Hydraulic hoses are indispensable in countless industries, from construction and agriculture to manufacturing and mining. Their ability to withstand high pressures, harsh environments, and the relentless demands of hydraulic systems depends heavily on the rubber compound used in their construction.
In this blog post, we’ll delve into the critical role of rubber compounding in hydraulic hose manufacturing.
We’ll explore:
- The importance of rubber compounding: How the composition of the rubber compound directly impacts hose performance.
- Key components of rubber compounds: Understanding the various ingredients that contribute to hose properties.
- The impact of rubber compounding on hydraulic hose performance: How different rubber compounds affect factors like pressure resistance, temperature tolerance, and chemical compatibility.
- Custom rubber compounding for specific applications: The ability to tailor rubber compounds to meet unique requirements.
By understanding the intricacies of rubber compounding, we can gain a deeper appreciation for the science and engineering behind hydraulic hose manufacturing.
So, let’s dive in and discover how rubber compounding is the backbone of hydraulic hose performance.
What Is Rubber Compounding
Rubber compounding is the process of mixing various ingredients with raw rubber to create a material with specific properties. These ingredients can include:
- Fillers: Substances like carbon black, silica, and clay that improve properties like strength, abrasion resistance, and cost.
- Reinforcements: Materials like steel wire, textile braid, or synthetic fibers that provide additional strength and durability.
- Vulcanizing agents: Chemicals like sulfur or peroxides that create cross-links between rubber molecules, giving it elasticity and strength.
- Plasticizers: Substances that improve the flexibility and processability of the rubber.
- Antioxidants: Chemicals that prevent the rubber from degrading due to oxidation.
- Colorants: Pigments or dyes that give the rubber a desired color.
The precise combination and amounts of these ingredients determine the final properties of the rubber compound, such as:
- Tensile strength: The ability to withstand stretching without breaking.
- Abrasion resistance: The ability to resist wear and tear.
- Compression set: The ability to maintain its shape after being compressed.
- Temperature resistance: The ability to withstand high or low temperatures.
- Chemical resistance: The ability to resist the effects of various chemicals.
- Flexibility: The ability to bend or twist without breaking.
By carefully selecting and blending these ingredients, manufacturers can create rubber compounds that are tailored to specific applications, such as hydraulic hoses, tires, gaskets, and other rubber products.
Why Rubber Compounding Is Important for Hydraulic Hose
Rubber compounding is a critical aspect of hydraulic hose manufacturing because it directly influences the hose’s performance and durability. The specific composition of the rubber compound determines the hose’s:
- Pressure resistance: The ability to withstand high pressures without bursting.
- Temperature tolerance: The ability to function in both hot and cold environments.
- Chemical resistance: The ability to resist the corrosive effects of hydraulic fluids and other chemicals.
- Abrasion resistance: The ability to withstand wear and tear from contact with other surfaces.
- Flexibility: The ability to bend and twist without cracking or breaking.
By carefully selecting and blending the right ingredients in the rubber compound, manufacturers can create hydraulic hoses that:
- Meet specific industry standards: Ensure compliance with safety regulations and performance requirements.
- Withstand demanding applications: Perform reliably in harsh environments and under heavy loads.
- Provide long-lasting service: Minimize maintenance and replacement costs.
In essence, rubber compounding is the foundation upon which the performance and reliability of hydraulic hoses depend. By understanding the importance of rubber compounding, manufacturers can produce hoses that are not only durable but also contribute to the overall efficiency and safety of hydraulic systems.
Rubber Compounding Process
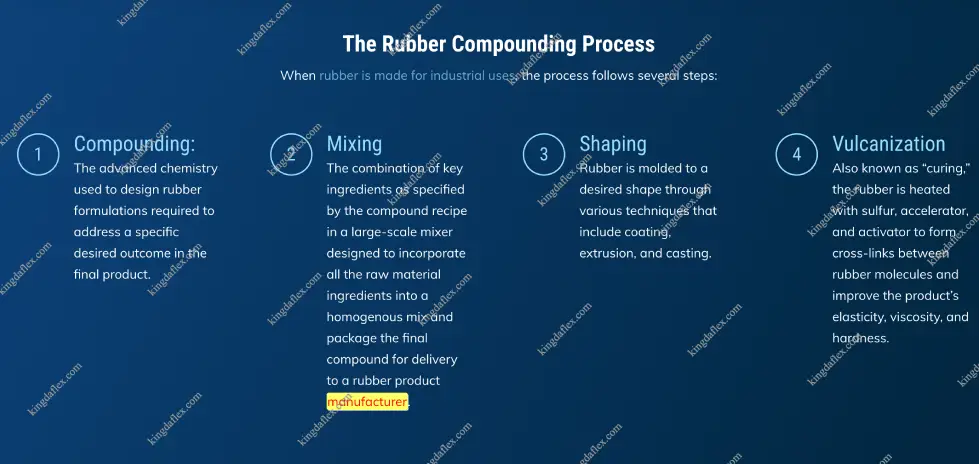
Rubber compounding is a complex process that involves mixing various ingredients with raw rubber to create a material with specific properties. Here’s a breakdown of the key steps involved:
1. Raw Rubber Selection:
- Natural Rubber: Derived from the latex of rubber trees, natural rubber offers excellent elasticity and resilience.
- Synthetic Rubber: Various types of synthetic rubber, such as nitrile, neoprene, and butyl, are available with different properties tailored to specific applications.
2. Ingredient Preparation:
- Fillers: Materials like carbon black, silica, and clay are prepared and weighed.
- Reinforcements: Steel wire, textile braid, or synthetic fibers are prepared.
- Vulcanizing Agents: Sulfur or peroxides are measured and added.
- Plasticizers, Antioxidants, and Colorants: These additives are prepared according to the desired properties.
3. Mixing:
- Banbury Mixer: A high-intensity mixer that combines the raw rubber and ingredients under intense heat and pressure.
- Internal Mixer: Another type of mixer that uses a rotating screw to mix the components.
4. Refining:
- Two-Roll Mill: A machine with two rotating rollers that refines the mixture, ensuring even distribution of ingredients and removing air pockets.
5. Extrusion:
- Extruder: The refined rubber compound is forced through a die to create a continuous length of rubber. This step is often used for producing rubber sheets or profiles.
6. Curing:
- Curing Chamber: The extruded rubber is placed in a curing chamber, where it is subjected to heat and pressure. This process causes the rubber to vulcanize, forming strong chemical bonds and giving it its final properties.
7. Finishing:
- Trimming, Cutting, or Molding: The cured rubber may be trimmed, cut, or molded into specific shapes or sizes.
8. Testing and Inspection:
- Quality Control: The finished rubber products are tested to ensure they meet specific standards for properties like tensile strength, abrasion resistance, and chemical resistance.
The rubber compounding process is highly customizable, allowing manufacturers to create rubber compounds with a wide range of properties tailored to specific applications. By carefully selecting and blending the right ingredients, manufacturers can produce rubber products that are durable, reliable, and suitable for various industries.
Conclusion
Rubber compounding is a critical aspect of hydraulic hose manufacturing, directly influencing the hose’s performance, durability, and suitability for various applications. By understanding the key steps involved in rubber compounding and the importance of ingredient selection, manufacturers can produce hydraulic hoses that meet the demanding requirements of modern industries.
Are you seeking high-quality hydraulic hoses that are tailored to your specific needs? Look no further than Kingdaflex. As a leading manufacturer of hydraulic hoses, Kingdaflex offers a wide range of products with exceptional performance and durability.
Contact us today to discuss your requirements and explore our extensive product line. Our team of experts can help you select the ideal hydraulic hoses for your application, ensuring optimal efficiency and reliability.
Visit our website or reach out to our sales team to learn more about Kingdaflex and our hydraulic hose solutions.