When it comes to hydraulic hose manufacturing, rubber, as the raw material is the basic important part for us to learn.
The hydraulic hose is made of synthetic rubber material, (Our hydraulic hose manufacturer resource the synthetic sheet to get preparations for making hydraulic hose) the and there are many different rubber types in the industry, and in this ultimate guide, let’s talk about the rubber types.
What Is Rubber?
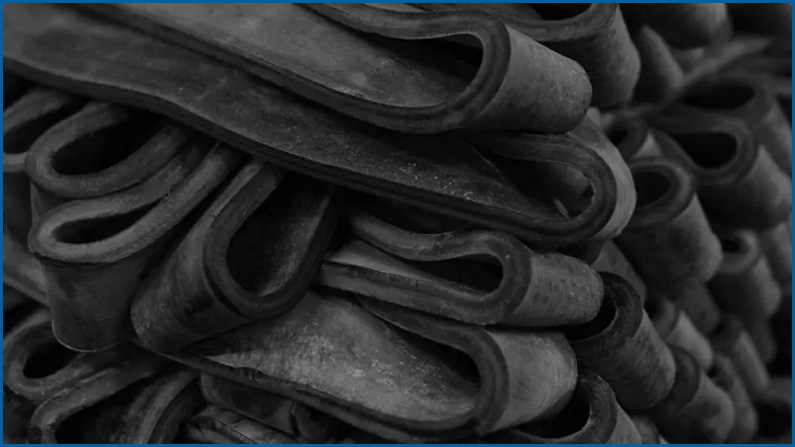
Rubber is an elastic material that can be produced naturally from plant sources or synthetically through a variety of chemical processes. And the rubber material has been in use for thousands of years, and the rubber material can be produced to numerous variations with distinct characteristics that make them suitable for different applications.
The hydraulic hose material properties include rubber material, to make the hydraulic hose as a whole, yes, the inner tube and outer cover of the hydraulic hose can be made of the rubber material, synthetic rubber.
Rubber History
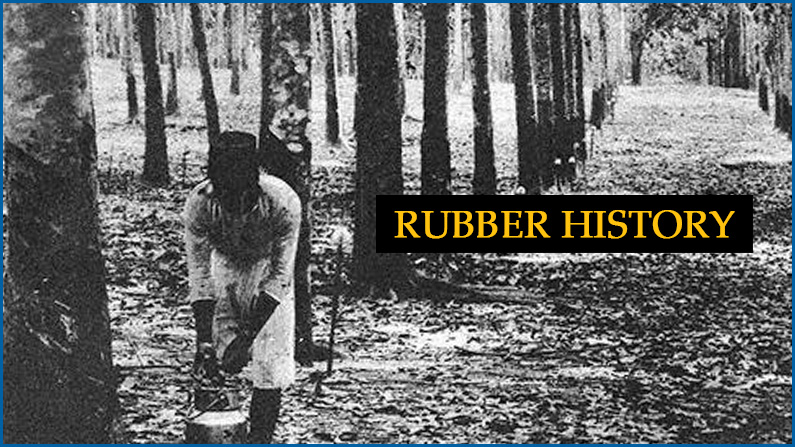
Have you considered the rubber history? As a matter of fact, the rubber was harvested for a long time, and the natural rubber was found much earlier than synthetic rubber.
The history of the development of the world rubber industry is roughly divided into four stages: the Formation Period, the Development Period, the Prosperity Period, and the Stable Development Period.
In the native Central and South American regions, the Mesoamerican civilizations started to use rubber from the plant named Castilla elastic.
The old Mesoamericans had a ball game with rubber balls. The Spanish conquistadores were so astounded by the dynamic bouncing of the rubber balls that they wondered if the balls were bewitched by evil spirits.
The Maya even made rubber shoes by dipping their feet into the latex mixture. Rubber has also been used in other contexts, such as strips for holding stone and metal tools to wooden handles and upholstery for tool handles.
Whereas the old Mesoamericans were not aware of vulcanization, they developed organic methods to treat rubber with similar outcomes, blending raw latex with various from other vineyards.
In Brazil, people understood the use of rubber to produce waterproof rags. A story tells that the first European to come back to Portugal with samples of this product, a rubberized fabric shocked people that it was brought up in the court for sorcery.
Humans have used natural rubber for centuries. During his voyage to discover the New World, Columbus discovered that a ball played by the natives of South America was made of hardened plant sap. Columbus and later explorers were all surprised by this elastic ball. Some samples were considered treasures and brought back to Europe. Later, people discovered that this kind of elastic ball can erase the traces of pencils, so they gave it a common name “Rubber”, which is still the English name of this substance, which is rubber.
Natural Rubber vs Synthetic Rubber
Things first, there are 2 main types, natural rubber, and synthetic rubber.
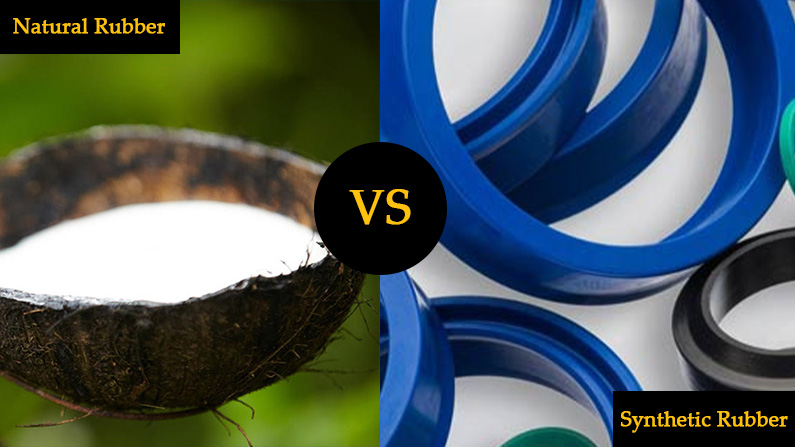
What Is Natural Rubber?
Natural rubber is extracted from the rubber tree liquid, the tree is cut and the sap of the rubber tree flows through a cup. This is the resource substance to extract and purify the rubber material, so the natural rubber comes from the sap of the Hevea Brasiliensis tree.
What Is Synthetic Rubber?
Compared to natural rubber, and synthetic rubber is derived from petroleum and natural gas. The raw material is fundamentally different from the root.
Basic Properties of Rubber
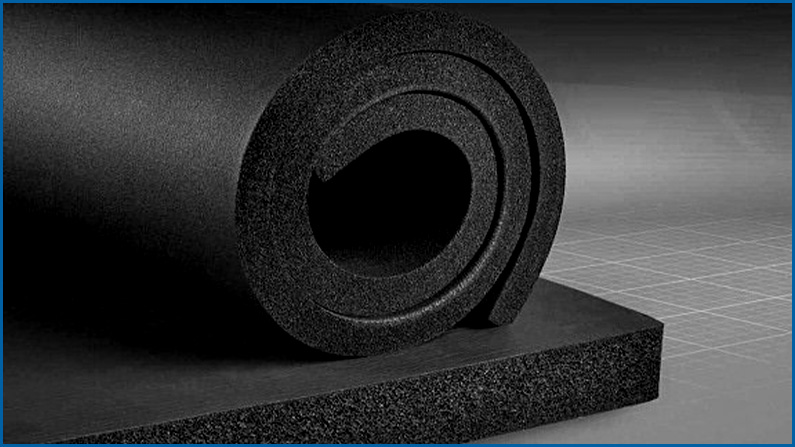
The rubber can come in several variations, and each rubber has unique properties making this rubber special compared with other rubber. Here I am happy to share with you some popular rubber properties.
- Elasticity: This is the basic elasticity of the rubber. The molecular structure of rubber materials allows them to return to their normal shape after being compressed or stretched. The molecular structure of the rubber can make it elastic because of its stable physical structure. The molecules of the rubber substances are attached to one another, and they can return to their original position when you remove your stretching or compressing force. So the rubber material can be made tires for cars, vehicles, and other transportation, because the wheels need to bear high pressure while running process.
- Thermal contraction: While most materials expand when heated, rubber contracts while heated. This unusual phenomenon results from how the rubber molecules respond to heat. When heat is applied, the already-tangled molecules become more tangled and twisted. When heat is removed, the molecules return to their resting state and the rubber regains its original shape.
- Durability: Most rubbers are highly durable, resisting damage and degradation from abrasive and tearing forces, impact, low temperatures, and water. They also exhibit a relatively slow heat buildup rate. So hydraulic hose is also durable, and you can use the hydraulic hose pipe for your hydraulic project for up to several years.
Rubber Applications
The rubber can be applied in many places, such as vehicle tires, automobile tires, and the rest of the rubber material is used to make mountings, gaskets, belts, toys, furniture, clothing, shoes, and hydraulic hoses.
And there are many different types of rubber for production needs.
Natural Rubber
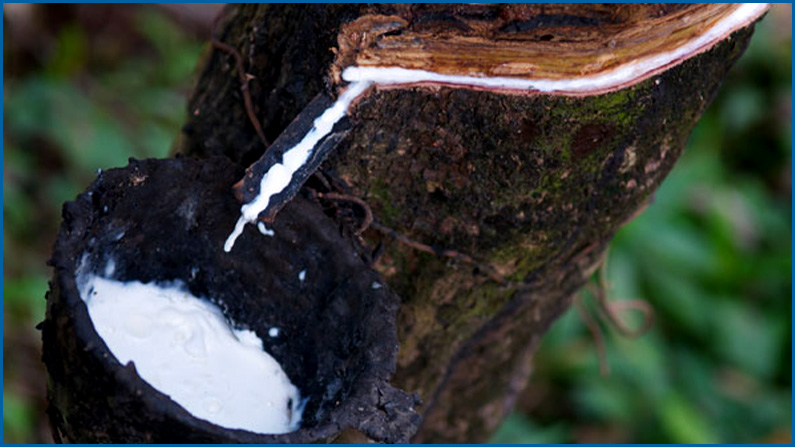
Natural rubber is the elasticity substance derived from the milky liquid from the Hevea brasiliensis tree, Brazilian tree, commonly the rubber tree. And rubber trees are from India, Thailand, Vietnam where have environmental conditions suitable for rubber tree growth.
And natural rubber is extracted from the rubber tree latex sap, and rubber farmers knot a cup to collect the rubber tree sap to the raw material for extracting natural rubber.
Natural Rubber Properties
The natural rubber consists of long, loosened isoprene polymer chains, and the chain reconnects once separated, and this structure gives elasticity to the natural rubber.
The natural rubber has flexibility and strength, as well as impurities and vulnerability to environmental conditions and hydrocarbons. Compared to other rubbers, natural rubber is one of the most flexible types, and it’s resistant to water and certain chemicals. It’s also resistant to cutting, tearing, wear, fatigue, and abrasion, with a working range between -58 to 212 degrees F. Additionally, it has a lot of tensile strength and adheres easily to other materials. However, natural rubber isn’t as effective at resisting heat, light, and ozone as other rubbers like neoprene. The material also varies with the tree it’s produced from, as well as containing natural impurities. While natural rubber is resistant to water and some chemicals, it’s still vulnerable to fuel, oil, and non-polar solvents.
Natural Rubber Application
Natural rubber is used in applications requiring a high level of wear and heat resistance. Thanks to its strength and compressibility, natural rubber is used in engineering applications, like anti-vibration mounts, drive couplings, springs, bearings, rubber bands, and adhesives. But the majority- 50% of natural rubber- is used in high-performance tires for race cars, buses, and aircraft thanks to its strength and heat resistance. It’s also used in hoses, automotive parts, foam mattresses, and battery boxes.
However, thanks to its adhesive properties, natural rubber is also found in rubber cement and the soil stabilization materials used around new roads. Even raw rubber is sometimes used for adhesives and as part of shoe soles. Additionally, about 10% of latex harvested from trees is simply reduced down to 60% rubber solution to make products like latex gloves or to use as a coating.
Neoprene Rubber (CR)
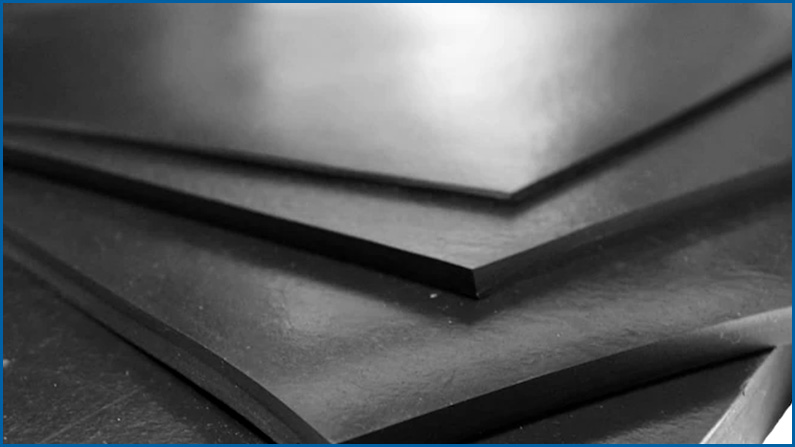
Neoprene rubber, also called chloroprene, is one of the most popular rubber materials, which has a wide application. Neoprene rubber is a synthetic rubber compound, and it can be widely applied in many industry fields.
Neoprene Rubber Properties
Compared with other types of rubber, and regular synthetic rubber, Neoprene rubber exhibits an exceptionally low susceptibility to burning, corrosion, and degradation. So Neoprene rubber is the perfect material for adhesives and corrosion-resistant coatings.
Neoprene Rubber Application
Neoprene rubber has a wide range of uses, mainly used as wire and cable sheaths, hoses, oil-resistant rubber products, heat-resistant conveyor belts, printing rubber sticks, rubber dams, construction sealing strips, road caulking sealants, bridge bearings, Oil field wire waterproof caps, flame-retardant rubber products, various gaskets, anti-corrosive linings for chemical equipment, and neoprene adhesives, etc. In recent years, neoprene has been developed for new uses in building waterproof materials, sealing materials, adhesives, marine development, medical and health, energy development, and people’s lives, and has expanded its application fields.
Silicone Rubber
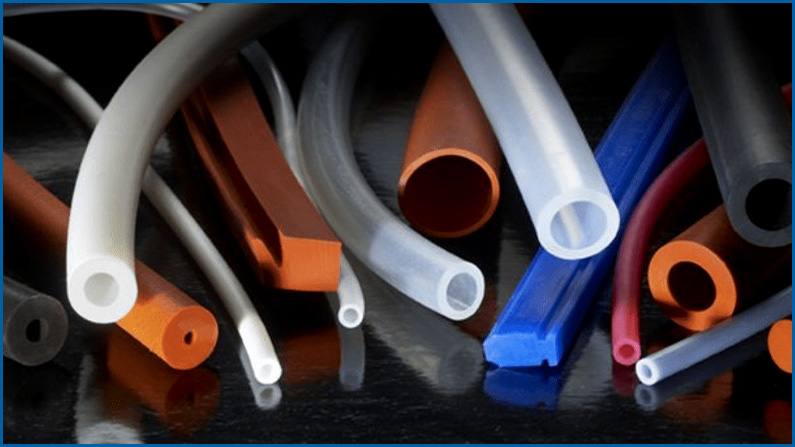
Silicone rubber—also referred to as polysiloxane—is known for its malleability, biocompatibility, and resistance to extreme temperatures, fire, ozone, and ultraviolet (UV) radiation. It is available in both solid and liquid forms in a variety of colors. Its chemically inert nature makes it ideal for use in parts and products that demand biocompatibility (such as gloves, respiratory masks, implants, and other medical products) and chemical resistance (such as baby care items, cosmetic applicators, and food containers and instruments).
Silicone rubber properties
- High and low-temperature resistance: Silicone rubber has the widest operating temperature range (-100~350℃). However, it must be pointed out that silicone rubber has poor resistance to high temperature and temperature sealing and aging. That is, when the air is isolated, especially when water is present, it will cause The mechanical strength to drop rapidly, and even breaks down into low-molecular-weight substances. This shortcoming can be achieved by adding a special heat-resistant stabilizer-a compound of cerium.
- Ozone aging resistance, oxygen aging resistance, weathering resistance performance: The performance of the silicone rubber vulcanized rubber has not changed significantly after being exposed to outdoor exposure in a free state for several years.
- Electrical insulation performance: The silicon dioxide produced after burning is still an insulator, and its corona resistance and arc resistance are extremely good.
- Special surface properties and physiological inertia: The surface energy of silicone rubber is lower than that of most organic materials. Therefore, it has low moisture absorption. Its water absorption rate is only 1% when immersed in water for a long time. The physical and mechanical properties are not reduced. Can play an isolation role. Silicone rubber is odorless, non-toxic, and has no adverse effects on the human body.
- High air permeability: The permeability of N2, O2, and air at room temperature are 30-40 times higher than that of NR. It also has the selective performance of gas permeability, and the permeability of O2 is 1 times that of N2.
The oil resistance, radiation resistance, and combustion resistance of special silicone rubber.
- Oil resistance: It has good stability to aliphatic, aromatic, and chlorinated hydrocarbon solvents, various petroleum-based fuel oils, lubricating oils, hydraulic oils, etc. at room temperature and high temperature, and has good resistance to ethanol, acetone, etc.
Flame retardant: Can be made using flame retardants.
Silicone Rubber Applications
high-temperature resistant insulation and sealing, medical materials, high voltage cables, adhesives, precision molds, isolating glue. Silicone rubber is mainly used in the aviation industry, electrical industry, food industry, and medical industry. Introduction to the application of silicone rubber is a linear polymer elastomer containing silicon-oxygen bonds (Si-O), so it has high thermal stability. It also has excellent resistance to ozone aging, oxygen aging, light aging, and weather aging. It also has excellent electrical insulation, mildew resistance, and high air permeability. It can be used to make many model products, such as various O-rings and gaskets. , Leather cups, oil seals, valves, shock absorbers, and diaphragms, etc. Because silicone rubber is physiologically inert, non-toxic, has no adhesion to other materials, and can withstand repeated cooking and sterilization, it is widely used in the medical and health, and food industries, such as artificial heart valves, artificial throats, artificial blood vessels, pacifiers and Medicine bottle stopper, etc. As the coating and sealing of various electronic tubes or electrical components, it has the effects of moisture-proof, dust-proof, shock-proof, and improved electrical performance.
Nitrile Rubber (NBR)
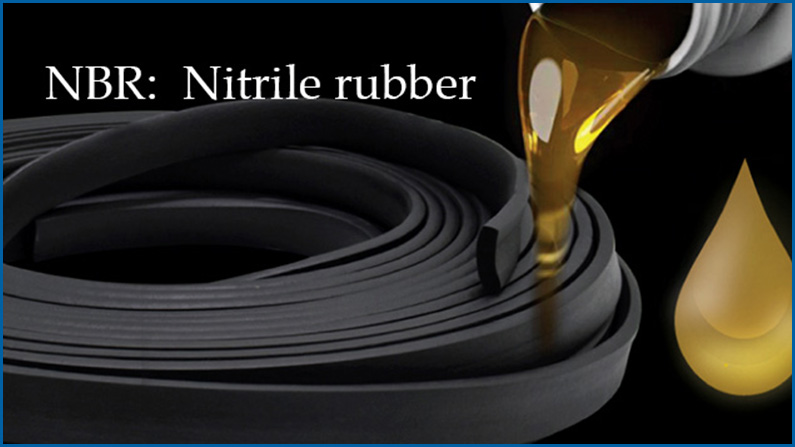
Nitrile rubber—also known as Buna-N rubber or nitrile butadiene rubber (NBR)—demonstrates several desirable mechanical and chemical properties, such as resistance to compression set, heat, oil and gas, and wear. These traits make it suitable for use in automotive gaskets and seals, O-rings, and engine hoses. It is also used in medical products (e.g., surgical gloves) since it lacks the allergenic proteins of latex-based rubbers and maintains its structural integrity better than silicone rubber.
Nitrile Rubber Properties
- Excellent abrasion resistance
- Good rebound, tear resistance, and non-polar solvent resistance
- Good water and oil resistance.
- Good resistance to gas permeability
- Good elongation properties and excellent compression set resistance
- Adequate resilience and tensile strength
- Good resistance to aliphatic hydrocarbons
- Excellent adhesion to metal and rigid materials
- Excellent colorability
Nitrile Rubber Application
EPDM Rubber
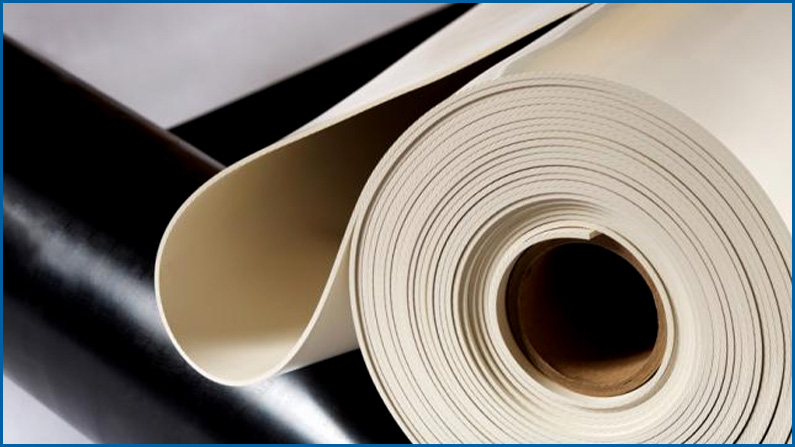
The main chain of EPDM rubber is composed of chemically stable saturated hydrocarbons, and only contains unsaturated double bonds in the side chain, so it is basically a kind of saturated rubber. Since there are no polar substituents in the molecular structure and the cohesive energy between molecules is low, the molecular chain can maintain flexibility in a wide temperature range. The chemical structure of ethylene propylene rubber makes its vulcanized products have unique properties.
EPDM Rubber Properties
Low density and high filling: EPDM rubber is a relatively low-density rubber with a density of 0.87. In addition, it can be filled with a large amount of oil and fillers, which can reduce the cost of rubber products and make up for the high price of EPDM rubber. The physical and mechanical properties are not significantly reduced.
Aging resistance: Ethylene-propylene rubber has excellent weather resistance, ozone resistance, heat resistance, acid and alkali resistance, water vapor resistance, color stability, electrical properties, oil-filling properties, and fluidity at room temperature. EPDM rubber products can be used for a long time at 120 ℃, at 150~200. C can be used briefly or intermittently. Adding suitable antioxidants can increase its use temperature. EPDM rubber crosslinked with peroxide can be used under more severe conditions. EPDM rubber does not crack when the ozone concentration is 50×10~ and is stretched by 30% for more than 150 hours.
Corrosion resistance: Because ethylene-propylene rubber lacks polarity and a low degree of unsaturation, it has good resistance to various polar chemicals such as alcohols, acids, alkalis, oxidants, refrigerants, detergents, animal and vegetable oils, ketones, and greases. ; But the stability is poor in fatty and aromatic solvents (such as gasoline, benzene, etc. and mineral oil. The performance will also decrease under the long-term action of concentrated acid.
EPDM Rubber Application
Where is EPDM used? EPDM rubber is used in seals, o-rings, glass-run channels, radiators, garden and appliance hoses, tubing, pond liners, washers, belts, electrical insulation, solar panel heat collectors, and speaker cone surrounds.
Styrene-Butadiene Rubber (SBR)
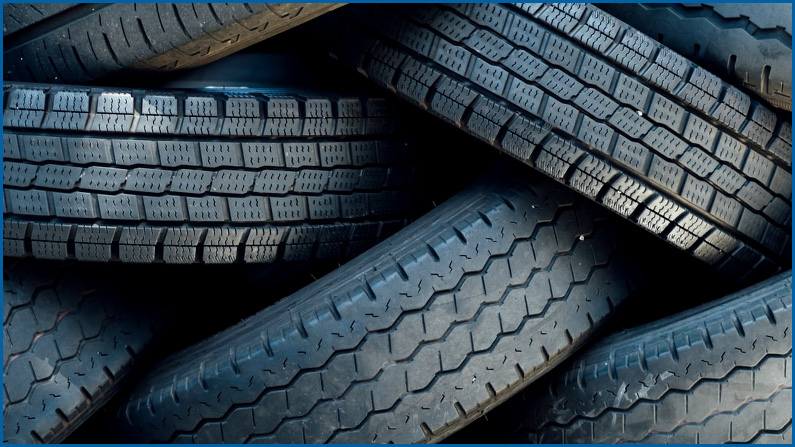
Styrene-Butadiene Rubber Properties
SBR is a copolymer of styrene and butadiene and has properties similar to Natural Rubber. It has good abrasion resistance, excellent impact strength, very good resilience, and high tensile strength.
Solution polymerized styrene-butadiene rubber has excellent wear resistance, groove crack resistance, and good grip on wet roads, heat resistance, and good flex resistance after prolonged exposure at high temperatures. In addition, it is mixed in an internal mixer. The characteristics of low heat generation during refining, low extrusion expansion rate, high filling volume, etc.
Styrene-Butadiene Rubber Application
Mainly used in tires, accounting for about 80% of the total output of solution polymerized styrene-butadiene rubber, such as the manufacture of car tires, large tire treads, snow tire carcasses, etc.
Butyl Rubber
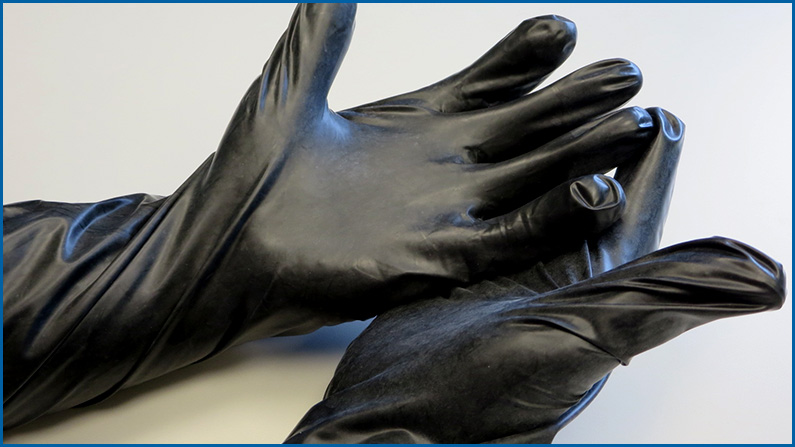
Butyl Rubber Properties
Butyl rubber, or polyisobutylene, is a vinyl elastomer very similar to polyethylene and polypropylene in its structure, except that every other carbon atom is substituted with two methyl groups rather than one. It is made by a process called cationic vinyl polymerization from the monomer isobutylene. Usually, 1-2% isoprene is added to the isobutylene. The reaction is very fast so it is usually synthesized at very low temperatures. The addition of isoprene creates double bonds that allow the material to be crosslinked by vulcanization, just like natural rubber. This was an important step in making the original material useful during World War II as a substitute for natural rubber in the manufacturing of tires and tank treads. Polyisobutylene was first synthesized in 1931 and developed into butyl rubber in 1937. Curing rates improved in the 1960s with the development of halogenated, chlorinated, and brominated forms. These forms are often abbreviated as CIIR (for chlorinated isobutylene isoprene rubber) and BIIR (for brominated isobutylene isoprene rubber).
Put simply, vulcanizing is a process that ties all the rubber molecules together to form a single large molecule that does not melt as it gets warm and does not embrittle as it gets cold. Vulcanizing was invented by Charles Goodyear in 1839. It is a thermosetting process, so vulcanizing takes place after the product is formed.
Butyl Rubber Application
Butyl rubber can be applied for the production of automotive tires, healthcare products, such as latex rubber gloves. The excellent properties of high damping, resistance to heat aging, resistance to ozone, and barrier properties make them perfect for manufacturing automotive vibration control, hoses, and gaskets. Butyl rubbers are also used to improve formulations for conveyor belts, tank linings, and condenser packaging. Construction Butyl rubber is also used in the construction industry. Using butyl rubbers, the weather ability of asphalt, contact cement, and sealant tapes can be improved. Adhesives Use butyl rubbers to provide adhesive properties in tapes, valve cement, and flooring adhesives. Consumer products Butyl rubbers are used in ball bladders for sports goods and electrical appliance condenser packing. Excellent air retention properties make butyl rubber a major component in bladders used in the sporting goods industry. Similarly, the low permeability and chemical inertness of butyl rubber make it ideal to make condenser packing for electrical appliances. Butyl rubber is used for making the gum base in chewing gums.
Fluorosilicone Rubber
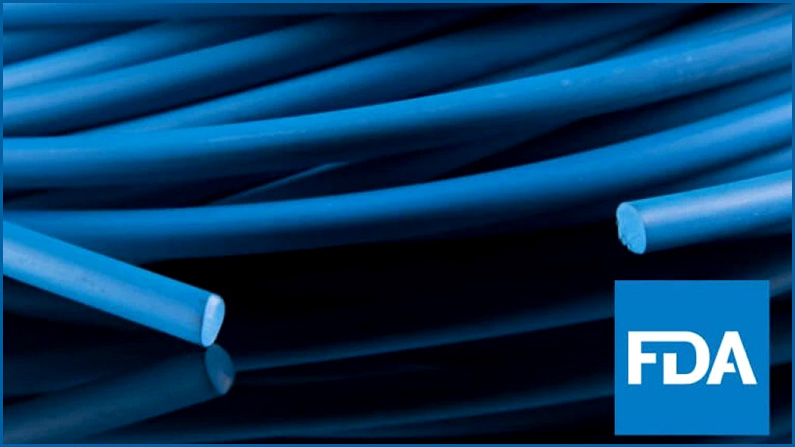
Fluorosilicone Rubber Properties
Like silicone, fluorosilicone rubber is a long-lasting elastomer that is stable and compression set resistant across temperature extremes, but unlike silicone, fluorosilicone contains trifluoropropyl groups that enhance its chemical resistance to non-polar solvents, fuels, oils, acids, and alkaline chemicals.
Fluorosilicone Rubber Application
For automotive applications, a range of silicone/ fluorosilicone polymers are also used to provide a combination of fluid resistance, moulding, and economy. The primary uses are for static seals in hydraulic and fuel systems.Natural Rubber
Latex Rubber
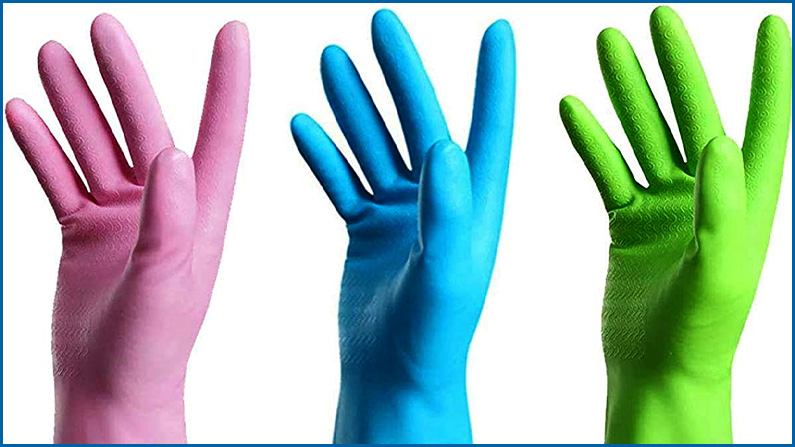
The latex rubber is the milky white liquid emulsion contained in some flowering plant cells, such as the rubber tree-Hevea brasiliensis, or any other synthetic rubber or plastic-based water emulsions.
The plant product is a complex mixture of substances suspended in a watery medium in which salts, sugars, tannins, alkaloids, enzymes, and other substances are dissolved including various gum resins, fats, or waxes and, in some cases poisonous compounds.
It is produced mainly by the cells of plants in the Asclepiadoideae subfamily and others in the Apocynaceae family but also by plants in the Sapotaceae, Euphorbiaceae, Papaveraceae, Moraceae, and Asteraceae families
A mature rubber tree’s latex is a soft white material found under the bark. Given the intensity and man-made feel of so many of its final uses, such as tires, rubber gloves, and tennis shoes, you might be shocked to think of latex as a natural material.
The reality is that natural rubber latex is derived from nature. Rubber tappers collect latex from trees using a procedure that has been passed down over centuries until it is processed.
Latex Rubber Properties
Latex is an excellent rubber substance after processing. Latex’s tensile and elongation properties, as well as tear resistance and overall durability, are well known.
Latex is unaffected by the majority of modern abrasives. Low temperatures are not a problem but high temperatures can be. Latex can corrode at temperatures above 82 degrees.
To protect latex from corrosion caused by heat, sunlight, and oxygen, treatment chemicals can be added. Latex should not be used in conjunction with petroleum products or solvents. This will cause the latex to break down.
Latex Rubber Application
Latex has a wide range of uses, from everyday objects to more advanced applications. The gloves swim caps, chewing gum, mattresses, catheters, rubber bands, balloons, tennis shoes, and a number of other sporting goods are all manufactured of natural rubber latex.
Coatings containing synthetic latexes, such as latex paint are popular. They are also used in glues because of their tendency to solidify when water evaporates from the latex polymer particles.
Synthetic latex can also be mixed into cement for resurfacing and repairing cracks in concrete.
Liquid Silicone Rubber
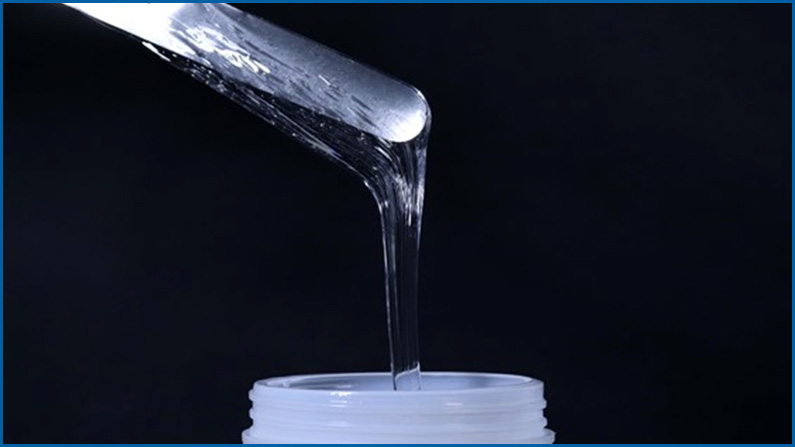
Liquid silicone rubber is a high purity, two-component platinum cured silicone that is suitable for the manufacture of technical parts that require strength, resistance and high quality.
LSRs are viscous, pumpable products that are primarily manufactured using liquid injection molding. Liquid Silicone rubber is used in a wide range of applications in the elastomer industry, from consumer goods to medical devices and anything in between.
Liquid Silicone Rubber Properties
Silicone rubber comes in a variety of grades, each with its own set of material properties. One of the reasons LSR is used in so many different applications is because of its flexibility.
Liquid silicone’s mechanical properties make it a great place to start if you need a medical or food-grade product with superior bacteria resistance or an automotive part that can withstand extreme heat.
The quick curing and low compression collection of silicone and its resistance to tearing, heat, water and oil, and electrical conductivity, and overall strength are all essential material properties.
LSR can be used at temperatures ranging from -100 to 200 degrees Celsius, exposed to wind, rain, and UV light for long periods of time, and immersed in water, oil or solvents.
LSR comes in a range of grades with material properties that can withstand even the most challenging applications.
Liquid Silicone Rubber Application
The manufacturing of LSR parts is the most common application for silicone rubber. LSR components are used in a variety of industries.
They are ideal for gaskets and hardware in consumer appliances like microwaves because of steam resistance and low compression set. They are suitable for electronic interfaces on keyboards and touchpads because of their conductivity and fatigue resistance.
Their oil resistance ensures that automotive components last long. Liquid silicone rubber is a highly adaptable material, with new uses being found and tested regularly.
It’s used in a variety of industries, including healthcare, automobile parts manufacturing, electronics, and consumer goods, gaskets and other hardware, and many others.
Final Thougts
This is the ultimate guide about the types of rubber material, thanks for your reading. If you want to know more about the rubber types and rubber basic knowledge, please feel free to contact us now.