Hydraulic hose manufacturing is a complex process that requires careful consideration of various factors to ensure the final product meets specific performance requirements. One crucial aspect is the selection of the appropriate mandrel, which serves as the core around which the hose is extruded.
In this blog post, we will delve into the two primary types of mandrels: soft cores and rigid cores, and discuss how to choose the right one for your specific needs.
What Is Soft Core for Hydraulic Hose
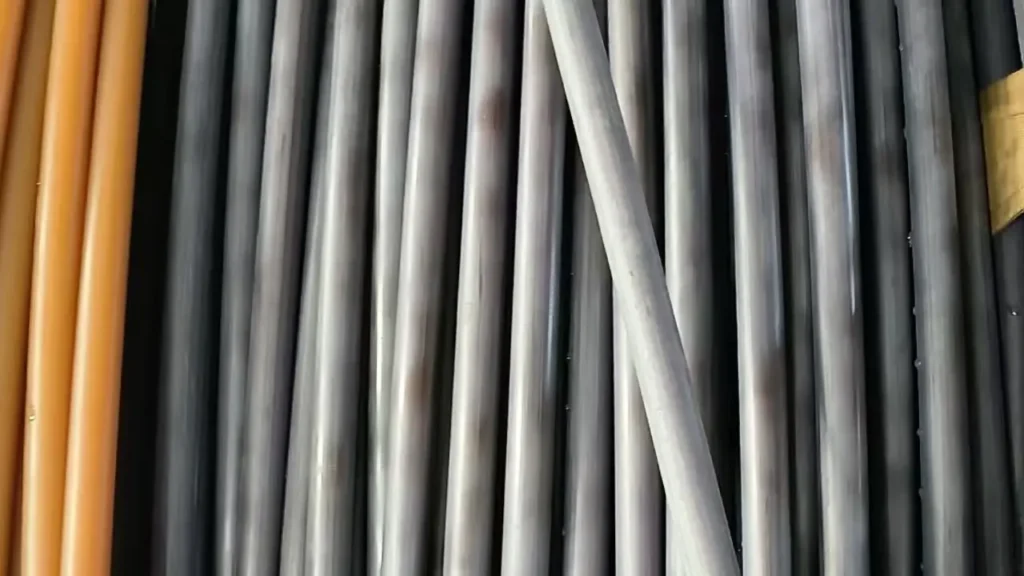
A soft core, also known as a mandrel, is a flexible, slender rod, typically made of polypropylene (PP) plastic. It’s a crucial component in the manufacturing process of hydraulic hoses.
Key Roles of a Soft Core:
- Shape Retention: The soft core provides a stable, cylindrical form around which the rubber or thermoplastic hose material is extruded. This ensures the hose maintains its intended diameter and shape throughout the manufacturing process.
- Smooth Inner Surface: The smooth surface of the soft core transfers to the inner surface of the hose, resulting in a smooth bore. This minimizes friction and improves fluid flow within the hose.
- Easy Extraction: After the hose is cured, the flexible soft core can be easily removed, often through mechanical or hydraulic means. This minimizes the risk of damaging the hose during the extraction process.
By using soft cores, manufacturers can produce high-quality hydraulic hoses with consistent dimensions, smooth inner surfaces, and optimal performance.
What Is Rigid Core for Hydraulic Hose
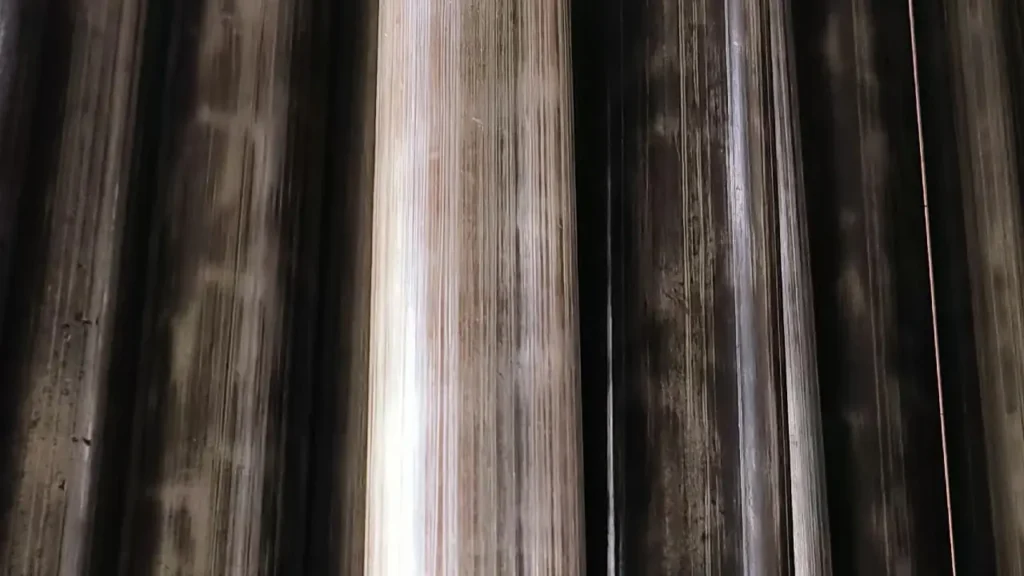
A rigid core, often made of steel, is a type of mandrel used in the manufacturing of hydraulic hoses, particularly larger diameter hoses.
It provides a strong, rigid structure that helps maintain the hose’s shape and integrity during the extrusion and curing processes.
Key characteristics of a rigid core:
- Strength and rigidity: Ideal for high-pressure applications.
- Dimensional stability: Ensures precise control over the hose’s inner diameter.
- Heat resistance: Can withstand high temperatures during the curing process.
Advantages of using a rigid core:
- Improved hose quality: Consistent shape, size, and wall thickness.
- Enhanced performance: Can handle higher pressures and temperatures.
- Increased durability: Offers better resistance to wear and tear.
While rigid cores offer significant advantages, their extraction process can be more complex than that of soft cores. Specialized equipment and techniques are often required to remove the core without damaging the hose.
Soft Core or Rigid Core
When manufacturing hydraulic hoses, the choice between a soft core (often made of polypropylene) and a rigid core (typically made of steel) is a critical decision that significantly impacts the final product’s quality and performance.
Understanding the Differences Between Soft Core and Rigid Core
Feature | Soft Core (PP) | Rigid Core (Steel) |
---|---|---|
Material | Polypropylene | Steel |
Flexibility | Flexible | Rigid |
Diameter Range | Smaller diameters | Larger diameters |
Extraction Method | Mechanical or hydraulic | Mechanical |
Advantages | Easy to extract, smooth inner surface | High strength, precise dimensions |
Disadvantages | May not be suitable for high-pressure applications | Can be more difficult to extract, potential for damage to hose |
How to Choose Soft Core or Rigid Core
The selection of a soft core or a rigid core for your hydraulic hose depends on several factors:
- Smaller Diameters: Soft cores, typically made of polypropylene, are suitable for smaller diameter hoses. Their flexibility allows for easier extraction and reduces the risk of damaging the hose.
- Larger Diameters: Rigid cores, often made of steel, are better suited for larger diameter hoses. They provide the necessary strength and rigidity to maintain the hose’s shape during the manufacturing process.
2. Pressure Rating:
- High-Pressure Hoses: Rigid cores can handle higher pressure applications due to their superior strength and durability.
- Lower-Pressure Hoses: Soft cores are sufficient for lower-pressure applications.
- Both soft and rigid cores can be used for various temperature ranges.
- The specific material and design of the core can influence its temperature resistance.
- The type of rubber or thermoplastic used in the hose can impact the choice of core material and extraction method.
5. Hydraulic Hose Manufacturing Process:
- The extrusion and curing processes can influence the suitability of different core types.
Sum up:
- Soft Cores: Ideal for smaller diameter, lower-pressure hoses. They are easier to extract but may not be suitable for high-temperature or high-pressure applications.
- Rigid Cores: Suitable for larger diameter, high-pressure hoses. They provide excellent dimensional stability and strength but require more complex extraction methods.
By carefully considering these factors, you can select the appropriate core material to ensure the production of high-quality hydraulic hoses that meet your specific application requirements.
Conclusion
The choice between a soft core and a rigid core for your hydraulic hose is a critical decision that significantly impacts the hose’s performance and durability. By carefully considering factors such as hose diameter, pressure rating, temperature requirements, and manufacturing processes, you can select the optimal core material to meet your specific needs.
Need a Custom Hydraulic Hose Solution?
At Kingdaflex, we specialize in providing high-quality, custom hydraulic hoses tailored to your specific requirements. Our experienced team utilizes advanced manufacturing techniques and premium materials to deliver hoses that exceed industry standards.
Contact us today to discuss your project and receive a personalized quote.