Hydraulic hoses play a crucial role in various industrial applications, transmitting fluid power within machinery and equipment. To ensure a secure and reliable connection, it is essential to crimp hydraulic hoses correctly.
In this article, we will provide a step-by-step guide on how to crimp hydraulic hoses, covering the necessary tools, techniques, and best practices.
What Is Hydraulic Hose Crimping
Hydraulic hose crimping is a method of joining hydraulic hoses and fittings by compressing them together using a crimping machine. The machine applies a specific amount of force to deform the fitting and hose, creating a tight and secure connection. The crimped connection prevents leaks, maintains system integrity, and enables efficient fluid transfer.
Importance of Crimping Hydraulic Hoses
Crimping hydraulic hoses is a crucial step in ensuring the safety and reliability of hydraulic systems. Proper crimping creates a secure, leak-proof connection between the hose and fitting, preventing fluid loss and potential accidents.
Key benefits of crimping hydraulic hoses:
- Leak-Proof Connections: A well-crimped connection ensures a tight seal, preventing fluid leakage that can lead to system failure and safety hazards.
- Durability and Longevity: A properly crimped hose can withstand high pressures and harsh operating conditions, extending its lifespan.
- Safety: A secure connection reduces the risk of accidents caused by hydraulic fluid leaks.
- Efficiency: A well-crimped hose ensures optimal fluid flow, improving system performance and efficiency.
Factors Affecting Crimp Quality:
- Crimping Machine: A high-quality hydraulic hose crimping machine is essential for precise and consistent crimps.
- Die Sets: The correct die set must be used for the specific hose size and fitting type.
- Operator Skill: The operator’s skill and experience play a crucial role in achieving a proper crimp.
- Hose and Fitting Compatibility: The hose and fitting must be compatible to ensure a secure connection.
By following proper crimping procedures and using high-quality equipment, you can ensure the reliability and safety of your hydraulic system.
Tools and Equipment Required for Hydraulic Hose Press
Before we dive into the crimping process, let’s take a look at the tools and equipment you’ll need:
- Hydraulic hose
- Hydraulic fittings
- Crimping machine
- Crimping dies
- Hose cutting machine or a fine-toothed hacksaw
- Measuring tape
- Lubricant
- Safety gloves and goggles
How to Crimp Hydraulic Hose
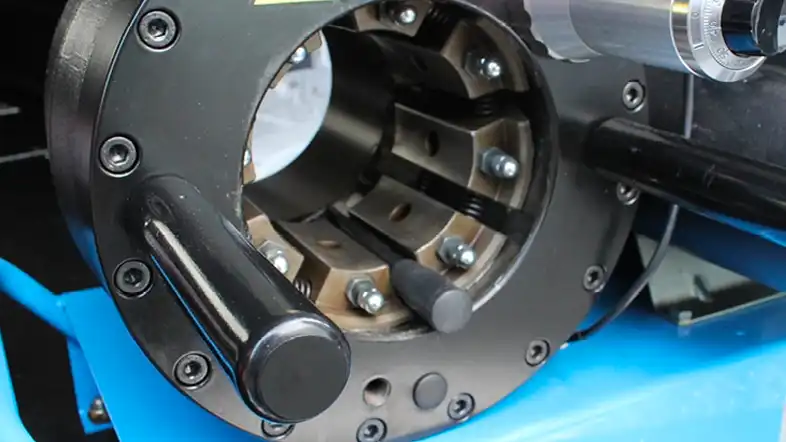
Now let’s explore the step-by-step process of crimping hydraulic hoses:
1. Inspecting the Hose and Fittings
Before you begin crimping, carefully inspect the hydraulic hose and fittings for any damage or defects. Look for signs of wear, such as abrasions, cracks, or bulges. Ensure that the fittings match the hose specifications and are suitable for the intended application.
2. Cutting the Hose to the Required Length
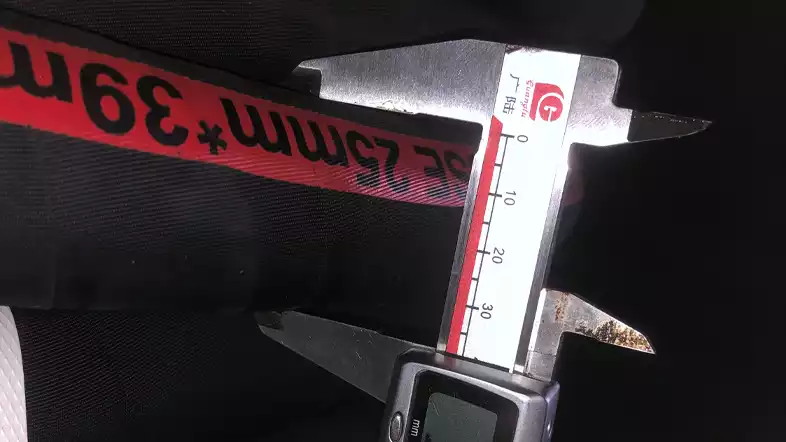
Measure and mark the hose to the required length using a measuring tape. Double-check the measurements before cutting. For a clean and precise cut, use a hose cutting machine or a fine-toothed hacksaw. How Do You Measure Hydraulic Hose?
3. Choosing the Correct Crimping Die
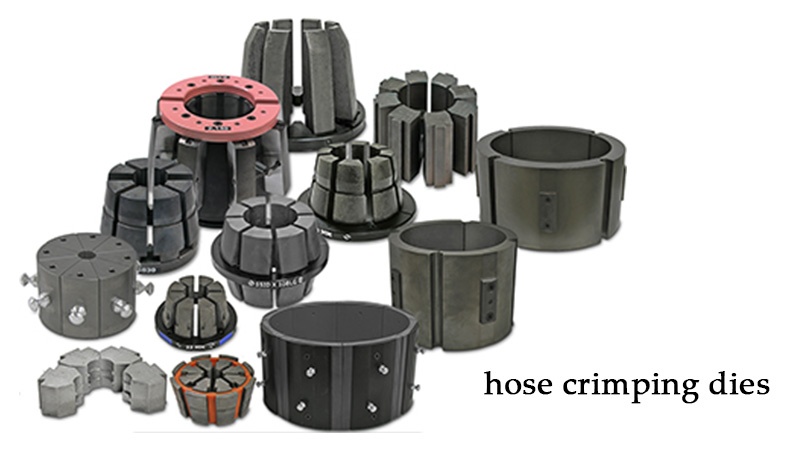
Select the appropriate crimping die size based on the hose and fitting specifications. Refer to the crimping machine’s manual or consult the manufacturer’s guidelines to determine the correct die size for your specific hose and fitting combination.
4. Preparing the Hose and Fittings
Remove any dirt or debris from the inside and outside of the hydraulic hose fittings. This ensures a clean and proper crimped connection. Use compressed air or a suitable cleaning agent to clean the components thoroughly.
5. Lubricating the Hose and Fittings
Apply a thin layer of lubricant oil to the inside of the hydraulic hose and the outside of the hydraulic hose fitting. This facilitates the insertion of the fitting into the hose and reduces friction during the crimping process.
6. Placing the Hose and Fittings into the Crimper
Position the crimping die in the crimping machine as instructed by the manufacturer. Insert the hose and fitting assembly into the crimping die, ensuring that the fitting aligns properly with the die’s shape.
7. Applying Pressure and Crimping the Hose
Activate the crimping machine to apply pressure and compress the crimping die onto the hose and fitting. Follow the recommended pressure and time settings provided by the machine’s manufacturer. Ensure a firm and uniform crimp throughout the length of the fitting.
8. Verifying the Crimped Connection
After crimping, visually inspect the connection for any signs of irregularities or deformations. Verify that the crimped connection meets the manufacturer’s specifications and the industry standards for hydraulic hoses.
Tips and Best Practices for Crimping Hydraulic Hoses
- Always follow the manufacturer’s guidelines and specifications for crimping hydraulic hoses.
- Use genuine and high-quality hydraulic hoses, fittings, and crimping equipment.
- Keep the crimping machine and dies clean and well-maintained for accurate and consistent results.
- Replace the crimping dies periodically to ensure precise and reliable crimped connections.
- Conduct regular inspections and pressure tests on crimped hoses to detect any potential issues.
Common Mistakes to Avoid
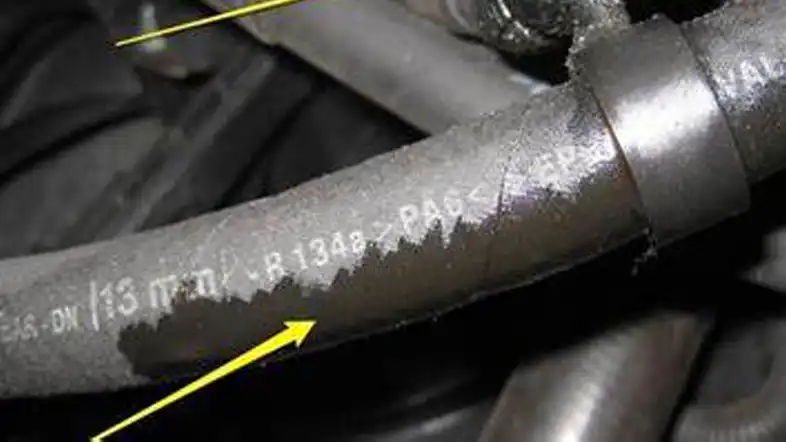
- Neglecting proper inspection of hoses and fittings before crimping.
- Using incorrect die sizes, resulting in an improper crimped connection.
- Failing to clean the hose and fittings adequately, leads to contamination and weakened connections.
- Applying insufficient or excessive crimping pressure compromises the integrity of the connection.
- Neglecting regular maintenance of crimping equipment, leading to inaccurate crimping results.
- Why Your Hydraulic Hose Is Broken? Here Are Some Common Hydraulic Hose Damage Reasons
Conclusion
Crimping hydraulic hoses is a critical process that ensures reliable and leak-free connections within hydraulic systems. By following the step-by-step guide outlined in this article and adhering to best practices, you can achieve secure and durable crimped connections.
Remember to use high-quality components, maintain your crimping equipment, and conduct regular inspections for optimal performance.