In industrial machinery and equipment, hydraulic systems play a crucial role in powering various operations.
Central to these systems are hydraulic hoses, which are responsible for transporting hydraulic fluid between components. Ensuring the proper functioning of hydraulic hoses is essential for maintaining equipment efficiency, safety, and overall productivity.
In this comprehensive guide, we will delve deep into the world of hydraulic hose inspection, covering every aspect from the importance of hydraulic hose inspection to the step-by-step process.
Importance of Hydraulic Hose Inspection
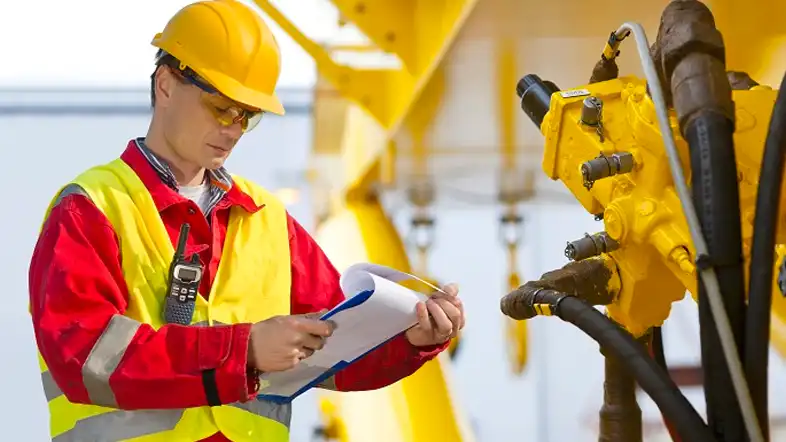
Hydraulic hoses endure immense pressure, extreme temperatures, and the wear and tear of daily operations. Regular inspections are imperative to identify potential issues before they escalate into major problems. Proper maintenance of hydraulic hoses not only extends their lifespan but also prevents unexpected failures that can lead to costly downtime and repairs.
Signs That Call for Inspection
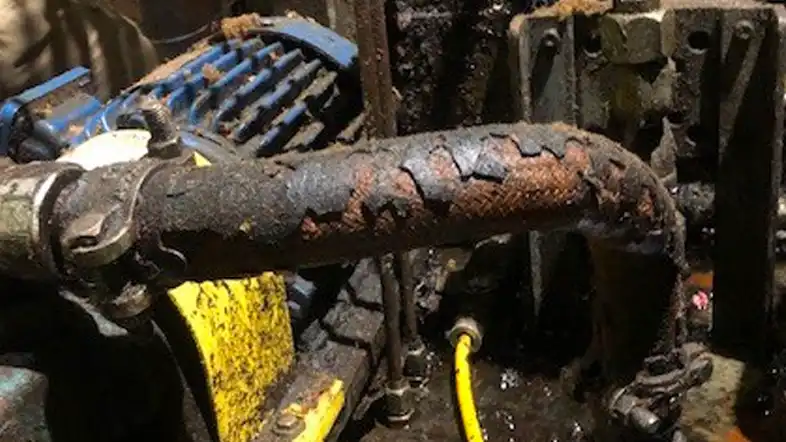
- Visible Damage: Inspect hoses for any visible signs of wear, such as cracks, abrasions, or leaks. Even minor damage can worsen over time, so it’s crucial to address it promptly.
- Fluid Leaks: Hydraulic fluid leaks are indicative of a compromised hose. The presence of fluid around a hose or fitting calls for an immediate inspection.
- Bulges or Swelling: Bulges along the hose’s length are signs of internal damage due to excessive pressure. Swelling indicates potential hose failure and should be assessed without delay.
- Brittleness: If a hose feels excessively stiff or brittle, it might be reaching the end of its lifespan. Such hoses are prone to cracking and should be inspected closely.
- Frayed Ends: Fraying at the hose ends can lead to leaks or separation from fittings. Inspect hose ends regularly and replace them if necessary.
- Reduced Performance: A drop in hydraulic system performance, such as slower operation or weaker force, could be due to hose issues.
Hydraulic Hose Inspection Checklist
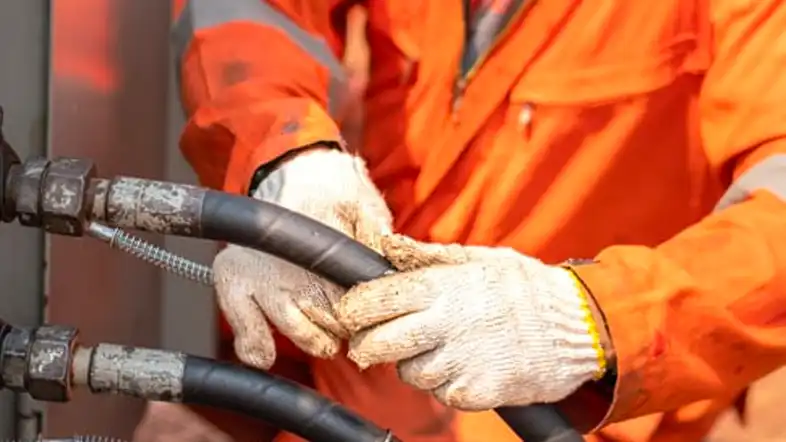
A hydraulic hose inspection checklist is a structured document used by maintenance and engineering professionals to systematically assess the condition of hydraulic hoses in industrial equipment and machinery. This checklist serves as a guide to ensure that all necessary aspects of hose inspection are covered thoroughly.
By following this checklist, technicians can identify potential issues, assess the overall health of hydraulic hoses, and determine if any maintenance or replacement is needed.
Here’s an explanation of the key components typically included in a hydraulic hose inspection checklist:
- Visual Examination: The checklist should start with a visual inspection of the hoses. Technicians look for visible signs of wear, such as cracks, abrasions, or leaks. This involves closely examining the entire length of the hose, including fittings and connections.
- Fluid Leaks: Checking for fluid leaks is a critical step. Any presence of hydraulic fluid around the hose or fittings is a clear indicator of a potential issue. Technicians note the location and severity of leaks.
- Bulges and Swelling: Bulges or swelling along the hose’s surface indicate internal damage caused by excessive pressure. This aspect of the inspection helps technicians identify hoses that might be at risk of bursting.
- Frayed Ends: Fraying at the ends of hoses can lead to leaks and separation from fittings. Technicians assess the condition of hose ends and determine if they need to be repaired or replaced.
- Flexibility Test: Hoses should have a certain degree of flexibility. Technicians gently bend the hose in different directions to check for any cracking sounds or signs of stiffness, which could indicate internal damage.
- Fitting Tightness: Loose fittings can lead to leaks and reduced system efficiency. The checklist includes a step to ensure that all fittings and connections are properly tightened.
- Pressure Test: In cases where no visible damage is present but there are suspicions of internal issues, a pressure test might be conducted. This involves pressurizing the hose within a controlled environment to identify hydraulic hose leaks or weaknesses.
- Record Keeping: Maintenance professionals keep detailed records of each inspection. This includes the date of inspection, findings, any actions taken (such as repairs or replacements), and the technician’s name. These records help track the history of each hose and make informed maintenance decisions.
- Replacement Schedule: The checklist often includes a section to note the manufacturer’s recommended replacement intervals for hoses. This information helps ensure that hoses are replaced proactively before they reach the end of their service life.
- Safety Precautions: Safety is paramount during inspections. The checklist may remind technicians to turn off and depressurize the hydraulic system before beginning the inspection. It may also recommend wearing safety gear, such as gloves and safety goggles.
- Additional Notes: This section provides space for technicians to add any additional observations, recommendations, or specific conditions that might be relevant to the particular inspection.
A well-structured hydraulic hose inspection checklist helps maintenance teams perform thorough and consistent assessments. Regular use of the checklist aids in early detection of potential issues, prevents unexpected failures, and contributes to the overall reliability and safety of industrial machinery.
Here is a hydraulic hose inspection checklist form that you can be free to use for your hydraulic hose maintenance routine.
Hydraulic Hose Inspection Checklist Form
Date: ________
Inspector: ________
Equipment Information:
- Equipment Name: ________
- Equipment ID/Serial Number: ________
Hydraulic Hose Details:
- Hose ID/Serial Number: ________
- Hose Length: ________
- Hose Manufacturer: ________
- Hose Type: ________
- Installation Date: ________
Inspection Points:
- Visual Inspection:
- Check for any visible signs of wear, abrasion, cuts, or damage on the hose surface.
- Inspect the hose fittings for leaks, corrosion, or damage.
- Ensure that the hose clamps are secure and in good condition.
- Look for any signs of oil, hydraulic fluid, or contaminants around the hose connections.
- Hose Integrity:
- Gently bend the hose to check for any stiffness, cracks, or bulges.
- Ensure that the hose retains its flexibility and doesn’t show signs of brittleness.
- Hose Connections:
- Tighten any loose fittings using appropriate tools.
- Check that the fittings are properly aligned and sealed.
- Verify that the connection points are free from dirt, debris, and contamination.
- Fluid Leakage:
- Inspect the hose and fittings for any visible signs of hydraulic fluid leakage.
- Wipe down the hose and fittings to remove any residual fluid and observe for fresh leaks.
- Hose Positioning:
- Ensure that the hose is properly routed and secured, avoiding sharp bends and kinks.
- Check for any contact points with other surfaces that might cause chafing or abrasion.
- Expiry Date/Service Life:
- If applicable, verify the hose’s expiration date or recommended service life.
- Replace hoses that have exceeded their recommended usage period.
- Overall Condition:
- Evaluate the overall condition of the hose based on the inspection.
- Determine if the hose is safe for continued use or if it needs immediate replacement.
Remarks and Recommendations:
Inspector’s Comments: ________
Recommendations: ___________
Signature: _________________
Date: _____________________
This is the Hydraulic hose inspection checklist template that you can download for your conference:
https://kingdaflex.com/wp-content/uploads/2023/08/Kingdaflex-Hydraulic-Hose-Inspection-Checklist.pdf
Hydraulic Hose Inspection Procedure
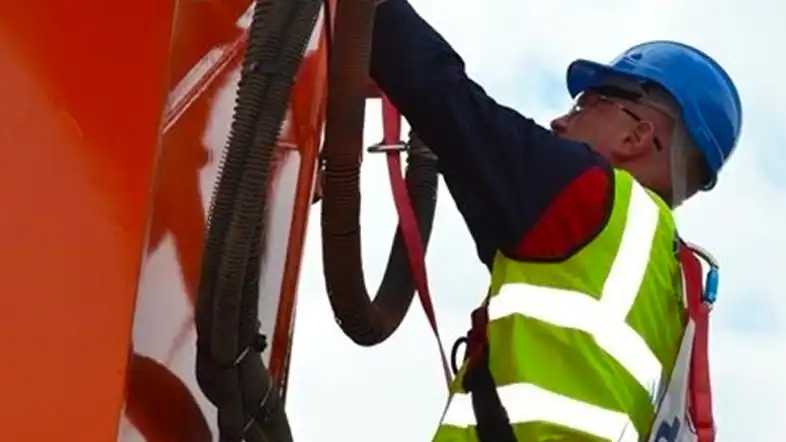
Safety First
Before starting the inspection, ensure that the hydraulic system is turned off and depressurized. Safety goggles and gloves are a must to protect against potential hazards.
Visual Examination
Inspect the entire length of the hose for any visible damage as outlined above. Pay close attention to connections and fittings as they are common points of failure.
Check for Leaks
Wipe down the hoses and fittings to remove any existing fluid. Run the system briefly and check for new fluid leaks. Leaks might indicate loose fittings or damaged hoses.
Assess Hose Flexibility
Gently bend the hose in different directions. A healthy hose should exhibit some flexibility without any cracking sounds. Excessive rigidity suggests internal damage.
Bulges and Swelling
Run the hydraulic system to its maximum pressure and inspect the hoses for any bulges or swelling. If present, replace the hose immediately to avoid potential bursts.
Fitting Tightness
Check the tightness of all fittings and connections. Loose fittings can cause leaks and compromise the system’s efficiency.
Perform Pressure Test
If you suspect a hose might be compromised but don’t see any visible signs, consider a pressure test. This involves pressurizing the hose in a controlled environment to check for leaks or weaknesses.
Keep Detailed Records
Maintain a thorough record of all inspections, including dates, findings, and any actions taken. This history helps in tracking the health of hoses over time.
Hydraulic Hose Inspection Criteria
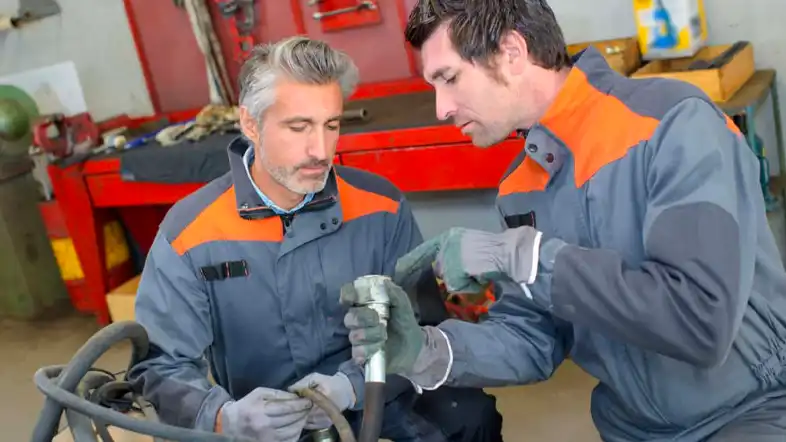
Hydraulic hose inspections are crucial for maintaining the safety and efficiency of hydraulic systems. Regular inspections help identify potential issues before they lead to failures or accidents. Here are the key criteria to consider when inspecting hydraulic hoses:
Visual Inspection:
- Check for any signs of external damage, such as cuts, abrasions, cracks, or bulges along the length of the hose.
- Look for signs of leakage, including oil or fluid residue along the hose or fittings.
Fitting Connections:
- Ensure fittings are securely attached to the hose without any signs of loosening or leakage.
- Check for visible cracks, corrosion, or damage on the fitting surfaces.
Bends and Twists:
- Avoid sharp bends or kinks that could lead to hose fatigue and failure over time.
- Check for any excessive twisting that might cause strain on the hose or fittings.
Abrasions and Wear:
- Inspect hoses for wear caused by friction against other surfaces or components.
- Pay special attention to areas where hoses pass through tight openings or come into contact with moving parts.
Hose Age and Usage:
- Consider the recommended service life of the hose based on the manufacturer’s guidelines.
- Evaluate the operational conditions the hose has been exposed to, as extreme temperatures, high pressures, and harsh environments can impact its lifespan.
Temperature and Fluid Compatibility:
- Ensure that the hose is compatible with the specific hydraulic fluid used in the system.
- Check if the hose is rated for the temperature range of the hydraulic system to prevent degradation or failure.
Crush Hazards:
- Inspect the hose routing to avoid potential crushing or pinching hazards, especially in areas with moving machinery or tight spaces.
Protective Covers and Guards:
- Verify that any protective covers or guards are in place and intact to shield the hose from external damage.
Leaks and Seepage:
- Look for signs of fluid leaks or seepage, which could indicate internal hose damage or fitting issues.
- Monitor for any sudden drops in hydraulic fluid levels, as this could indicate a leak.
Overall Condition:
- Assess the overall condition of the hose, considering all the above factors.
- Decide whether the hose needs immediate replacement or if it can continue in service for a specific period based on its condition.
Remember that regular inspections should be performed based on the operating conditions of the hydraulic system. Following the manufacturer’s guidelines for inspection intervals and maintenance practices is crucial to ensure the longevity and reliability of hydraulic hoses. If any doubts or concerns arise during the inspection, consult with hydraulic system experts or professionals for further guidance.
Regular Maintenance and Replacement
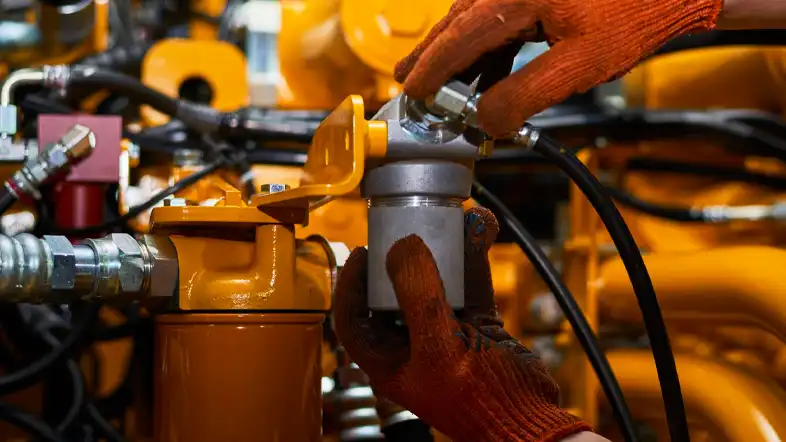
The regular maintenance and replacement of hydraulic hoses is crucial to keep your hydraulic hose safe and strong up.
Regular Maintenance: Regular maintenance is a systematic approach to keeping hydraulic hoses and the entire hydraulic system in good working condition. The goal is to prevent unexpected failures, reduce downtime, and extend the lifespan of components.
Here’s what’s involved in regular maintenance:
- Scheduled Inspections: Set up a routine inspection schedule based on factors such as operating hours, manufacturer recommendations, and environmental conditions. During these inspections, follow the criteria mentioned earlier to identify signs of wear, damage, leaks, or other issues.
- Cleaning: Keep hoses and fittings clean to prevent the accumulation of dirt, debris, and contaminants. A clean system reduces the risk of abrasion and corrosion.
- Lubrication: Apply suitable lubricants to fittings and moving parts to minimize friction and wear. However, be cautious as certain lubricants may be incompatible with hydraulic fluids.
- Tightening: Check and tighten fittings if they show signs of loosening. But, be careful not to over-tighten, as this can damage fittings or cause leaks.
- Record Keeping: Maintain a record of inspections, maintenance actions, and any repairs performed. This record can help track the history of the hoses and guide future maintenance decisions.
Replacement: Replacing hydraulic hoses is necessary when they no longer meet safety and operational standards. Here are the key factors that warrant hose replacement:
- Visible Damage: Hoses with cuts, cracks, bulges, severe abrasions, or other visible damage hydraulic hoses cannot be repaired and should be replaced immediately.
- Leakage: Hoses showing signs of leakage, whether minor seepage or significant leaks, should be replaced to prevent loss of hydraulic fluid and potential system failure.
- Age and Wear: Even if a hose appears to be in good condition, hoses have a finite service life. Over time, the materials can degrade due to factors like temperature, pressure, and exposure to fluids. Replace hoses according to the manufacturer’s recommended service life or if they are showing signs of wear.
- High-Pressure Applications: Hoses used in high-pressure applications may experience accelerated wear. Regularly monitor such hoses and replace them if they exhibit signs of weakening or damage.
- Fluid Compatibility: If you’re changing the hydraulic fluid type, ensure that the hoses are compatible with the new fluid. Incompatibility can lead to degradation and failure.
- Safety Concerns: If a hose is in an area where it’s at risk of being pinched, crushed, or damaged by moving parts, it should be replaced with a hose that has appropriate protective features.
- Upgrades and Improvements: If you’re upgrading or modifying your hydraulic system, consider whether the existing hoses are suitable for the new operating conditions. Replacing hoses might be necessary to ensure optimal performance.
Regular hydraulic hose maintenance involves hydraulic hose routine inspections, cleaning, and basic upkeep to keep hoses in good condition. Replacement is necessary when hoses are damaged, worn out, or no longer suitable for the system’s requirements.
Following these practices will help you maintain a safe and efficient hydraulic system while minimizing downtime and potential risks.
Conclusion
Hydraulic hoses are the lifelines of industrial operations, and their health directly impacts productivity and safety. Regular and meticulous inspection is a responsibility that should never be overlooked. By following the step-by-step process outlined in this guide, you can ensure the longevity and optimal performance of hydraulic hoses within your machinery.
Remember, the safety of your operations relies on the integrity of your hydraulic hoses. Don’t compromise on inspections and maintenance. Stay vigilant, stay safe, and keep your operations running smoothly.