Hydraulic hose crimping is a vital process in assembling hydraulic systems, ensuring secure and leak-free connections between hoses and fittings. Understanding what it is and how it works is crucial for maintaining the integrity and efficiency of hydraulic equipment. This blog will delve into the fundamentals of hydraulic hose crimping.
We’ll explore the mechanics behind crimping, the tools involved, and the best practices for achieving reliable connections. Whether you’re a professional in the hydraulic industry or simply curious about the process, this guide will provide valuable insights into this essential aspect of hydraulic system maintenance.
What Is Hydraulic Hose Crimping
Hydraulic hose crimping is the process of permanently attaching fittings to the ends of hydraulic hoses using a specialized crimping machine. This process involves compressing a metal sleeve or ferrule around the hose end, securing the fitting in place. The crimping machine applies precise pressure to deform the ferrule, creating a tight seal that can withstand the high pressures common in hydraulic systems. This secure connection is essential for preventing leaks and ensuring the efficient transfer of hydraulic fluids.
The crimping process is critical because hydraulic systems operate under substantial pressure, and any weakness in the hose-fitting connection can lead to catastrophic failure. Proper crimping ensures that the fitting and hose become a single, integrated unit capable of handling the system’s operating pressures. Achieving this requires precise measurements, correct die selection, and accurate machine calibration. This method is the industry standard for creating reliable hydraulic hose assemblies.
Hydraulic Hose Crimping Machine
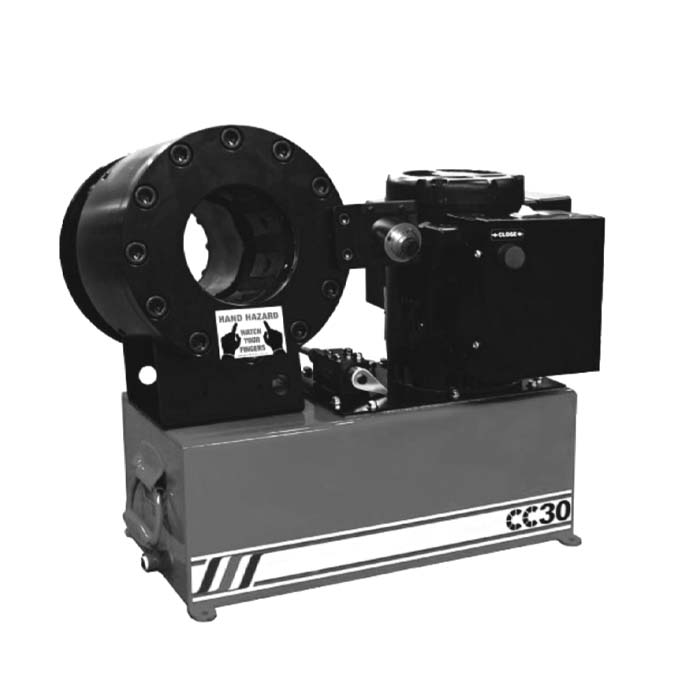
The hydraulic hose crimping machine, also called hydraulic hose crimper, hydraulic hose crimping tool, high-pressure hose crimping machine, high-pressure hose crimping tool, is used to crimp the hydraulic hose. Here we have the professional hydraulic hose crimping machine in our hydraulic hose manufacturer, so the hydraulic hose crimping machine is the machine that can enable any users to make hydraulic hose assemblies in-house.
The hydraulic hose crimping machine used in the factory is the electric hydraulic hose crimper, only experienced hydraulic hose technicist can use it well. And please do not operate the pressure hose crimping tool if you are not acknowledged of the hydraulic hose crimper.
If you want to stall the hydraulic hose for your home-depot hydraulic project, you can use the portable hydraulic hose crimping machine for hydraulic hose crimping. And the portable hydraulic hose crimping tool can help you save time and money on your hydraulic hose assemblies.
Of course, you can get the used hydraulic hose crimping machine for sale, a second-hand hydraulic crimping machine for sale, to buy a second-hand hydraulic hose crimping tool to finish the hydraulic hose crimping.
And hydraulic hose crimping is the must-have hydraulic hose tool if you were a hydraulic hose technique or hydraulic hose engineer. You need to use it any time, to replace the hydraulic hose, crimp the hydraulic hose, install the hydraulic hose fittings and etc.
How to Crimp Hydraulic Hose Fittings
Here is a short video showing the process of how crimp a hydraulic hoses.
Crimping hydraulic hose fittings accurately is crucial for ensuring leak-free and reliable connections in hydraulic systems. Improper crimping can lead to system failures and safety hazards.
We’ll guide you through the essential steps to achieve a secure and professional crimp.
Step 1: Select the Correct Hydraulic Hose and Fittings
First, you must select the appropriate hydraulic hose and fittings that are compatible with your system’s pressure, temperature, and fluid requirements. Ensure the hose and fittings are the correct size and type for your application. Inspect them for any damage or defects before proceeding. Using the right components is fundamental to achieving a reliable crimp.
Confirm that the fittings and hose are designed to work together, considering factors like material compatibility and pressure ratings. Refer to the manufacturer’s specifications to ensure you have the correct components. This careful selection prevents leaks and ensures the longevity of your hydraulic system.
Step 2: Cut and Prepare the Hose
Next, you need to cut the hydraulic hose to the required length using a specialized hose cutter. Ensure the cut is clean and square to prevent leaks and ensure proper fitting insertion. Remove any debris or frayed edges from the cut end. Proper preparation of the hydraulic hose end is critical for a secure crimp.
A clean, square cut provides a uniform surface for the fitting to grip. Use a dedicated hose cutter to avoid crushing or distorting the hose, which can compromise the crimp. Inspect the inside of the hose after cutting to ensure no debris remains that could contaminate the hydraulic system.
Step 3: Mark the Crimping Length
Measure and mark the crimping length on the hydraulic hose according to the fitting manufacturer’s specifications. This mark indicates the area where the fitting will be crimped onto the hose. Accurate marking ensures the fitting is properly seated and crimped. This step is crucial for achieving a secure and leak-free connection.
Refer to the fitting manufacturer’s crimp chart or specifications to determine the precise crimping length. Use a marker that will be visible during the crimping process. This ensures that the fitting is positioned correctly and that the crimp is applied to the appropriate area of the hose.
Step 4: Insert the Hydraulic Hose into the Fitting
Carefully insert the hydraulic hose into the fitting until it reaches the marked crimping length. Ensure the hydraulic hose is fully inserted and properly aligned with the fitting. This step is crucial for achieving a secure and leak-free connection. Proper insertion ensures the fitting grips the hose correctly during the crimping process.
Make sure the hydraulic hose is inserted straight and fully seated within the fitting. Any misalignment or incomplete insertion can result in a weak crimp or leaks. You may need to apply some force to fully insert the hose, especially with high-pressure hoses.
Step 5: Set Up the Crimping Machine
Select the correct die set for the hydraulic hose and fitting size. Install the dies into the crimping machine according to the manufacturer’s instructions. Adjust the crimping machine’s settings to the required crimping diameter, based on the fitting manufacturer’s specifications. Proper setup of the crimping machine ensures accurate and consistent crimping results.
Consult the crimping machine’s manual and the fitting manufacturer’s specifications to determine the correct die set and crimping diameter. Ensure the dies are clean and in good condition. Proper setup prevents damage to the hose and fitting and ensures a consistent crimp.
Step 6: Crimp the Hydraulic Fitting
Position the hydraulic hose and fitting assembly into the crimping machine. Activate the crimping machine to compress the dies and crimp the fitting onto the hose. Apply consistent pressure and ensure the fitting is crimped evenly around the hose. After crimping, inspect the connection to ensure it is secure and meets the manufacturer’s specifications.
Monitor the crimping process to ensure the machine applies consistent pressure and that the fitting is crimped evenly. Avoid over-crimping, which can damage the hose or fitting. Inspect the crimped connection for any signs of damage or deformation.
Step 7: Verify the Crimped Connection
After crimping, verify the connection’s integrity by measuring the crimped diameter and comparing it to the manufacturer’s specifications. Inspect the crimped area for any signs of damage, such as cracks or deformations. Perform a pull test, if required, to ensure the fitting is securely attached to the hose. Accurate verification ensures a reliable and leak-free hydraulic connection.
Use calipers or a micrometer to measure the crimped diameter and compare it to the manufacturer’s specifications. Conduct a pull test to ensure the fitting can withstand the expected operating pressures. Document your measurements and test results for quality control purposes.
Types of Hydraulic Hose Crimping Machine
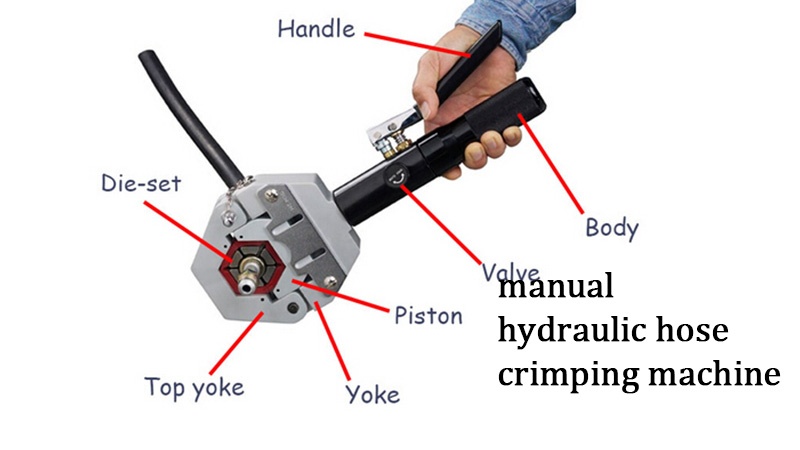
Choosing the right hydraulic hose crimping machine is essential for ensuring secure and reliable connections in hydraulic systems. Different types cater to varying needs and scales of operation. We’ll explore the main types of crimping machines to help you make an informed decision.
Manual Hydraulic Hose Crimping Machines
If you require portability and flexibility for on-site repairs or low-volume production, a manual hydraulic hose crimping machine is ideal. These machines are hand-operated, using a lever to generate hydraulic pressure. They are compact and don’t require electrical power, making them perfect for field work. You’ll find them simple to use and maintain, offering a cost-effective solution for small-scale operations.
Electric Hydraulic Hose Crimping Machines
For medium to high-volume production and applications demanding consistent crimping force, an electric hydraulic hose crimping machine is your best choice. These machines use an electric motor to generate hydraulic pressure, providing increased speed and efficiency. You’ll benefit from automated crimping, adjustable force settings, and digital control panels for precise adjustments. They are perfect for workshops and production facilities.
Pneumatic Hydraulic Hose Crimping Machines
When you need a balance of speed and power, consider a pneumatic hydraulic hose crimping machine. These machines utilize compressed air to generate hydraulic pressure, offering fast crimping cycles and consistent results. You’ll find them ideal for industrial settings where compressed air is readily available. They are compatible with automated production lines, enhancing your operational efficiency.
Automated Hydraulic Hose Crimping Machines
For the highest level of efficiency and precision in high-volume production, automated hydraulic hose crimping machines are the optimal choice. These machines incorporate robotic arms and advanced control systems to automate the crimping process. You’ll experience maximum productivity, consistent crimping quality, and reduced labor costs. They are perfect for large-scale manufacturing operations where speed and accuracy are paramount.
Hydraulic Hose Crimping Charts
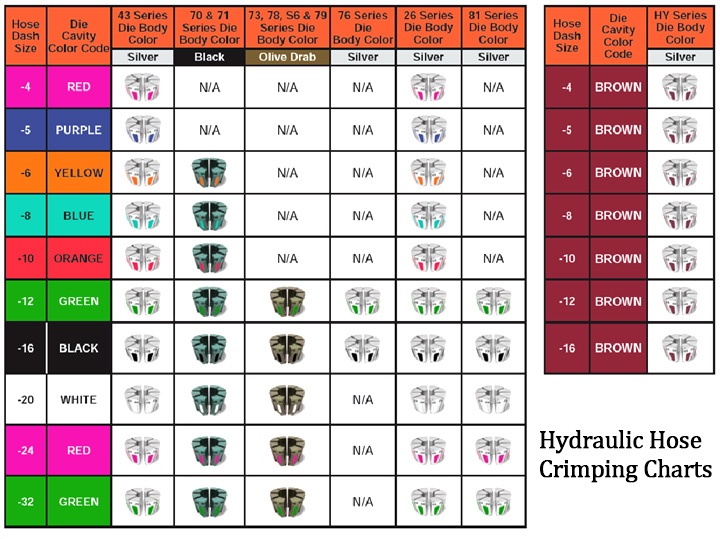
Before the hydraulic hose crimping process, it is also important to choose the right hydraulic hose crimping machine. You need to select a hydraulic hose crimper, with the proper diameter for the suitable hydraulic hose assembly.
The hydraulic hose crimping chart with the proper data can help you a lot, essential to crimp the right hydraulic hose fitting to your hydraulic hose.
Here are some tips to help you to get the hydraulic hose crimping suitable.
- Choose the right hydraulic hose fitting to match your hydraulic hose’s inner diameter.
- Select the right hydraulic hose fitting based on the dash size of the hydraulic hose. [PS: You can get the dash size of the hydraulic hose from our hydraulic hose detailed product page, and of course, you can contact us to get the proper hydraulic with the desired dash size).
- Find the corresponding hydraulic hose fitting and dash size to help you find the correct crimp die for your hose assembly.
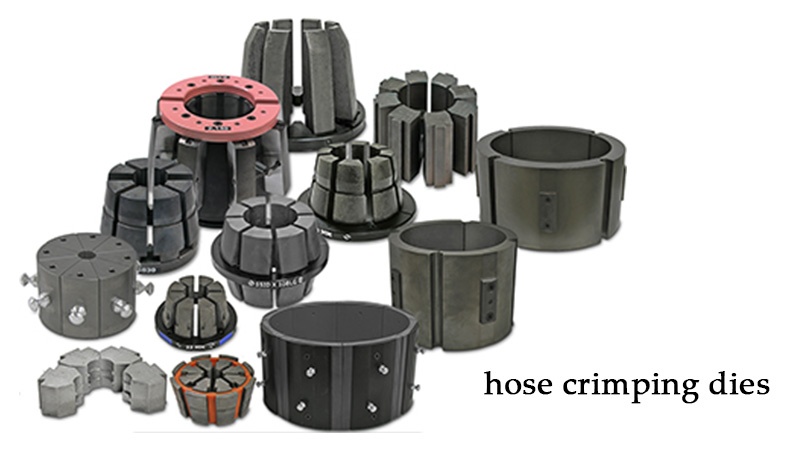
This is the hydraulic hose crimping die set above in the picture. It’s important to know the diameter of the hose crimping dies, here are many hose crimping dies to match the hydraulic hose with different specifications.
The crimping die is used for hydraulic hose crimping machines designed for crimping connectors and during electrical and installing work. It is very important to choose a suitable crimping die, with the right parameters. The right crimping die is helpful to connect the hydraulic hose fitting to the hydraulic hose firmly.
Swaging vs Crimping
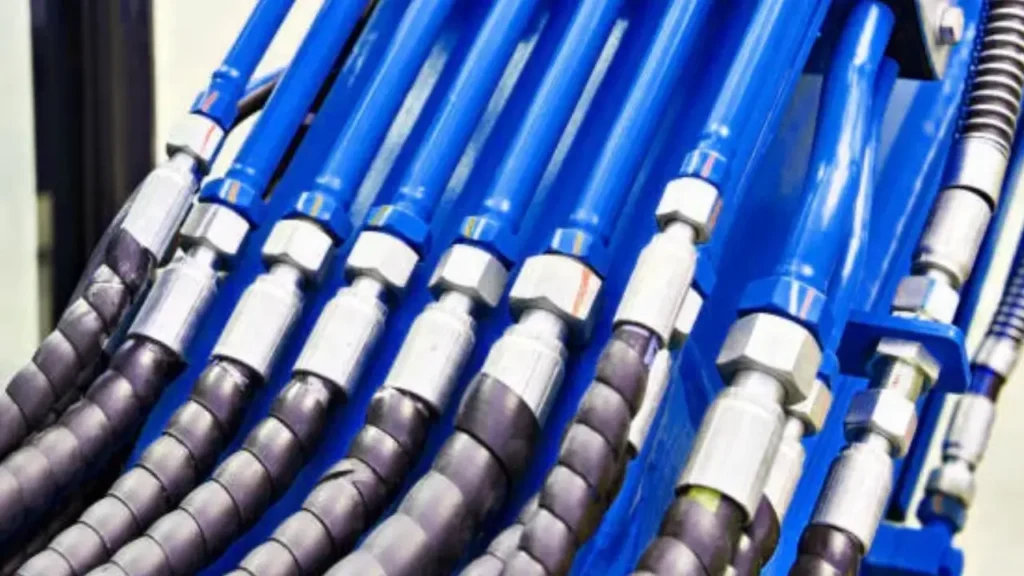
Understanding the difference between swaging and crimping is crucial for ensuring proper connections in various applications, particularly in hydraulic systems. While both processes involve deforming a material to secure a fitting, they differ in their methods and applications.
Let’s explore the key distinctions between swaging and crimping.
Swaging
Swaging is a process that reduces the diameter of a tube or fitting by applying compressive force. This is typically done using rotary swaging machines or hydraulic presses. You’ll find that swaging often involves a gradual reduction in diameter along the length of the workpiece, creating a smooth and uniform deformation.
This method is commonly used to create tapered connections or to form precise shapes in metal tubing. Swaging is known for its ability to produce strong, seamless connections and is often used in applications where high precision and strength are required.
Crimping
Crimping, on the other hand, involves compressing a fitting onto a hose or wire using a specialized crimping machine. This process focuses on deforming a specific section of the fitting to secure it onto the hose or wire. You’ll see that crimping often involves applying concentrated pressure to a localized area, creating a mechanical interlock.
This method is widely used in hydraulic hose assemblies and electrical connections, where a secure and reliable connection is essential. Crimping is valued for its speed and efficiency, making it suitable for high-volume production and on-site repairs.
In essence, swaging is a more gradual and uniform deformation process used to reduce the diameter of tubes or fittings, while crimping is a localized compression process used to secure fittings onto hoses or wires.
Conclusion
In conclusion, hydraulic hose crimping is a critical process for creating secure and reliable connections in hydraulic systems. Understanding its mechanics and best practices ensures optimal performance and safety. Proper crimping prevents leaks and failures, extending the lifespan of hydraulic equipment.
By following precise steps and using the right tools, you can achieve consistent and dependable crimps. This process is essential for maintaining the integrity of hydraulic systems across various industries. Investing in quality crimping ensures long-term efficiency and reduces maintenance costs.
For high-quality wholesale hydraulic hoses and crimping solutions, choose Kingdaflex. We offer a comprehensive range of products tailored to meet your specific needs. Contact us today for a quote and ensure your hydraulic systems operate at peak performance.