuracy. Grinding uses abrasive wheels to remove very small amounts of material, refining surfaces and achieving extremely tight tolerances that are difficult to reach with standard cutting tools. This step is particularly important for critical sealing surfaces where even microscopic imperfections can lead to leaks.
Finishing processes may also include deburring, which removes any sharp edges or burrs left by machining, ensuring safe handling and preventing particles from entering the hydraulic system. Polishing or honing may also be applied to specific surfaces to further improve surface finish and enhance sealing performance.
Step 6: Heat Treatment
For many hydraulic fittings, especially those made from steel, heat treatment is a crucial step that enhances their mechanical properties. This process involves heating the fittings to specific temperatures, holding them for a defined period, and then cooling them at controlled rates. Heat treatment can increase hardness, tensile strength, and fatigue resistance, making the fittings more durable and capable of withstanding high operating pressures and repetitive stress cycles without deforming or failing.
Different types of heat treatment, such as hardening, tempering, or case hardening, are chosen based on the desired final properties and the specific material of the fitting. This process is carefully controlled to prevent unwanted distortions or internal stresses that could compromise the fitting’s integrity.
Step 7: Thread Type and Surface Treatment
The creation of precise threads is fundamental to a hydraulic fitting’s ability to connect and seal. Threads are typically formed during the CNC machining phases, using specialized cutting tools or thread rolling processes. The accuracy of these threads, in terms of pitch, diameter, and form, is critical for ensuring proper engagement with mating components and for achieving a secure, leak-free connection. Various international thread standards (e.g., NPT, BSP, JIC, Metric) are meticulously replicated.
Following machining, many fittings undergo a surface treatment to enhance their corrosion resistance and overall durability. Common treatments include zinc plating (often with clear or yellow chromate), nickel plating, or black oxide coatings. These treatments provide a protective barrier against rust and chemical degradation, extending the fitting’s service life, particularly in harsh or exposed environments.
Step 8: Quality Check
The final stage in the manufacturing of hydraulic fittings is a rigorous quality check. This involves comprehensive inspections to ensure that every fitting meets the stringent specifications for dimensions, thread quality, surface finish, and material integrity. Automated optical inspection systems are often used for rapid and accurate dimensional verification, alongside manual checks.
Quality control technicians also perform functional tests, such as pressure testing, to ensure the fittings can withstand their rated working pressures without leaking or deforming. Destructive testing on a sample basis may also be conducted to verify tensile strength and burst pressure. This multi-layered quality assurance process guarantees that only high-quality, reliable hydraulic fittings reach the market.
How to Find Reliable Hydraulic Fitting Manufacturers?
Finding reliable hydraulic fitting manufacturers is crucial for ensuring the quality, safety, and longevity of your hydraulic systems. It involves a thorough vetting process that goes beyond just comparing prices. A dependable manufacturer will consistently deliver products that meet international standards, perform under demanding conditions, and offer excellent customer support.
- Certifications and Standards: Look for manufacturers holding relevant certifications like ISO 9001 (quality management) and adherence to industry standards such as SAE, DIN, BSP, and JIC. This indicates a commitment to quality control and product compatibility.
- Experience and Reputation: Prioritize manufacturers with a long-standing history in the hydraulic industry and a strong reputation for producing durable and reliable fittings. Seek out testimonials, case studies, or industry references.
- Quality Control Processes: Inquire about their internal quality control procedures, including material inspection, in-process checks, and final product testing (e.g., pressure testing, dimensional checks). A transparent QC process is a good sign.
- Material Sourcing and Traceability: A reliable manufacturer will have clear processes for sourcing high-grade raw materials and be able to provide traceability for their products, ensuring consistent quality and enabling recall if necessary.
- Production Capabilities and Technology: Assess their manufacturing facilities and the technology they employ (e.g., advanced CNC machining, robotic automation). Modern equipment often translates to higher precision and efficiency.
- Customization and Engineering Support: If you require specialized or custom fittings, evaluate their engineering capabilities and willingness to work with you on specific designs and applications.
- Customer Service and Technical Support: A good manufacturer offers responsive customer service, technical assistance, and after-sales support, which is vital for troubleshooting and ongoing relationships.
- Pricing and Lead Times: While not the sole factor, competitive pricing coupled with realistic and consistent lead times are important practical considerations.
- Market Presence and Distribution: A manufacturer with a strong global or regional presence and a robust distribution network often signifies reliability and accessibility.
Conclusion
The manufacturing of hydraulic fittings is a testament to precision engineering, involving meticulous design, advanced CNC machining, and specialized treatments. This multi-stage process ensures each fitting boasts the strength, exact dimensions, and durability required to perform reliably under demanding hydraulic pressures.
Every step, from material selection to final surface treatment, is critical in producing components that guarantee leak-free connections and extend system longevity. This rigorous approach underscores the importance of quality in hydraulic system integrity and safety.
For hydraulic fittings tailored precisely to your unique needs, look no further. You can get custom hydraulic fittings from us at Kingdaflex, engineered to the highest standards for your specific applications.