If you’re involved in fluid systems and hydraulic machinery, you know the importance of secure connections and reliable performance. Hydraulic hose clamps play a vital role in ensuring the safety, efficiency, and longevity of these systems.
In this article, we will explore the ins and outs of hydraulic hose clamps, their functions, types, installation methods, and much more. Whether you’re a professional in the field or simply interested in learning more, this guide has got you covered.
What Are Hydraulic Hose Clamps?
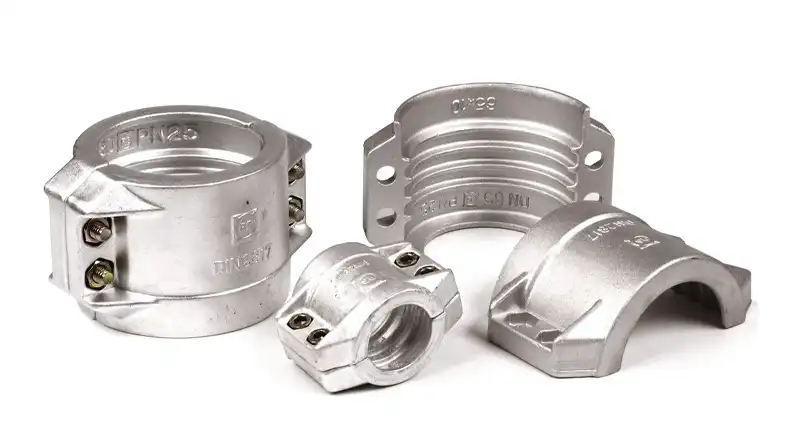
Hydraulic hose clamps, also known as hose clips or hose clamps, are mechanical devices used to secure hydraulic hoses onto fittings, preventing leaks and ensuring a secure connection. They provide the necessary clamping force to hold hydraulic hoses in place, even under high-pressure conditions.
Hydraulic hose clamps only prevent leaks. False
While preventing leaks is a crucial function, hydraulic hose clamps also:
- Withstand pressure:They provide a secure seal to contain high-pressure hydraulic fluid within the hose.
- Reduce vibration and movement: Clamps help to minimize hose movement and vibration, which can cause wear and tear and ultimately lead to leaks.
- Enhance system stability: By securing the hose to fittings, clamps contribute to the overall stability and reliability of the hydraulic system.
Hydraulic hose clamps are essential for preventing leaks in hydraulic systems. True
Hydraulic hose clamps securely fasten hydraulic hoses to fittings, preventing fluid leakage. They provide a strong and reliable connection, ensuring the integrity of the hydraulic system. Properly installed and maintained clamps are crucial for:
- Preventing fluid loss: Minimizing costly fluid leaks and environmental contamination.
- Maintaining system pressure: Ensuring optimal system performance and efficiency.
- Preventing hose failure: Reducing the risk of hose blowouts and potential damage to equipment.
- Enhancing safety: Mitigating potential hazards associated with leaking hydraulic fluid.
What Are Hydraulic Hose Clamps Used For
Hydraulic hose clamps are essential components for any hydraulic system, serving a crucial role beyond just holding a hose in place. Their primary purpose is to provide a secure, tight seal between the hydraulic hose and its fitting. This is vital for preventing fluid leaks under high pressure, which can lead to costly downtime, environmental contamination, and safety hazards. By providing a strong mechanical connection, clamps ensure the integrity and efficiency of the entire hydraulic system.
- Preventing Hydraulic Hose Leaks: Clamps apply a consistent and even pressure around the hose, creating a reliable seal at the connection point. This is fundamental to maintaining system pressure and preventing the escape of hydraulic fluid, which is often under extreme pressure.
- Reducing Vibration and Movement: In dynamic applications, hoses are subject to constant movement and vibration. Clamps secure the hose in its intended position, minimizing this movement. This reduces wear and tear, prevents abrasion against other components, and extends the overall life of the hose.
- Enhancing System Stability: By securely fastening hoses to equipment frames, clamps contribute to the overall stability of the hydraulic system. This prevents hoses from sagging or interfering with other components, ensuring proper routing and a neat, organized setup.
Hydraulic Hose Mounting Clamps
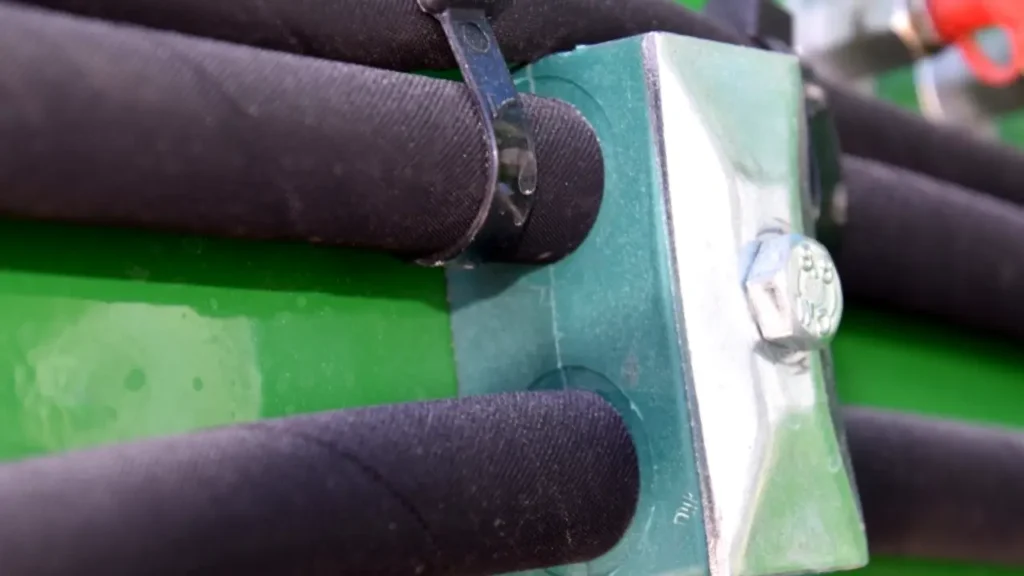
Hydraulic hose mounting clamps are specifically designed to support and secure hydraulic hoses during installation and operation.
Purpose of using a mounting hydraulic hose clamp
Support and Stabilization:
- Prevent sagging and drooping of hoses, especially in long runs or where they are subject to gravity.
- Reduce stress on the hose and fittings caused by weight or movement.
Prevent Abrasion: Protect the hose from contact with sharp edges, moving parts, or other surfaces that could cause wear and tear.
Maintain Position: Secure the hose in its intended position, preventing movement and potential interference with other components.
Types of Mounting Clamps:
- Strap Clamps: Used to secure hoses to various surfaces, such as machinery frames, walls, or ceilings.
- Channel Clamps: Guide hoses along specific paths, often used in conjunction with channels or tracks.
- Vibration Isolators: Reduce the transmission of vibrations to the hose, minimizing fatigue and wear.
- Specialized Clamps: Available for specific applications, such as high-temperature environments or applications with extreme vibration.
Benefits of Using Mounting Clamps:
- Improved Hose Life: Reduced stress and abrasion lead to longer hose lifespan and reduced maintenance costs.
- Enhanced System Performance: Improved hose support contributes to more reliable and efficient hydraulic system operation.
- Improved Safety: Minimize the risk of hose failures and potential hazards.
- Reduced Downtime: Minimize equipment downtime due to hose failures.
Improve Safety:
Minimize Fire Hazards: By preventing leaks and ruptures, hose clamps contribute to a safer operating environment, reducing the risk of fires caused by leaking hydraulic fluid.
In essence, hydraulic hose clamps are essential safety and performance components in any hydraulic system. They ensure reliable operation, minimize downtime, and enhance the overall safety of the system.
How to Choose Suitable Hydraulic Hose Clamps?
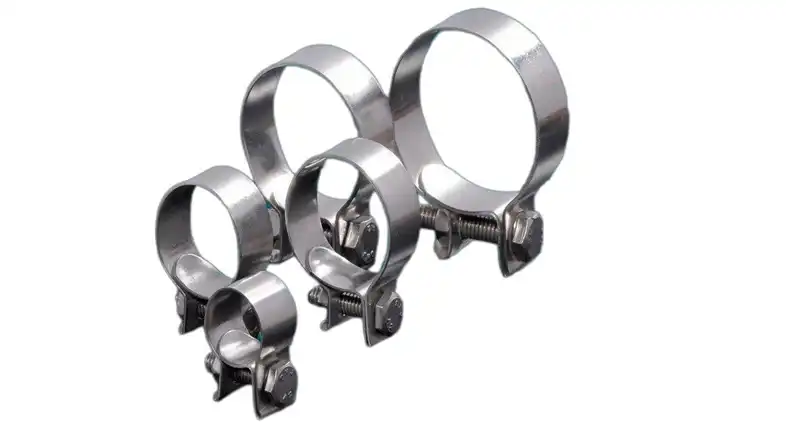
Choosing the right hydraulic hose clamp is a critical step in building a reliable and safe hydraulic system. An improperly chosen clamp can lead to leaks, hose damage, and system failure. To ensure you make the best choice, you must consider the specific operating conditions and requirements of your application, focusing on the hose’s size, the system’s pressure, and the environment in which it will be used.
By carefully evaluating these factors, you can select a clamp that provides a secure seal and extends the life of your hydraulic components.
- Hydraulic Hose Size and Type: The clamp must be perfectly matched to the outer diameter of your hydraulic hose and the fitting. A clamp that is too large or too small will not create a secure seal, risking leaks and hose damage. Always measure the hose’s outside diameter with the fitting installed for an accurate fit.
- Pressure and Application: Consider the maximum pressure your system will encounter. For low-pressure applications, a simple worm gear clamp may be sufficient, while high-pressure or high-vibration systems require heavy-duty T-bolt clamps or specialized constant tension clamps to maintain a secure and consistent grip.
- Environmental Conditions: The operating environment dictates the material of the clamp. For outdoor or corrosive environments, such as marine or chemical applications, a stainless steel clamp is essential for rust and corrosion resistance. In less demanding settings, a carbon steel clamp might be a more economical and suitable option.
Hydraulic Hose Clamp Types
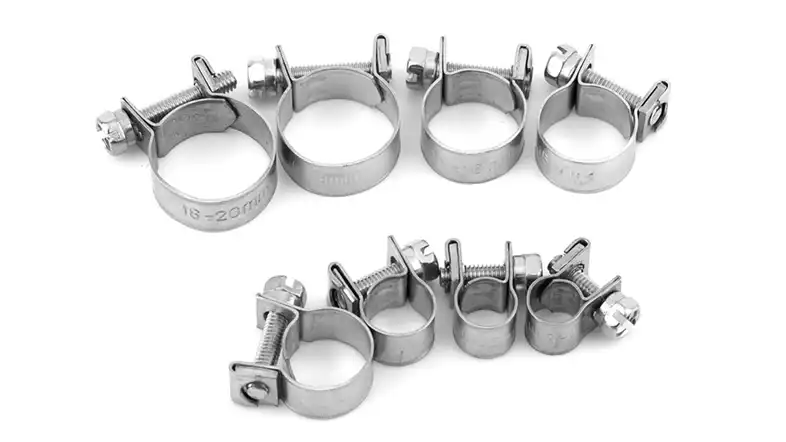
Hydraulic hose clamps come in various designs and configurations to suit different applications and hose sizes. Let’s explore some common types of hydraulic hose clamps:
- Worm Gear Clamps: This is one of the most common and versatile clamps we offer. It uses a screw mechanism to tighten a perforated band, allowing for a wide range of adjustability. These are ideal for general-purpose, low-pressure applications and are easy to install and remove.
- T-Bolt Clamps: For high-pressure and high-vibration applications, we recommend our T-bolt clamps. They provide a much stronger and more consistent clamping force than worm gear clamps. Featuring a T-bolt and nut mechanism, they are made from heavy-duty materials, ensuring a reliable and durable seal.
- Spring Clamps: These clamps are designed to maintain a constant tension, making them perfect for systems that experience temperature fluctuations. As the hose expands and contracts, the spring-loaded design of the clamp adjusts to maintain a tight seal, preventing “cold flow” leaks in cooling systems and other thermal applications.
- Ear Clamps: We use ear clamps for a permanent, tamper-proof seal. They feature one or more “ears” that are crimped with a special tool, creating a strong and secure connection that cannot be easily loosened. These are commonly used in automotive and industrial applications where a permanent seal is desired.
Hydraulic Hose Routing Clamps
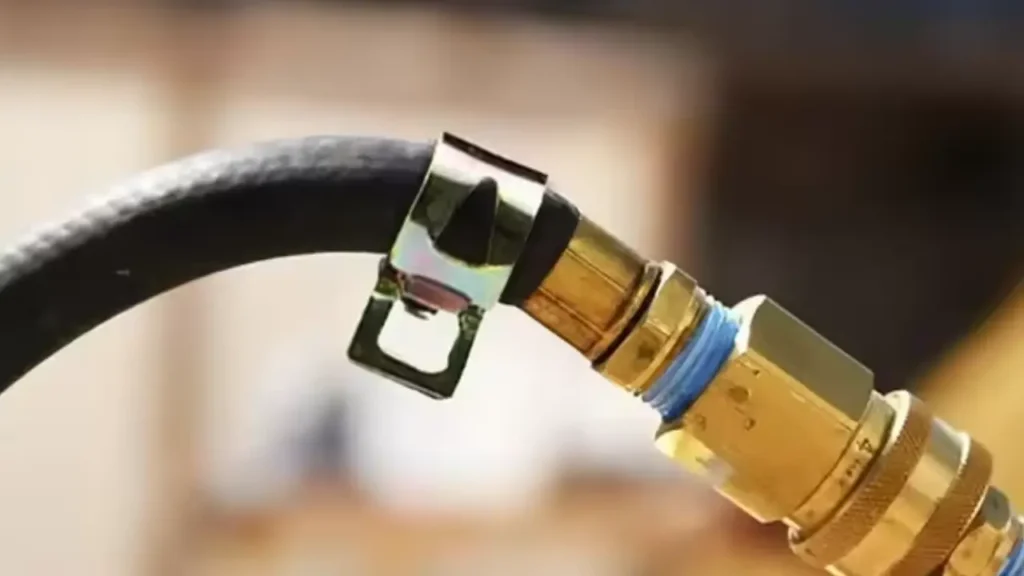
Hydraulic hose routing clamps are essential components for safely and effectively managing hydraulic hose installations. Here’s a breakdown:
Purpose:
Support and Protection:
- Prevent Abrasion: Clamps protect the hose from abrasion and wear caused by contact with sharp edges, moving parts, or other surfaces.
- Reduce Strain: They support the hose’s weight, preventing excessive stress and potential damage due to bending, twisting, or pulling.
- Maintain Position: Clamps secure the hose in its intended position, preventing movement and potential interference with other components.
Improve Safety:
- Prevent Leaks: By preventing excessive movement and stress, clamps help to minimize the risk of leaks and hose failures.
- Reduce Fire Hazards: Proper routing and support can help prevent accidental hose ruptures and the potential for fire hazards.
Types of Routing Clamps:
- Strap Clamps: Simple and versatile, used to secure hoses to various surfaces.
- Channel Clamps: Designed to guide hoses along specific paths, often used in conjunction with channels or tracks.
- Vibration Isolators: Reduce the transmission of vibrations to the hose, minimizing fatigue and wear.
- Specialized Clamps: Available for specific applications, such as high-temperature environments or applications with extreme vibration.
Benefits of Using Routing Clamps:
- Increased Hose Life: Reduced wear and tear leads to longer hose lifespan and reduced maintenance costs.
- Improved Safety: Minimize the risk of leaks, ruptures, and fire hazards.
- Enhanced System Performance: Improved hose support and protection contribute to more reliable and efficient hydraulic system operation.
- Reduced Downtime: Minimize equipment downtime due to hose failures.
Key Considerations:
- Hose Size and Type: Select clamps appropriate for the size and type of hydraulic hose.
- Application Requirements: Consider the specific operating conditions, such as temperature, pressure, vibration, and exposure to chemicals.
- Installation: Ensure proper installation to achieve maximum effectiveness.
By using appropriate routing clamps, you can significantly enhance the performance, safety, and longevity of your hydraulic hose installations.
Benefits of Choosing the Right Clamp
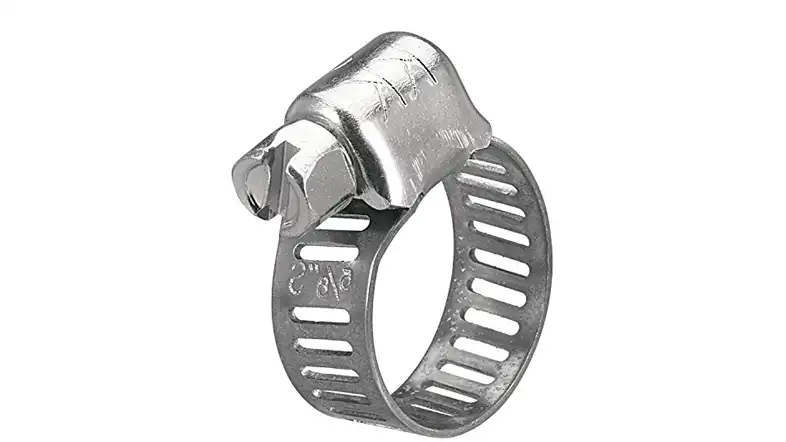
Selecting the appropriate hydraulic hose clamp offers several benefits:
- Leak Prevention: The right clamp ensures a tight and secure connection, minimizing the risk of leaks and fluid loss.
- Enhanced Safety: A properly secured hose prevents accidents, such as hose blowouts, which can result in injuries and damage to equipment.
- Improved System Efficiency: By maintaining a leak-free connection, the clamp helps optimize system performance and efficiency.
- Longevity of Components: Proper clamping reduces stress on hoses and fittings, extending their lifespan and reducing maintenance costs.
Installation Methods for Hydraulic Hose Clamps
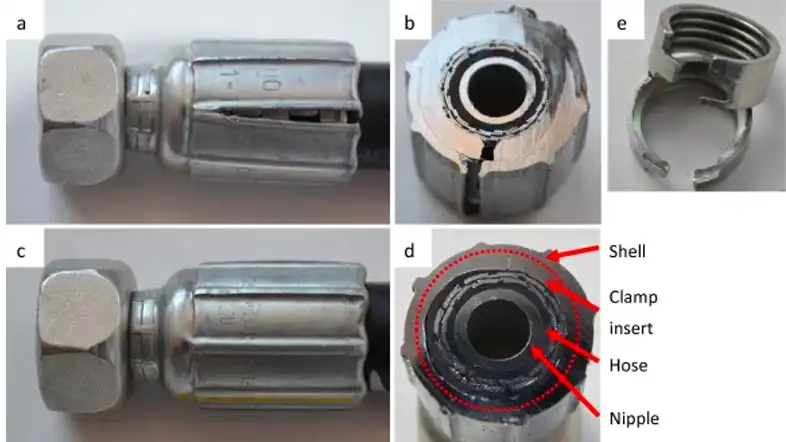
Method 1: Worm Gear Clamps
- Slide the clamp onto the hose, ensuring it is positioned over the fitting.
- Tighten the clamp using a screwdriver or wrench, making sure it applies even pressure around the hose.
- Check the tightness by gently tugging on the hose. It should remain secure without any movement.
Method 2: T-Bolt Clamps
- Position the clamp over the hose and fitting, aligning the bolt holes.
- Insert the T-bolt through the holes and thread the nut onto the bolt.
- Tighten the nut using a wrench until the clamp applies sufficient pressure on the hose.
Method 3: Ear Clamps
- Use a crimping tool specifically designed for ear clamps.
- Place the ear clamp over the hose and fitting, ensuring it covers the barb completely.
- Position the crimping tool on the ear and squeeze it firmly to create a secure connection.
Maintenance and Inspection of Hydraulic Hose Clamps
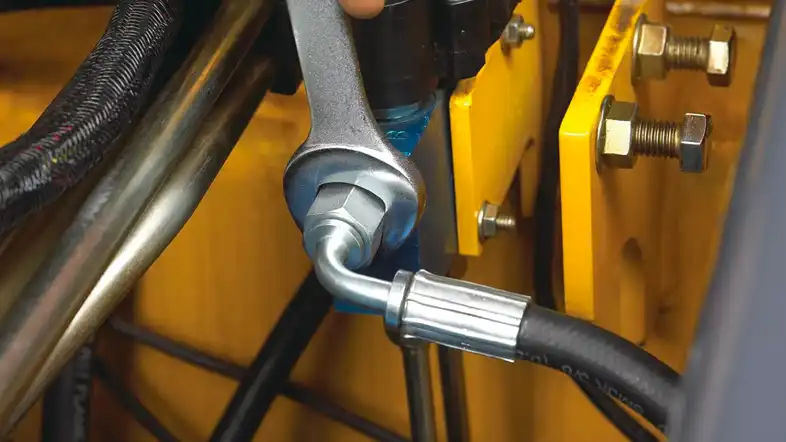
To ensure the optimal performance and longevity of hydraulic hose clamps, regular maintenance and inspection are essential. Follow these guidelines:
- Visual Inspection: Regularly inspect clamps for signs of damage, corrosion, or wear. Replace any clamps that show signs of deterioration.
- Tightness Check: Periodically check the tightness of clamps to ensure they are securely holding the hoses in place. Tighten or readjust as necessary.
- Environmental Factors: Consider the operating conditions and environmental factors that may affect the performance of the clamps. Take necessary precautions to protect them from extreme temperatures, chemicals, or excessive vibration.
Common Issues and Troubleshooting
Leaks
Cause: Insufficient clamping force or worn-out clamps.
Solution: Replace the clamps with ones that provide adequate clamping force. Ensure proper installation and verify the compatibility with hose diameter and pressure requirements. 5 Reasons That Cause Hydraulic Hose Leak
Hose Blowouts
Cause: Improper clamp selection or installation, excessive pressure, or weakened hoses.
Solution: Select the appropriate clamp for the application, considering pressure ratings and hose specifications. Reinstall the clamp following proper installation methods. Inspect hoses for any signs of wear or damage and replace them if necessary.
Corrosion
Cause: Exposure to moisture or corrosive substances.
Solution: Choose clamps made from corrosion-resistant materials like stainless steel. Regularly inspect clamps and replace any that show signs of corrosion.
FAQs About Hydraulic Hose Clamps
What are the key components of a hydraulic hose clamp?
The key components include the band, screw, housing, and locking mechanism.
Can hydraulic hose clamps be reused?
Yes, hydraulic hose clamps can be reused, but it is important to inspect them for any signs of wear or damage before reuse. Replace any clamps that are no longer in optimal condition.
Are hydraulic hose clamps compatible with different types of fluids?
Yes, hydraulic hose clamps are designed to be compatible with a wide range of fluids. However, it is important to consider the material compatibility and ensure the clamp is suitable for the specific fluid being used.
Can hydraulic hose clamps withstand high-pressure conditions?
Yes, hydraulic hose clamps are designed to withstand high-pressure conditions. However, it is crucial to select clamps with the appropriate pressure ratings to ensure optimal performance and safety.
How often should hydraulic hose clamps be inspected and replaced?
Hydraulic hose clamps should be inspected regularly, ideally during routine maintenance checks. Replace any clamps that show signs of wear, damage, or corrosion to maintain system safety and efficiency.
Can hydraulic hose clamps be used in other industries besides hydraulic systems?
Yes, hydraulic hose clamps have applications in various industries beyond hydraulic systems. They are commonly used in automotive, industrial, marine, and agricultural sectors where secure hose connections are necessary.
Conclusion
Hydraulic hose clamps are crucial components in fluid systems, ensuring secure connections and reliable performance. By selecting the right clamp, installing it correctly, and conducting regular maintenance, you can enhance safety, prevent hydraulic hose leaks, and optimize the efficiency of your hydraulic machinery.
Remember to consider factors such as clamp type, material, pressure ratings, and compatibility with fluid types to make informed decisions. Stay proactive with inspections and troubleshooting to address any issues promptly.
By prioritizing the quality and reliability of hydraulic hose clamps, you can ensure the smooth operation of your fluid systems and machinery.