The hydraulic hose is important in resource conveyance in the industrial field, including the building and mining industries. Hydraulic hose maintenance is also very important to ensure that heavy-duty machinery can work as normal.
Here are some tips that help you protect your hydraulic hose properly, to make it work longer to expand its service life.
Let’s dive into this guide to get some hacks.
What Causes Hydraulic Hose Damage
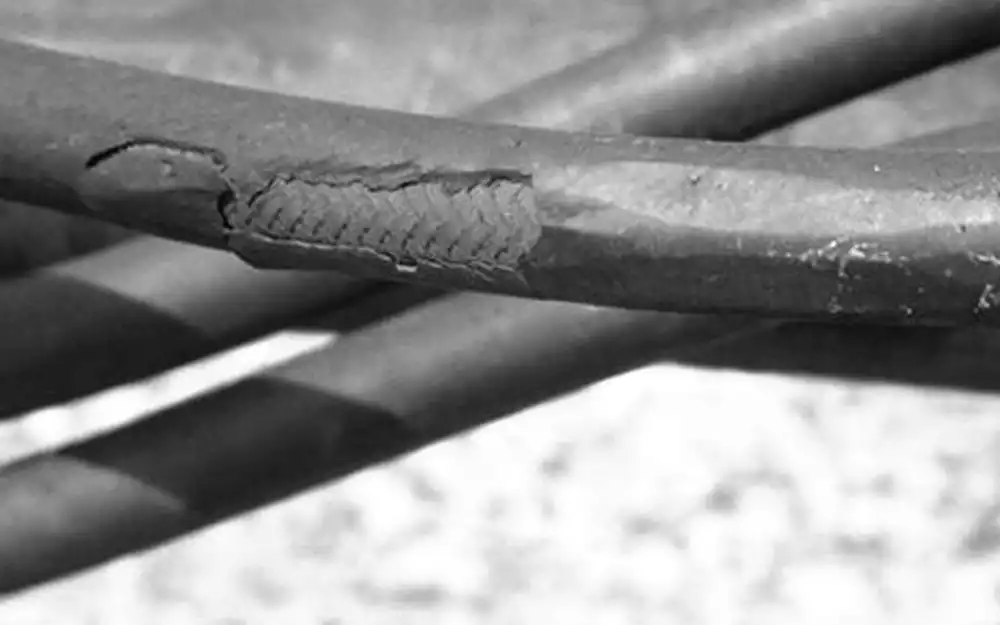
Hydraulic hose damage can stem from a variety of factors, both internal and external.
Here are some of the most common causes resulting in the hydraulic hose damages:
- Abrasion: This is the most frequent culprit. Constant rubbing against machinery, sharp edges, or rough surfaces wears down the hose’s outer cover, exposing the inner layers and ultimately leading to failure.
- Kinking and Bending: Excessive bending or twisting can weaken the hose’s internal structure, causing cracks and leaks.
- High Temperatures: Exposure to extreme heat can cause the hose’s materials to degrade, harden, and become brittle. This makes them more susceptible to cracking and rupture.
- Low Temperatures: In very cold conditions, hoses can become stiff and brittle, increasing the risk of cracking or splitting, especially during flexing.
- Chemical Exposure: Certain chemicals can attack and degrade the hose’s materials, weakening them over time.
- Internal Pressure Surges: Sudden pressure spikes within the hydraulic system can cause excessive stress on the hose, leading to leaks or ruptures.
- Improper Installation: Incorrectly installed fittings, crimped hoses, or insufficient clamping can all weaken the hose and increase the risk of failure.
- Age and Fatigue: Over time, hoses naturally degrade due to age and the cumulative effects of use and environmental factors.
Preventing these issues involves:
- Proper routing and installation: Avoiding sharp bends, securing hoses properly, and maintaining adequate clearance.
- Using appropriate hydraulic hose guards: Such as spring guards, spiral wraps, or sleeves to protect against abrasion and external damage.
- Regular inspection and maintenance: Regularly checking hoses for signs of wear and tear and replacing damaged hoses promptly.
- Selecting the right hose for the application: Choosing hoses that are compatible with the hydraulic fluid, operating temperature range, and environmental conditions.
By understanding these common causes and implementing preventative measures, you can significantly extend the lifespan of your hydraulic hoses and reduce the risk of costly failures and downtime.
How to Protect Hydraulic Hoses
Regular visual inspections are sufficient for maintaining hydraulic hose health. False
While visual inspections are important, they may not always detect internal issues like abrasion, fatigue, or internal leaks. Regular pressure testing and other non-destructive testing methods are crucial for identifying potential problems before they lead to catastrophic failures.
Proper hose routing and installation significantly reduce the risk of wear and tear. True
Avoiding sharp bends, excessive flexing, and contact with hot surfaces during installation minimizes stress on the hose, reducing the likelihood of kinking, abrasion, and fatigue.
Hydraulic hose failures are always preventable. False
While proper maintenance and preventative measures significantly reduce the risk of hose failures, some failures can occur unexpectedly due to unforeseen circumstances, such as extreme external forces, sudden pressure surges, or manufacturing defects.
Regular maintenance checks, including pressure testing, can help prevent unexpected failures. True
Regular inspections, including pressure tests, can help identify potential issues early on, such as leaks, internal wear, or weakening of the hose material, allowing for timely repairs or replacement before catastrophic failure occurs.
All hydraulic hoses are interchangeable. False
Hydraulic hoses are designed for specific applications and operating conditions. Factors such as pressure ratings, temperature ranges, fluid compatibility, and hose construction (braided, wire reinforced, etc.) vary significantly. Using the wrong hose can lead to serious safety hazards and equipment damage.
Hose savers are only necessary for hoses exposed to extreme environments. False
Hose savers provide protection against abrasion, kinking, and other forms of damage in various environments, not just extreme ones. Even in seemingly benign conditions, hoses can be subjected to wear and tear, leading to premature failure. Using hose savers is a proactive measure to extend hose life and prevent unexpected downtime.
1. Hydraulic Hose Guards
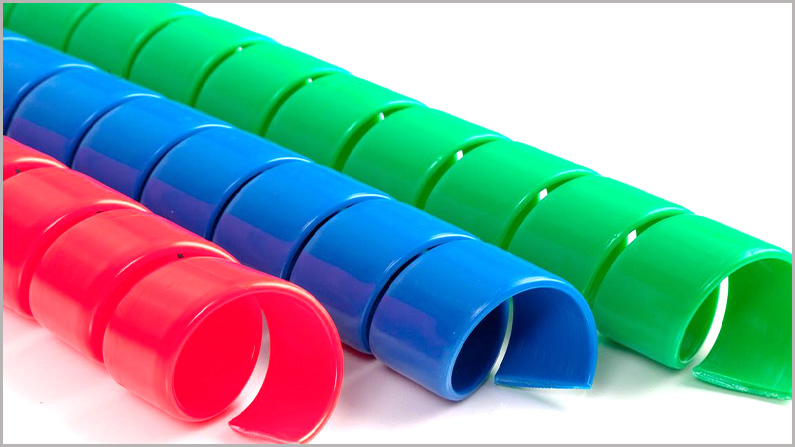
Hydraulic Hose Spring Guards: These are coiled metal springs that encase the hose, providing excellent abrasion resistance and protection against kinking.
Benefits:
- High abrasion resistance
- Protection against sharp edges and debris
- Prevents kinking and twisting
- Durable and long-lasting
Applications: Ideal for use in harsh environments with high levels of abrasion, such as construction sites, mining operations, and heavy equipment applications.
Spiral Wraps: Flexible, often plastic, wraps that protect hoses from abrasion, cuts, and crushing. They can also help contain leaks in case of a rupture.
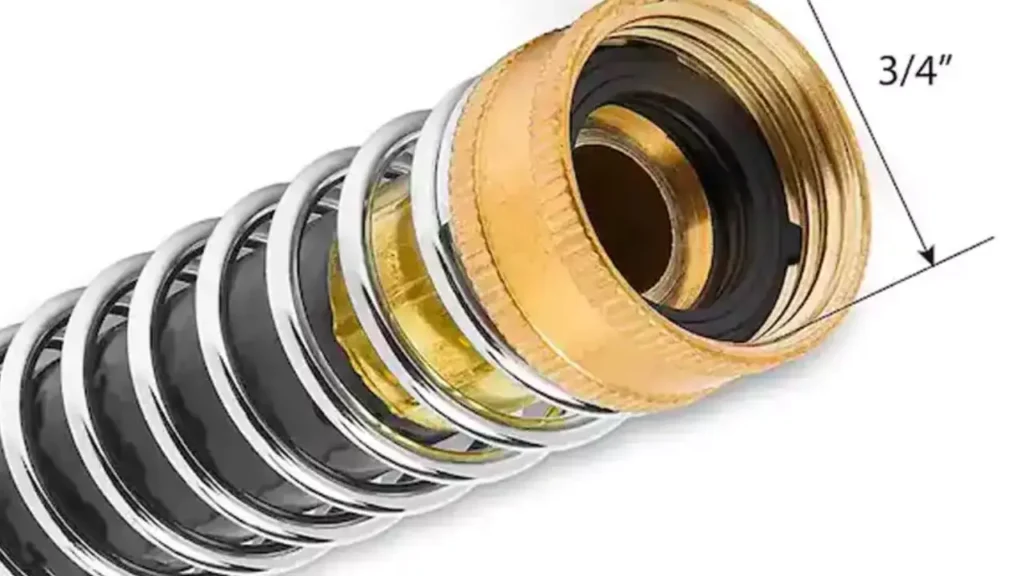
Benefits:
- Good abrasion resistance
- Protects against cuts and punctures
- Can help contain leaks
- Relatively easy to install
Applications: Suitable for a wide range of applications, including those with moderate levels of abrasion and potential for external damage.
Sleeves: Fabric or synthetic sleeves that cover the hose to protect it from abrasion, chemicals, and UV radiation.
Benefits:
- Protects against abrasion and cuts
- Can provide chemical resistance
- Protects against UV degradation
- Can improve hose appearance
Applications: Ideal for applications where chemical exposure, UV radiation, or a need for a more aesthetically pleasing solution is a concern.
2. Proper Routing and Installation
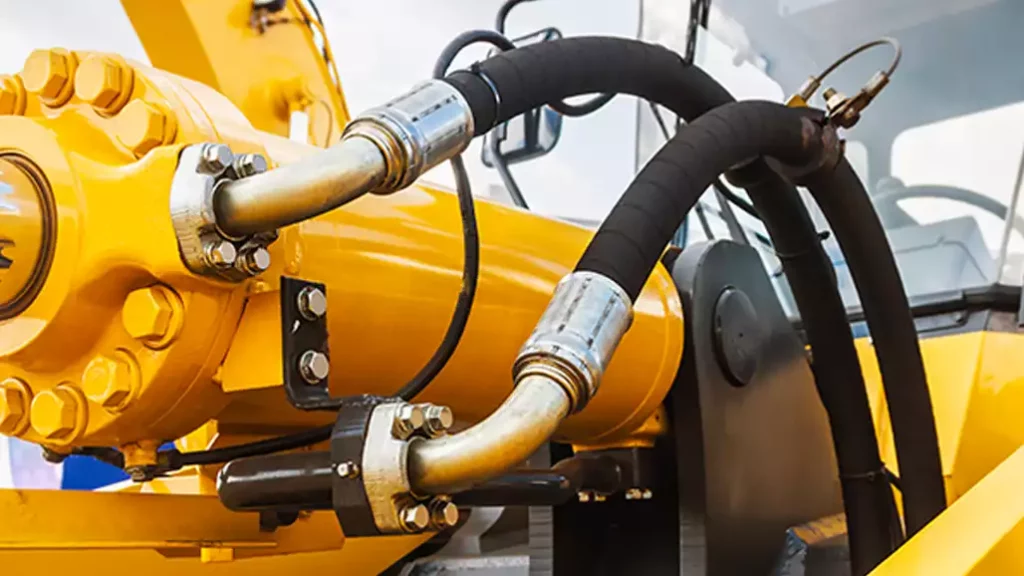
Avoid Sharp Bends: Excessive bending can weaken the hose and cause premature failure. Route hoses smoothly with gentle curves.
Guidelines:
- Use hose reels or guides to minimize sharp bends.
- Avoid routing hoses over sharp edges or corners.
- Provide adequate clearance for hose movement.
- Securely Mount Hoses: Use proper clamps and brackets to secure hoses to prevent chafing and movement that can cause damage.
Best Practices:
- Use clamps that are the correct size and type for the hose.
- Securely attach clamps to prevent loosening.
- Use brackets to support hoses at regular intervals.
Maintain Adequate Clearance: Ensure sufficient clearance between hoses and other components, such as moving parts or hot surfaces.
Considerations:
- Keep hoses away from heat sources.
- Avoid routing hoses near moving parts that could cause abrasion.
- Provide enough space for proper airflow around hoses.
3. Regular Inspection and Maintenance
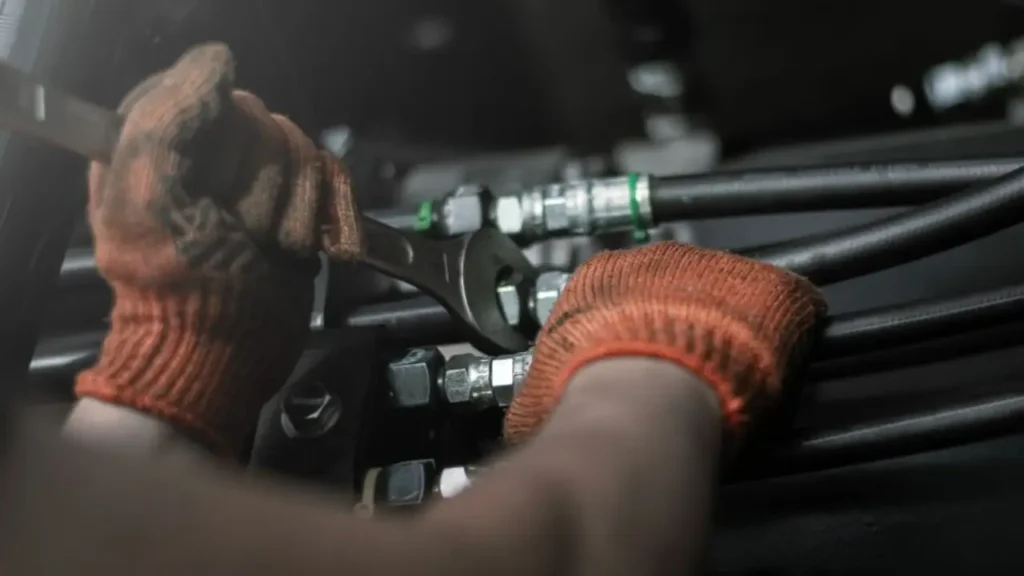
Visual Inspections: Regularly inspect hoses for signs of wear and tear, such as cuts, abrasions, bulges, or leaks.
Frequency: Conduct visual inspections at regular intervals, such as daily or weekly, depending on the severity of the operating environment.
Pressure Testing: Periodically pressure test hoses to identify potential weaknesses.
Guidelines:
- Follow manufacturer‘s recommendations for pressure testing procedures.
- Use appropriate testing equipment.
- Document test results for future reference.
Replace Damaged Hoses Promptly: Replace any damaged hoses immediately to prevent further problems and ensure safety.
Importance:
- Do not attempt to repair damaged hoses.
- Replace hoses with the correct type and size.
- Follow proper installation procedures.
4. Consider the Environment
Extreme Temperatures: If operating in extreme temperatures, select hoses and protective measures that can withstand those conditions.
Considerations:
- Use hoses designed for high or low temperatures.
- Consider using heat shields or insulation to protect hoses from extreme temperatures.
Chemical Exposure: If exposed to chemicals, choose hoses and protective coverings that are resistant to those specific chemicals.
Guidelines:
- Consult with our hydraulic hose supplier to select the appropriate chemical-resistant hose.
- Use chemical-resistant sleeves or wraps to provide additional protection.
Abrasive Environments: In environments with high levels of abrasion, utilize robust protective measures like heavy-duty spring guards or abrasion-resistant sleeves.
Recommendations:
- Use high-quality spring guards with tightly wound coils.
- Consider using abrasion-resistant sleeves made from materials such as Kevlar or nylon.
By implementing these protective measures, you can significantly extend the lifespan of your hydraulic hoses, reduce the risk of failures, and improve the overall safety and efficiency of your hydraulic systems.
How to Make Hydraulic Hoses Last Longer
Here’s how to make your hydraulic hoses last longer:
- Match the Application: Select hoses specifically designed for the fluid, pressure, temperature, and environment they’ll encounter.
- Consider Material: Choose hoses with covers resistant to abrasion, chemicals, and UV radiation.
- Quality Matters: Invest in high-quality hoses from reputable manufacturers.
2. Proper Installation:
- Avoid Sharp Bends: Minimize sharp bends in the hose line. Use hose reels or guides to create smooth curves.
- Secure Mounting: Use proper clamps and brackets to secure hoses to prevent chafing and movement.
- Maintain Adequate Clearance: Ensure sufficient space around hoses to prevent contact with hot surfaces, sharp edges, or moving parts.
3. Protection is Key:
- Hose Guards: Utilize spring guards, spiral wraps, or sleeves to protect hoses from abrasion, cuts, and punctures.5
- Environmental Considerations: If operating in extreme temperatures, consider using heat shields or insulation. For chemical exposure, select chemical-resistant hoses and coverings.
4. Regular Maintenance:
- Visual Inspections: Regularly inspect hoses for signs of wear and tear, such as cuts, abrasions, bulges, or leaks.
- Pressure Testing: Periodically pressure test hoses to identify potential weaknesses.
- Replace Damaged Hoses Promptly: Replace any damaged hoses immediately to prevent further problems and ensure safety.
5. Minimize Internal Stress:
- Maintain Proper Fluid Levels: Ensure adequate fluid levels to prevent cavitation and pressure surges.
- Avoid Excessive Pressure: Operate within the recommended pressure limits for the hose.
- Proper Filtration: Maintain clean hydraulic fluid to prevent internal wear and tear.
By following these guidelines, you can significantly extend the lifespan of your hydraulic hoses, reduce the risk of failures, and improve the overall efficiency and safety of your hydraulic systems.
How Do I Keep My Hydraulic Hose From Cracking
Hydraulic hose cracking is a common problem that can lead to leaks, equipment failure, and safety hazards. Here’s how to minimize it:
1. Choose the Right Hose:
- Material Matters: Select hoses with covers made from materials resistant to UV radiation, ozone, and chemicals.
- Temperature Range: Ensure the hose is rated for the temperature extremes it will encounter.
- Chemical Compatibility: Choose hoses compatible with the hydraulic fluid used in your system.
2. Proper Installation:
- Avoid Sharp Bends: Minimize tight bends that can stress the hose and cause cracks.
- Secure Mounting: Use proper clamps and brackets to prevent movement and chafing.
- Maintain Adequate Clearance: Ensure sufficient space around hoses to prevent contact with hot surfaces, sharp edges, or moving parts.
3. Protection is Key:
- Hose Guards: Utilize spring guards, spiral wraps, or sleeves to protect hoses from abrasion and external damage.
- Environmental Considerations: If operating in harsh environments, consider using additional protective measures like heat shields or insulation.
4. Regular Maintenance:
- Visual Inspections: Regularly inspect hoses for signs of cracking, abrasion, or other damage.
- Pressure Testing: Periodically pressure test hoses to identify potential weaknesses.
- Replace Damaged Hoses Promptly: Replace any cracked or damaged hoses immediately to prevent further problems.
5. Minimize Internal Stress:
- Maintain Proper Fluid Levels: Ensure adequate fluid levels to prevent cavitation and pressure surges.
- Avoid Excessive Pressure: Operate within the recommended pressure limits for the hose.
- Proper Filtration: Maintain clean hydraulic fluid to prevent internal wear and tear.
6. Storage Considerations:
- Protect from Sunlight: Store hoses out of direct sunlight to prevent UV degradation.
- Avoid Extreme Temperatures: Store hoses in a cool, dry place away from extreme temperatures.
By implementing these preventative measures, you can significantly reduce the risk of hydraulic hose cracking and ensure the safe and reliable operation of your equipment.
Conclusion
Protecting your hydraulic hoses is crucial for the safety, efficiency, and longevity of your hydraulic systems. By implementing a combination of protective measures, including proper routing, regular inspections, and the use of high-quality hose guards, you can significantly reduce the risk of hose failures, minimize downtime, and improve the overall performance of your equipment.
Ready to invest in the best protection for your hydraulic hoses? Our premium hydraulic hose guards are engineered to provide superior protection against abrasion, kinking, and other forms of damage. Contact us today to learn more about our products and how we can help safeguard your hydraulic systems.