Hydraulic hoses are ubiquitous in various industries, from construction and agriculture to manufacturing and automotive. These flexible tubes, designed to withstand high pressures and harsh conditions, are essential for transporting fluids efficiently. A crucial component in the manufacturing process of these hoses is the hydraulic hose mandrel, often referred to as a PP stick.
In this comprehensive guide, we will delve into the world of hydraulic hose mandrels, exploring their purpose, materials, and the significance of PP sticks in ensuring the quality and performance of hydraulic hoses.
What Is Hydraulic Hose Manderl?
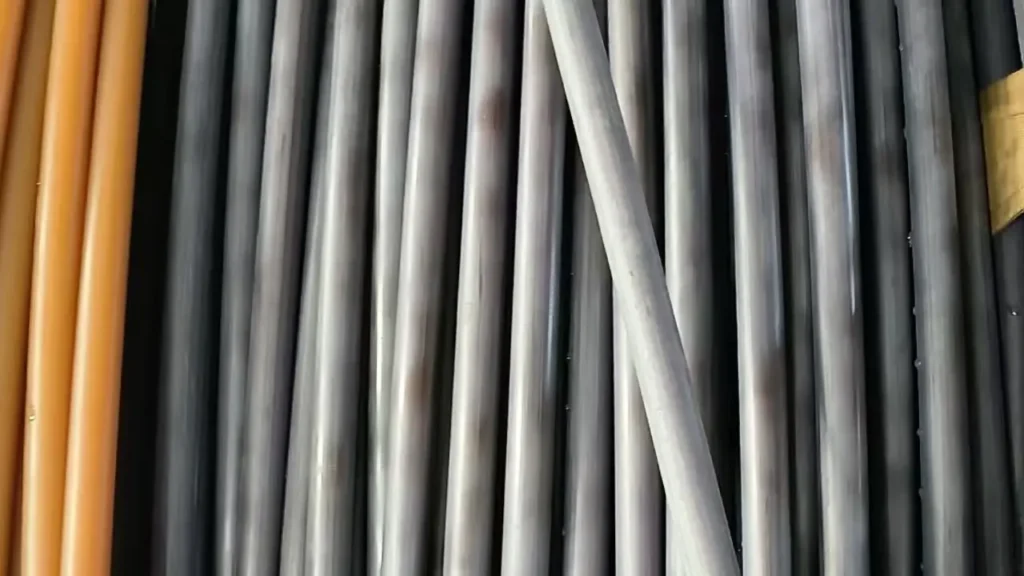
A hydraulic hose mandrel, often referred to as a PP stick, is a long, slender rod typically made of polypropylene (PP) plastic. It plays a crucial role in the manufacturing process of hydraulic hoses.
Key Functions of a Hydraulic Hose Mandrel:
- Shape Retention: The mandrel provides the initial shape and structure for the hose, ensuring it maintains its intended diameter and length.
- Mandrel for Extrusion: It acts as a core around which the rubber or thermoplastic hose material is extruded, ensuring even thickness and consistent quality along the hose length.
- Internal Support: The mandrel remains inside the hose, providing internal support and preventing collapse or deformation under pressure.
- Smooth Inner Surface: The smooth surface of the mandrel contributes to reduced friction and improved fluid flow within the hose.
By understanding the role of hydraulic hose mandrels, we can appreciate the importance of this seemingly simple component in ensuring the quality and performance of hydraulic hoses across various industries.
PP Stick Is Soft Core for Hydraulic Hose
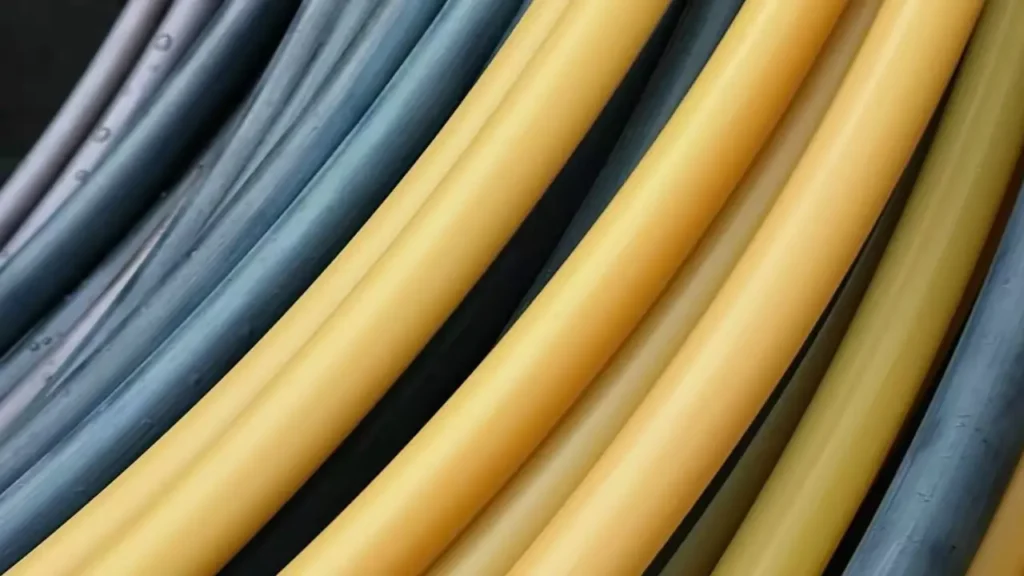
A PP stick is often referred to as a soft core in the hydraulic hose manufacturing process. It’s a flexible, slender rod made of polypropylene plastic that serves as a mandrel during the extrusion process.
Key roles of PP sticks as soft cores:
- Shape Retention: Maintains the desired shape of the hose during extrusion and curing.
- Smooth Inner Surface: Ensures a smooth inner surface of the hose, reducing friction and improving fluid flow.
- Easy Extraction: The flexibility of PP makes it easier to extract from the cured hose, reducing the risk of damage to the hose.
By using PP sticks as soft cores, manufacturers can produce high-quality hydraulic hoses with consistent dimensions and optimal performance.
What Is Hydraulic Hose Manderl Made of?
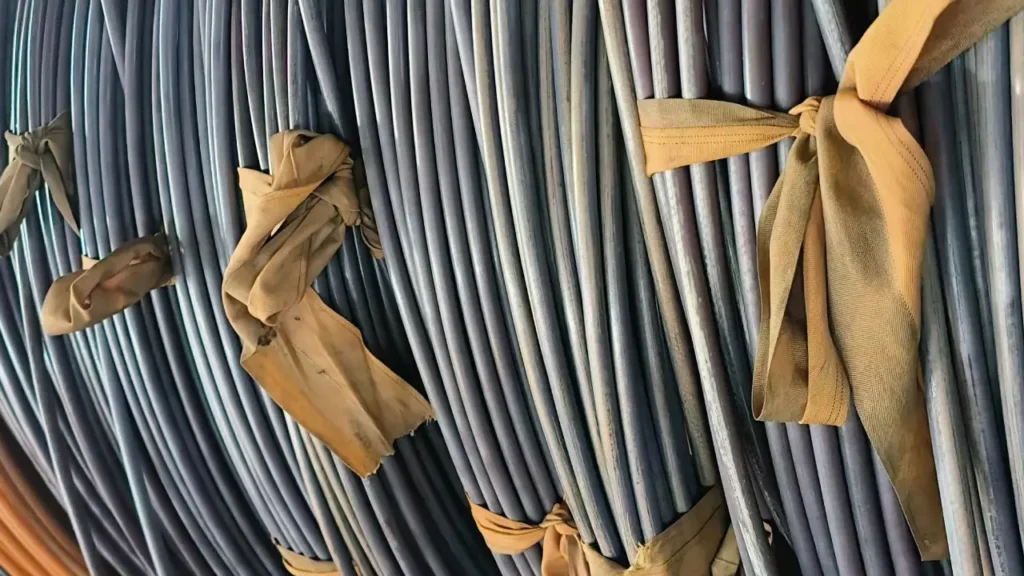
Hydraulic hose mandrels are typically made of polypropylene (PP) plastic.
PP is a popular choice for mandrels due to its:
- Thermal stability: It can withstand the high temperatures involved in the hose manufacturing process.
- Chemical resistance: It is resistant to various chemicals and fluids that may come into contact with the hose.
- Ease of processing: PP is relatively easy to mold and shape into the desired mandrel form.
By using PP mandrels, manufacturers can ensure the production of high-quality hydraulic hoses that meet industry standards.
What Is Hydraulic Hose Manderl Used for?
Hydraulic hose mandrels, often referred to as PP sticks, are essential tools in the manufacturing process of hydraulic hoses.
1. Shape Retention:
- Precise Dimensional Control: Mandrels provide a rigid core that ensures the hose is extruded to the exact diameter and length specified. This precision is crucial for proper fitting and performance.
- Consistent Geometry: By maintaining a consistent shape throughout the manufacturing process, mandrels help to ensure that the hose has a uniform cross-sectional area. This uniformity is essential for optimal fluid flow and pressure handling.
2. Mandrel for Extrusion:
- Even Wall Thickness: The mandrel acts as a central axis around which the rubber or thermoplastic material is extruded. This process ensures that the material is distributed evenly across the hose wall, resulting in consistent thickness.
- Smooth Inner Surface: The smooth surface of the mandrel is transferred to the inner surface of the hose. This minimizes friction and reduces pressure loss, improving the overall efficiency of the hydraulic system.
3. Internal Support:
- Preventing Collapse: The mandrel provides structural support to the hose, especially during high-pressure applications. It helps to prevent the hose from collapsing or deforming, which could lead to leaks and system failure.
- Maintaining Shape under Load: Even when subjected to external forces or internal pressure, the mandrel helps to maintain the hose’s shape, ensuring optimal performance.
4. Smooth Inner Surface:
- Reduced Friction: A smooth inner surface minimizes frictional losses, allowing for efficient fluid flow. This is particularly important in high-pressure applications where even small losses can significantly impact system performance.
- Preventing Particle Accumulation: The smooth surface also helps to prevent the accumulation of particles and debris within the hose, which can lead to clogging and reduced flow.
By understanding the critical role of hydraulic hose mandrels, manufacturers can ensure the production of high-quality hoses that meet the demanding requirements of various industries.
PP Stick is Used for Small-Diameter Hydraulic Hose
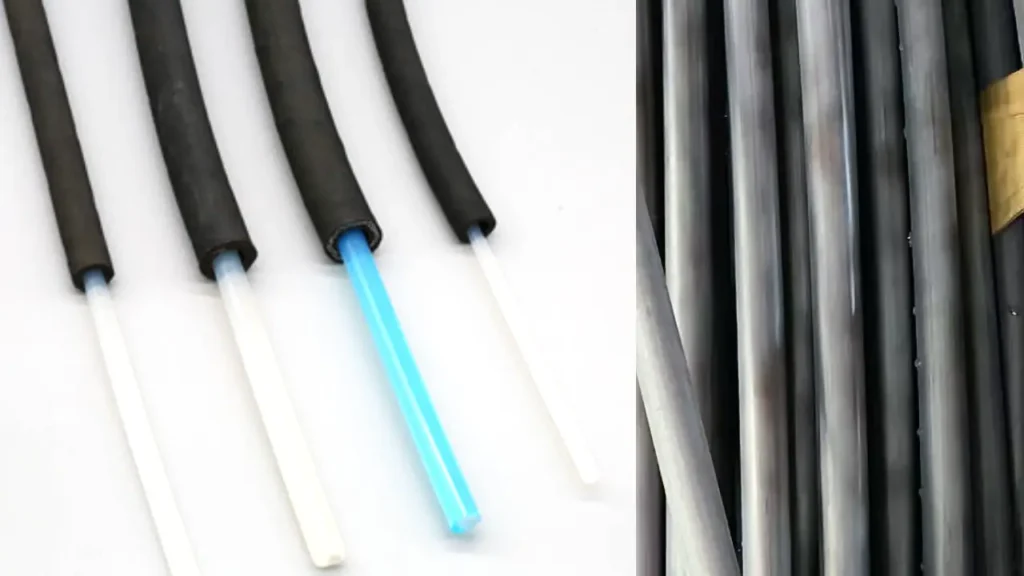
While PP sticks are commonly used in the manufacturing of smaller-diameter hydraulic hoses, their application isn’t solely limited to this size range.
The choice of mandrel material, including PP, depends on several factors:
- Hose diameter: Smaller diameter hoses often benefit from the flexibility and ease of extraction offered by PP sticks.
- Hose material: The type of rubber or thermoplastic used in the hose can influence the choice of mandrel material.
- Manufacturing process: The specific extrusion and curing techniques employed can impact the suitability of different mandrel materials.
- Desired hose properties: Factors such as pressure rating, temperature resistance, and flexibility can affect the choice of mandrel.
In addition to PP, other materials like metal and composite materials may be used for mandrels, especially for larger diameter hoses or those with complex geometries.
Ultimately, the selection of the appropriate mandrel material is a critical decision that can significantly impact the quality, performance, and cost-effectiveness of hydraulic hoses.
When to Use Hose Manderls During Hydraulic Hose Manufacturing Process
Hose mandrels are employed at various stages of the hydraulic hose manufacturing process to ensure the desired shape, size, and internal surface quality. Here are the key instances when mandrels are utilized:
1. Inner Tube Extrusion:
- Shape Retention: The mandrel provides a core around which the rubber or thermoplastic material is extruded, ensuring the inner tube maintains its intended diameter and shape.
- Smooth Inner Surface: The smooth surface of the mandrel transfers to the inner surface of the tube, reducing friction and improving fluid flow.
2. Reinforcement Layer Application:
- Dimensional Control: The mandrel maintains the inner diameter of the hose, ensuring proper alignment and tension of the reinforcement layers.
- Uniform Wall Thickness: By providing a consistent core, the mandrel helps to achieve uniform wall thickness throughout the hose.
3. Outer Cover Extrusion:
- Shape Preservation: The mandrel prevents the inner layers from collapsing or deforming during the outer cover extrusion process.
- Consistent Diameter: The mandrel helps maintain the overall diameter of the hose, ensuring proper fit and performance.
The PP stick hose material will stay in the hydraulic hose the whole way during the hydraulic hose production process, and it will be removed away using water pressure after hydraulic hose manufacturing.
How to Choose Hose Mandrels for Hydraulic Hose?
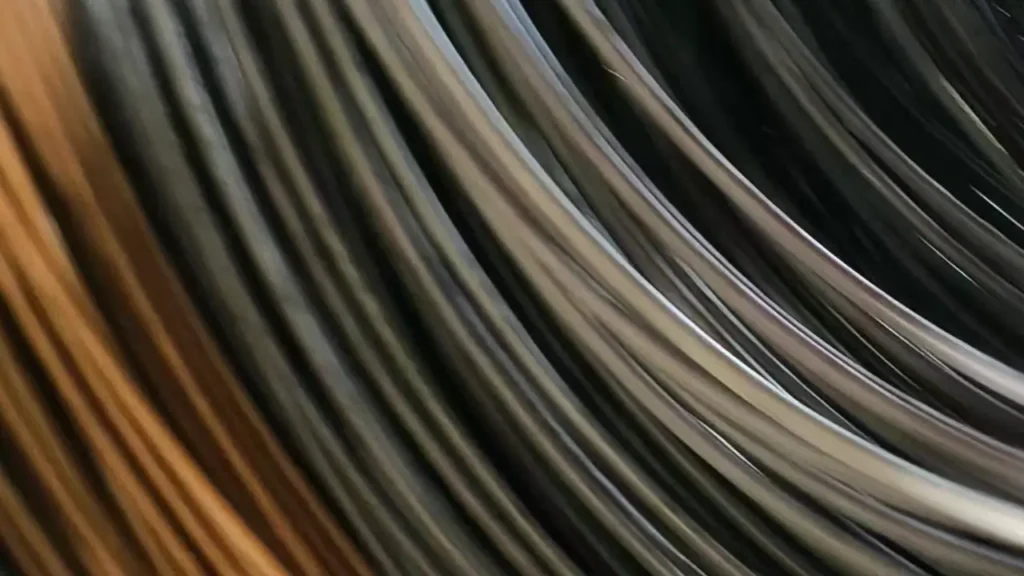
Choosing the right mandrel for your rubber hose ensures optimal performance and product quality.
Here are some key factors to consider when selecting a mandrel:
1. Mandrel Material:
- Polypropylene (PP): A common choice due to its cost-effectiveness, thermal stability, and chemical resistance. Ideal for general-purpose hoses.
- Nylon: Offers higher strength and stiffness compared to PP. Suitable for hoses requiring increased durability and dimensional stability.
- EPDM: Provides excellent heat resistance and weatherability. Ideal for hoses used in high-temperature or outdoor environments.
- TPE: Offers flexibility and ease of extraction. Suitable for hoses with complex geometries or delicate inner layers.
2. Mandrel Diameter:
- Precise Fit: The mandrel diameter should be slightly smaller than the desired inner diameter of the hose to allow for material expansion during the extrusion process.
- Tolerance: The tolerance of the mandrel diameter is critical to ensure consistent hose dimensions.
While the hose mandrel’s diameter does influence the final inner diameter of the hydraulic hose, it’s not a direct correlation.
The hose mandrel’s diameter is typically slightly smaller than the desired inner diameter of the hose. This is because the rubber or thermoplastic material expands around the mandrel during the extrusion process, resulting in a slightly larger final inner diameter.
The exact relationship between the mandrel diameter and the final inner diameter can vary depending on the material used, the extrusion process, and the desired tolerance.
It’s important to note that the mandrel serves as a core or former to shape the hose, provide internal support, and ensure a smooth inner surface. Its primary function is not to directly determine the inner tube diameter, but rather to influence its shape and quality.
3. Mandrel Surface Finish:
- Smoothness: A smooth surface finish minimizes friction and prevents damage to the hose inner layer.
- Texture: In some cases, a textured surface can be beneficial for improved adhesion between the hose material and the mandrel.
4. Mandrel Length:
- Hose Length: The mandrel should be long enough to accommodate the desired hose length, plus additional length for the curing process and extraction.
5. Mandrel Extraction Method:
- Mechanical Extraction: Suitable for simple mandrel designs and low-volume production.
- Hydraulic Extraction: Efficient for high-volume production and complex mandrel designs.
- Thermal Extraction: Involves heating the hose to facilitate mandrel removal.
Additional Considerations:
- Hose Application: The specific application of the hose will influence the choice of mandrel material, diameter, and surface finish.
- Production Volume: High-volume production may require specialized mandrels with features like quick-release mechanisms or automated extraction systems.
- Environmental Factors: The operating environment of the hose, such as temperature, humidity, and chemical exposure, can impact the choice of mandrel material.
By carefully considering these factors, you can select the appropriate mandrel to ensure the production of high-quality rubber hoses that meet the specific needs of your application.
Would you like to delve deeper into any specific aspect of hose mandrel selection or hydraulic hose manufacturing processes?
How to Remove PP Stick from Hydraulic Hose
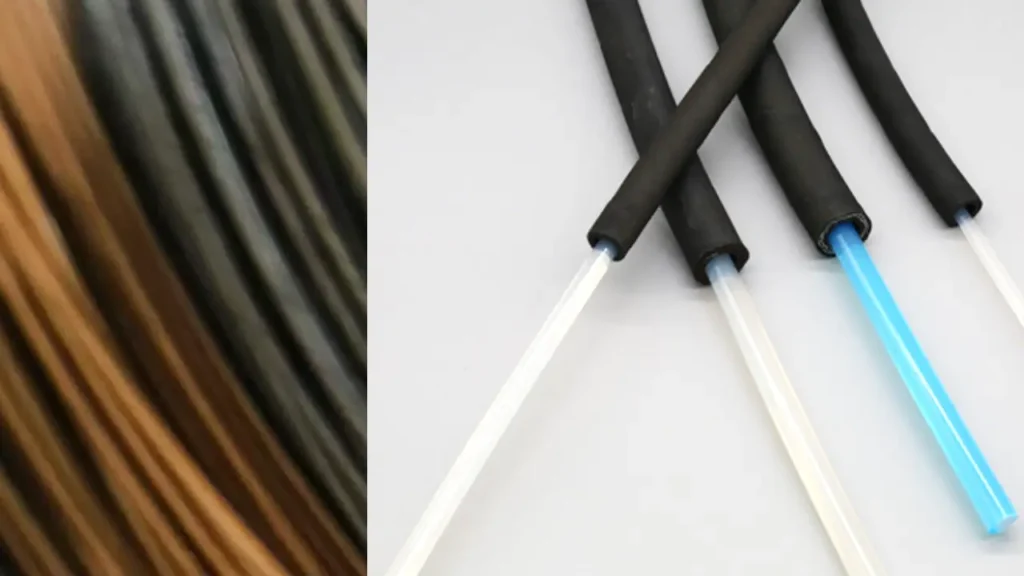
This method involves using high-pressure water to force the mandrel out of the hose.
Here’s a more detailed explanation about taking PP stick out of inner tube of hydraulic hose:
Mandrel Extraction Lines for Hydraulic Hoses
Mandrel extraction is a crucial step in the hydraulic hose manufacturing process. It involves removing the mandrel, which is a core used to shape the hose during extrusion and curing.
Flexible Mandrel Extraction
As you mentioned, hydraulic extraction is a common method for removing flexible mandrels. Here’s a breakdown:
- Hose Preparation: The cured hose is positioned on a conveyor system.
- Sealing: One end of the hose is sealed to prevent water leakage.
- High-Pressure Water Injection: High-pressure water is injected into the sealed end of the hose.
- Mandrel Ejection: The water pressure forces the mandrel out of the open end of the hose.
Rigid Mandrel Extraction
For rigid mandrels, a mechanical extraction process is often employed:
- Conveyor System: The cured hoses, with rigid mandrels inside, are placed on a conveyor system.
- Mandrel Extraction Machine: The conveyor system feeds the hoses into a machine equipped with grippers or clamps to hold the hose.
- Mandrel Removal: The machine pulls the mandrel out of the hose, often using a combination of mechanical force and hydraulic pressure.
- Mandrel Storage: The extracted mandrels are collected and stored on racks for reuse.
Key Considerations for Mandrel Extraction Lines:
- Efficiency: The line should be designed to maximize throughput and minimize downtime.
- Mandrel Damage: The extraction process should be gentle to avoid damaging the mandrels, especially reusable ones.
- Hose Integrity: The extraction process should not damage the hose itself.
- Operator Safety: The line should be designed with safety features to protect operators from injuries.
- Environmental Impact: The extraction process should minimize waste and pollution.
By optimizing these factors, manufacturers can ensure efficient and effective mandrel extraction, contributing to the overall productivity and quality of hydraulic hose production.
Advantages of Hydraulic Extraction:
- Efficiency: It’s a relatively quick and efficient method for removing mandrels from long hoses.
- Reduced Damage: Compared to mechanical methods, hydraulic extraction can minimize the risk of damaging the hose.
Considerations for Hydraulic Extraction:
- Water Pressure: The water pressure must be sufficient to overcome the friction between the mandrel and the hose.
- Hose Material: The hose material must be resistant to high-pressure water to avoid damage.
- Equipment: Specialized equipment, such as high-pressure pumps and fittings, is required.
By carefully controlling the water pressure and ensuring proper equipment setup, hydraulic extraction can be a reliable method for removing mandrels from hydraulic hoses.
Conclusion
In conclusion, hydraulic hose mandrels, particularly PP sticks, play a vital role in the manufacturing process of hydraulic hoses. By understanding their function and the factors influencing their selection, manufacturers can ensure the production of high-quality hoses that meet the demanding requirements of various industries.
From shape retention and extrusion to internal support and surface finish, mandrels contribute significantly to the overall performance and reliability of hydraulic hoses. By carefully considering factors like material, diameter, surface finish, and extraction method, manufacturers can optimize the mandrel selection process and produce hoses that meet specific application needs.
Need a Custom Hydraulic Hose Solution?
At Kingdaflex, we specialize in providing high-quality, custom hydraulic hoses tailored to your specific requirements. Our experienced team utilizes advanced manufacturing techniques and premium materials to deliver hoses that exceed industry standards.
Contact us today to discuss your project and receive a personalized quote.