Hydraulic Hose Safety: Protecting Workers from High-Pressure Hazards is paramount in industrial environments. High-pressure hydraulic systems, while incredibly efficient, pose significant risks if not properly managed. Understanding these dangers and implementing robust safety protocols is crucial for preventing serious injuries and costly accidents on the job.
This blog post will delve into the critical aspects of hydraulic hose safety, highlighting the potential hazards associated with high-pressure fluid injection, hose ruptures, and improper handling. We’ll explore practical strategies and best practices to ensure a safer working environment for everyone operating near hydraulic machinery, minimizing risks effectively.
What Effect Hydraulic Hose Safety
Hydraulic hose safety has a profound impact across various aspects of operations. Here’s a look at those effects, broken down into key areas:
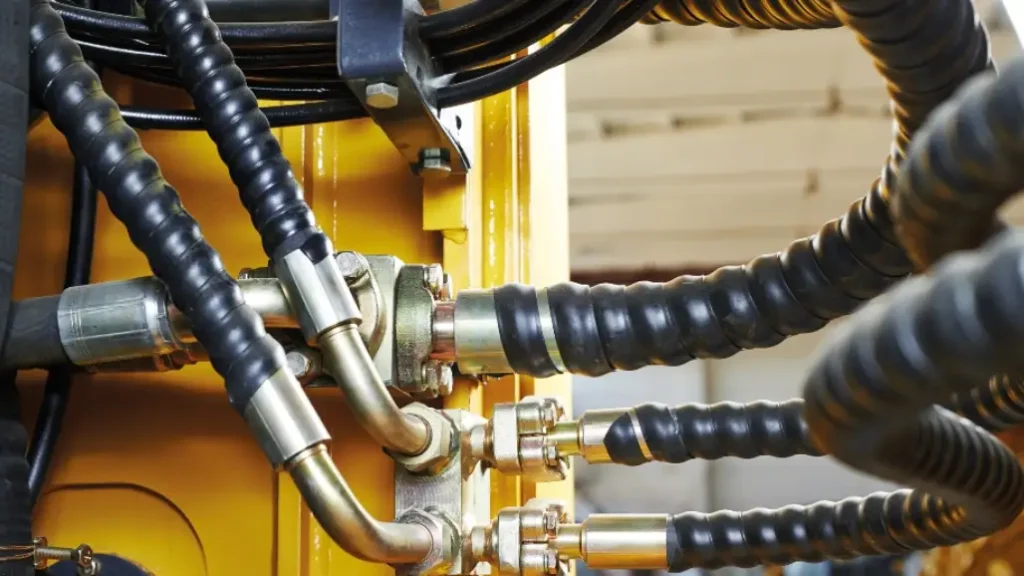
1. Personnel Safety
A primary effect of prioritizing hydraulic hose safety is the protection of personnel. High-pressure hydraulic fluid leaks and hose bursts can cause severe injuries, including skin punctures, burns, and even fatalities. Implementing safety measures, such as regular inspections, proper hose selection, and protective shielding, significantly reduces the risk of these incidents. Well trained employees are much less likely to have accidents. Proper safety also increases moral within the workforce. When employees feel safe, they are more productive.
Furthermore, a culture of safety fostered by adherence to hydraulic hose safety protocols promotes awareness and proactive behavior among workers. When personnel are educated about the risks and understand the importance of preventative measures, they are more likely to identify and report potential hazards before they escalate. This creates a safer work environment for everyone.
2. Equipment and Operational Efficiency
Hydraulic hose failures can lead to costly equipment downtime and repairs. When a hose bursts, it can cause damage to other components in the hydraulic system, as well as the surrounding equipment. This disruption can significantly impact productivity and operational efficiency. By implementing a robust hydraulic hose safety program, businesses can minimize these disruptions and maintain smooth operations. Keeping machines running well, also increases the life span of the machines.
Moreover, preventative maintenance and regular inspections can extend the lifespan of hydraulic hoses, reducing the frequency of replacements and associated costs. Properly maintained hydraulic systems also operate more efficiently, consuming less energy and reducing waste. This translates to increased productivity and cost savings over time.
3. Financial and Legal Implications
Hydraulic hose failures can result in substantial financial losses due to equipment damage, downtime, and potential legal liabilities. Accidents caused by hose failures can lead to worker compensation claims, lawsuits, and regulatory fines. Adhering to hydraulic hose safety standards can mitigate these financial risks and protect the company’s reputation. Also, insurance premiums can rise when companies have many accidents.
Furthermore, compliance with safety regulations is essential to avoid legal penalties and maintain a positive standing with regulatory bodies. By prioritizing hydraulic hose safety, businesses demonstrate their commitment to workplace safety and reduce the risk of legal repercussions. This proactive approach can also enhance the company’s image and build trust with customers and stakeholders.
Hydraulic Hose Safety Rules
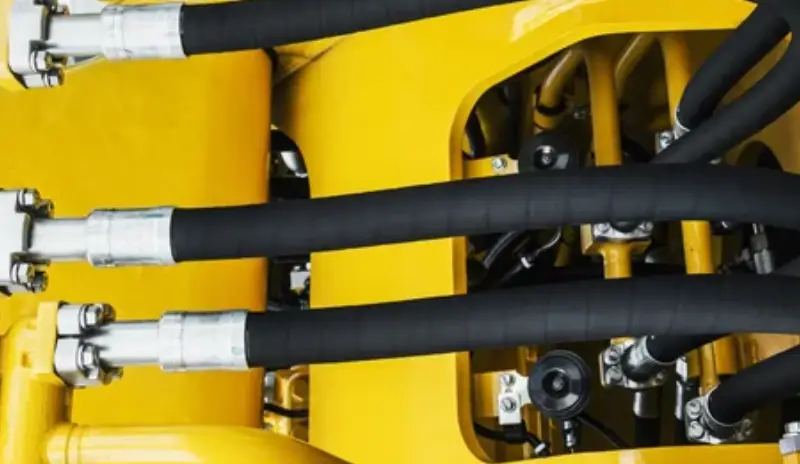
Here are essential hydraulic hose safety rules to protect workers from high-pressure hazards. Adhering to these guidelines is vital for preventing serious injuries and maintaining operational safety in any environment utilizing hydraulic systems.
- Always conduct pre-operation inspections: Before starting any hydraulic equipment, visually inspect all hoses for signs of wear, abrasion, cuts, bulges, or leaks. Ensure all connections are secure and free from damage, as even minor issues can lead to catastrophic failures under pressure.
- Never exceed recommended pressure ratings: Each hydraulic hose is designed for a specific maximum working pressure. Operating hoses above their rated capacity can cause sudden rupture, leading to explosive fluid release and potential severe injury or equipment damage.
- Wear appropriate Personal Protective Equipment (PPE): When working with or near hydraulic systems, always use safety glasses, gloves, and protective clothing. High-pressure fluid injection injuries can be extremely severe, often requiring immediate medical attention.
- Properly route and secure hydraulic hoses: Ensure hoses are routed away from sharp edges, hot surfaces, and moving parts that could cause abrasion or damage. Use clamps or ties to secure hoses, preventing kinking, twisting, or excessive bending, which can compromise their integrity.
- Depressurize hydraulic systems before maintenance: Before performing any maintenance, adjustments, or hose replacements, always shut down the hydraulic system and fully relieve all residual pressure. This crucial step prevents unexpected fluid discharge and potential injection injuries.
Hydraulic Hose Safety Factors
Ensuring hydraulic hose safety requires careful consideration of several key factors.
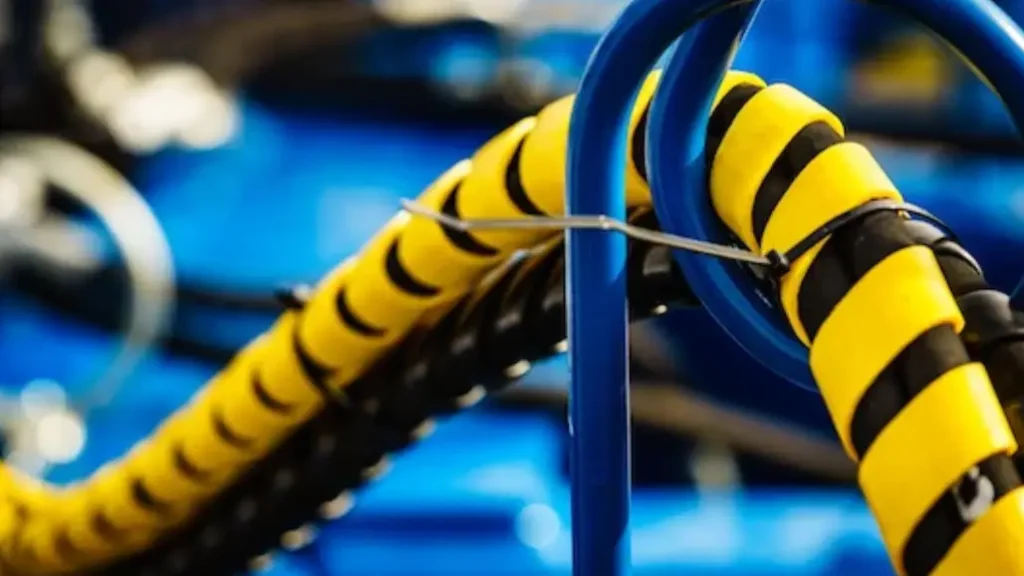
1. Material Compatibility and Hose Selection
Choosing the right hydraulic hose material is paramount. The hydraulic fluid, operating temperatures, and environmental conditions must be compatible with the hose’s inner tube, reinforcement layers, and outer cover. Incompatible materials can degrade, leading to premature failure and hazardous leaks. For instance, some fluids can cause certain rubber compounds to swell or harden, compromising the hose’s integrity.
Selecting the appropriate hose size and pressure rating is equally crucial. The hose must be capable of withstanding the maximum operating pressure and flow rate of the hydraulic system, including potential pressure surges. Undersized or under-rated hoses can burst under pressure, posing a significant safety risk. Additionally, the hose’s construction, including the number and type of reinforcement layers, must be suitable for the intended application.
2. Installation and Routing Procedures
Proper hydraulic hose installation is essential for preventing hose failures. Incorrect routing, twisting, or kinking can create stress points that weaken the hose and lead to premature wear. Hoses should be routed to avoid sharp edges, hot surfaces, and moving parts that could cause abrasion or damage. Securing hoses with clamps or brackets can prevent excessive movement and vibration, which can also contribute to wear.
Fittings must be correctly selected and installed to ensure a leak-free connection. Over-tightening fittings can damage the hose or fitting, while under-tightening can lead to leaks. Using compatible fittings and following the hydraulic hose manufacturer‘s torque specifications are crucial for a secure and reliable connection. Additionally, ensuring proper bend radius is observed during installation will prevent kinking and premature failure.
3. Inspection and Maintenance Protocols
Regular hydraulic hose inspections are vital for detecting signs of wear, damage, or deterioration. Visual inspections should include checking for cracks, abrasions, bulges, leaks, and loose fittings. Implementing a scheduled inspection program and keeping detailed records can help identify potential problems before they lead to failures. Also pressure testing the lines periodically can show a weakness that a visual inspection may not.
Preventative maintenance, such as replacing hoses according to the manufacturer‘s recommendations or when signs of wear are detected, can significantly extend hose lifespan and prevent failures. Maintaining clean hydraulic fluid is also essential, as contaminated fluid can damage the hose’s inner lining and accelerate wear. Implementing a fluid filtration system and regularly changing the fluid can help maintain system cleanliness and prolong hose life.
How to Protect Hydraulic Hoses
Protecting hydraulic hoses is crucial for preventing failures and ensuring safety. Here are some of common and effective hydraulic hose protection methods in the following:
1. Protective Sleeves and Wraps:
Abrasion Resistance:
- These products, often made of durable materials like ballistic nylon or high-density polyethylene, shield hoses from rubbing against surfaces, preventing wear and tear.
- They act as a sacrificial layer, taking the brunt of the abrasion and extending the hose’s lifespan.
Burst Protection:
- Specialized sleeves can contain hydraulic fluid in the event of a hose burst, minimizing the risk of high-pressure fluid injection injuries.
- These are particularly important in applications where personnel are in close proximity to hydraulic systems.
2. Spiral Guards:
Impact and Crush Protection:
- Spiral guards, typically made of plastic or metal, wrap around the hose, providing a barrier against impacts and crushing forces.
- They’re effective in environments where hoses are exposed to heavy machinery or falling objects.
Flexibility and Routing:
- These guards maintain hose flexibility while providing protection, allowing for proper routing and preventing kinks.
3. Spring Guards:
Kink Prevention:
- Spring guards, made of coiled metal, prevent hoses from kinking, which can restrict fluid flow and lead to pressure buildup.
- They distribute bending forces evenly along the hose, ensuring a smooth flow path.
Heavy-Duty Protection:
These are especially useful in heavy duty applications where hoses are exposed to very harsh conditions.
4. Fire Sleeves:
Heat Resistance:
- Fire sleeves, made of heat-resistant materials, protect hoses from extreme temperatures and flames.
- They’re essential in applications where hoses are exposed to hot surfaces or potential fire hazards.
5. Correct Hose Routing and Clamping:
Avoiding Stress Points:
- Proper hose routing minimizes stress points, preventing excessive bending, twisting, or stretching.
- Hoses should be routed away from sharp edges, hot surfaces, and moving parts.
Secure Fastening:
Clamps and brackets should be used to securely fasten hoses, preventing movement and vibration that can lead to wear and tear.
Proper clamping also keeps hoses from rubbing against other machine components.
6. Bend Restrictors:
Maintaining Bend Radius:
- These devices prevent hoses from bending beyond their minimum bend radius, which can damage the hose’s reinforcement layers.
- They help to ensure proper fluid flow and prevent premature hose failure.
By implementing these protection methods, you can significantly reduce the risk of hydraulic hose failures and create a safer working environment.
Quote Hydraulic Hoses from Kingdaflex
Prioritizing Hydraulic Hose Safety is not merely a compliance issue; it’s a fundamental commitment to worker well-being and operational integrity. By diligently implementing the safety measures discussed, from regular inspections and proper maintenance to comprehensive training, you can significantly mitigate the risks associated with high-pressure hydraulic systems. A proactive approach safeguards your most valuable asset: your employees.
Investing in high-quality hydraulic hoses and fittings is a crucial step in bolstering your safety protocols. Superior materials and manufacturing processes directly contribute to the reliability and longevity of your hydraulic systems, reducing the likelihood of unexpected failures and dangerous incidents. Don’t compromise when it comes to the components that keep your operations running smoothly and safely.
For all your hydraulic hose needs, trust Kingdaflex.com. We offer a wide range of wholesale hydraulic hoses designed to meet rigorous safety standards and deliver exceptional performance in demanding industrial applications. Visit Kingdaflex.com today to secure reliable, high-quality hydraulic hoses that will help you maintain a safe and efficient working environment.