Hydraulic hose pressure drop is the loss of fluid pressure as it travels through a hose, impacting system efficiency. This occurs due to friction between the fluid and hose walls, influenced by factors like hose length, diameter, and fluid viscosity.
Understanding pressure drop is crucial for optimizing hydraulic systems. Excessive drop reduces power and speed, potentially causing system failure. Analyzing these factors allows for proper hose selection and maintenance, ensuring optimal performance.
What Is Hydraulic Hose Pressure Drop
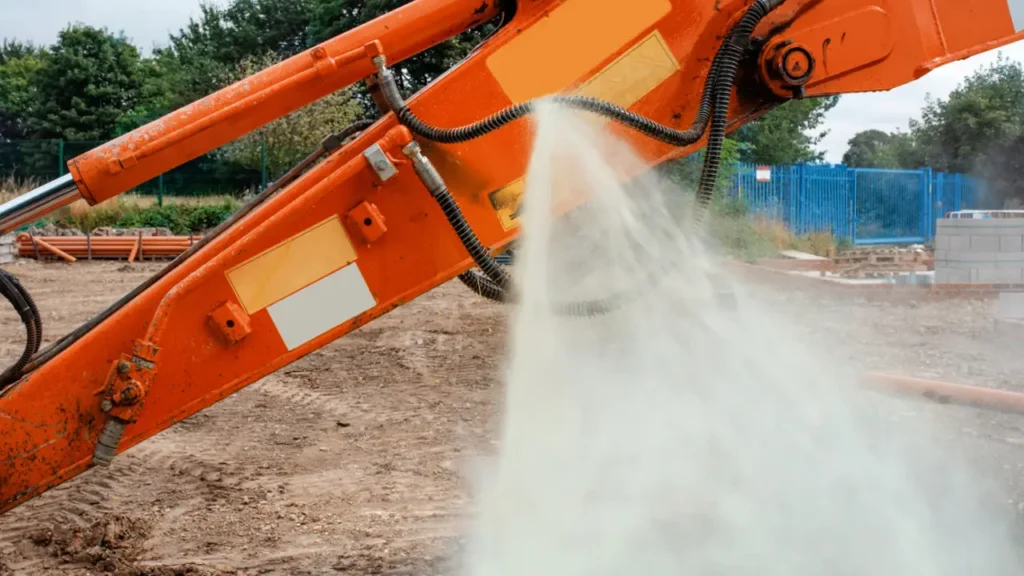
Hydraulic hose pressure drop refers to the reduction in fluid pressure that occurs as hydraulic fluid flows through a hose. This pressure loss is a natural phenomenon caused by friction between the fluid and the inner walls of the hose.
Essentially, it’s the difference between the pressure of the fluid entering the hose and the pressure of the fluid exiting it.
Several factors influence the amount of pressure drop, including:
- Hose Length and Diameter: Longer hoses and smaller diameters increase friction, resulting in a greater pressure drop.
- Fluid Viscosity: Thicker fluids (higher viscosity) experience more resistance to flow, leading to higher pressure drops.
- Flow Rate: Higher flow rates increase the speed of the fluid, which in turn increases friction and pressure drop.
- Hose internal surface roughness: the rougher the internal surface is the more friction will occur.
Importance of Hydraulic Pressure Drop
Understanding and managing hydraulic pressure drop is crucial for optimizing the performance and longevity of hydraulic systems. Excessive pressure drop can lead to significant energy losses, as the system must work harder to maintain the required fluid flow and pressure. This results in increased fuel consumption or electricity usage, directly impacting operational costs and environmental footprint.
Furthermore, uncontrolled pressure drop can cause a range of operational issues. Reduced system efficiency translates to slower cycle times, decreased power output, and inconsistent performance. In critical applications, this can lead to production delays or even system failures. Additionally, the increased strain on components due to higher operating pressures can accelerate wear and tear, requiring more frequent maintenance and replacements.
Ultimately, proper consideration of hydraulic pressure drop during system design and maintenance is essential for ensuring efficient, reliable, and cost-effective operation. By selecting the right hoses, minimizing restrictions, and optimizing fluid flow, engineers can significantly reduce pressure drop and maximize the overall performance and lifespan of their hydraulic systems.
Reasons Causing Pressure Drop in Hydraulic Systems
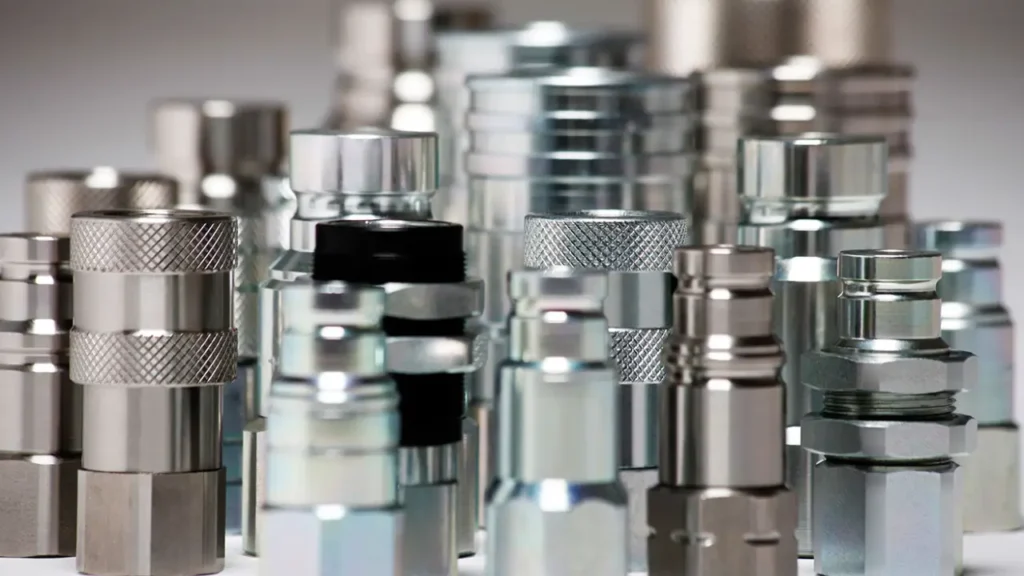
What are the reasons causing pressure drop in hydraulic systems?
Pressure drop in hydraulic systems is an unavoidable consequence of fluid flow. Understanding its causes is vital for optimizing system efficiency and preventing performance issues.
Here are the three some reasons why hydraulic hose pressure drop occurs:
Friction: This is the primary cause, arising from the interaction between the hydraulic fluid and the inner walls of hoses or pipes. Factors like hose length, diameter, internal roughness, and fluid viscosity directly influence the amount of friction and, consequently, the pressure drop.
Restrictions: Any obstruction that impedes the smooth flow of fluid contributes to pressure drop. This includes fittings, bends, valves, and contamination within the system. Sharp bends and undersized fittings create particularly significant resistance.
Flow Rate: The velocity of the fluid directly impacts pressure drop. Higher flow rates increase velocity, leading to increased friction and resistance. Exceeding the system’s design flow capacity can result in a substantial pressure drop.
Factors Affecting Hydraulic Pressure Drop
Delving deeper into the factors affecting hydraulic pressure drop reveals a complex interplay of fluid dynamics and system design.
Here’s a more comprehensive look:
Hose Length and Diameter: The Foundation of Friction:
- Length: As hydraulic fluid travels through a hose, it encounters frictional resistance along the entire length. A longer hose provides more surface area for this friction to occur, leading to a proportionally higher pressure drop. This is a linear relationship; doubling the hose length roughly doubles the pressure drop, assuming other factors remain constant.
- Diameter: The hose’s internal diameter significantly impacts flow velocity and, consequently, friction. A smaller diameter forces the fluid to move faster, increasing the shear stress between the fluid layers and the hose wall. This relationship is not linear; a small reduction in diameter can result in a disproportionately large increase in pressure drop.
Fluid Viscosity: The Resistance to Flow:
- Viscosity: This property describes a fluid’s resistance to flow. High-viscosity fluids, like thick oils, experience greater internal friction, requiring more energy to move. This translates directly to increased pressure drop.
- Temperature Dependence: Viscosity is highly sensitive to temperature. As temperature increases, viscosity decreases, and vice versa. Therefore, changes in ambient or operating temperatures can significantly alter pressure drop. This is especially important in systems subject to wide temperature variations.
Flow Rate: Velocity and Turbulence:
- Flow Rate: The volume of fluid moving through the hose per unit of time. Higher flow rates necessitate higher fluid velocities.
- Turbulence: Increased velocity can transition laminar flow (smooth, layered flow) to turbulent flow (chaotic, irregular flow). Turbulent flow generates significantly more friction and, thus, pressure drop. The Reynolds number is used to predict the change between these two types of flow.
Hose Internal Roughness: Surface Irregularities:
- Surface Finish: The smoothness of the hose’s inner wall directly affects friction. Even microscopic imperfections can create turbulence and increase resistance.
- Material and Manufacturing: Hose materials and manufacturing processes influence internal roughness. Rubber hoses, for instance, may have different surface finishes than PTFE hoses.
Fittings and Bends: Localized Resistance:
- Fittings: Connectors, adapters, and other fittings create restrictions and changes in flow direction, leading to localized pressure drops. The design and size of these fittings are critical.
- Bends: Bends in the hose disrupt smooth flow, creating turbulence and increasing resistance. Sharp bends are particularly problematic, as they force the fluid to change direction abruptly.
Component Restrictions: System-Wide Impact:
- Valves: Control valves, including directional control valves and pressure relief valves, introduce restrictions to regulate flow and pressure.
- Filters: Filters are essential for removing contaminants but also contribute to pressure drop. The filter’s efficiency and cleanliness influence the amount of pressure drop.
- Pumps: Pumps themselves create a pressure drop on their suction side.
Contamination: Unintended Obstructions:
- Particles and Debris: Contaminants in the hydraulic fluid can accumulate in hoses, fittings, and components, creating obstructions and increasing resistance.
- Fluid Degradation: Degraded hydraulic fluid can form sludge and varnish, which can coat internal surfaces and restrict flow.
- Air Inclusion: Air bubbles in the hydraulic fluid are compressible, and disrupt the flow of the non compressible hydraulic fluid, changing the systems pressure.
How Can You Determine the Amount of Pressure Drop
Determining the amount of pressure drop in a hydraulic system involves a combination of theoretical calculations and practical considerations. Here are the key methods to determine the hydraulic hose pressure drop
1. Theoretical Calculations:
Formulas:
Engineers use established hydraulic formulas, often involving the Darcy-Weisbach equation, to calculate pressure drop. These formulas take into account factors like:
- Fluid viscosity
- Fluid flow rate
- Hose length and diameter
- Hose internal roughness
- Calculating the Reynolds number is also important to determine if the flow is laminar or turbulent, as this affects the friction factor used in pressure drop calculations.
Calculators and Software:
Many online calculators and specialized hydraulic software tools are available to simplify these complex calculations. These tools often allow users to input specific system parameters and generate accurate pressure drop estimates.
2. Practical Considerations:
Manufacturer’s Data:
- Hydraulic hose manufacturers often provide pressure drop data for their products, which can be used as a reference.
Testing:
In critical applications, actual pressure drop measurements may be taken using pressure gauges at various points in the hydraulic system. This provides real-world data to validate theoretical calculations.
Factors that complicate calculations:
- Fittings and Bends: pressure drop is also increased by the use of fittings and bends in the hydraulic system.
- Temperature: Fluid viscosity is effected by temperature, therefore changes in temperature will change the pressure drop.
In essence, determining pressure drop requires a blend of theoretical analysis and practical observation to ensure accurate and reliable results.
How to Measure Hydraulic Hose Pressure Drop
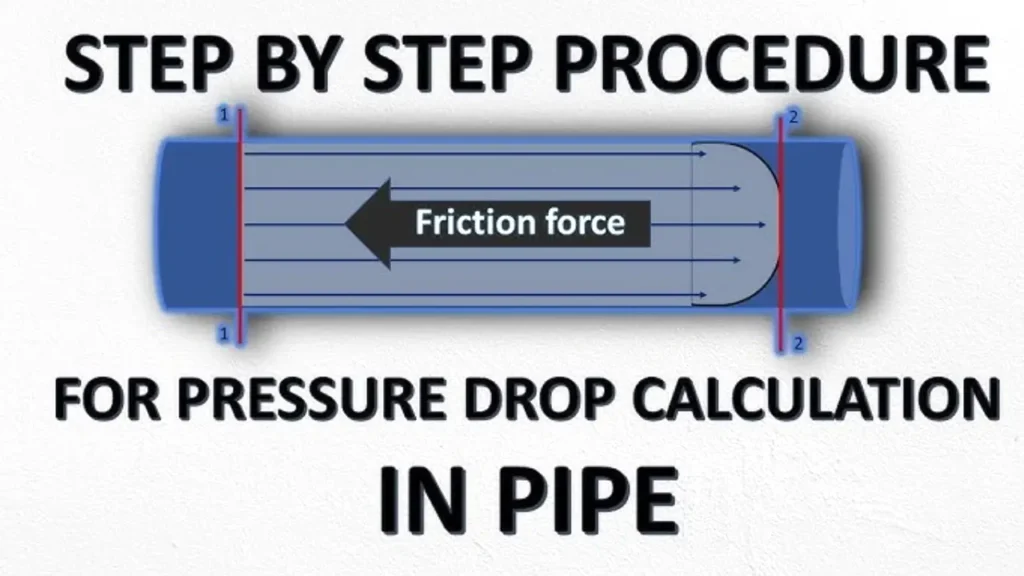
Accurately measuring hydraulic hose pressure drop is essential for diagnosing system inefficiencies. This step-by-step guide outlines the process, ensuring precise readings and effective troubleshooting. Here’s how to do it:
Step 1: Prepare the Hydraulic System and Equipment
Before measuring hydraulic hose pressure drop, ensure the system is operating under typical working conditions. This involves bringing the system up to its normal operating temperature and pressure, allowing the hydraulic fluid to stabilize. Verify that the fluid level is adequate and that there are no visible leaks or signs of damage to the hoses or components. Additionally, ensure the system is in a safe condition for testing, isolating any potential hazards.
Gather the necessary measurement tools, including two calibrated pressure gauges, ideally with ranges that encompass the expected pressure drop. Select gauges with appropriate accuracy for the system’s operating pressures. Prepare any required adapters or fittings to connect the gauges to the system at the desired measurement points. Ensure that all measurement equipment is clean and in good working order to prevent contamination or inaccurate readings.
Step 2: Identify Measurement Points and Install Pressure Gauges
Select two appropriate measurement points along the hydraulic hose where you want to determine the pressure drop. The first point should be located as close as possible to the hose’s inlet, and the second point should be near the hose’s outlet. These points should ideally be at locations where pressure taps or ports are already available. If not, you may need to install temporary T-fittings or adapters to accommodate the pressure gauges.
Install the pressure gauges at the chosen measurement points, ensuring they are securely connected and properly sealed to prevent leaks. The gauges should be positioned to allow for easy reading and observation. Take care to avoid introducing air into the system during installation. If using threaded connections, apply thread sealant to prevent leaks. Once the gauges are installed, double-check all connections for tightness and stability.
Step 3: Operate the System and Record Pressure Readings
With the system operating at its normal conditions, allow the fluid to stabilize and the pressure readings to settle. Carefully observe and record the pressure readings from both gauges simultaneously. Ensure that the readings are taken under steady-state conditions, avoiding any transient pressure fluctuations. Take multiple readings over a short period to ensure consistency and accuracy.
Record the pressure readings from both gauges, noting the units of measurement (e.g., PSI, bar, kPa). It is crucial to record the readings at the exact same moment to obtain an accurate pressure drop measurement. If the system experiences fluctuations, you may need to average multiple readings or use a data logger to capture pressure trends over time. Document the system’s operating conditions, including fluid temperature, flow rate, and any other relevant parameters.
Step 4: Calculate and Analyze the Pressure Drop
Calculate the pressure drop by subtracting the pressure reading at the outlet (second gauge) from the pressure reading at the inlet (first gauge). The resulting value represents the pressure loss across the hydraulic hose. Ensure that the pressure readings are in the same units before performing the subtraction.
Analyze the calculated pressure drop in relation to the system’s design specifications and operating requirements. Compare the measured pressure drop to manufacturer’s specifications or industry standards. If the pressure drop exceeds acceptable limits, investigate potential causes, such as hose restrictions, fluid viscosity issues, or excessive flow rates. Consider adjusting system parameters or replacing components as needed to optimize performance and minimize pressure loss.
Significance of Pressure Drop in Hydraulic Applications
The significance of pressure drop in hydraulic applications cannot be overstated, as it directly impacts system efficiency, performance, and longevity. An excessive pressure drop indicates a loss of energy, meaning the system requires more power to achieve the desired output. This translates to increased operational costs, whether through higher fuel consumption in mobile machinery or increased electricity usage in industrial settings. Moreover, it can lead to reduced system responsiveness and slower cycle times, negatively affecting productivity.
Beyond energy consumption, pressure drop also plays a crucial role in component health. High pressure drops can create localized stress and heat buildup within the hydraulic system, accelerating wear and tear on hoses, pumps, valves, and other critical components. This can lead to premature failures, costly downtime, and increased maintenance requirements. In applications where precision and consistency are paramount, such as in aerospace or manufacturing, even small pressure drops can compromise performance and product quality. Therefore, careful consideration of pressure drop during system design, maintenance, and troubleshooting is essential to ensure optimal performance and minimize operational costs.
How to Calculate Hydraulic Hose Pressure Drop
Accurately calculating hydraulic hose pressure drop is vital for system optimization. This step-by-step guide simplifies the process, ensuring precise results for effective design and troubleshooting.
Step 1: Gather Necessary Information
Before calculating pressure drop, you’ll need specific data about your hydraulic system. This includes:
- Hose length (L) in meters or feet.
- Hose internal diameter (D) in meters or inches.
- Fluid flow rate (Q) in liters per minute (LPM), gallons per minute (GPM), or cubic meters per second (m³/s).
- Fluid viscosity (ν) in centistokes (cSt) or square meters per second (m²/s).
- Fluid density (ρ) in kilograms per cubic meter (kg/m³) or pounds per cubic foot (lb/ft³).
- Hose internal roughness (ε) in meters or inches.
- The type of flow (laminar or turbulent).
Step 2: Determine the Reynolds Number (Re)
The Reynolds number helps determine if the flow is laminar or turbulent, which affects the friction factor used in pressure drop calculations. Calculate Re using the following hydraulic pressure drop formula:
Re = (ρ * V * D) / μ, where:
- V is the fluid velocity (m/s or ft/s).
- μ is the dynamic viscosity (Pa·s or lb·s/ft²).
- V can be calculated by V = Q / A, where A is the cross-sectional area of the hose.
- μ can be obtained from the kinematic viscosity (ν) by μ = ν * ρ.
If Re < 2300, the flow is laminar.
If Re > 4000, the flow is turbulent.
If 2300 < Re < 4000, the flow is in the transition region.
Step 3: Determine the Friction Factor (f)
The friction factor depends on the Reynolds number and the hose’s internal roughness.
Laminar Flow (Re < 2300):
- f = 64 / Re
Turbulent Flow (Re > 4000):
Use the Darcy-Weisbach equation or the Colebrook-White equation to find the friction factor. The Colebrook-White equation is an implicit equation, often solved iteratively or with online calculators:
1 / √f = -2 * log10 (ε / (3.7 * D) + 2.51 / (Re * √f))
For commercial steel pipes, empirical equations or Moody charts are often used.
Step 4: Calculate the Pressure Drop (ΔP)
Use the Darcy-Weisbach equation to calculate the pressure drop:
ΔP = f * (L / D) * (ρ * V² / 2), where:
- ΔP is the pressure drop (Pa or psi).
- f is the friction factor.
- L is the hose length.
- D is the hose internal diameter.
- ρ is the fluid density.
- V is the fluid velocity.
Step 5: Convert Units (If Necessary)
Ensure that all units are consistent before performing the calculations. If necessary, convert units to the desired system (e.g., SI or imperial). The resulting pressure drop will be in the units corresponding to the units used in the calculations.
Conclusion
Understanding hydraulic hose pressure drop is crucial for optimizing system efficiency and preventing premature component wear. Factors like hose length, diameter, fluid viscosity, and flow rate significantly impact pressure loss. Accurately calculating and minimizing this drop ensures consistent power delivery and reliable operation. Neglecting pressure drop can lead to reduced system performance and costly downtime.
Accurate pressure drop analysis allows for precise hose selection, maximizing the lifespan and effectiveness of your hydraulic systems. By considering these principles, you can ensure your machinery operates at peak performance, minimizing energy waste and maximizing productivity.
For high-quality, wholesale hydraulic hoses designed to minimize pressure drop and maximize your system’s efficiency, contact Kingdaflex today. Get the perfect hoses for your needs and ensure reliable, long-lasting hydraulic performance.