Hydraulic systems are the workhorses of many industries, powering everything from construction equipment to farm machinery. But when those essential hydraulic hoses refuse to connect, it can bring your entire operation to a screeching halt.
If you’ve ever wrestled with stubborn hoses, you’re not alone. This guide will delve into the reasons why hydraulic hoses might not connect and provide solutions to get you back up and running smoothly.
Residual Hydraulic Pressure
The most common reason for connection woes is residual hydraulic pressure trapped within the system. This pressure acts like an invisible hand pushing back against the hose fitting, preventing a secure connection.
Here’s how it happens:
- Improper Disconnection: When an attachment is disconnected from the hydraulic system while the engine is running or the control valve is still engaged, pressure can become trapped in the lines.
- Thermal Expansion: Even when the system is off, parked equipment exposed to direct sunlight can cause the hydraulic oil to expand, creating pressure within the hoses.
Signs of Residual Pressure
Before diving into solutions, here are some tell-tale signs that residual pressure might be the culprit:
- Stiff or Difficult to Push: The male coupler (the plug-like end) feels unusually stiff when attempting to insert it into the female coupler (the socket-like end).
- Hissing or Sputtering: While connecting, you might hear a hissing sound or experience a small spurt of hydraulic fluid as pressure releases.
Why Won’t My Hydraulic Hoses Connect
There’s a good chance your woes stem from residual hydraulic pressure trapped in the system. This pressure acts like an invisible force pushing back on the hose fitting, making a secure connection difficult. Here’s a breakdown:
- The Culprit: Residual pressure can be left behind from:
- Disconnecting attachments while the engine is running or the control valve is engaged.
- Thermal expansion of hydraulic oil due to parked equipment being in direct sunlight.
- Signs of the Problem:
- The male coupler feels stiff and hard to push in.
- You hear a hissing sound or experience a small spurt of fluid when connecting.
- Relieving the Pressure Safely:
- Turn off the engine and cycle the hydraulic control levers for the attachment.
- Use Caution: With a rag to capture escaping fluid, loosen the fitting on the attachment side slightly to release trapped pressure (wear eye protection and gloves!).
Relieving the Pressure
Before resorting to forceful measures, it’s crucial to relieve the pressure safely and effectively. Here are two common methods:
- Engine Off and Control Lever Manipulation: Turn off the engine and cycle the hydraulic control levers for the attachment several times. This allows trapped fluid to return to the reservoir, relieving pressure in the lines.
- Controlled Release with a Wrench (Use Caution): Identify a safe location to point the disconnected hose away from yourself and others. With a rag to capture any escaping fluid, loosen the fitting on the attachment side slightly. This allows a small amount of oil to escape, releasing the trapped pressure. Important Note: Always wear eye protection and gloves when working with hydraulic systems.
Other Reasons for Connection Issues
While residual pressure is the most common culprit, here are some other factors that might hinder a smooth connection:
- Incorrect Hose Selection: Double-check that you’re using the correct hose for the specific application. Hoses are designed for different pressure ratings and types of hydraulic fluid. Using an incompatible hose could lead to connection issues and potential safety hazards.
- Damaged Couplings: Inspect the couplers for any nicks, dents, or excessive wear. Damaged threads or a bent sleeve on the male coupler can prevent a secure connection.
- Dirt or Debris: Foreign objects lodged within the coupler can hinder a proper seal. Ensure both the male and female couplers are clean and free of debris before attempting connection.
Maintaining a Smooth Connection: Preventive Measures
An ounce of prevention is worth a pound of cure, so here are some tips to keep your hydraulic connections smooth:
- Develop a Disconnection Routine: Always turn off the engine and cycle the control levers before disconnecting hoses. This helps to eliminate residual pressure from the get-go.
- Inspect Regularly: Make it a habit to visually inspect hoses and couplers for damage or wear during routine maintenance checks. Replace any worn or damaged components promptly.
- Keep it Clean: Wipe down couplers with a clean rag before connection to remove any dirt or debris that could hinder a proper seal.
How to Disconnect Hydraulic Hose From John Deere Tractor
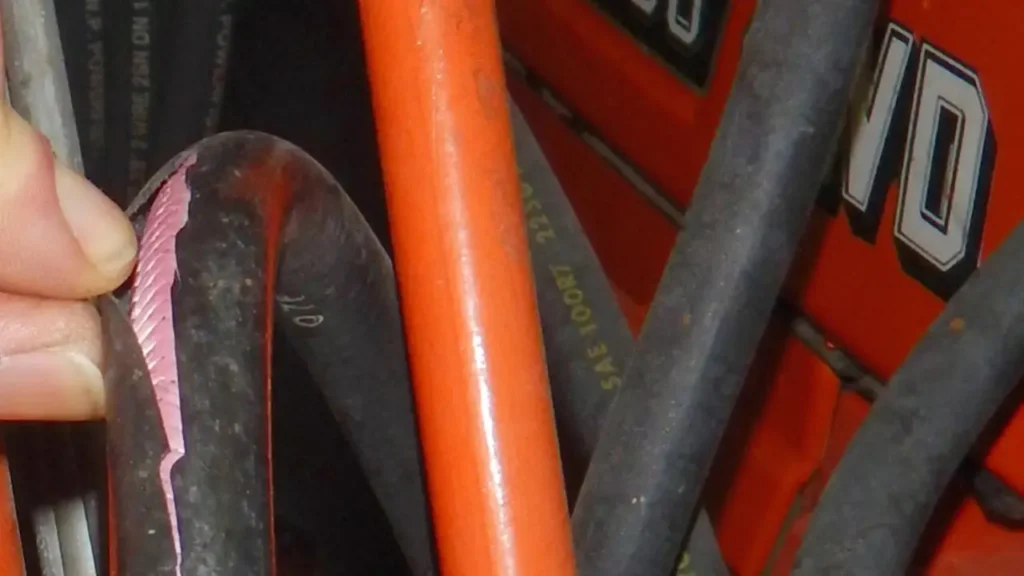
Here’s a step-by-step guide on how to safely disconnect a hydraulic hose from a John Deere tractor:
Safety First:
- Wear Protective Gear: Always wear safety glasses, gloves, and long sleeves to protect yourself from potential oil splashes and injuries.
- Release Pressure: Before disconnecting any hose, ensure all hydraulic pressure is released. This can be done by:
- Turning off the tractor engine.
- Operating the hydraulic levers to their neutral positions.
- Lowering any hydraulically operated implements to the ground.
Disconnection Steps:
- Locate the Coupling: Identify the quick-connect coupling you want to disconnect. It will typically have a sleeve or collar that needs to be pushed back to release the hose.
- Push the Sleeve Back: Using your gloved hand, firmly push the sleeve back on the coupling. This will disengage the locking mechanism.
- Pull the Hose: Once the sleeve is pushed back, gently pull the hose straight out of the coupling. Avoid jerking the hose, as this could damage it or cause oil to spray.
- Clean Up: If any oil spills during the disconnection process, clean it up immediately using appropriate cleaning agents.
Additional Tips:
- Difficulty Disconnecting: If you encounter resistance while disconnecting, double-check that all pressure is released. If the issue persists, consult your John Deere manual or a qualified mechanic.
- Hose Replacement: If you’re replacing a hose, ensure you get the correct size and type of hose. It’s also advisable to replace the fittings at the same time to prevent future leaks.
- Professional Help: If you’re unsure about any step or encounter difficulties, seek assistance from a qualified mechanic or your local John Deere dealer.
Visual Aid:
For a visual demonstration, you can refer to this helpful video:
Remember: Safety should always be your top priority when working with hydraulic systems. By following these steps and taking necessary precautions, you can safely disconnect hydraulic hoses on your John Deere tractor.
Conclusion
By understanding the reasons behind stubborn hydraulic hose connections and following these simple solutions, you can keep your equipment running smoothly and avoid unnecessary downtime. Remember, safety is paramount when working with hydraulic systems.
Always wear appropriate personal protective equipment and consult your equipment manual or a qualified technician if you have any doubts. With a little knowledge and preventative measures, you can ensure a frustration-free future for your hydraulic connections.
Bonus Tip: If you’re still encountering difficulties after trying these solutions, consider consulting your equipment manual for specific instructions or contacting a qualified hydraulic service technician for further assistance.