Properly tightening hydraulic hose fittings is paramount for the safe and efficient operation of any hydraulic system. Whether you’re assembling a new system or maintaining an existing one, the correct torque applied to each fitting prevents costly leaks, minimizes downtime, and extends the lifespan of your equipment.
This guide will walk you through the essential steps to ensure your hydraulic fittings are tightened accurately. From understanding the nuances of different fitting types to using the right tools and techniques, mastering this skill is key to achieving leak-free performance and avoiding potential hazards associated with improperly secured connections.
How Tight Should Hydraulic Fittings Be?
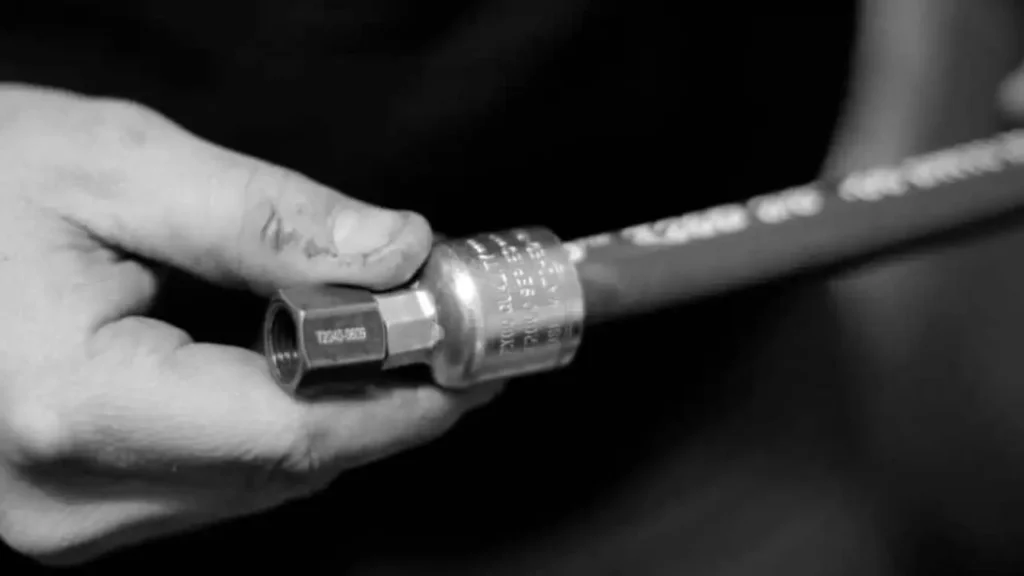
The proper tightness of hydraulic fittings is critical for preventing leaks and ensuring the safe and efficient operation of a hydraulic system. It’s not simply a matter of “as tight as possible”; both under-tightening and over-tightening can lead to catastrophic failures. The correct tightness is achieved when the fitting’s sealing mechanism is fully engaged without causing damage to the threads, body, or sealing components.
This often involves specific torque values or “turns past finger tight” methods, which vary significantly based on the fitting type, size, and material.
- Manufacturer’s Torque Specifications: This is the most reliable and recommended method. Manufacturers provide precise torque values (in ft-lbs or Nm) for their fittings, often in charts specific to the fitting type (e.g., JIC, ORFS, NPT, Metric) and size. Using a calibrated torque wrench to achieve these specifications ensures the optimal balance between a secure seal and avoiding damage.
- “Turns Past Finger Tight” Method: For some fitting types, particularly certain flared or compression fittings, manufacturers may specify a certain number of turns past the point where the fitting is “finger tight.” This method relies on the operator feeling the initial resistance and then applying a precise additional rotation.
- Flats from Wrench Resistance (FFWR): Similar to turns past finger tight, this method involves tightening until wrench resistance is felt, then rotating the nut a specified number of hexagonal “flats” to achieve the final torque. This can be a practical method when a torque wrench is difficult to use.
- Consequences of Under-tightening: Leads to immediate or gradual leaks, loss of hydraulic fluid, reduced system pressure and performance, and potential for air ingress into the system, which can cause cavitation and component damage.
- Consequences of Over-tightening: Can deform or crack the fitting body, strip threads, crush or damage O-rings and other seals, and make future disassembly extremely difficult, ultimately leading to leaks and the need for fitting replacement. It can also put excessive stress on the hose or tubing, leading to premature failure.
How to Tighten Hydraulic Hose Fittings?
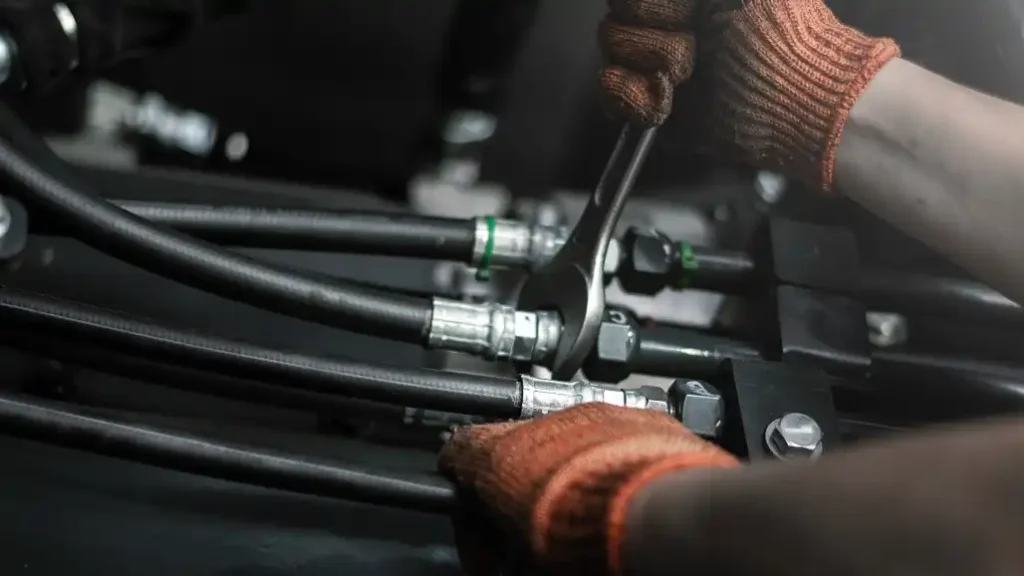
Tightening hydraulic hose fittings properly is crucial for ensuring a secure and leak-proof connection in your hydraulic system.
Here are the two main methods to tight hydraulic hose fittings:
1. Turning (Hand-Tightening):
This method is suitable for low-pressure applications and often used for quick repairs or installations. It manually tightens the fitting until it feels snug against the mating surface.
Here’s how you do for tightening hydraulic fittings:
- Ensure the hose is properly inserted into the fitting and the threads (if applicable) are clean and free of debris.
- Use an appropriate wrench or socket that fits the fitting size securely. Avoid adjustable wrenches, which can damage the fitting or bolts.
- Hand-tighten the fitting by turning the wrench or socket in a clockwise direction. Apply firm but controlled pressure until you feel resistance.
- Do not overtighten! Overtightening can damage the threads, hose, or fitting itself.
2. Torque Wrench Tightening (Recommended for Most Applications):
This method is the preferred approach for most hydraulic systems, especially those operating at high pressures. It ensures a precise and secure connection by applying a specific amount of torque (rotational force) measured in pound-feet (lb-ft) or newton meters (Nm).
Here’s what you’ll need:
- Torque wrench with a calibration certificate (ensures accuracy).
- Socket or wrench that fits the fitting size.
- The manufacturer‘s recommended torque specifications for the specific fitting and hose combination. These are usually found in the manufacturer‘s instructions or data sheets.
Steps to tighten hydraulic hose fittings
- Follow steps 1 and 2 from the turning method (hand-tighten the fitting).
- Set your torque wrench to the recommended torque value for the fitting and hose size. Refer to the manufacturer‘s specifications.
- Hold the fitting body with one wrench (to prevent it from turning) and tighten the nut or connector with the torque wrench in a clockwise direction.
- Once the torque wrench clicks or reaches the set value, stop turning. This indicates the proper tightness has been achieved.
Safety Precautions:
- Pressure relief: Ensure the hydraulic system is depressurized before starting any work on the fittings.
- Proper tools: Use the correct size wrench or socket and a calibrated torque wrench.
- Eye protection: Wear safety glasses to protect your eyes from debris or potential fluid spray during tightening.
Additional Tips:
- Double-check: After tightening, visually inspect the connection for any leaks or loose bolts. Re-tighten if necessary, but never overtighten.
- Don’t use thread sealant for hydraulic hose fittings unless specifically recommended by the manufacturer. Most fittings rely on the mechanical connection for sealing.
- Regular inspections: Regularly inspect your hydraulic system for leaks or loose fittings, especially after initial installation or any maintenance work.
Remember, for critical applications or if you’re unsure about the proper tightening method or torque specifications, consult a qualified hydraulics technician. They can ensure your system is assembled safely and functions optimally.
Choose the Proper Wrenches
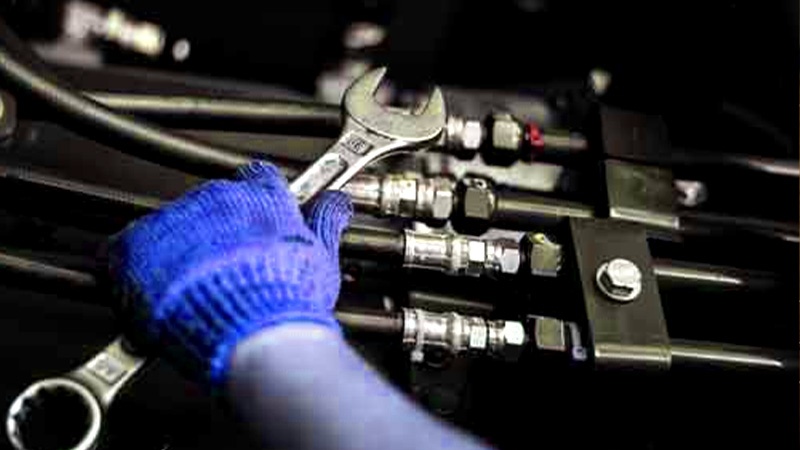
It is basically important to choose the proper wrenches for hydraulic hose fittings while installing hydraulic hoses or fixing hydraulic hoses to the hydraulic system. Use the wrench with the right size. Serious about choosing the wrench the made for working on hydraulics.
If you are not an expert in hydraulic hose assemblies, please don’t be hesitate to ask about the hydraulic hose techniques, they will give you some advice about the hydraulic wrench selection.
Please use the wrench in the right way for your hydraulic hose fittings.
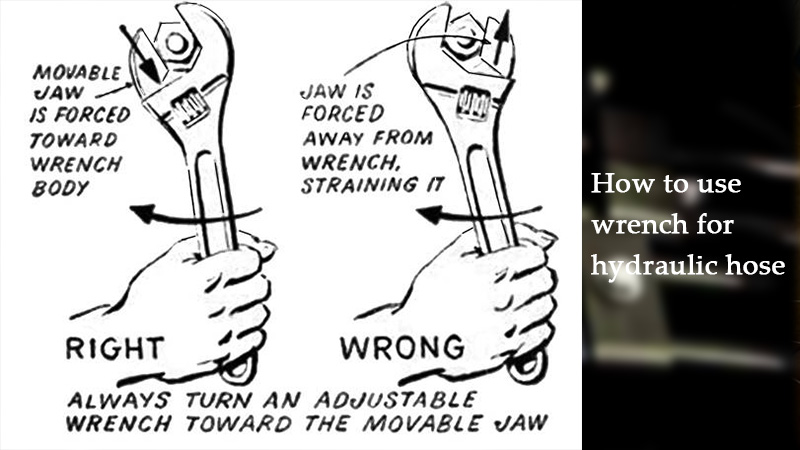
The movable jaw of the wrench is forced toward the wrench body when you need to tighten up the hydraulic hose fittings, don’t hold your wrench in the wrong way. And always turn an adjustable wrench toward the movable haw.
And then try your best to tighten up the hydraulic hose fittings, until you feel so hard to turn the wrench. The hydraulic hose will be stuck well by the hydraulic hose fittings.
Don’t Skive Too Much
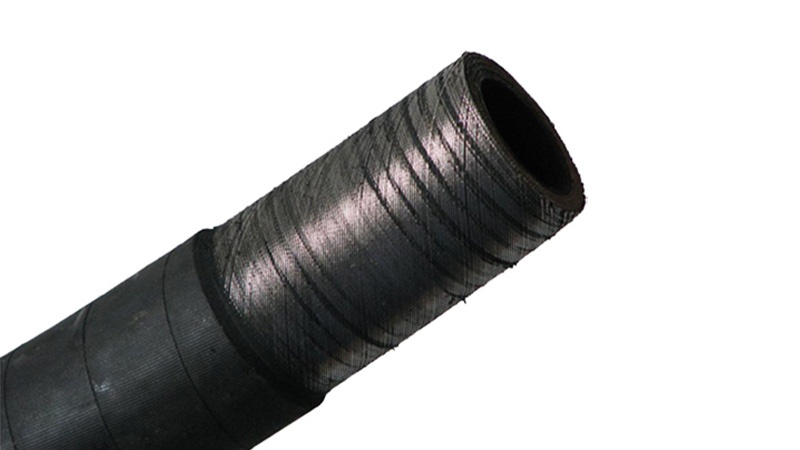
Before hydraulic hose assemblies, you also need to skive the hydraulic hose. You need to use the hydraulic hose skiving tool to skive the cover of the hydraulic hose, to make it much easier to match the size of the hydraulic hose fittings. Skiving hydraulic hose is to reduce the diameter of the hydraulic hose to make it much easier to connect the hydraulic hose fittings.
If you don’t want to loosen hydraulic hose fittings, please don’t skive too much to make it much thinner. Skive hydraulic hose and no skive hydraulic hose, you can choose the most suitable one for your hydraulic system.
Here is the video showing you the process of hydraulic hose skiving.
Skive the hydraulic hose cover to better fit the hydraulic hose fitting connection.
Skiving is to remove the outer cover at the end of a hydraulic hose in the location of the crimp fitting before the hydraulic hose crimping process.
For some high-pressure applications, the hydraulic hose’s inner diameter may be skived to allow the hose tail to be a better fit.
Using a specialized machine with externally rotating mandrels, the tooling cuts and then peels the outer carcass. Depending on the hydraulic hose skiving machine, the skiving process may take 30, 40 seconds.
Crimping Hydraulic Hose
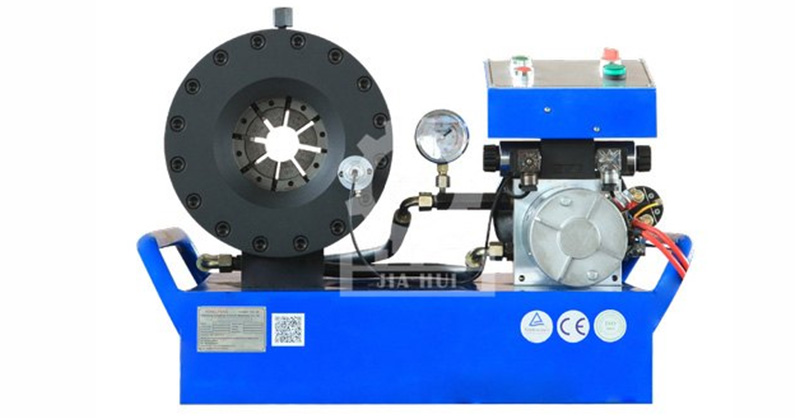
Then next please pay attention to the hydraulic hose crimping process, and you need to use the right hydraulic hose crimper dies to fit the hydraulic hose. The proper hydraulic hose dies of the hydraulic hose crimping machine can be used to tighten the hydraulic hose well.
Here is the hydraulic hose crimping process.
If you have any other questions bout the hydraulic hose crimping, please be free to contact us at any time.
How to Loosen Hydraulic Hose Fittings
To loosen hydraulic hose fittings, follow these steps:
- Turn off the hydraulic system: Before working on hydraulic hose fittings, ensure that the hydraulic system is turned off and the pressure is released. This step is crucial to prevent any accidental movement or release of pressurized hydraulic fluid.
- Use a wrench or spanner: Select an appropriately sized wrench or spanner that fits the fitting you want to loosen. Most hydraulic fittings have flats or hexagonal shapes, which allow you to grip them securely.
- Apply penetrating oil: If the hydraulic fitting is stuck or difficult to loosen, you can apply a penetrating oil or lubricant to the fitting. Let it sit for a few minutes to allow the oil to penetrate and loosen any corrosion or rust.
- Position the wrench: Position the wrench on the flats or hexagonal portion of the fitting. Ensure that the wrench is fully engaged and properly aligned to prevent slippage or damage to the fitting.
- Turn counterclockwise: Apply steady and gradual force in a counterclockwise direction to loosen the fitting. Avoid applying excessive force, as it may damage the fitting or cause it to break.
- Use leverage: If the fitting is still difficult to loosen, you can use a longer wrench or a pipe extension to increase the leverage. Be cautious when using additional leverage, as it may require more force to control and could cause injury if not handled properly.
- Check for movement: As you apply force, check for any movement or loosening of the fitting. If you feel the fitting starting to turn, continue turning it counterclockwise until it is fully loosened.
- Inspect the fitting: Once the fitting is loosened, inspect it for any damage or wear. If the fitting is damaged or shows signs of excessive wear, it may need to be replaced.
It’s important to exercise caution when loosening hydraulic hose fittings, as they can be under pressure or contain residual hydraulic fluid. If you encounter any difficulties or are uncertain about the process, it is recommended to consult a professional hydraulic technician for assistance.
Conclusion
Properly tightening hydraulic hose fittings is crucial for preventing leaks and ensuring system integrity. By understanding the correct torque specifications and using the right tools, you can establish secure, reliable connections that withstand operational demands. This precision in tightening extends the lifespan of your hydraulic components.
Avoid overtightening, which can damage threads and seals, or undertightening, which leads to immediate leaks. Following manufacturer guidelines and employing a torque wrench are best practices that guarantee optimal performance and enhance the safety of your hydraulic systems.
For all your hydraulic fitting needs, look no further. We supply a wide range of wholesale hydraulic fittings, ensuring you have the high-quality components necessary to achieve perfectly tightened, leak-free connections every time.