When it comes to welding hose, having the right equipment is crucial for ensuring safety and efficiency. One such equipment that plays a significant role in welding operations is the welding hose. However, many individuals often overlook the importance of using the correct type of welding hose.
In this article, we will explore the different types of welding hoses available in the market and the key differences between them.
Understanding Welding Hoses
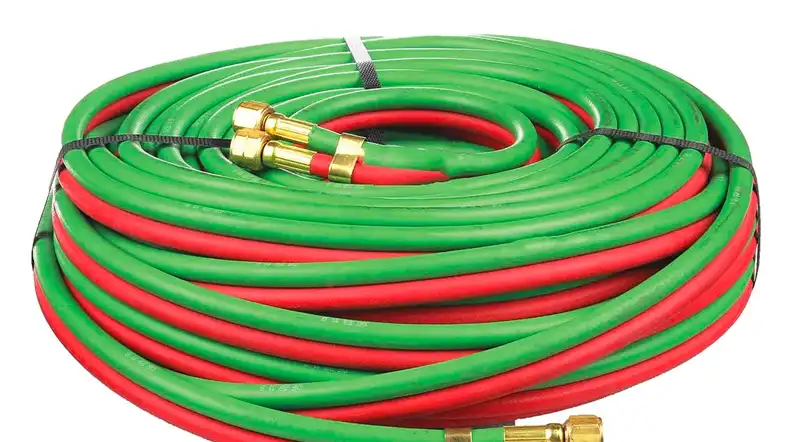
Before delving into the differences, it is essential to understand what welding hoses are and their role in welding operations. Welding hoses are flexible tubes that connect the welding torch to the gas supply and welding machine. They are responsible for transporting the fuel gases, such as acetylene or propane, and the oxygen required for the welding process.
Types of Welding Hoses
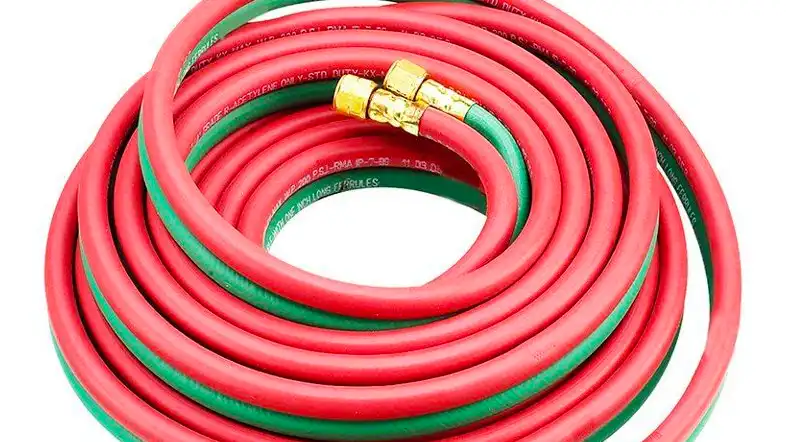
There are primarily two types of welding hoses commonly used in welding applications: rubber hoses and twin hoses.
Rubber Hoses
Rubber welding hoses are single hoses that are designed to transport a single type of gas, either acetylene or propane. They are known for their flexibility, ease of use, and durability. Rubber hoses are suitable for light to medium-duty welding tasks and are a cost-effective option for many welders.
Twin Hoses
Twin welding hoses, as the name suggests, come as a pair of hoses joined together. One hose transports the fuel gas, while the other carries oxygen. They are often color-coded, with the fuel gas hose being red and the oxygen hose being green. Twin hoses are preferred for heavy-duty welding applications as they offer increased safety and efficiency by keeping the gases separate.
Key Differences
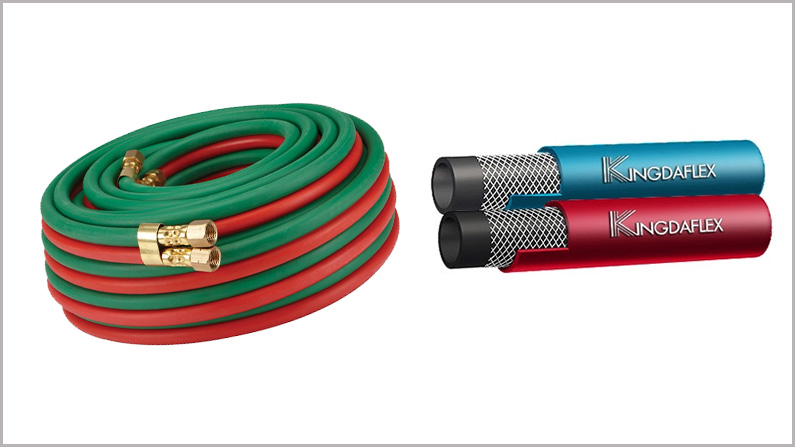
Now that we have an understanding of the two main types of welding hoses, let’s explore their key differences.
Gas Separation
The most significant difference between rubber hoses and twin hoses lies in how they handle gas separation. Rubber hoses transport only one type of gas, making them more suitable for basic welding tasks where only one gas is needed. On the other hand, twin hoses keep the gases separated, ensuring there is no risk of accidental mixing, which is vital for critical welding applications.
Safety
Safety is paramount in welding operations, and the type of hose used can significantly impact it. Rubber hoses, being single hoses, are more prone to kinking and tangling. This can create hazards and potentially lead to accidents. Twin hoses, with their durable construction and gas separation feature, offer better safety and are less likely to tangle or kink.
Versatility
For welders who perform various types of welding tasks, the versatility of equipment is essential. Rubber hoses are limited to carrying a single gas, which may require switching hoses for different applications. Twin hoses, with their ability to transport both fuel gas and oxygen simultaneously, provide more versatility and convenience to the welder.
Burst Resistance
Burst resistance is another critical factor to consider. In this aspect, twin hoses have the advantage due to their sturdy construction and gas separation design. Rubber hoses, while durable, may be more susceptible to bursting when subjected to extreme conditions or mishandling.
Conclusion
Choosing the right welding hose is crucial for the safety and efficiency of welding operations. While rubber hoses offer flexibility and affordability, twin hoses provide added safety, gas separation, and versatility. For heavy-duty welding applications or when working with critical materials, twin hoses are the recommended choice. However, for general welding tasks, rubber hoses can be a cost-effective option.
Remember, always prioritize safety and select the welding hose that best suits your specific needs and requirements. Using the appropriate welding hose will not only enhance your welding performance but also ensure a safer working environment.
Frequently Asked Questions (FAQs)
Can I use a rubber welding hose for all types of welding?
Rubber hoses are suitable for light to medium-duty welding tasks but may not be ideal for heavy-duty applications.
Are twin hoses more expensive than rubber hoses?
Yes, twin hoses are generally more expensive due to their design and gas separation feature.
Can I mix up the gas hoses when using twin hoses?
No, twin hoses are color-coded for easy identification, and it is essential not to mix them up to avoid hazards.
How often should I inspect and replace welding hoses?
Regularly inspect your hoses for signs of wear and damage and replace them if any issues are detected. Follow the manufacturer’s recommendations for replacement intervals.
Can I repair a damaged welding hose on my own?
It is recommended to have damaged welding hoses repaired or replaced by a qualified professional to ensure safety and proper functionality.
When looking to understand the difference between welding hoses, one of the most important things to consider is hose size. Generally, there are three common sizes of hoses – “A”, “B” and “C”. Each hose connection has a matching connecting nut, hose stem and ferrule.
Oxy-fuel applications require left hand nut threads for fuel and right hand threads for oxygen. There is also a “B” size for inert gases; however, the left hand thread configuration of both “B” and “C” sizes are not very common. Whether the standard coupling nut has external or internal threads determines intended gas use. Generally, internal threads are for oxy-fuel applications and external threads are for inert gases, water or industrial air.
Hose Fittings – Sizes and Types:
When selecting the connection size, the primary consideration should be the gas volume required and if it is a light, standard or heavy-duty application:
- Light Duty: Size “A” are typically used for light gas volume work such as HVAC, arts and crafts, etc.
- Standard Duty: “B” size fittings are by far the most common in our industry and probably comprise 95% or more of the market. They are primarily used for oxy-fuel applications that require standard or medium gas volumes. There are also “B” (“Inert”) size fittings used for many inert gas applications including MIG and TIG welding.
- Heavy Duty: Size “C” is for heavy-duty applications such as heavy duty cutting (≥ 30”) and scarfing. These larger size hose connections are required to ensure the high volumes needed for these types of applications. Harris manufactures gas supply equipment, regulators and manifolds, as well as torches that require “C”size connections because they are necessary on certain equipment for high gas volume applications, but limited to a 200 PSIG maximum working pressure.
Relate:
Any questions or interested, please contact us.
Whatsapp: 008618562767380
Email: [email protected]
Skype: kingdaflex