Have you ever wondered what goes into creating the robust protection that fire sleeves provide? These essential components shield critical hoses, cables, and wires from extreme heat and flames, but their advanced capabilities aren’t by chance.
Manufacturing a fire sleeve is a precise process, combining specialized materials and meticulous engineering. It’s a testament to how careful production ensures these sleeves deliver reliable safety and longevity in the most demanding environments.
Fiberglass Fire Sleeve
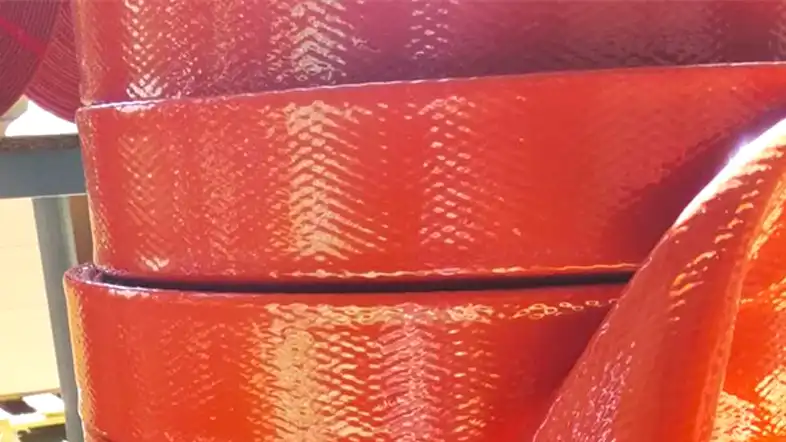
A fiberglass fire sleeve is a protective covering made from woven fiberglass fabric. It is designed to provide insulation and fire resistance to various types of hydraulic hoses, cables, and wires. The sleeve is typically installed over these components to protect them from high temperatures, flames, and other potential hazards.
Fiberglass fire sleeves are commonly used in industrial and automotive applications where there is a risk of heat or fire exposure. They can withstand extreme temperatures and provide a barrier that helps prevent the spread of fire and heat transfer to nearby objects or materials.
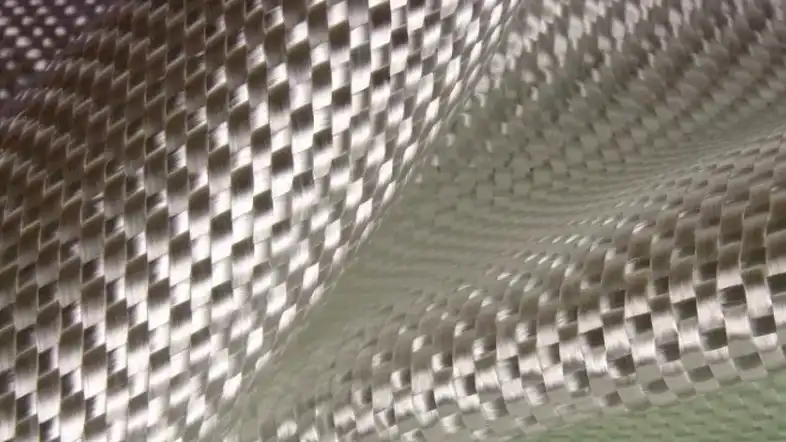
The woven fiberglass material used in these sleeves is known for its excellent thermal insulation properties. It can resist high temperatures and effectively dissipate heat, thereby reducing the risk of damage to the protected components.
Additionally, silicone fiberglass fire sleeve can also protect against abrasion, chemicals, and moisture.
These sleeves come in various sizes and configurations to accommodate different types of hoses, cables, or wires. They are typically flexible and easy to install, often featuring a hook-and-loop closure or a zipper for convenient application and removal.
The fiberglass fire sleeve is a protective covering made from woven fiberglass fabric. It is used to safeguard hoses, cables, and wires from heat, flames, and other potential hazards. Its thermal insulation properties make it an effective solution for applications where fire resistance and temperature protection are crucial.
Why is Fiberglass Fire-Resistant
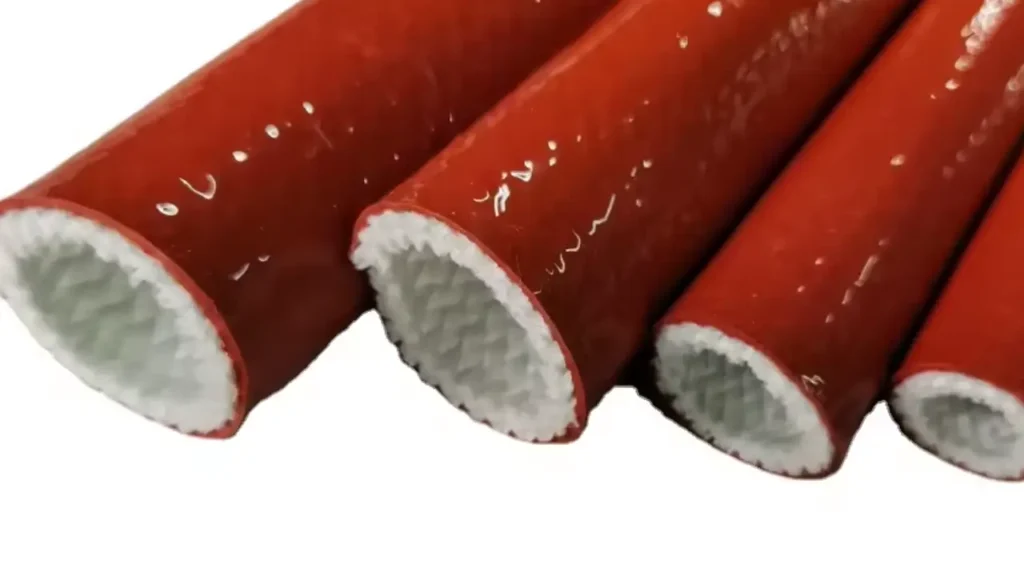
Fiberglass is considered fire-resistant due to its inherent silicone coated fiberglass fire sleeve properties:
- Inorganic Composition: Fiberglass is primarily composed of silica (silicon dioxide), the main component of glass. Silica is an inorganic material, meaning it doesn’t contain carbon and therefore cannot burn.
- High Melting Point: Glass, and consequently fiberglass, has a very high melting point. This means it can withstand significant heat exposure without melting or igniting.
- Non-Combustible: Fiberglass itself does not burn or contribute fuel to a fire. It doesn’t release flammable gases when exposed to heat.
Key Points:
- Fire-resistant, not fireproof: While highly resistant, fiberglass can still be affected by extreme heat.
- Flame-retardant treatments: Some fiberglass products may be treated with flame-retardant chemicals to further enhance their fire resistance.
Fiberglass’s inherent composition, high melting point, and non-combustible nature make it a suitable material for applications where fire resistance is important.
How to Manufacture Fire Sleeves?
Have you ever wondered about the intricate process behind creating fire sleeves? These vital protective components shield hoses and cables from extreme heat, flame, and molten splash. Manufacturing high-quality fire sleeves requires a blend of specialized materials, advanced technology, and meticulous craftsmanship to ensure they deliver superior safety and performance in demanding environments.
Gather Materials and Equipment
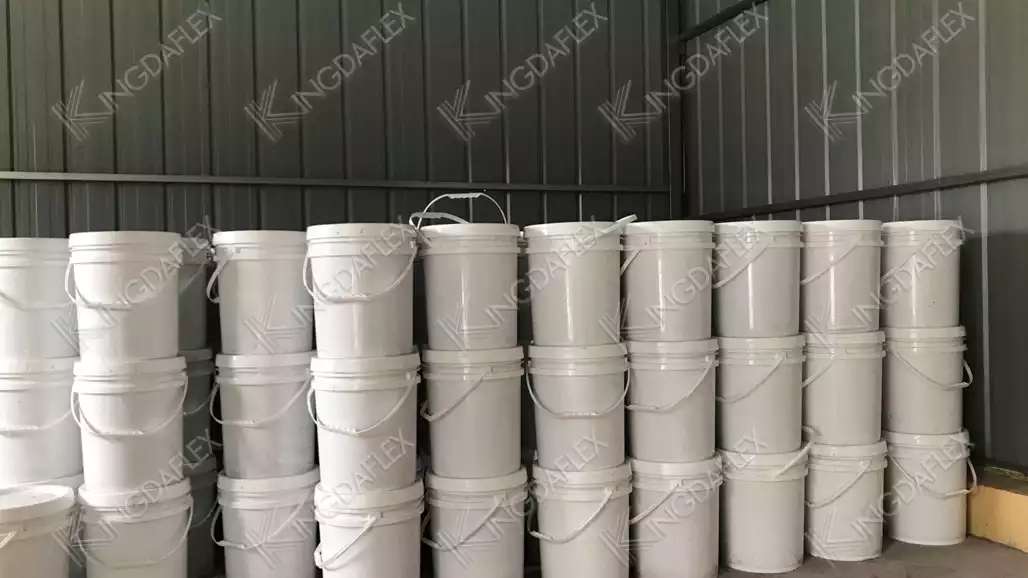
To manufacture fire sleeves, you will need the following materials and equipment:
Before manufacturing begins, all raw materials are meticulously prepared. This includes sourcing high-grade silicone rubber compounds, which provide the essential heat resistance and flexibility, and selecting durable fiber yarns, typically fiberglass or basalt, that form the sleeve’s structural core. Specialized braiding or knitting machines are set up, along with curing ovens and coating equipment.
Quality control checks are performed on all incoming materials to ensure they meet strict specifications for purity, strength, and thermal resistance. This initial quality assurance step is vital to guarantee the final fire sleeve product will perform reliably under extreme conditions, offering superior protection against fire and high temperatures.
- High-temperature resistant fiberglass yarn
- Braiding machine
- Heat-resistant silicone or other high-temperature coating material
- Measuring tape or ruler
- Cutting machine (optional)
Step 1: Mixing Silicone Rubber
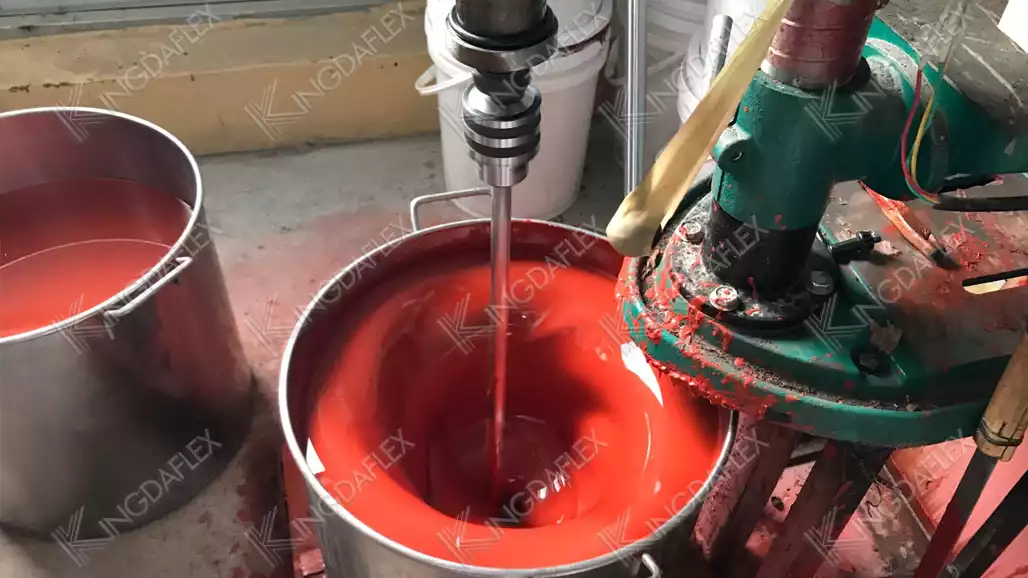
The manufacturing process begins with the careful mixing of the silicone rubber compound. Various additives, including pigments for color, catalysts for curing, and flame retardants for enhanced fire resistance, are precisely blended into the raw silicone. This ensures the compound achieves the desired consistency, elasticity, and thermal properties required for the finished fire sleeve.
This mixing stage is critical as it directly impacts the final product’s performance. The homogenous blend guarantees uniform heat resistance and durability across the entire sleeve. Automated mixing equipment precisely controls temperature and time, optimizing the compound’s characteristics for subsequent coating processes and ensuring consistent quality.
Step 2: Coiling Fiber Yarn
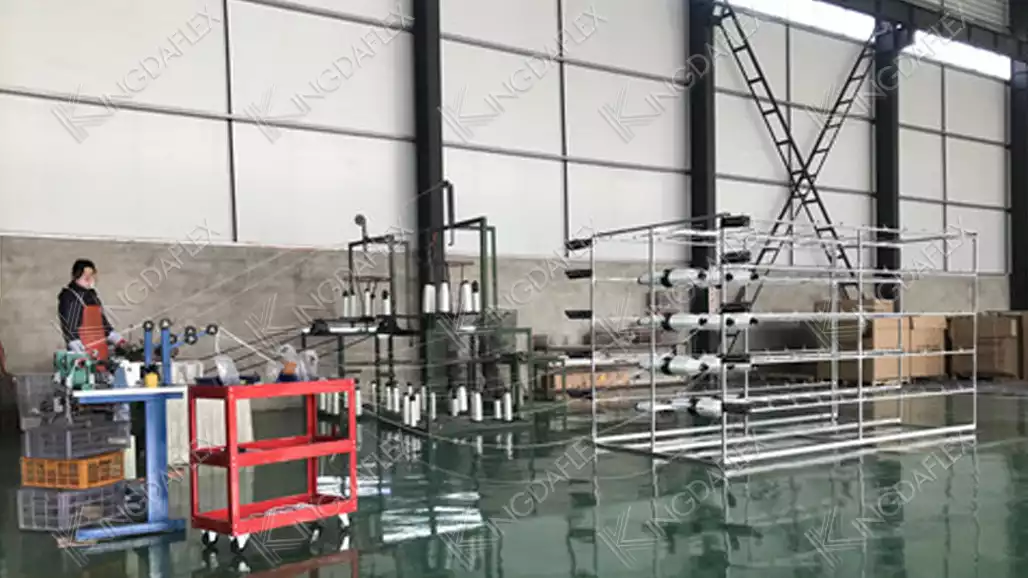
Coiling fiberglass yarn for fire sleeves involves wrapping the yarn around a mandrel or spool to create a uniform, compact roll. This process is used to make fire sleeves that are used to protect hoses, wires, and cables from high temperatures, flame, and fire.
Next, the selected fiber yarn, typically fiberglass or basalt, is meticulously coiled or braided to form the sleeve’s inner core. This process creates a flexible, strong, and heat-resistant substrate onto which the silicone rubber will be applied. Precision coiling ensures uniform density and structural integrity, which are vital for the sleeve’s overall durability and protective capabilities.
Specialized machinery controls the tension and winding pattern of the yarn, creating a consistent tubular structure. This fiber core acts as the primary thermal barrier and provides mechanical strength, preventing the sleeve from collapsing or deforming under heat. The quality of this coiling directly influences the fire sleeve’s ability to withstand extreme temperatures.
Step 3: Fire Sleeve Coating
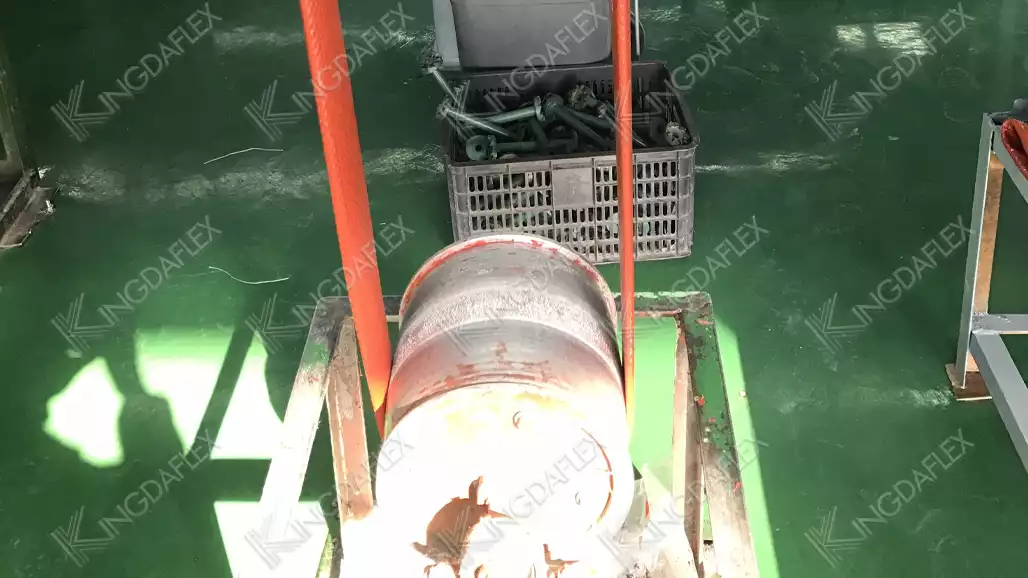
Fire sleeve coating is a protective layer applied to the outside of a fire sleeve to improve its performance and extend its lifespan. The coatings are typically made of materials such as silicone, fiberglass or other high-temperature resistant materials.
The purpose of the fire sleeve coating is to provide additional insulation and protection from high temperatures, flames, and other hazardous conditions. It helps to prevent the spread of fire and reduces the risk of damage to the underlying hoses, wires, and cables.
There are different types of fire sleeve coatings available, each designed to meet specific performance requirements. Some coatings provide additional abrasion resistance, while others have improved resistance to chemicals and fuels.
After coating, the fire sleeve undergoes a shaping process, often involving mandrels or specialized dies, to achieve its precise internal and external diameters. This step ensures the sleeve maintains a consistent cylindrical form, allowing for easy installation over hydraulic hoses and cables. The shaping process is critical for dimensional accuracy and fit.
The shaped sleeve is then typically subjected to a curing process, often in a heated oven. This heat activates the catalysts in the silicone, permanently solidifying the rubber and bonding it firmly to the fiber core. Proper curing ensures the silicone achieves its full mechanical strength, flexibility, and thermal resistance, making the sleeve robust and durable.
Step 4: Fire Sleeve Shaping
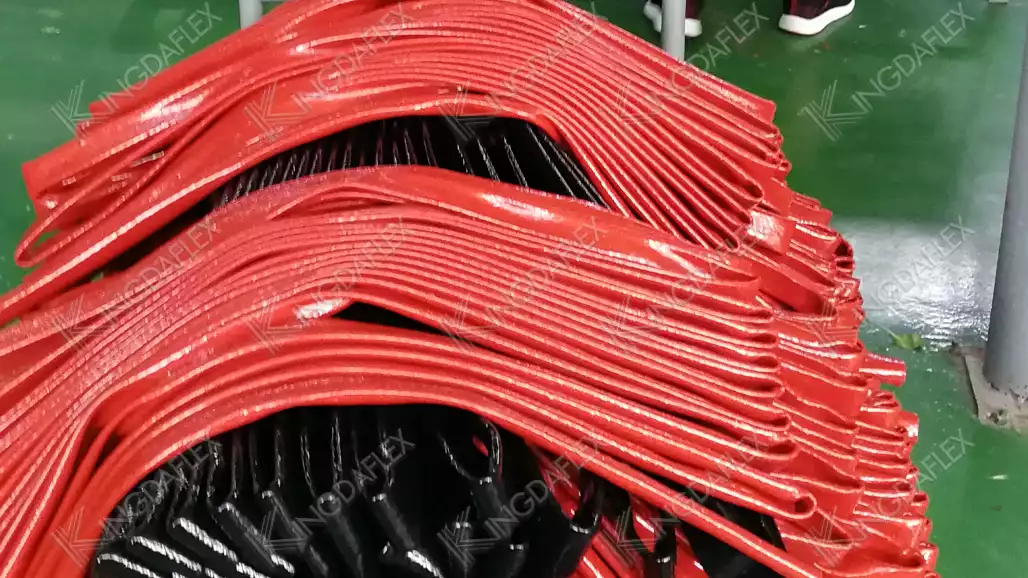
After the process of fire sleeve coating process, the finished fire sleeve tube is manufactured successfully.
Shaping the tube of a fire sleeve involves forming the tube into a specific shape or configuration that is suitable for the intended application. The process of shaping the tube can be done using a variety of techniques, including heat-forming, molding, or mechanical shaping.
The following are some common methods for shaping the tube of a fire sleeve:
- Heat-forming: Heat-forming involves heating the tube to a specific temperature and then applying pressure to form it into the desired shape. This method is typically used for creating shapes that are not possible to achieve with molding or mechanical shaping.
- Molding: Molding involves using a mold to form the tube into the desired shape. This method is often used for producing fire sleeves with complex shapes or for creating multiple identical parts.
- Mechanical shaping: Mechanical shaping involves using mechanical equipment such as a press or a hydraulic machine to shape the tube. This method is typically used for producing simple shapes and for shaping large quantities of tubes.
Regardless of the method used, it is important to consider the type of material used in the fire sleeve, as well as its intended application, to determine the appropriate shaping method. The heat resistance and abrasion resistance of the material can also impact the shaping process, as some materials may become brittle or weaken when exposed to high temperatures or abrasion.
Step 5: Fire Sleeve Inspection
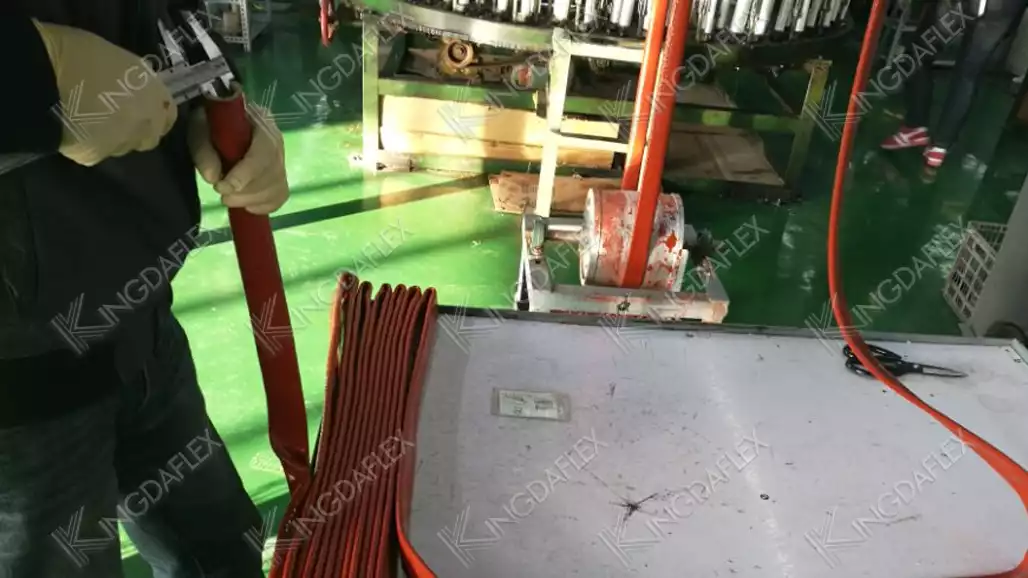
Fire sleeve inspection is a critical process that helps to ensure the continued performance and safety of the fire sleeve. Regular inspections can identify potential problems or damage that could compromise the ability of the fire sleeve to protect hoses, wires, and cables from high temperatures, flames, and fire.
The following are some common steps for conducting a fire sleeve inspection:
- Visual inspection: Begin by visually inspecting the fire sleeve for any signs of damage, such as cuts, tears, or abrasions. Look for any signs of discoloration or charring, which could indicate exposure to high temperatures.
- Measurement: Check the dimensions of the fire sleeve to ensure that it is the correct size for the intended application. This includes measuring the length, diameter, and wall thickness of the tube.
- Functionality: Check the functionality of the fire sleeve by verifying that it fits properly over the hoses, wires, or cables that it is intended to protect. Make sure that the end fittings or covers are secure and that the fire sleeve is not binding or kinking.
- Testing: Perform a test to verify that the fire sleeve meets the performance requirements for its intended application. This may include exposure to high temperatures, flame, or abrasion.
- Documentation: Document the results of the inspection, including any damage or issues that were identified. This information can be used to track the performance of the fire sleeve over time and to plan for any necessary repairs or replacements.
It is important to follow proper safety procedures when conducting a fire sleeve inspection, such as wearing protective gloves and clothing and working in a well-ventilated area. Additionally, it is essential to follow the manufacturer’s guidelines and specifications for the specific fire sleeve to ensure that the inspection and testing methods are appropriate for the material and intended application.
Step 6: Fire Sleeve Rolling
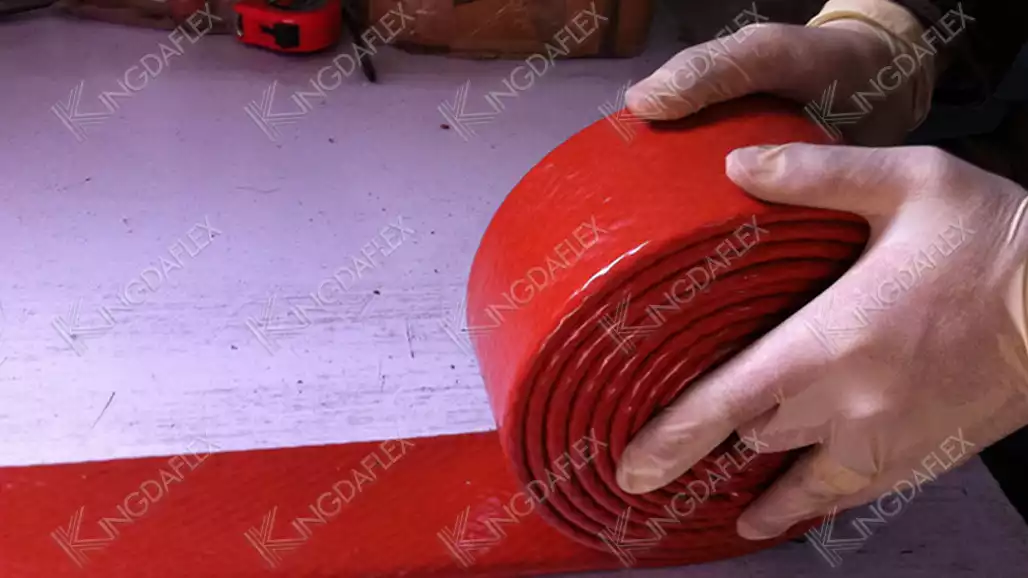
Hydraulic hose rolling is a process used to bend or shape hydraulic hoses into specific configurations. This is typically done to make the hoses more easily routable or to match the routing requirements of the intended application.
Once inspected and approved, the finished fire sleeves are carefully rolled into manageable lengths, typically on spools or into coils. This process facilitates efficient handling, storage, and transportation of the product. Automated rolling machines ensure consistent tension and uniform winding, preventing kinks or damage to the sleeve material.
The rolled sleeves are then prepared for packaging. Proper rolling minimizes the footprint for storage and shipping, making the logistics more efficient. This step also protects the integrity of the sleeve during transit, ensuring it arrives at its destination in optimal condition, ready for immediate use in various protective applications.
Step 7: Fire Sleeve Packing
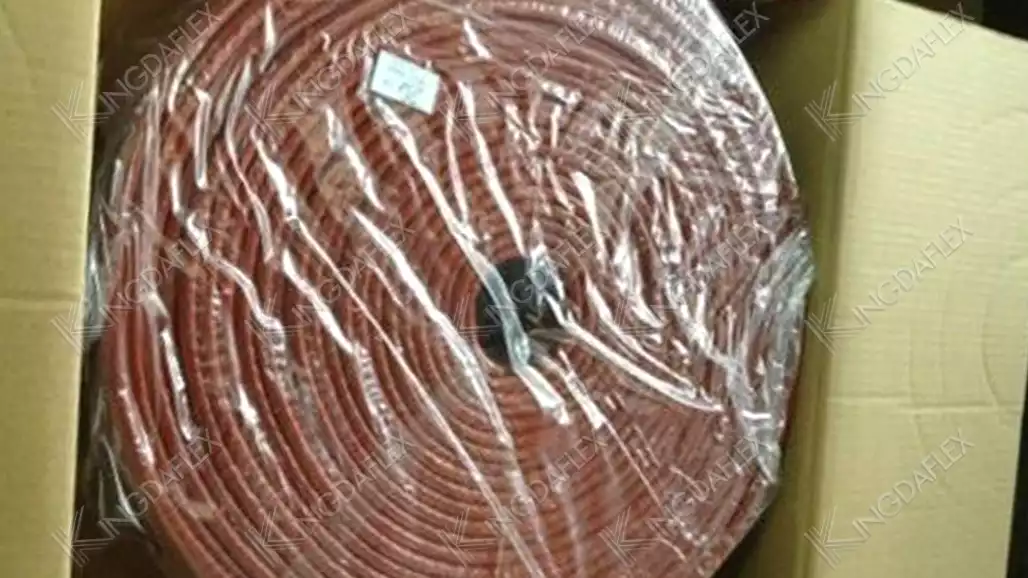
We offer fire sleeves that are designed to protect your hoses and wires from extreme temperatures and heat. And the best part is that we can customize the packaging with your own private label.
Your brand name will be prominently displayed on the packaging, making it easier for your customers to identify and remember your product. Plus, having a private label on the packaging adds a professional touch and sets your product apart from the competition.
Don’t settle for generic, off-the-shelf fire-sleeve packaging. Choose a solution that is tailored to your specific needs and reflects your brand. Contact us today to learn more about our private label customization options!
Hydraulic hose packing is the process of wrapping or covering a hydraulic hose to protect it from damage and extend its service life. This can be accomplished using a variety of materials, including protective sleeves, heat-shrink tubing, and spiral wrap.
The following are some common steps involved in hydraulic hose packing:
- Preparing the hydraulic hose: Clean the hose thoroughly and check for any signs of damage, such as cuts, abrasions, or kinks. Make sure that the hose is free of any contaminants, as these can affect the performance and integrity of the hose.
- Measuring the hose: Measure the length and diameter of the hose to determine the amount of protective material that is required.
- Selecting the protective material: Choose the appropriate protective material based on the intended application and the requirements for the hose. This may include considering factors such as abrasion resistance, heat resistance, and flexibility.
- Applying the protective material: Apply the protective material to the hose, following the manufacturer’s instructions for the specific material. This may involve sliding the protective material over the hose, wrapping it around the hose, or heat-shrinking the material onto the hose.
- Inspecting the hose: Inspect the hose after the protective material has been applied to make sure that it has been applied correctly and that the hose is fully covered.
It is important to follow the manufacturer’s guidelines for the specific protective material and hose to ensure that the packing process is appropriate for the material and intended application.
Additionally, it is essential to wear protective gloves and clothing and to follow proper safety procedures when conducting hydraulic hose packing to avoid injury.
Step 8: Fire Sleeve Pallet
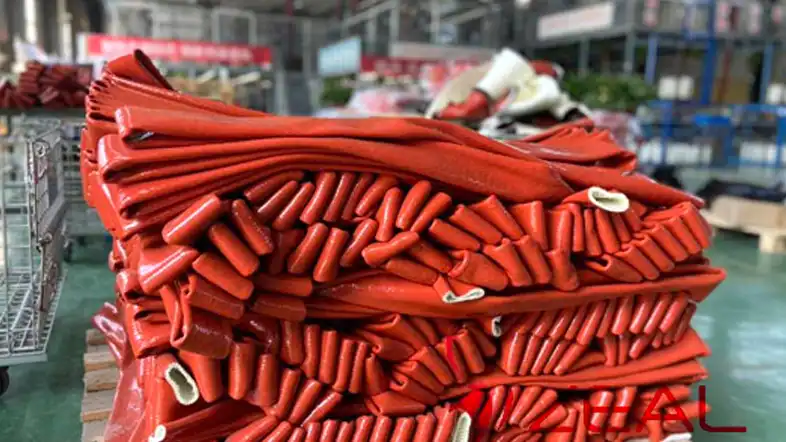
The fire sleeve is typically packaged and shipped on a pallet to ensure that it is protected during transit and that it arrives in good condition. The following are some common steps involved in packaging a fire sleeve on a pallet:
- Preparing the fire sleeve: Inspect the fire sleeve to make sure that it is in good condition and free of any damage or defects.
- Measuring the fire sleeve: Measure the length, diameter, and wall thickness of the fire sleeve to determine the size and weight of the package.
- Preparing the pallet: Choose a pallet that is appropriate for the size and weight of the fire sleeve package. Make sure that the pallet is clean, dry, and free of any contaminants that could affect the fire sleeve.
- Loading the fire sleeve: Load the fire sleeve onto the pallet, making sure that it is positioned securely and that it will not shift or become damaged during transit.
- Wrapping the fire sleeve: Wrap the fire sleeve in protective material, such as stretch wrap or a protective cover, to secure it in place and to protect it from damage.
- Securing the pallet: Secure the pallet by applying shrink wrap, banding, or other restraints to make sure that the fire sleeve package will not shift during transit.
- Labeling the pallet: Label the pallet with the appropriate information, such as the contents, destination, and shipping information.
It is important to follow the manufacturer’s guidelines for packaging and shipping the fire sleeve to ensure that it is protected during transit and that it arrives in good condition. Additionally, it is essential to follow proper safety procedures when handling and packaging the fire sleeve to avoid injury.
Step 9: Fire Sleeve Container
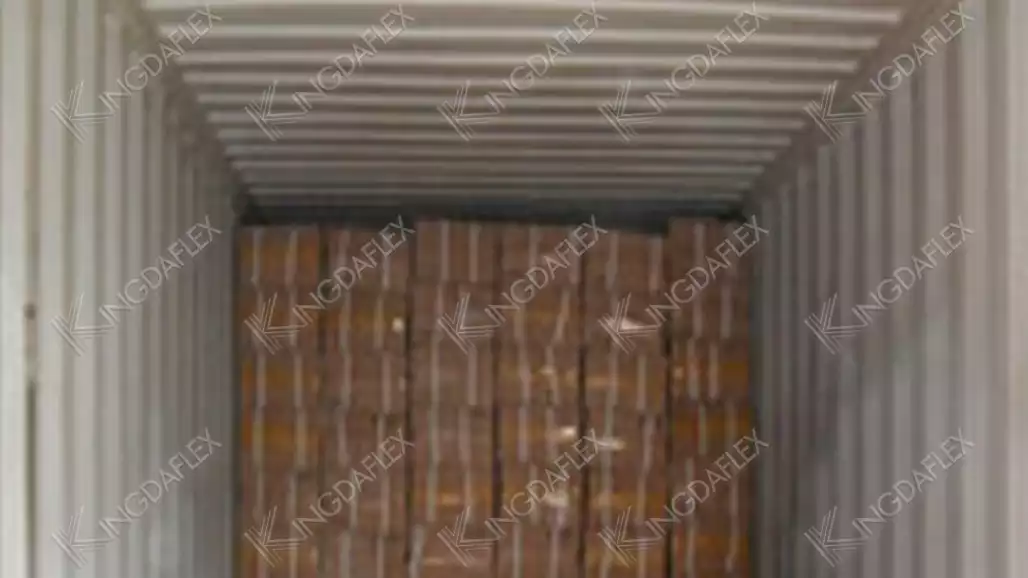
The fire sleeve container is a protective container that is used to store and transport fire sleeves. The container is designed to protect the fire sleeves from damage and to keep them organized and accessible.
The specific design and features of a fire sleeve container will depend on the intended use and requirements for the fire sleeves. It is important to choose a container that is appropriate for the fire sleeves and to follow the manufacturer’s guidelines for storage and transport to ensure that the fire sleeves are protected and remain in good condition.
Fire Sleeve Cargo
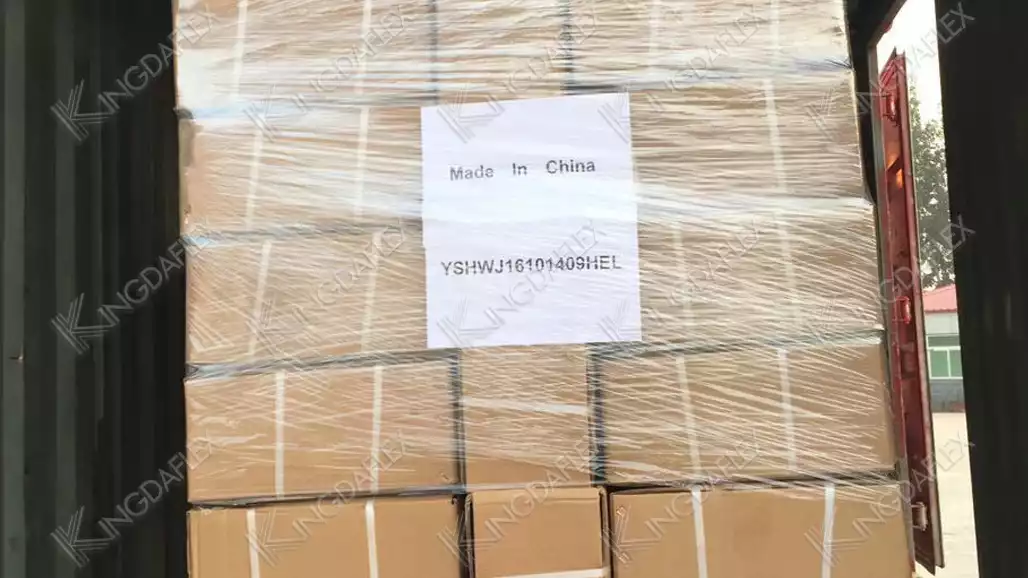
Fire sleeve cargo refers to the shipment or transport of fire sleeves, which are used to protect hydraulic hoses, electrical cables, and other components from high temperatures and heat.
The following are some common steps involved in shipping fire sleeve cargo:
- Preparing the fire sleeves: Inspect the fire sleeves to make sure that they are in good condition and free of any damage or defects.
- Packaging the fire sleeves: Package the fire sleeves in protective material, such as stretch wrap or a protective cover, to secure them in place and to protect them from damage during transit.
- Loading the fire sleeves: Load the packaged fire sleeves into the appropriate shipping container, making sure that they are positioned securely and that they will not shift or become damaged during transit.
- Securing the shipment: Secure the shipment by applying shrink wrap, banding, or other restraints to make sure that the fire sleeves will not shift during transit.
- Labeling the shipment: Label the shipment with the appropriate information, such as the contents, destination, and shipping information.
It is important to follow the manufacturer’s guidelines for shipping fire sleeves to ensure that they are protected during transit and that they arrive in good condition. Additionally, it is essential to follow proper safety procedures when handling and shipping fire sleeves to avoid injury. It is also important to comply with any applicable regulations and standards for shipping hazardous materials.
Conclusion
The journey from raw materials to a finished fire sleeve is a testament to precision manufacturing and material science. Each step, from specialized braiding to meticulous silicone coating and curing, contributes to creating a product capable of withstanding extreme conditions, ultimately safeguarding critical systems and personnel.
Understanding this intricate process highlights why quality control is paramount. A well-manufactured fire sleeve is not just a product; it’s a vital safety component, engineered to offer reliable protection against heat, flame, and abrasion in the most demanding industrial, automotive, and aerospace applications.
For those seeking robust and dependable fire protection, remember that the manufacturing quality directly impacts performance. You can confidently get wholesale fire sleeves from Kingdaflex, knowing they are produced with the expertise and rigorous standards necessary to deliver exceptional safety and longevity.