Hydraulic hoses are crucial components in hydraulic systems, responsible for transmitting fluid and power. To ensure optimal performance, longevity, and prevent costly downtime, it’s essential to prioritize regular hydraulic hose maintenance.
In this blog post, we will discuss key tips and best practices for hydraulic hose maintenance, empowering you to keep your hydraulic systems operating smoothly and efficiently.
How Often Should You Inspect A Hydraulic Hose?
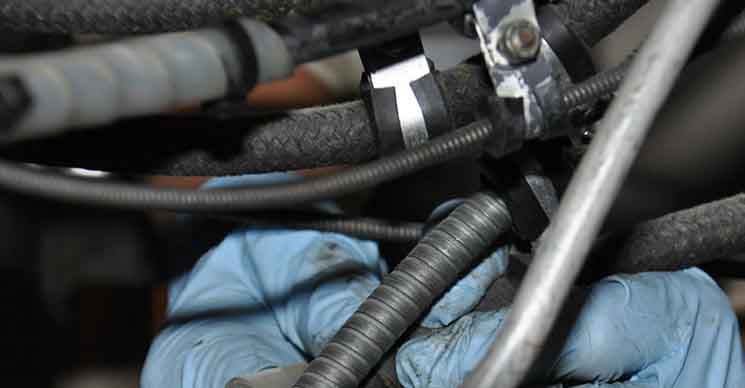
The frequency of hydraulic hose inspections depends on various factors such as the application, operating conditions, and manufacturer’s recommendations. However, as a general guideline, it is recommended to inspect hydraulic hoses at least every three to six months.
In more demanding environments or high-stress applications, more frequent inspections may be necessary. Additionally, any time the hydraulic system undergoes significant changes or modifications, it is crucial to conduct a thorough inspection to ensure the integrity of the hoses.
Remember, early detection of any signs of wear, damage, or leaks during inspections can help prevent costly failures and downtime. Regular visual inspections, along with periodic maintenance, will help maintain the performance and longevity of hydraulic hoses.
What Happens in a Hydraulic Hose Inspection?
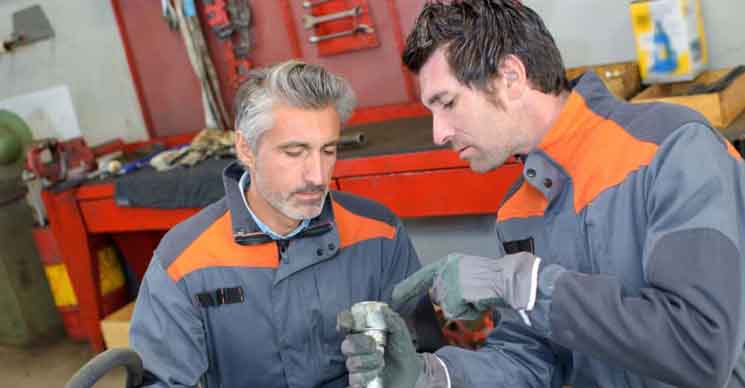
During a hydraulic hose inspection, several key steps are typically followed to assess the condition and integrity of the hoses. Here’s what generally happens in a hydraulic hose inspection:
- Visual Examination: The inspector visually inspects each hydraulic hose thoroughly. They look for signs of wear, such as cracks, abrasions, bulges, or cuts on the hose’s outer surface. They also check for any leaks or signs of fluid seepage around the hose connections.
- Fitting Inspection: The hydraulic hose fittings and connections are closely examined for tightness and signs of damage. The inspector checks if the fittings are securely attached to the hose without any visible leaks or gaps.
- Bend Radius Evaluation: The inspector ensures that the hydraulic hoses are not subjected to excessive bending or twisting, as this can lead to kinking or premature failure. They check if the hoses are properly routed and have sufficient clearance to avoid strain.
- Hose Identification and Labeling: The inspector verifies if the hoses are correctly labeled with important information such as the manufacturer, part number, and pressure rating. Proper labeling ensures easy identification and assists in replacement or troubleshooting.
- Fluid Compatibility Assessment: The compatibility between the hydraulic fluid and the hose material is reviewed. The inspector ensures that the fluid being used is suitable for the specific hose construction. Incompatible fluids can cause hose degradation or failure.
- Operating Pressure Verification: The inspector checks if the operating pressure of the hydraulic system aligns with the recommended pressure range for the hoses. Excessive pressure can put undue stress on the hoses, leading to potential damage or failure.
- Documentation and Hydraulic Hose Maintenance Schedule: The findings of the inspection are documented, including any identified issues, required repairs, or recommended replacements. A maintenance schedule is established based on the inspection results and industry guidelines.
It’s important to note that the specific steps and procedures for a hydraulic hose inspection may vary based on the industry, equipment, and regulatory requirements.
Following manufacturer guidelines and seeking professional assistance can ensure a thorough and accurate inspection of hydraulic hoses.
Proper Hydraulic Hose Installation
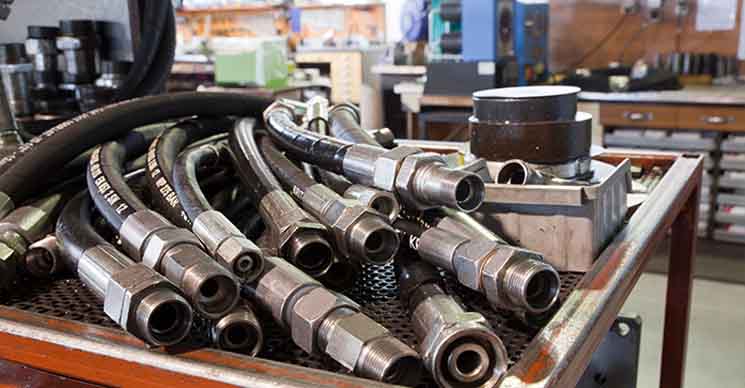
Correct hydraulic hose installation is vital for their performance and durability. Ensure that hoses are properly routed, avoiding sharp bends or twists that could cause strain or kinking. Use proper fittings, clamps, and brackets to secure hoses in place, preventing excessive vibration and potential damage.
Proper installation of hydraulic hoses is essential for the safe and efficient operation of hydraulic systems. Incorrect installation can lead to leaks, premature wear, and even system failure. In this article, we will discuss the key factors and best practices to ensure the proper installation of hydraulic hoses, maximizing their performance and longevity.
- Selecting the Right Hose: Choose a hydraulic hose that is suitable for the specific application and meets the system’s requirements in terms of pressure rating, temperature range, and compatibility with the hydraulic fluid. Consult the manufacturer’s specifications and guidelines to ensure the correct hose is selected.
- Correct Hose Routing: Proper hydraulic hose routing is crucial to avoid excessive bending, twisting, or abrasion that can lead to hose failure. Ensure that hoses are routed in a way that minimizes stress, maintains adequate clearance, and prevents interference with moving parts or other components.
- Hose Length and Allowance: When installing hydraulic hoses, ensure they have the appropriate length to accommodate system movement and flexing without being stretched or compressed. Allow for sufficient slack or expansion to prevent undue stress on the hose during operation.
- Clean Connections and Fittings: Before installation, thoroughly clean the hose connections and fittings to remove any dirt, debris, or contaminants. This helps ensure a proper seal and prevents the introduction of foreign particles into the hydraulic system.
- Correct Assembly: Follow the manufacturer’s instructions for assembling the hose and fittings. Use proper tools and techniques to crimp or attach fittings securely to the hose ends. Avoid overtightening, as it can damage the hose or fittings.
- Use Proper Sealing and Protection: Utilize suitable sealing methods, such as O-rings or thread sealants, to ensure leak-free connections. Protect hose assemblies from abrasion, chafing, or contact with sharp edges or surfaces by using protective covers, sleeves, or clamps.
- Adequate Support: Support hydraulic hoses adequately to prevent excessive stress, vibration, or sagging. Use clamps or brackets specifically designed for hydraulic hoses and position them at appropriate intervals to maintain stability and minimize movement.
- Regular Inspection and Maintenance: After installation, regularly inspect the hydraulic hoses for signs of wear, damage, or leaks. Incorporate routine maintenance checks into your schedule to identify any issues early and address them promptly. Replace hoses as necessary to prevent potential failures.
- Training and Expertise: Ensure that individuals responsible for hydraulic hose installation are properly trained and knowledgeable about the correct procedures and safety precautions. Seek professional assistance or consult hydraulic experts for complex installations or unfamiliar applications.
Regular Cleaning
Keeping hydraulic hoses clean is essential to prevent the accumulation of dirt, debris, or contaminants that can lead to internal damage or blockages. Use a soft brush or cloth to remove any surface dirt regularly.
Avoid using harsh chemicals that can degrade the hose material. Clean hoses contribute to smoother fluid flow and overall system efficiency.
Maintenance of Hose Ends
Pay close attention to the hose ends, where fittings and connections are located. Inspect them for signs of corrosion, damage, or leaks. Tighten fittings if necessary but be careful not to overtighten, as it can cause damage to the hose or fittings.
Replace damaged or worn-out fittings promptly to maintain a secure and leak-free connection.
Fluid Compatibility
Ensure that the hydraulic fluid used is compatible with the hose material. Incompatible fluids can cause deterioration or swelling of the hose, leading to premature failure.
Refer to the manufacturer’s recommendations or consult with hydraulic experts to ensure the proper fluid selection for your specific hoses.
Regular Pressure Checks
Monitor and maintain the appropriate operating pressure for your hydraulic system. Excessive pressure can strain hoses, leading to damage or failure.
Use pressure gauges and regulators to ensure that the system operates within the recommended pressure range.
Scheduled Replacements
Despite regular maintenance, hydraulic hoses have a finite lifespan. Develop a preventive maintenance schedule that includes periodic hose replacements based on usage, environmental conditions, and manufacturer recommendations.
Proactively replacing hoses helps prevent unexpected failures and system downtime.
Conclusion
Proper hydraulic hose maintenance is crucial for the longevity and optimal performance of your hydraulic systems. By following these essential tips and best practices, you can minimize the risk of hose failures, improve system reliability, and maximize the lifespan of your hydraulic hoses.
Stay proactive and incorporate regular maintenance into your operational routine to ensure efficient and uninterrupted operations.