Well, when it comes to hydraulic hoses, it’s what’s on the outside that can make all the difference. Dive in with me, and let’s unravel the world of hydraulic hose insulation.
Introduction to Hydraulic Hoses
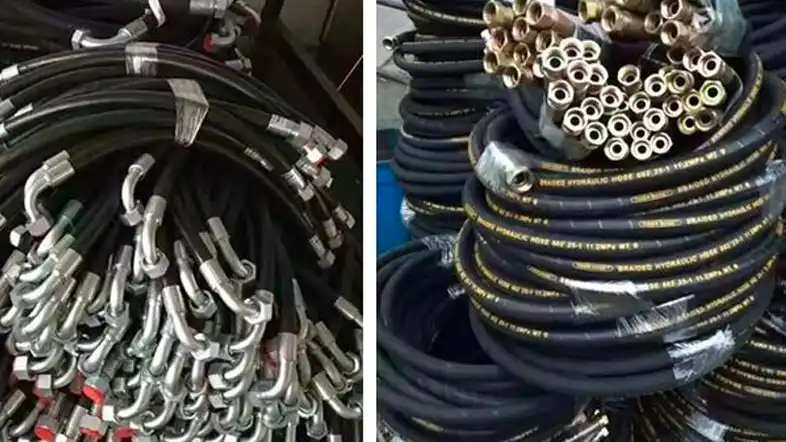
In the intricate web of machinery and systems, there lies a silent facilitator called the hydraulic hose. At its core, a hydraulic hose is a high-pressure tube designed to transport fluid within hydraulic machinery. Think of it as the veins of a machine, ensuring that hydraulic fluid flows seamlessly, powering different parts of the system.
Originating from the field of fluid mechanics, the concept behind hydraulic hoses revolves around Pascal’s Law. This law stipulates that pressure applied at any point in a confined fluid is transmitted undiminished throughout the fluid in all directions. Essentially, by applying pressure, hydraulic hoses allow machinery to perform powerful tasks, like lifting heavy objects or operating intricate components.
Constructed primarily from rubber, thermoplastics, or Teflon, these hoses are designed to handle the immense pressure and to be flexible. This flexibility ensures that they can be routed through tight spaces and around obstacles, ensuring that machinery can be designed for efficiency and functionality.
Over the years, as machinery has evolved, so has the complexity and importance of hydraulic hoses. They come in various sizes, pressure ratings, and even temperature capacities, catering to diverse industrial needs. From construction equipment like bulldozers and cranes to simpler mechanisms like car brakes, these hoses play a pivotal role in ensuring systems operate flawlessly.
However, with the power of transporting hydraulic fluids comes the responsibility of maintenance. A small rupture or leak in a hydraulic hose can lead to malfunctioning machinery, or worse, accidents. Therefore, regular inspection and timely replacement are crucial for safe operations.
In essence, while they might seem like just another component in a machine, hydraulic hoses are fundamental to the optimal functioning of many systems. Their silent yet significant role ensures that our world, dominated by machinery and equipment, runs smoothly and efficiently.
Importance of Hydraulic Hoses
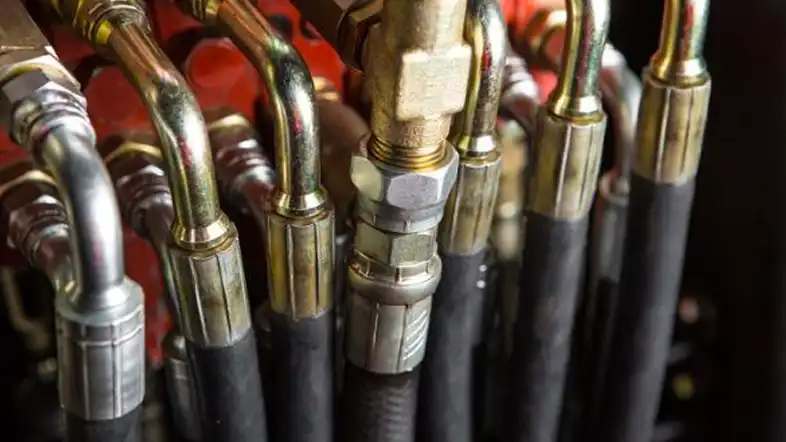
When you look at the vast expanse of industries and machines around us, hydraulic hoses might seem like minor players. However, akin to our circulatory system’s blood vessels, these hoses play a pivotal, often understated role. Let’s delve into why they’re so important.
Power Transmission:
The primary function of a hydraulic hose is to transmit power. Hydraulic systems harness the power of pressurized liquids, and hoses are the channels through which this liquid flows. The force generated by the fluid movement enables heavy machinery to lift, push, pull, and perform tasks that would be impossible with manual labor.
Flexibility & Adaptability:
Unlike rigid pipes, hydraulic hoses are flexible. This malleability allows them to be routed around corners, through tight spaces, and across movable parts of machinery. This means designers and engineers have greater freedom when creating machinery, making them more efficient and compact.
Safety:
Hydraulic hoses play a crucial role in safety. With the right material and construction, they ensure that pressurized hydraulic fluids stay contained, preventing spills and potential accidents. Furthermore, they’re designed to withstand high temperatures, reducing the risk of fires or explosions.
Versatility:
Different machinery requires hydraulic hoses with varying specifications, be it pressure capacity, temperature tolerance, or size. The vast array of hydraulic hoses available ensures that they cater to a broad spectrum of applications, from heavy-duty construction machinery to precision medical equipment.
Cost-Efficiency:
Hydraulic systems, facilitated by hoses, often provide a more cost-effective solution for power transmission compared to electrical or mechanical systems. They require less maintenance, have fewer moving parts, and offer higher power density.
Diverse Applications:
Beyond industrial machinery, hydraulic hoses are used in a multitude of applications. Car brakes, aircraft flight control systems, elevators, and even theme park rides rely on these hoses to function efficiently and safely.
Environmental Protection:
By containing and directing the flow of hydraulic fluids, these hoses prevent potential leaks and spills, which can be detrimental to the environment. In industries where environmental contaminants can be a concern, the integrity of hydraulic hoses is paramount.
What is Hydraulic Hose Insulation?
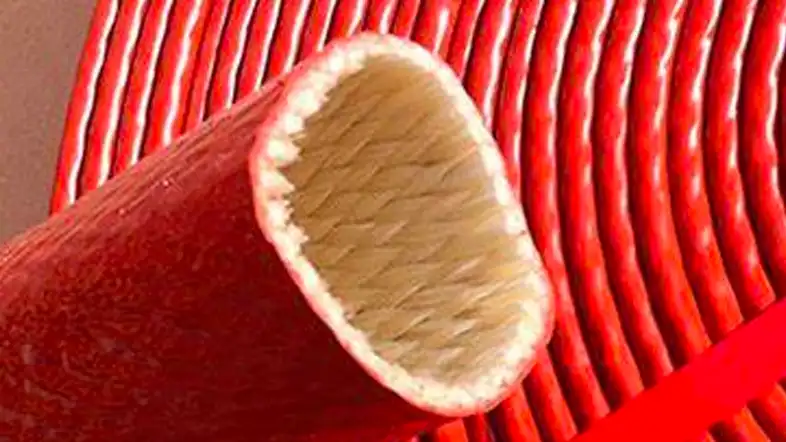
Hydraulic hose insulation refers to protective coverings or layers added to hydraulic hoses to shield them from external factors, ensuring optimal functionality and longevity.
These coverings can range from protective sleeves, wraps, or specialized coatings, all designed to protect the hose and the fluid within from temperature extremes, potential electrical interference, or physical damage.
Hydraulic Hose Insulation Purpose & Benefits
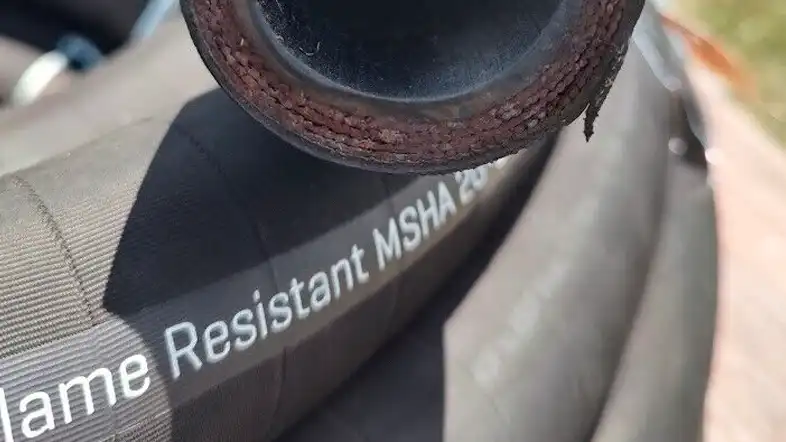
Temperature Regulation:
Hydraulic fluids have optimal operating temperatures. Insulation ensures that the fluid remains within this range, regardless of external conditions. Whether it’s the scorching heat of an industrial furnace or the freezing conditions of a snowy construction site, insulation ensures that the hydraulic fluid doesn’t overheat or freeze.
Protection Against Physical Damage:
Hoses often run through tight spaces or close to moving parts, which can lead to abrasion or punctures. Insulated protective sleeves act as a buffer, shielding hoses from such potential damage.
Electrical Insulation:
In environments where electrical currents might be present, it’s crucial to ensure that these currents don’t interfere with the hydraulic fluid. Certain insulations can protect hoses from such interference, ensuring that operations continue without electrical disruptions.
Enhanced Durability & Longevity:
With proper insulation, hydraulic hoses are less likely to deteriorate quickly. This means fewer replacements, less downtime, and cost savings in the long run.
Safety:
A malfunctioning hydraulic hose can be hazardous. By protecting them with appropriate insulation, the chances of bursts, leaks, or other malfunctions are significantly reduced.
Types of Hydraulic Hose Insulation
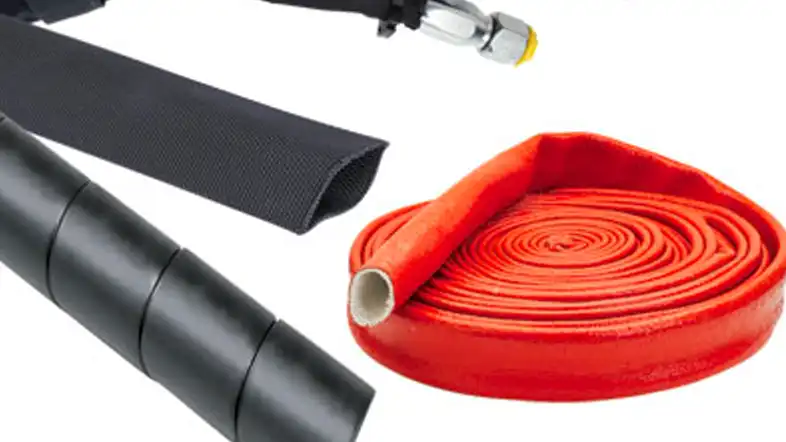
Hydraulic hose insulation isn’t a one-size-fits-all solution. Depending on the specific challenges and needs of an application, various insulation types are employed to safeguard these vital components. Let’s delve into the most common types:
Thermal Insulation:
- Purpose: As the name suggests, thermal insulation is designed to regulate the temperature of the fluid within the hydraulic hose.
- Material: Often made from materials with low thermal conductivity, such as fiberglass, silicone, or foamed plastics.
- Applications: Ideal for environments with extreme temperatures, whether they’re very hot (like near industrial furnaces) or very cold (like in Arctic oil drilling operations).
- Benefits: Helps prevent the hydraulic fluid from overheating or freezing, ensuring consistent flow and reducing the risk of hose damage due to temperature extremes.
Electrical Insulation:
- Purpose: Protects the hydraulic hose from electrical interference or surges.
- Material: Typically made of non-conductive materials like rubber or specific plastics designed to prevent the transfer of electricity.
- Applications: Essential in environments with strong electromagnetic fields or where electrical equipment is prevalent, like in some manufacturing units or near power lines.
- Benefits: Ensures that electrical currents don’t interfere with the hydraulic fluid’s operation, thereby preventing potential malfunctions or hazards.
Abrasion-Resistant Insulation:
- Purpose: Provides a protective layer against physical wear and tear.
- Material: Constructed from tough materials like polyurethane, nylon, or dense rubber.
- Applications: Especially valuable in environments where the hose might rub against other surfaces or components, such as in mobile machinery or construction equipment.
- Benefits: Extends the lifespan of the hose by reducing the wear and tear from continuous movement or contact with abrasive surfaces.
Protective Sleeves:
- Purpose: Shields the hose from various external threats like cuts, crushes, or abrasions.
- Material: Often made from woven materials or dense plastics that can wrap around or envelope the hose.
- Applications: Useful in almost any setting but particularly in places with a lot of moving parts or sharp objects.
- Benefits: Offers a flexible protective layer, making it easier to install and replace as needed.
Fire-Resistant Insulation:
- Purpose: Designed to protect hydraulic hoses from open flames or extreme heat.
- Material: Composed of materials that can resist combustion, such as silicone-coated fiberglass or other specialized composites.
- Applications: Critical in sectors like welding, steel manufacturing, or any environment where open flames or high heat are prevalent.
- Benefits: Prevents the hose and the fluid inside from catching fire, ensuring safe operations and minimizing potential damages.
Just as a knight selects the right armor for battle, choosing the right insulation type for a hydraulic hose ensures that it stands up to the challenges of its environment. Whether facing temperature extremes, electrical fields, or physical threats, the proper insulation guarantees that hydraulic hoses continue to operate efficiently and safely.
Installation and Maintenance Tips
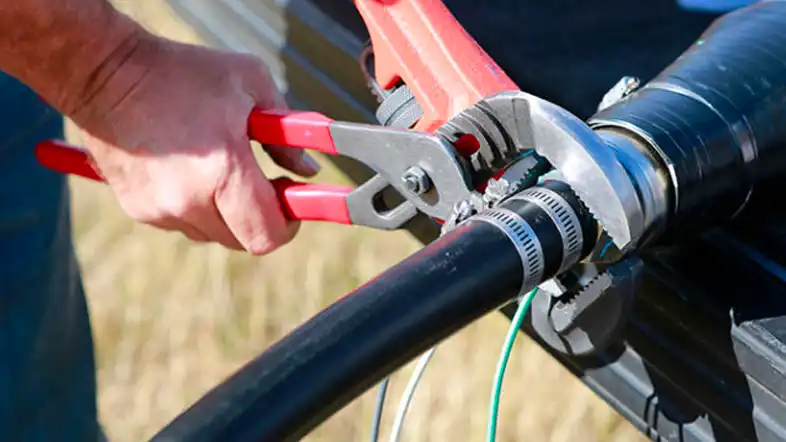
Regular Inspections: Incorporate routine checks into your maintenance schedule. Look for signs of wear, like abrasions, cracks, or leaks. Pay attention to fittings and ensure they’re still tight and leak-free.
Replace Aged Hoses: Over time, even the best hydraulic hoses will wear out. If you notice the outer cover becoming brittle or excessively worn, consider a hydraulic hose replacement.
Monitor Temperature: Extremely high temperatures can degrade hoses quickly. If a hose feels too hot to touch, it might be operating beyond its recommended temperature range. Consider insulation or rerouting to address the issue.
Stay Within Pressure Limits: Continually operating at the upper pressure limits can reduce a hose’s lifespan. Ensure your system’s pressure is within the hose’s specified range. Hydraulic Hose Pressure Rating: Working Pressure Vs Bursting Pressure
Clean the System: Contaminants can significantly impair a hydraulic hose’s performance. Regularly flush and clean the system to get rid of any foreign particles. How to Clean Hydraulic Hoses Effectively for Hydraulic Hose Maintanance
Track Hose Lifespan: Keep a record of when each hose was installed. Even if there’s no visible wear, hoses have a shelf life and should be replaced after a specific period, especially in high-demand applications.
Use Protective Sleeves: If a hose is in a particularly abrasive environment, consider adding protective sleeves or guards to shield it from potential damage.
Installing and maintaining hydraulic hoses might seem like a daunting task, but with a bit of diligence and attention to detail, it’s entirely manageable.
By ensuring proper installation and committing to regular maintenance, you not only extend the life of your hydraulic hoses but also ensure the safety and efficiency of the entire hydraulic system. Remember, a little effort in care can save a lot in potential downtime and repair costs down the road.
Conclusion
Hydraulic hose insulation might seem like a small detail, but it’s a game-changer in ensuring efficiency, safety, and longevity. So, next time you come across a hydraulic hose, remember: it’s not just what’s inside but also what’s on the outside that counts.
FAQs
Why is hydraulic hose insulation essential?
Insulation ensures temperature regulation, enhances durability, and promotes safety.
How often should I check my hydraulic hose insulation?
Regular inspections, preferably every few months, are ideal.
What are the main types of hydraulic hose insulation?
The primary ones are thermal and electrical insulation.
Can I install insulation on my old hydraulic hoses?
Absolutely! However, ensure the hoses are in good condition before insulation.
How long does hydraulic hose insulation last?
With proper care, insulation can last for several years, depending on the type and environmental conditions.